Sustainability in electronics and semiconductors episode 2 transcript
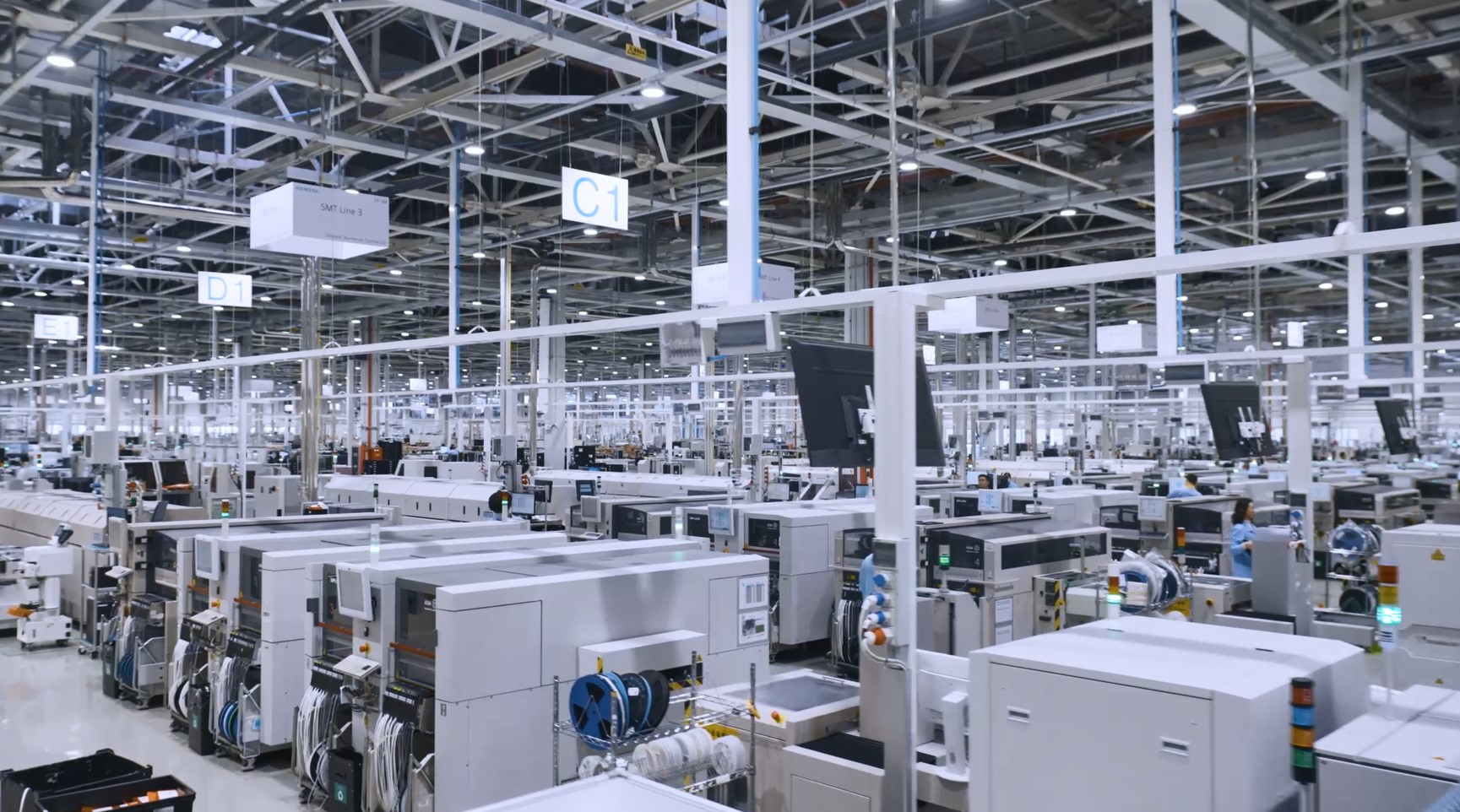
Maria Mosto: Hello, and welcome to part 2 of our discussion on sustainability in the electronics and semiconductor industries. I’m Maria Mosto, your host and moderator for today’s session. Today, we continue our conversation between Alan Porter, VP of our electronics industry that Siemens and Michael Munsey, VP of semiconductor industry at Siemens.
Michael, you touched earlier on digital technologies such as the digital twin. How would automation and simulation tools make semiconductor production more environmentally friendly? How would how would that help?
Michael Munsey: If you look at where we’re at today, the semiconductor industry has largely been driven by the digital twin, even though in the past they may not have referred to it as a digital twin. The nature of doing the semiconductor design has always been virtual.
You don’t realize that semi directed device into eventually gets to manufacturing, so the fact that we work in a virtual environment already today on the design front allows us to create that environment to be able to produce lower power devices.
And again, it’s a matter of being able to have the tools in the libraries associated with that to be able to do very detailed analysis of power consumption and look at the functionality that ship and make decisions on how to reduce the power, whether that is through design changes by moving more things to software from hardware if possible, and really make those decision.
That’s very much the way things have been going today and the way designs have been done today, but there is an imperative on the companies that provide EDA tools to really allow for the ability to do drastic part reduction in the designs. Engineers have to meet a schedule, and if they’re given a requirement or a spec that your chip could only consume so much power, they’ll do everything possible to meet that spec. But if they’re given tools and methodologies that allow them to exceed that and still allow them to stay within their schedules, that will even go even further to helping us reduce the power that semiconductor devices look at.
We’re already developing that technology and doing a very good job in that space, and we could continue to improve and make improvements on the way we do that now on the fab side of things, this is where there’s a lot of new opportunities for us. As I mentioned before, semiconductor companies in the past have basically built their new fab the way that they built their own fab because it’s something works. You might as well keep working and doing it the same way we just signed a MAU with Intel to help them build the digital twin of their new fabs.
This is a new concept in the in the industry because by being able to build that digital twin of that fab will allow companies to make a lot of optimizations for sustainability moving forward by understanding in the virtual world before a brick has ever been laid for the fab to understand what the power requirements, what the water requirements, what the HVAC requirements are all going to be of that fab and be about optimize that fab moving forward.
And then the next logical step after that is working with the semiconductor equipment manufacturers and having them be able to provide digital twins of their semiconductor equipment into the fab.
Now we can start looking at performing optimizations all the way from design through manufacturing, all in the virtual world. We’re able to be able to dial in the performance requirements and everything else in the virtual world without going through the way we’ve done it in the past, which is optimized the design, hand it off the manufacturing and then ramp yield, which itself is very wasteful when you think about the number of wafers with low yield and the amount of energy and the amount of chemicals that went into that all to be scrapped as we start to ramp yield, being able to do this all in the virtual environment, we’ll definitely improve things for the better and then we could take real time information from the fab and drive that back into the design shift left and start to produce better libraries and better models.
We could do a better job of actually designing with real time fabric from information to optimize the design even better and be able to produce more often designs. So it’s really about taking where we are today and improving that and then extending it throughout the entire manufacturing process now and creating the digital twin of the entire design and manufacturing for semiconductors to provide those types of optimizations moving forward.
Maria Mosto: Right. My next question really relates to taking that power consumption and energy consumption is such a large part of sustainability. This question is really for the both of you. How are companies designing power intensive products like AI chips going to be addressing energy consumption? It’s not just at the point where the chips are me, but it’s obviously downstream when they’re actually operating in the systems of products.
Michael Munsey: Yeah. This this is a real problem right now there’s there was a study recently that said within the next five years, the amount of electricity needed to power a data center with the latest AI technology would be the equivalent of, at least in the US of the US having a build 47 new nuclear power reactors to be able to supply that. This is going to be a huge problem, and we don’t have a grid that will be able to support this move forward.
There’s going to have to be changes in the actual development of devices to make them much more power efficient and a lot goes into what I said before with the ability to capitalize on advanced technologies in terms of packaging to reduce the power.
But there are lots going to have to go into looking at things at the system level and the software and the semiconductors together. And the workload of the software running on those AI devices. That’s just looking at it from the semiconductor point of view.
These devices are going to go into racks of computers that are going into these systems, and I think that even at the electronics point of view, things are going to have to happen.
Alan Porter: Oh yeah. I mean in terms of when you have that, that huge power consumption, you’re now talking about cooling systems. At the data center level also in the rack level at the board level, all to be able to handle this amount of power. You have the cooling systems; you have the power that that’s driving the systems and the cooling systems and then you have all the chemicals and or water that that’s required for that as well.
As that demand grows and the amount of data centers required grows, you’re looking at more and more stress on an already difficult problem.
I mean, our customers are now even looking at data centers in the ocean to be utilized both from a cooling perspective and also drawing power from tides of all things.
Maria Mosto: This question is for both of you as well. Knowing that large players in the industries have the power to set environmental standards and what’s the agreement and consistency for sustainability metrics and models, and does every consumer company have different KPI?
Michael Munsey: If you look at all the companies, all of them have some initiative right now for some net 0 carbon footprint moving forward, right? And the lot of them have been targeting 2030. Whether they all meet that or not, it’s still yet to be determined, but this is this is the perfect example of companies are trying to do the right things.
I wouldn’t just say it’s just the large players in the industries doing it. It’s also up to the consumers, right? The consumers can make choices on what products they ultimately buy from, which companies based on what their sustainability standards are. And it’s not only the workplace in the industries having the initiatives and driving towards these initiatives, I think it’s a matter of also the consumers holding those companies accountable for their own sustainability standards moving forward.
Alan Porter: Yeah, it’s very market driven and I think that what also comes into play from the metrics and models standpoint is the compliance issues from a localized standpoint, are there carbon tokens available to kind of push the envelope here.
Countries can try to either enforce sustainability aspects or they can reward for sustainability aspects, and this may help the SMBs or the startups even more than the OEMs. But it’s still a factor in determining what? What’s being done from this perspective?
Maria Mosto: Thanks, Alan and Michael for noting that startups can definitely participate in these things. It’s not just as you say, the large players in the industry because it affects all.
At the end of the day, how is Siemens really contributing to helping our customers in the industry meet these sustainability goals? Michael, maybe we could start with you, if that’s ok?
Michael Munsey: Yes. So to start off with it, Siemens, we have the SiGreen initiative and that’s been very successful so far in a number of industries and we’re bringing it now to the semiconductor and electronics industry and just to give everybody an understanding of a SiGreen, in the past the way companies would measure their sustainability would be in a way of looking at what they’ve done in the past in terms of manufacturing and manufacturing performance and using that to set up a set of metrics to improve upon. And then basically iterate across that to improve those metrics.
What makes SiGreen different is that we’re actually dealing with real time data, and we have the ability to measure manufacturing in real time and make improvements, while the actual manufacturing’s happening. It allows us to create this closed loop that allows for instantaneous feedback and instantaneous improvement of manufacturing processes to drive towards the goals that we have in terms of sustainability.
Now, of course, what’s important to this is how do you manage all this data that you collecting, and it fits right in with the digital twin, right? Siemens has a comprehensive digital twin and when you talk about comprehensive, we have to look across all the systems and the systems are software and semiconductors and electronics and mechanical aspects that make up the entire system and you need that comprehensive digital twin to be able to map all of this data that we’re collecting against the predictions of the model that we had to begin with. It’s a combination of real time feedback and data gathering and be able to put it into a data model that matches the entire system that we’re trying to optimize.
Alan Porter: Yeah. Michael mentioned the importance of managing that real time data and that that’s where Teamcenter for manufacturing comes into play and then extending Teamcenter all the way through the design world at the electronic system level. You’re connecting the dots in real time and being able to manage that information cross domain.
What that does is allow you to, if that information left to predictive analysis and also it allows you to collaborate in a more efficient manner and from a design perspective we have supply frame where we’re able to grab that real time information for components and we can make intelligence decisions for the BOMs and really update the BOMs and be able to act on our sustainability metrics from at the design level.
When we’re in the design level with our expedition tools, designing the PCB’s for the system, we can take that information and do the right things from a sustainability perspective, for example, we can choose components that may have a lower carbon footprint or are more thermally tolerant, you need less cooling or perhaps less power. I think there’s a lot of different areas where this comes into play and the digital twin and Siemens has the portfolio across the different domains to realize that.
Maria Mosto: Thank you. This has been a really enlightening conversation. Alan and Michael, thank you both for joining me to discuss how the electronics and semiconductor industries are really transforming their design and operational processes to lessen the environmental impact. Thank you for listening. And we really hope to see you back here soon to continue exploring how these industries are tackling sustainability.