Digital twin implementation: steps to leverage the benefits
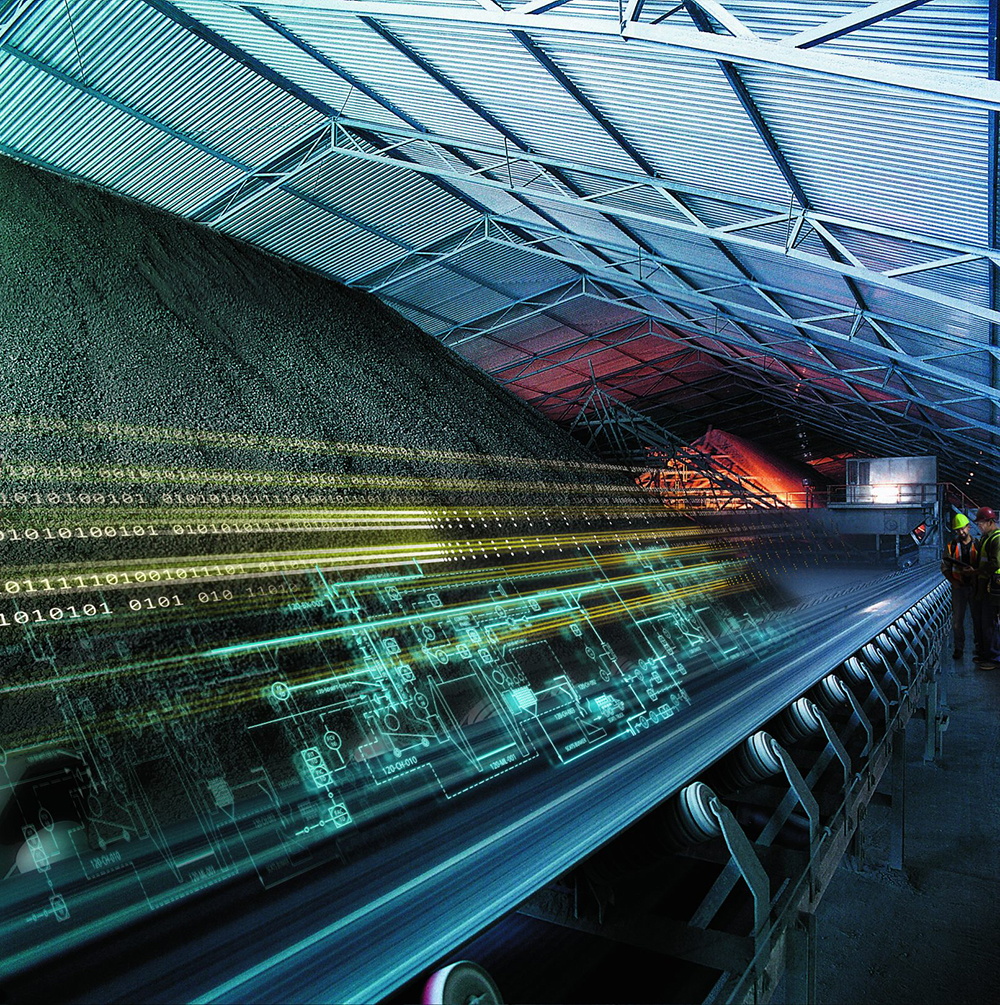
Digital twin implementation can be daunting. In my last blog about the digital twin, I mentioned how many manufacturing companies are hesitant to take advantage of it. Though they know the benefits of the digital twin, they are concerned it’s too complicated to integrate into their current system or too extensive and costly a process.
As a remedy, these manufacturers can leverage something called the dirty digital twin: a minimalist approach to using the digital twin. This method uses a reduced set of data to begin creating a smaller digital twin with a focus on one detail in your process versus the entire system.
The digital twin is usually perceived as 3D models, which includes both CAD and 3D simulations, with all the physics included. However, manufacturers could begin with digital twin implementation at a more pedestrian level, like using a simple calculation sheet and then moving upward to more sophisticated models. Given this scenario, a company can leverage the benefits of a digital twin without the complexities, time or high costs.
Focus on crucial areas when implementing a digital twin
The intricacies of manufacturing mean companies don’t have the time for trial and error as part of the process of improving efficiency – which is the key to maximising the time spent on engineering. The digital twin helps to stitch that process together through the use of 3D technology in other forms.
Balancing that effort is critical to moving forward by considering the value of your current status. Begin with what is already working and connecting for you, and then jump in from that point of production to proceed to next steps.
When implementing a digital twin, one worst case scenario is burning valuable time and effort by proceeding to build a full digital twin, only to discover in the short-term that it’s no longer an accurate model. Start small by creating 1D models in the form a spreadsheet – for example, how you can cut build-time in half – with 1D analysis being ten times faster than 3D models. So, don’t rely on 3D models exclusively, but use other methods (such as a spreadsheet) to build proposed models faster and smarter before proceeding to create more advanced simulation methods.
Digital twin implementation is more than simulation
Less complex models provide enhanced speed to implement early, crucial decisions before beginning full simulation to benefit an eventual system-wide model with higher intelligence. In turn, a connected collection of solved problems at a smaller, more specific scale can circumvent what could become more significant issues at the system level.
Every simulation company has thousands of models performing diverse functions to build the main product. By organising your data and connecting it to a spreadsheet, such as a CAD model via a 1D design, you enable a broader vision of your digital twin. This focused approach leads to a substantially improved scope in creating a larger-scale digital twin of your product.
This concludes part two in our series on defining and building a dirty digital twin. In part three, we’ll continue by discussing how to build your dirty digital twin.
About the author
Bruce Jackson is an account orchestrator for Siemens Digital Industries Software and works closely with aerospace and defence companies in the U.K. He has been working in the PLM and CAE space for more than 25 years and is currently working with companies across Europe to help them achieve productivity gains through digitalisation.