Podcast transcript: Intelligent Performance Engineering (Part 1)
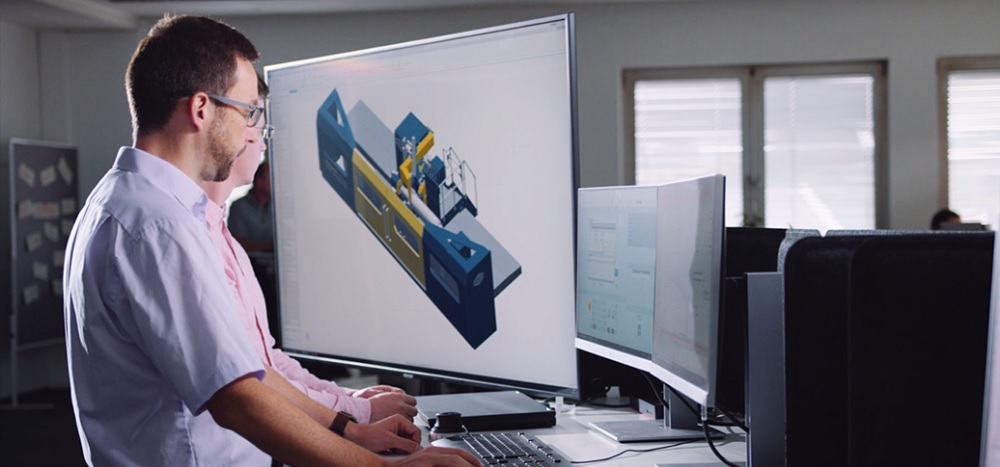
Complicated new machine introductions for machine builders requires the added expertise of Intelligent Performance Engineering (IPE) for industrial machinery companies to develop engineering standards in step with the increasing sophistication of new machines. (Listen to audio podcast)
Read the transcript from the first IPE Podcast:
Bill Butcher: Hi everyone and welcome to our latest Industrial Machinery podcast series. My name is Bill Butcher, and I’m the marketing leader for the Industrial Machinery industry. During this podcast series, we will be focusing on the Intelligent Performance Engineering solution from Siemens Digital Industries Software.
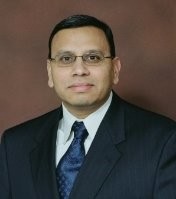
I feel very fortunate to have with me two leading experts representing the industrial machinery industry: Rahul Garg and Giulio Camauli. Rahul is the Industry Leader for Siemens Industrial Machinery industry and Giulio is the industrial Machinery Industry leader for the simulation and test solutions within Siemens Digital Industries Software. Both Rahul and Giulio have over 30 years of experience respectively – and I’d like to thank both of you for taking the time to talk with me today.
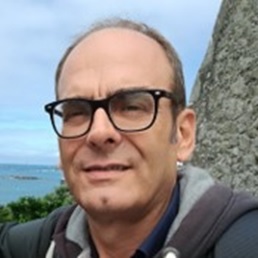
We know that the machinery manufacturers are faced with many challenges. Of course, one of the biggest challenges is complexity. This complexity surrounding new machine introductions is only increasing for machine builders.
So, I’d like to start and ask you, to help the listeners understand, what is Intelligent Performance Engineering? And why is this critical for industrial machinery companies to develop new engineering practices in order to keep pace with this growing complexity associated with machine introduction? So, Rahul, let’s start with you. The term ‘Intelligent Performance Engineering’, what does it mean? And why is it important to machine manufacturers?
Rahul Garg: Thanks a lot. When we look at what machinery companies are doing and what you just mentioned about complexity – one of the things that they are trying to manage and address their market needs is improving the reliability of their equipment, and address the growing needs of these customers. To support the growing needs of these customers, while trying to balance the reliability and improve the performance of the machines, they must figure out how to do that in a very quick manner. To get that speed and ability to quickly respond to those customer needs, we have this whole concept of a digital thread – and Intelligent Performance Engineering is one of our key digital threads to support these companies.
The idea behind this thread is providing the companies the ability to evaluate their designs, to verify their designs, test their designs, and really help them improve their innovation process. Once they can do those things, they can determine whether the design they’re making, along with the machine component, will work reliably and perform in the circumstances that they wanted to? So that’s what Intelligence Performance Engineering is, in trying to make sure that the designs and concepts that you’re trying to build, and the challenges of complexity you’re trying to address can support the reliability and performance requirements. And where we bring in the whole intelligent aspect of it is the ability to see on an ongoing basis how that machine is performing and fine-tune the parameters. So that’s the idea behind Intelligent Performance Engineering to be able to improve the innovation cycle, and to get products out the door faster.
Bill Butcher: Okay, so if I’m hearing you correctly, you mentioned digital thread and it relates to the very popular phrase which is out in the marketplace today: digital twin. So, to support the machine design in the context of simulation for machine manufacturers today, Giulio, can traditional process support this digital twin approach that Rahul just talked about?
Giulio Camauli: So, thank you, Bill, for your question and your introduction. Let me say that one of the most important aspects of designing new industrial equipment or modifying an existing design lies in the verifying and testing procedure and how it will perform before it reached the customer. So, everybody can understand that it costs much less to fix a problem identified during the designing process than later in the product development cycle. Therefore, industrial OEMs have adopted a collection of digital simulation and analysis tools used to understand that our design choices affect the performance and failure modes for a component, device or machine. In the traditional approach, we must say that there are still manual handoffs between design and simulation processes. Engineers can often use design level simulation that then provides a baseline assessment of the design or as a definitive design analysis or, eventually, they need a more advanced simulation. As enterprises attempt to deliver machines with faster cycle rates and delivery schedules are being compressed, teams are feeling pressure to do more simulation upfront rather than test many physical prototypes and assume the physical tests are sufficient. So, let me add that the best option is to have simulation and test working together efficiently.
Bill Butcher: Okay, thanks. So, these are some big topics we’re talking about – very high-level topics. We’re talking about digitalization. Neither of you has mentioned it yet, but industry 4.0 is a topic that most machine manufacturers are aware of. And it seems like there’s pressure building up between these traditional approaches, that Giulio mentioned, and the desire to stay competitive with the growing complexity associated with new machine introduction. So, Rahul, I’ll come back to you – would you say that technology has been the biggest catalyst for change in the machinery industry? And, are there other factors that are creating the need for this advanced technology solution in the machinery space?
Rahul Garg: Technology has certainly been a catalyst to get the industrial machinery companies to determine what they should do. But there are many more factors that have been driving companies to be looking to do something differently. It’s all the way from one of the issues around the customers demanding the machines in their own specifications with their own customized requirements, ensuring that the machine meets and exceeds the performance requirements of those specific use cases. Those personalizations and use cases are increasing by the day and machines need to support them. The other big issue that comes about is the global competition in being able to differentiate your product, innovating quickly and serving your customers at a faster pace with lower cost. So being able to address many of those needs has traditionally been around. Therefore, technology has become the catalyst that has fueled this whole process and caused all companies to consider and evaluate how they are meeting the needs, challenges and how digitalization can help them in that process.
Bill Butcher: So, Giulio, coming back to you, Rahul mentioned about how technology continues to advance – mentioning a couple of examples. Also, expectations on customization from consumers is increasing, right? And all this leads to this continued increase in complexity that tests the limits of the technology advancements. It’s kind of a chicken and egg, right? So, with the need to address the growing demands of flexibility and complexity, it appears that this can’t be done without the ability to quickly evaluate machine behaviors and provide information back in the model. Do you see this happening today? Is this a standard process? Or is this something we’re reaching for?
Giulio Camauli: Yes, we have to say that some manual work is involved in running the simulations used to verify various characteristics of the equipment – and these simulations are often performed by different tools. As a result, basic simulations don’t always reflect the interdependency of electromagnetic interference, structural loads, heat and vibration together. This is becoming more of an issue with smarter equipment, which increases the complexity of wiring, electronics and software. The designer may run a basic analysis to prove the design is safe, but this may not allow the designer to explore the performance ramifications of various engineering trade-offs. Designers may also over-engineer a design so that they don’t have to run as many tests. This can lead to added cost weight or reduce the performance of the machine to meet safety requirements. And more complex processes are adopted by the analysts to address the complexity of the simulation tools and the lack of integration into the design tool. Delays in the process can also mean that an analysis is being done on an outdated design and this risk is very high.
Bill Butcher: I want to come back to one of the terms you just used there, which is the lack of integration. It seems to be in conflict with some of these other terms that we’re hearing about that are taking over the marketplace today – you know, the terms like digitalization, more specifically the digital twin – these are high-level topics that also imply high levels of integration, or the desire to have high levels of integration. So, more specifically towards the digital twin and in the context of intelligence performance engineering, can you elaborate a bit on the concept of digitalization and why it is so important for machine builders?
Giulio Camauli: Yes, industrial machine manufacturers are currently under pressure to deliver faster, reliable and smarter machines. So, a comprehensive digital twin can improve the ability to simulate different characteristics of components and equipment more accurately. Digital threads can help automate the processes of sharing information between engineering teams, analyst production, test team and service engineers. This allows teams to evaluate the capability and limitation of product variations in the most efficient way. Better integration between designers, analysts and live data can enable OEMs to adopt intelligent performance engineering practices for improving performance while ensuring safety, reliability and cost-effectiveness.
Bill Butcher: Okay, thank you! That’s a good explanation. Appreciate that, Giulio! Rahul, at the start of this podcast you described – let me see if I got this correct – Intelligent Performance Engineering as an approach that improves reliability and addresses risk by building a set of highly accurate models that help predict product behavior during the lifecycle phases. And you have termed this approach Intelligent Performance Engineering. Can you help the listeners understand what exactly is Intelligence Performance Engineering or what makes it so special? And why is it a unique approach in the marketplace today?
Rahul Garg: One of the things that we have been looking at is understanding how customers are addressing the needs of their product engineering process, and what are some of the challenges that they have. Based on those issues that we have identified, there are three key areas that we are trying to focus on. The first one is what we call a multi-physics simulation which is basically giving them the ability to balance multiple attributes under one umbrella. This is one of the issues that many companies face where they may do a thermal analysis or a stress analysis, but then, how do you kind of figure out the stress and thermal analysis together? What happens when the heat rises and what’s the impact on the stability of that product? These are some of the multi-physics simulation angles that we are trying to bring in, addressing many needs that typically get addressed maybe one at a time.
The second one is integrated design and simulation. This is trying to look at how performance engineering can be addressed all the way from the front-end product design to the commissioning process and making sure that the models that are used are consistent with the high variability and number of changes that one is trying to address. You do not lose any information, so you can keep all the information in sync, which becomes very critical. And then, the last piece and not the least is closed-loop validation. So, this is where we are really trying to expand the test horizon and not just look at the testbed or the prototype as your test environment, but really look at your customers’ operations and your machine operations as the test environment. As you gain more information from the usage of the machine, you’re getting a real-time feed from the usage of the machine and using that as part of the test analysis. So, this is basically bringing in the closed loop validating your usage, testing, front-end simulation and design. Then it keeps all of that in sync to evaluate whether the upfront test parameters were right or wrong.
Bill Butcher: That’s wonderful! So, I think we’ll take a pause here and wrap up this first podcast. For the listeners, we want to let you know that we will be examining each one of those differentiators that Rahul just described in our next subsequent podcast. So, I’d like to thank both Rahul and Giulio for your insights today. It’s clearly apparent that, as industrial equipment becomes more complex, leading industrial OEMs must find a way to build more effective and trustworthy simulations.
Developing industrial machinery requires finding the best balance between productivity, accuracy, reliability and efficiency – and being able to do that digitally can only help you out-innovate your competition. So, please join us for our next podcast on Intelligence Performance Engineering, as we take a deeper dive into the benefits of multi-physics simulation and how this can be applied to machine builders. Have a great day!
Siemens Digital Industries Software drives the transformation to enable a digital enterprise where engineering, manufacturing and electronics design meet tomorrow.
Xcelerator, the comprehensive and integrated portfolio of software and services from Siemens Digital Industries Software, helps companies of all sizes create and leverage a comprehensive digital twin that provides organizations with new insights, opportunities and automation levels to drive innovation.
Listen to podcast01, podcast02 and podcast03 from this series.
Also, for more information on Siemens Digital Industries Software products and services, visit siemens.com/software or follow us on LinkedIn, Twitter, Facebook and Instagram.
Siemens Digital Industries Software – where today meets tomorrow.
About our experts:
Giulio Camauli – Simcenter Industry Solutions Manager at Siemens Digital Industries Software. Giulio has been with Siemens almost 30 years, covering many roles from application engineer for test solutions, to customer services manager responsible for strategic initiatives dealing with several key-customers in the Italian market. In his current role he contributes to the Industry campaigns and strongly collaborates with the different Simcenter sub-segments, marketing and regions to define broad and balanced Simcenter messaging and promotion.
Rahul Garg is the Vice President for Industrial Machinery & SMB Program, responsible for defining and delivering key strategic initiatives and solutions and global business development. He and his team are responsible for identifying key initiatives and developing solutions for the industry while working closely with industry leading customers and providing thought leadership on new and emerging issues faced by the machinery industry. Rahul’s experience and insight are derived from 25 year career delivering software-based solutions for product engineering and manufacturing innovation for the global manufacturing industry, spanning a career in R&D to program management, sales and P&L management and having focused exclusively on the industrial machinery and heavy equipment industry since 2007.