Designing remanufacture into sustainable products
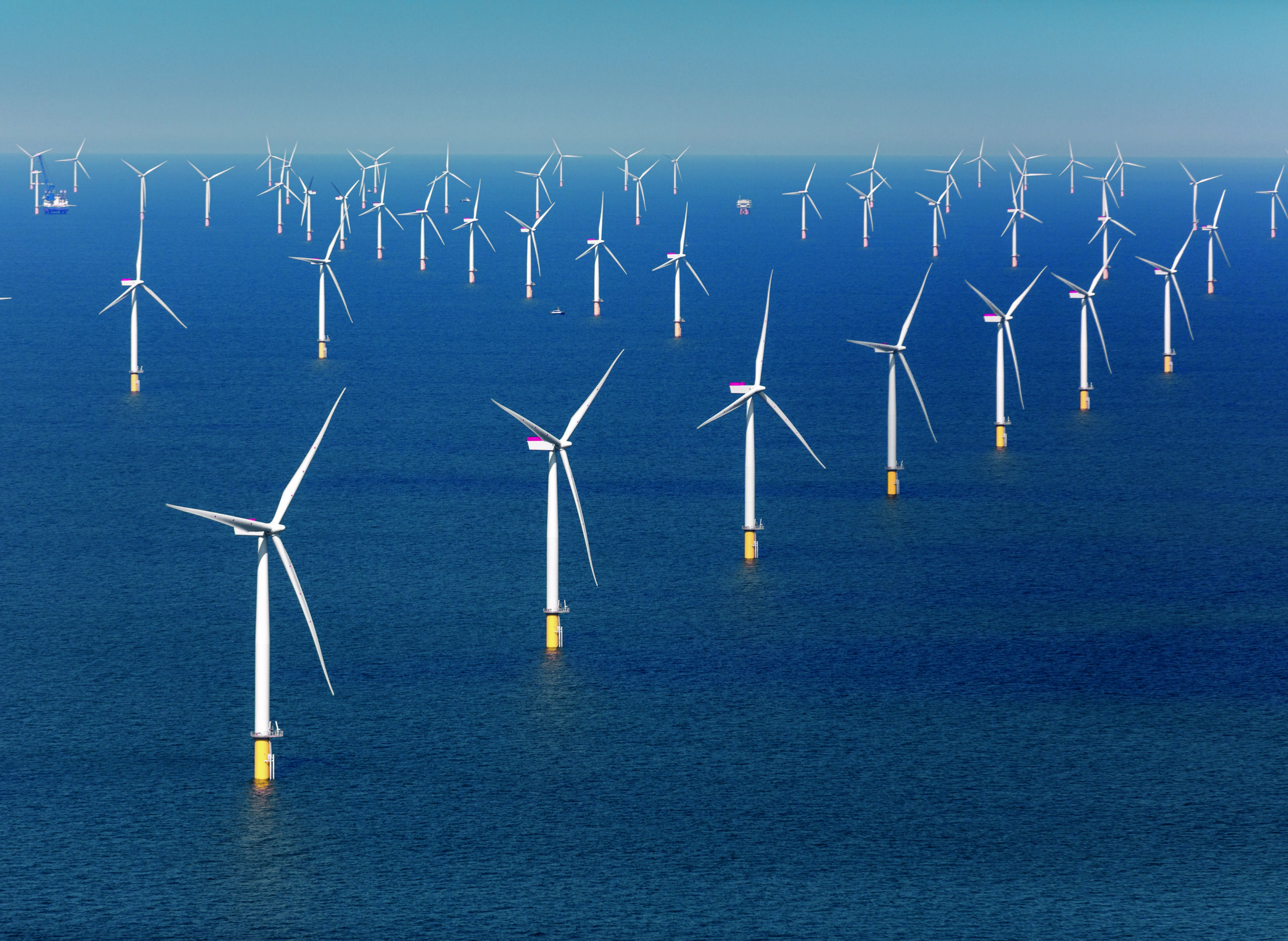
Waste is a huge problem around the world. It takes many different forms, in many different industries. But not all waste is equal. Some is well and truly unusable for its intended purpose and needs to be downcycled or composted into other useable forms. But many of the materials produced around the world can be reused, remanufactured, or recycled to remove it from the waste stream. The challenge is that only a fraction of the materials that can be diverted from becoming waste, do not do so on a regular basis – only around 13%.
Wind turbines are a great example of this need. While they can contribute to the decarbonization of electrical grids, they are still energy and material intensive products. The massive blades that convert the wind’s kinetic energy into electrical energy cannot do so without large gearing ratios to also convert the high torque at the blades to a high rotational velocity in the generator. Even with the best digital tools to design the gearing ratios and material properties to extend part longevity, wear is an inevitability. Keeping the turbine running optimally often means replacing the gears as the teeth wear down and energy is not as easily transferred internally.
Our customer Chiron Group is trying to change this status quo with an innovative business plan and set of technologies. Rather than rip out the gearing system and send it off to be melted down into another product, they are remanufacturing the gears with Additive Manufacturing (AM) technologies. When the gears become worn from constant use offshore in saltwater environments, their process for repair kicks into action.
As these gears require high precision, an important first step is understanding what geometry the gear will need to get back to day one quality. By using digital twin technology to compare the original shape and the degraded form, Chiron is able to remove the worn teeth and determine the required remanufacturing processes. Many scenarios for how to integrate the new printed teeth and improvements that could be made to the design are run through digital tests to prevent further waste from incorrect assumptions. Once the process is understood in the digital world, the AM process takes over to rebuild the teeth on the gears. Layer by layer, the teeth are built up based on the appropriate geometry for the teeth. And as AM has industrialized over the years, this process gets closer to deployment quality – minimizing the amount of material that needs to be removed during any finishing operations.
Given the size of these gears for offshore wind installations, the lead times for all-out replacement can be very lengthy. But by remanufacturing gears, the Chiron Group is saving time and costs. The replaced gears are also 60 to 85% more energy efficient compared to recycling and re-ordering. Breaking down a product every time it needs repair is not a sustainable endeavor, and the Chiron Group is proving that an alternative is possible today.
For more information on the Chiron Group, please check out our website.
Siemens Digital Industries (DI) is a leading innovator in automation and digitalization. In close cooperation with its partners and customers, DI is the driving force for the digital transformation in the process and manufacturing industries. With its Digital Enterprise portfolio, Siemens provides companies of all sizes with all the necessary products, along with consistent solutions and services for the integration and digitalization of the entire value chain. Optimized for the specific requirements of individual industries, this unique portfolio enables customers to enhance their productivity and flexibility. DI continuously extends its portfolio to include innovations and the integration of future-oriented technologies. Siemens Digital Industries, with its headquarters in Nuremberg, has a workforce of around 72,000 people worldwide.
For more information on Siemens Digital Industries products and services, follow us on LinkedIn, Facebook, Twitter, and YouTube.