How digitalization enables multidisciplinary aerospace design
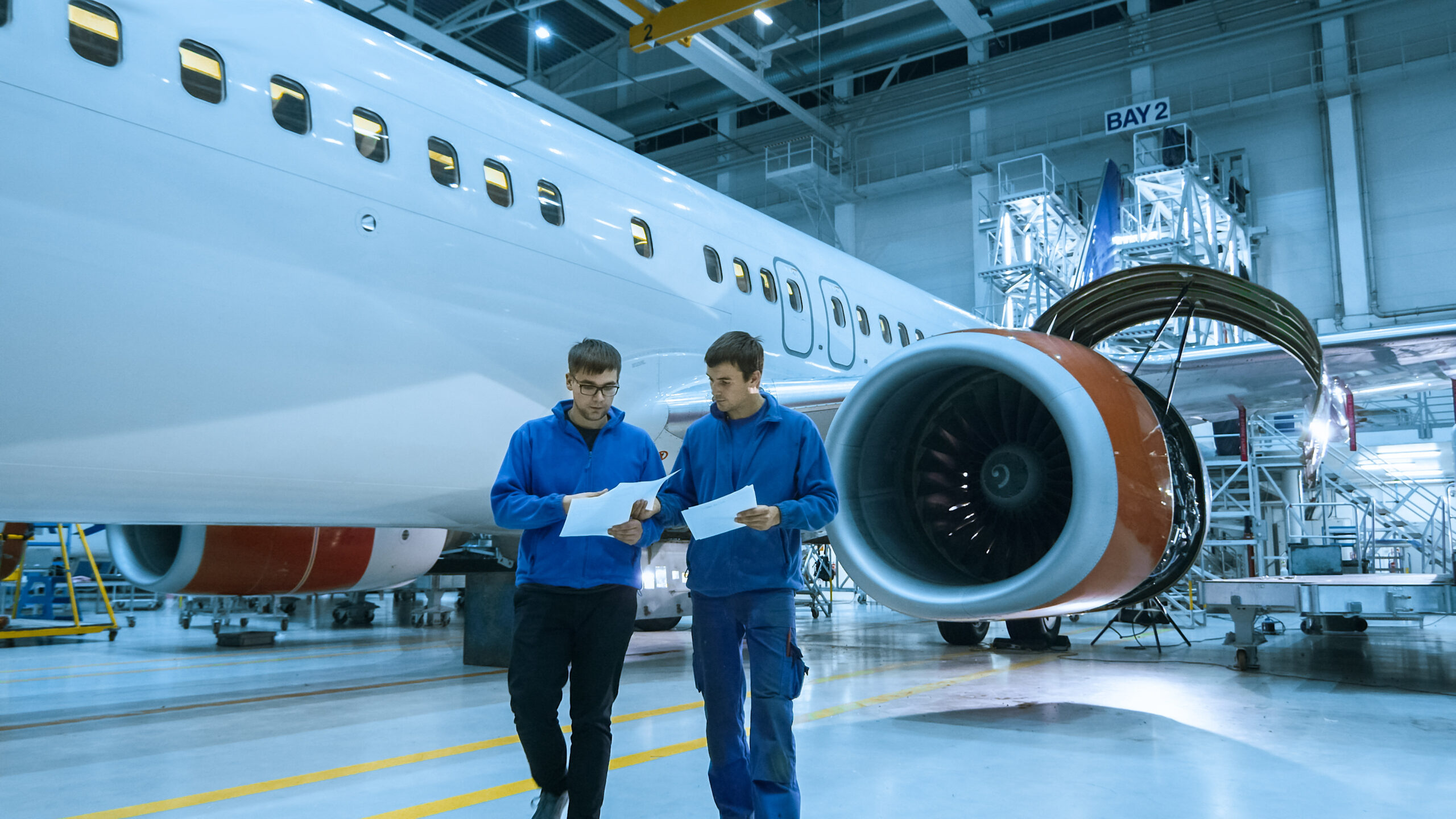
One of the most pressing challenges in the aerospace and defense (A&D) industry today is product complexity. After all, aircraft and spacecraft themselves are products integrating some of the most advanced systems and technologies available. As new innovations are added to meet today’s demands in the industry, ensuring they work together as a whole becomes more difficult, especially when using disconnected design processes. A&D companies will need to explore multidisciplinary approaches to design if they want to establish themselves as industry leaders.
They key to achieving multidisciplinary design is digitalization. This is the subject in a recent webinar hosted by Aviation Week and sponsored by Siemens, featuring Anthony Nicoli, Global Director Aerospace & Defense for Siemens Digital Industries Software, Thierry Olbrechts, Director of Aerospace and Defense Industries Simcenter Solutions, and John O’Connor, Director of Aerospace Product and Management.
Together, they discuss how A&D companies can leverage tools such as the digital twin and digital threads to bridge engineering teams from across the product lifecycle and overcome the increasing complexity pervading the industry.
Complexity and siloed engineering
Much of the product complexity in A&D is derived from the integration of new technologies and systems into aerospace designs. For example, many designs for sustainable aircraft aim to utilize propulsion systems different from typical fossil fuel combustion engines, such as batteries or hydrogen. In addition to making an entirely new propulsion system, engineers must also consider how the thermal dynamics of their new system affects the aircraft’s other systems, including the mechanical system, electronics, and more.
Working in these new complex systems is challenging enough, but the problem worsens when the design teams responsible for these systems are siloed, working in isolation from each other during the design process. This lack of visibility and communication between teams can lead to reduced productivity, errors, and delays, increasing the time it takes to get a new aircraft or spacecraft out to mark it, as well as the risk of the project getting cancelled entirely. Allowing design teams easy access to each other’s data during the design process can increase the chances of the final product working the first time.
Overcoming complexity with digitalization
As explained in the webinar by Anthony, Thierry, and John, companies can reduce the effect of product complexity in A&D and dismantle engineering silos is leveraging key technologies brough by digitalization.
The digital twin, for example, is a vital tool that can help engineers design and optimize their systems, no matter how complex they might be. As the virtual representation of the product, the digital twin offers engineers a way to build their product and its systems digitally before ever building them physically. They can then test their digital twin with physics-based simulations and optimize their designs based on their performance. By enabling key insights to be gained earlier in the design process, the digital twin gives engineers have more time to manage product complexity, saving resources and reducing potential rework down the line.
Yet the digital twin alone cannot solve engineering silos. This is where digital threads come into play. Digital threads work with the digital twin by creating a consistent, collaborative platform between engineering domains that helps improve traceability and connection. They provide an authoritative source of truth where engineers can find real-time data from other teams and use it to optimize their systems accordingly. Not only can digital threads improve communication in design, however, but they can also do so for anywhere in the product lifecycle, from manufacturing to service, to ensure everyone has access to the most up-to-date information on a product.
Holistic aerospace engineering
By leveraging elements of digitalization such as the digital twin and digital threads, A&D companies can build that holistic, multidisciplinary approach to their engineering processes, making it easier to integrate new electronics, software, propulsion, and other innovations into their designs. Additionally, connecting high-level data architecture across all design tools helps connect otherwise disparate teams and domains across the product lifecycle, reducing the chances of miscommunications that can lead to errors and delays.
Digitalization presents numerous opportunities for companies to connect their people and processes, allowing the next generation of aircraft and spacecraft to take off on time.
For more information on digitalization and multidisciplinary aerospace design, be sure to check out the webinar from Aviation Week.
Siemens Digital Industries Software helps organizations of all sizes digitally transform using software, hardware and services from the Siemens Xcelerator business platform. Siemens’ software and the comprehensive digital twin enable companies to optimize their design, engineering and manufacturing processes to turn today’s ideas into the sustainable products of the future. From chips to entire systems, from product to process, across all industries. Siemens Digital Industries Software – Accelerating transformation.