The Importance of Simulation for Successful Space Missions
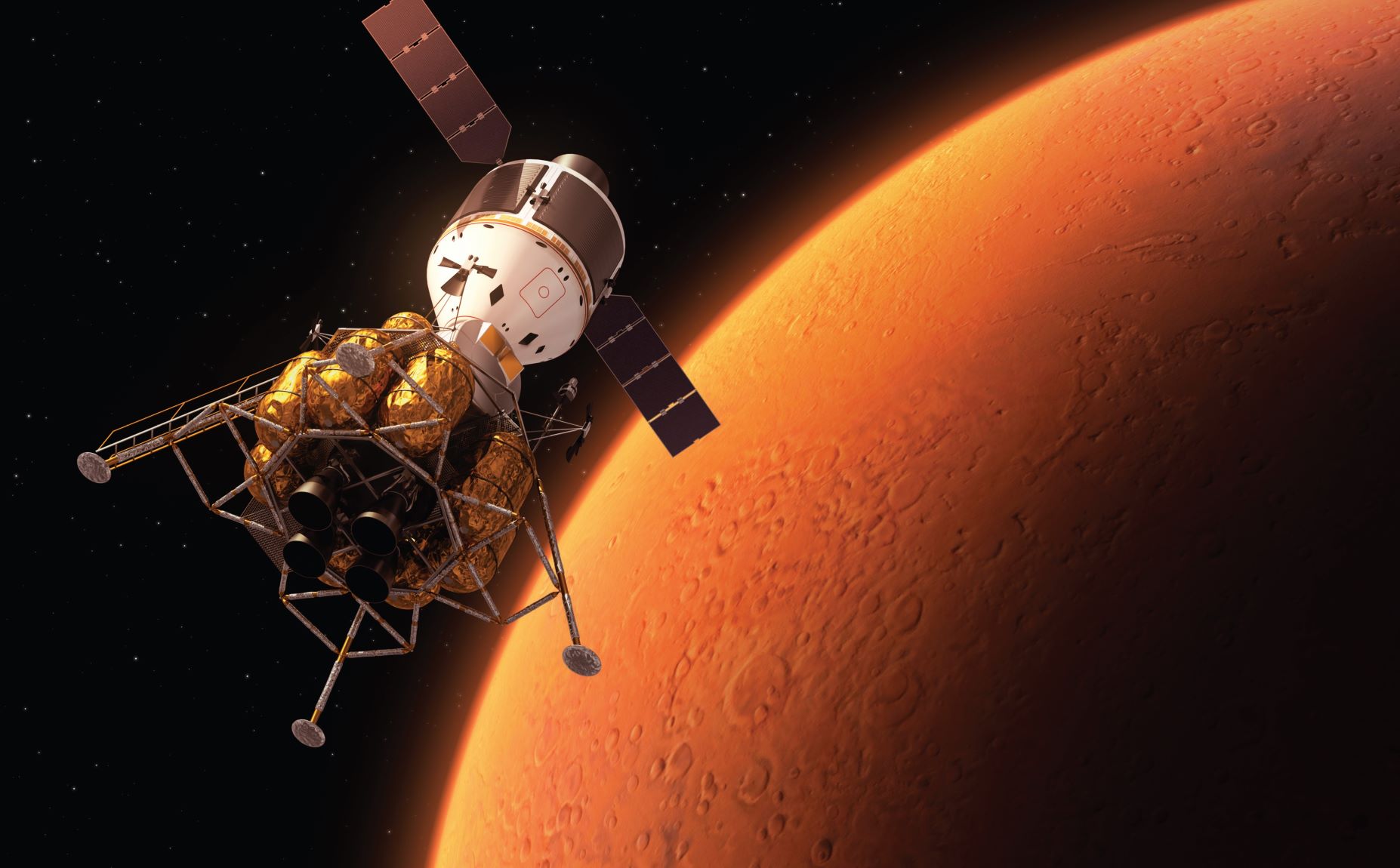
To say the space industry has been taking off in recent years would be an understatement. The costs of rocket launches have continued to decrease, key players in both the public and private sectors are achieving milestones in spacecraft technology, and new startups offer to inject new momentum into the race. The odds of expanding human presence beyond Earth’s orbit in the coming decades has never been greater.
Despite all these initiatives, the space is still an industry where mission failure can come with great consequences, especially if more humans are expected to be aboard future spacecraft. A lot of complex engineering goes into making the rockets that send satellites, scientific instruments, and more into some of the most extreme physical conditions in the universe, often to where nobody can fix an issue if something goes wrong.
That is why it is imperative companies and space agencies fully leverage simulation in their engineering processes to optimize their spacecraft designs and mitigate risks as early as possible.
Tackling complex design
Spacecraft are some of the most impressive, complex products of engineering devised by humans, consisting of multiple systems that incorporate design decisions and principles across engineering disciplines. If designed improperly, the interaction between these disciplines can increase failure risk.
Consider the fueling system of a rocket as an example. If using a nonsolid rocket fuel, the fuel pumps must transfer its fuel to the rocket’s tanks under cryogenic conditions and high pressure in order to keep the oxidizer and fuel in a liquid state. Not only are there thermal considerations to account for, but engineers must also ensure all impacted systems and components have the structural integrity to operate in such temperatures and pressures. These systems need to contend with such conditions while simultaneously transferring the maximum amount of fuel in a safe, efficient manner.
Designing spacecraft systems that successfully balance these goals can be significantly easier with digital tools aided by simulation. Simulations capable of model-based reliability, availability, and maintainability solutions can model an entire system, enabling engineers to test and optimize individual components and subsystems to work better together. Additionally, different kinds of simulation can be carried out, including thermal, structural, and fluid dynamics analyses, giving engineers insight into every aspect of their designs.
Preparing for launch
Of course, the real challenges with building successful spacecraft come after leaving the launchpad. The launch process itself subjects the spacecraft to extreme temperatures from ignition, as well as immense acoustic vibrations—up to 146 decibels or higher—risk structural damage and jeopardizing sensitive equipment such as solar panels and antennae.
The problems only rise as the spacecraft leaves the atmosphere for outer space proper. Parts of the spacecraft facing the sun will experience extreme heat, while parts facing away from the sun will experience near absolute zero. All the while, consistent bombardments of solar radiation, which not only risk damaging equipment, but can also be detrimental to the health of human passengers. There is no way to rescue a spacecraft once it ventures too far from Earth (yet), so the solutions to these conditions must be found on the ground first.
Once again, simulation can assist engineers in finding those solutions far earlier in the design process. For example, to account for the extreme temperature variations a spacecraft will experience in space, engineers can simulate those thermal conditions to ensure low and uniform temperature distribution across a spacecrafts and its systems. They can then make changes to the spacecraft’s design, as well as analyze the effects of other strategies such as rotating the craft to evenly distribute exposure to the sun’s heat.
Simulation can also support physical testing that prepares equipment and systems for outer space conditions with help from the comprehensive digital twin, a multi-physics virtual representation of a product or process. Engineers can build a digital twin of a test they conduct physically, simulating the test conditions virtually while being able to introduce new conditions that are not physically replicated. The data gathered virtually can be used to supplement the physical data, giving engineers well-rounded insights of their product and better preparing it for the harshness of space.
Building successful spacecraft will need to address more challenges than those discussed, but one thing that is certain is simulation’s role in overcoming them. Simulation has already been utilized by space agencies to explore these challenges to great effect. It will only become more crucial to stay ahead in an increasingly crowded field and spread humanity beyond Earth’s gravity well.
Read more on simulation’s role in ensuring space mission success in this white paper.
Siemens Digital Industries Software helps organizations of all sizes digitally transform using software, hardware and services from the Siemens Xcelerator business platform. Siemens’ software and the comprehensive digital twin enable companies to optimize their design, engineering and manufacturing processes to turn today’s ideas into the sustainable products of the future. From chips to entire systems, from product to process, across all industries. Siemens Digital Industries Software – Accelerating transformation.