Guaranteeing long-term product excellence with service lifecycle analytics
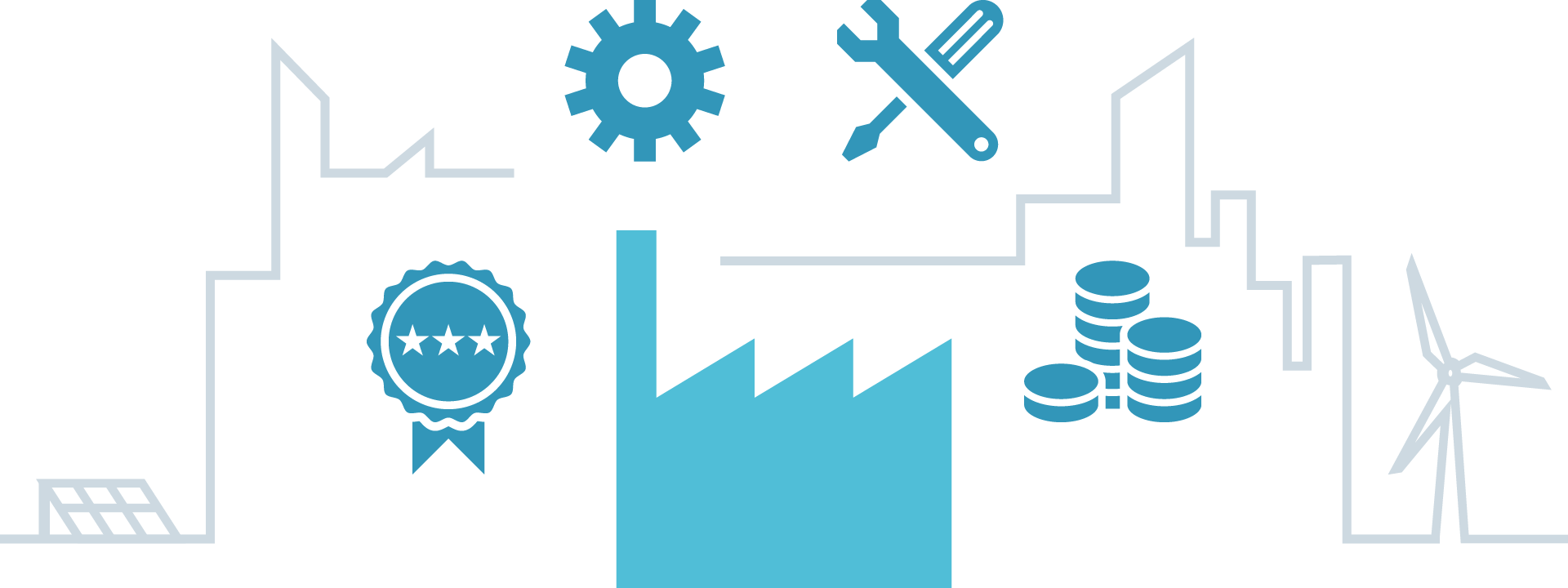
As the manufacturing landscape becomes more complex, so do the machines on the shop floor. While newer machines help factories become more efficient, flexible, and environmentally friendly, their problems may be more difficult to diagnosis compared to simpler machines. Integrating CRM and PLM software enables manufacturers to enrich their service capabilities through enhancing service lifecycle analytics.
In turn, SLA solutions can help identify performance issues with the added benefits of increasing revenues and bolstering resilience. On top of new revenue service offerings, machine builders can secure long-term product excellence and help make the next generation of machines even better.
Proactive planning for service excellence
To ensure comprehensive service excellence, key service integration must be considered early on. Addressing service needs during the design phase enables manufacturers to better control and predict how, when, and where machines will be serviced.
Ultimately, taking initiative during the design phase will improve machine maintainability while mitigating the impact of unplanned downtime. Organizations can utilize service data collected through CRM software to properly manage products and processes in this phase. CRM supplies a unified environment by tracking customer interactions, including customer contracts, warranties, as well as past and current cases.
Combining these capabilities with PLM, which manages when the machine should be serviced during the design, engineering, and manufacturing phases, will enable organizations to establish closed loop service. Leveraging accurate documentation and service histories, technicians can make quick assessments and diagnoses before recommending solutions, enabling them to potentially service the machines in a single shot.
Benefits of service excellence
Properly utilizing SLA solutions can optimize uptimes and downtimes, significantly bolster machine service accuracy, and drive continuous service improvements. Companies that employ SLA solutions have seen:
- Maintenance times reduced by 30%
- Error detection times decreased by 66%
- Technician productivity increased by 30%
- Technician utilization improved by 85%
Overall, most organizations report creating new revenue streams through implementing comprehensive maintenance software, with 60% of companies saying that low-code platforms have increased their revenue. Furthermore, 86% have seen increases in profitability, with 40% to increase spending on similar solutions in the next fiscal year.
Machine builders are especially predisposed to see gains from SLA solutions powered by CRM and PLM. Through improving maintainability, traceability, and predictability, machine builders can ensure high-quality repairs, maintenance, and upgrades for their customers.
Not only that, when these tools are combined with AI and simulation technologies, machine builders can access for data than ever before. This fuels continuous improvements to the machine design and support processes. Unlocking crucial information leads to machines that are easier to maintain and more sustainable.
Becoming a reliable service partner
Modern machines need modern solutions. Fusing CRM and PLM revolutionizes SLA in the industrial machinery industry, empowering machine builders to optimize service delivery and improve efficiency. Companies can take control of machine uptime and downtimes through addressing service needs in the design phase. Powered by data collected through CRM and PLM, organizations can make necessary changes to their products and processes throughout the machine’s entire lifecycle.
Additionally, the integration of data helps technicians become more knowledgeable and accurate, increasing both error detection and productivity. Armed with information and the right digital tool, technicians could potentially properly service machines in one go.
With the machine data properly homogenized and utilized, manufacturers can guarantee closed loop service, which will give engineers new insights into design changes for future machines. Enhanced SLA ultimately leads to more reliable machines, lower maintenance costs, and higher customer satisfaction; in essence, it allows machine builders to diversify their revenue streams and ensure resilience no matter the industry conditions.
Siemens Digital Industries Software helps organizations of all sizes digitally transform using software, hardware and services from the Siemens Xcelerator business platform. Siemens’ software and the comprehensive digital twin enable companies to optimize their design, engineering and manufacturing processes to turn today’s ideas into the sustainable products of the future. From chips to entire systems, from product to process, across all industries. Siemens Digital Industries Software – Accelerating transformation.