Digital twin-enabled robotics
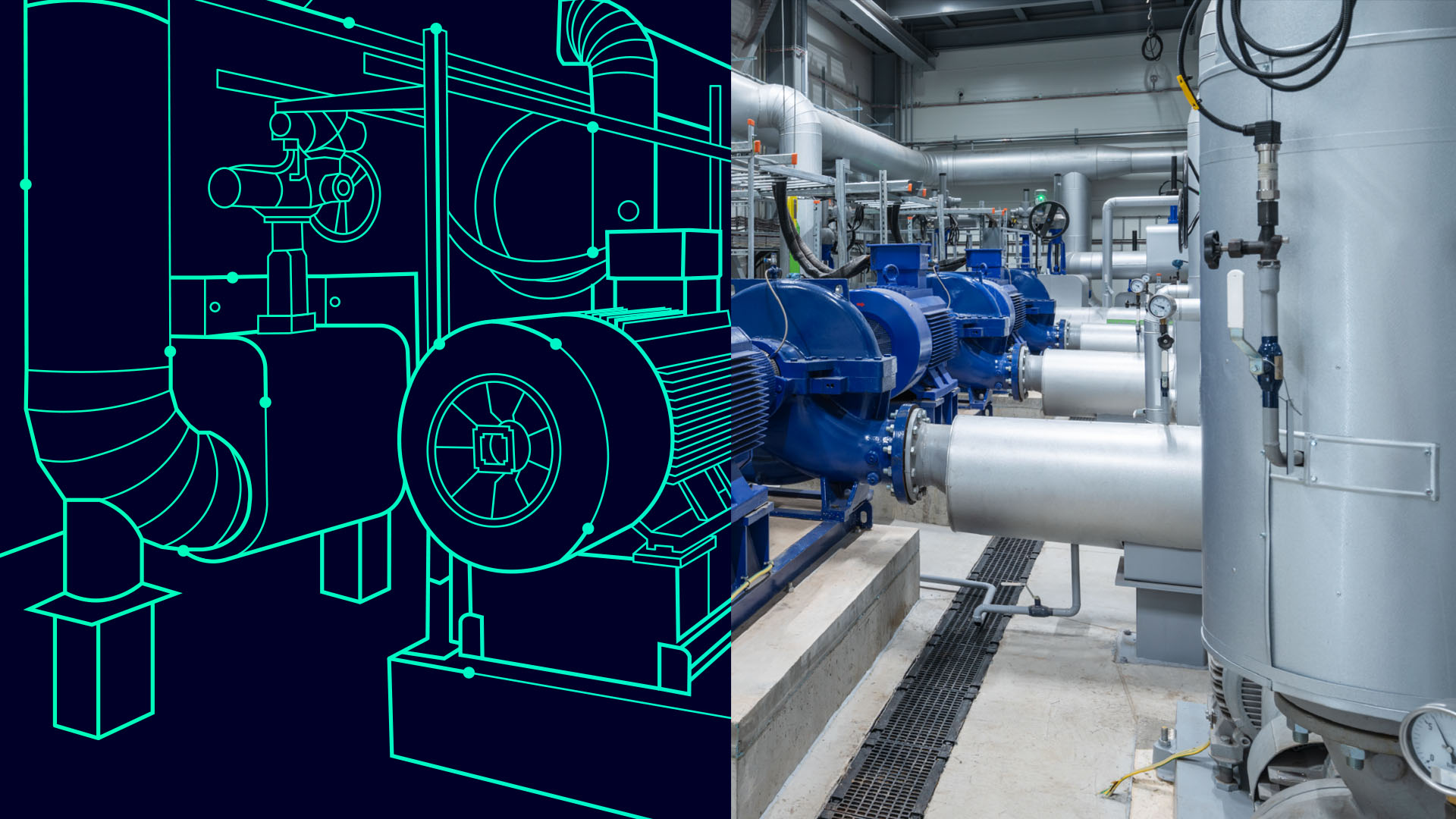
When most think about the digital twin, the first thing that comes to mind is product prototype simulation. Siemens has extended this concept to include the entire product lifecycle, including the factory and the equipment within it; after all, the factory is a highly complex product at the end of the day. This digital twin that emulates production systems is known as the comprehensive digital twin (cDT) for the factory.
Crafting the cDT has become even more critical as the production landscape transforms into a mix of low-volume and high product. The factory cDT allows rapid iteration of production processes and optimization with minimal investment through combining the digital and real world thereby enabling manufacturers to virtually commission factory systems.
Automation and the digital twin
When an organization has a seamless flow of data across teams and processes (aka, digital threads) and leverage them with the cDT, it can use them to evaluate traditional automation equipment alongside complex robotic systems and humans. With digital threads and the cDT, manufacturers can do a complete and holistic orchestration at multiple levels – of each factory, line, cell, robot, product, and even human—to analyze how they interact in harmony across the entire line.
Guaranteeing harmony requires a tight handshake between the automation systems, robots, and humans. And this handshake is supported by the cDT which helps robots become more adaptable and easier to program. When customers require more flexibility in their facilities, they often move to flexible, reconfigurable robots. Each robot has its own programming tools, which has led Siemens to develop robot programming libraries, so that different robots can be set up and tested with very minimal robot manufacturer-specific knowledge.
And manufacturers can leverage cDT behavioral models beyond machines and processes. Using the cDT, organizations can optimize and validate human interactions and processes. The cDT incorporates physics-based human models, enabling companies to simulate for safety by optimizing tasks and working environments; illustrating how automation, robots, and humans can coexist during processes that require all three.
Going beyond the physical
The cDT has the ability to unlock a manufacturing plant’s true potential. Along with software-defined automation and AI, the cDT move the industry towards creating the industrial metaverse. The industrial metaverse is the concept of a digital world to mirror and simulate real machines and factories; it is a digital world that enables users to interact with virtual representations of physical assets in real-time. It will help organizations break distance barriers, stimulate collaboration, and understand problems and processes better to find the most optimal solutions. The industrial metaverse can optimize processes and drive sustainable practices, ultimately shaping the future beyond simulation.
Within the industrial metaverse, factory workers can perform analysis of the scene and simulation and collaborate while fully immersed using VR hardware to perform real-time computational calibration for sub-millimeter accuracy, leading to faster alignment of manufacturing cells, increased production quality, shorter physical commissioning times, and easier collaboration and change management.
Today, Siemens continues to advance the industrial metaverse by offering three core building-block technologies – Industrial AI, the digital twin, software-defined automation – and our platform, Siemens Xcelerator. Siemens also has the unique position where we not only build our software and automation but also use it in our own more than 250 factories globally and work closely with top players to drive continuous improvements in our own software and hardware solutions.
Siemens Digital Industries Software helps organizations of all sizes digitally transform using software, hardware and services from the Siemens Xcelerator business platform. Siemens’ software and the comprehensive digital twin enable companies to optimize their design, engineering and manufacturing processes to turn today’s ideas into the sustainable products of the future. From chips to entire systems, from product to process, across all industries. Siemens Digital Industries Software – Accelerating transformation.