Performing model-based mission assurance for spacecraft with the digital twin
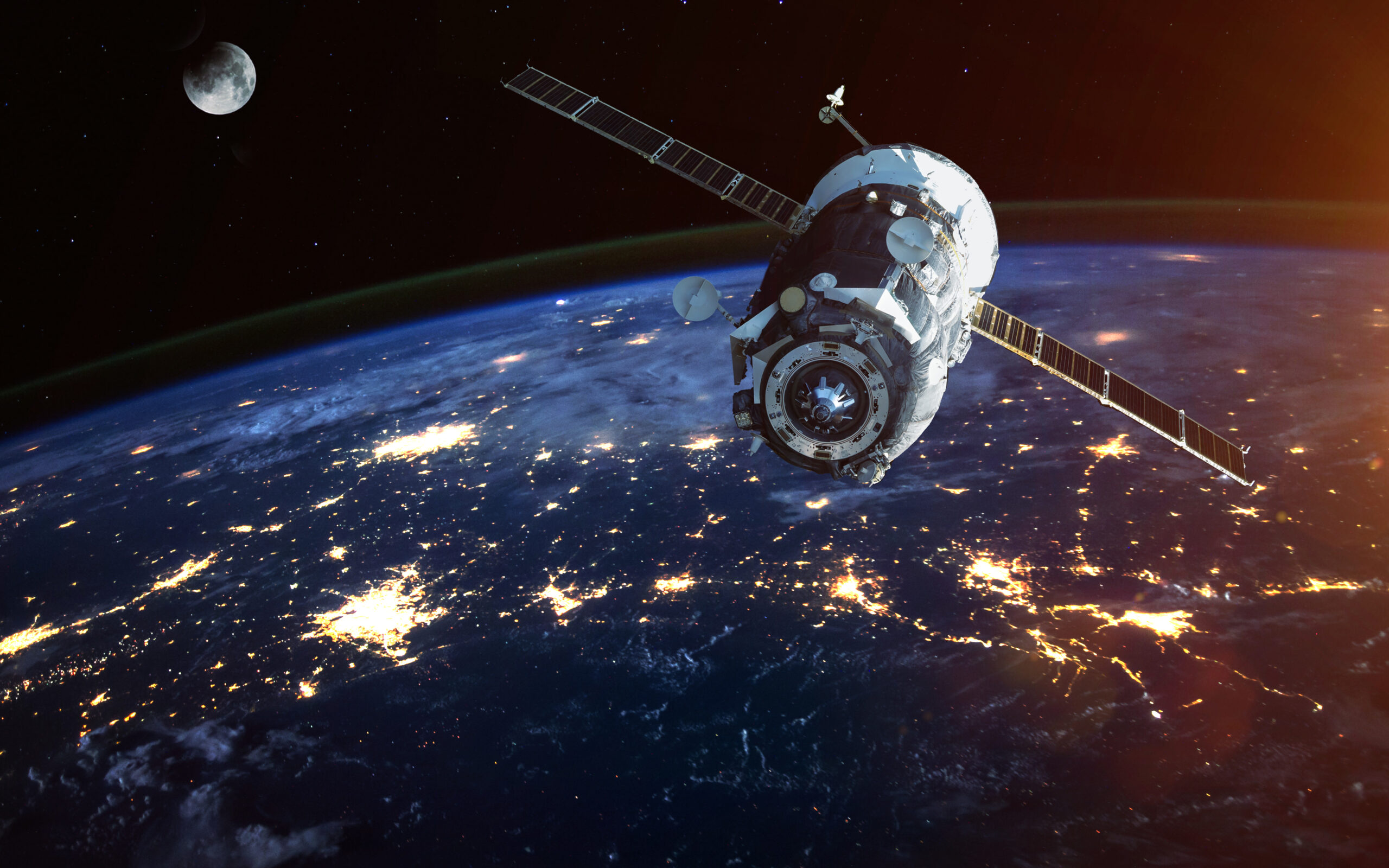
Mission assurance, the process of identifying and mitigating risks for mission success, is one of the most critical stages in the development of spacecraft and can determine whether they complete their missions. However, the process is too often marred by manual, document-based approaches that lead to siloed domains, slowing down the process and harming the accuracy of analyses. Space agencies can overcome these issues by creating a digital twin. New, model-based approaches pave the way toward building a reliable, unified mission assurance process.
The importance of mission assurance
Fixing a spacecraft in deep space is exceedingly difficult, even impossible, if something were to happen to it mid-mission. Having a reliable mission assurance process early on is crucial to avoid that scenario in the first place. For example, if a satellite going to Mars suffered damage to its scientific instruments in the middle of its journey, nothing can be sent out in time for repair, and the mission is essentially scrapped. Failures like this are unacceptable as space agencies propel their missions well beyond Earth’s orbit. Not only can such failures lead to expensive and potentially unrecoverable consequences for agencies, but they can also be fatal aboard manned missions. Therefore, it is important that any risks are identified as early in the development cycle as possible so that engineers have time to mitigate them and secure the spacecraft before launch.
Fragmented processes
Mission assurance is a complex endeavor and many space agencies struggle with it for a myriad of issues, many stemming from a siloed, document-based approach. Agencies have had to rely on paper documents, and later electronic documents, for decades due to a lack of alternatives, but the increasing complexity of spacecraft is stretching the feasibility in managing such documents. With so many essential electronics systems being added to spacecraft without a centralized method of storing their design data, engineering processes like mission assurance become increasingly fragmented by depending on traditional tools.
Fragmentation forces mission assurance analysts to carry out the process manually, and therefore inefficiently. Data is not generated, but must instead be authored by analysts. This can lead to a lack of consistency with terminology and design parameters between analysts that prevents easy data integration. The result is that analysts must come together and combine their analyses manually. Not only are these manual methods more time-consuming, but they also increase the potential inaccuracy of analyses, raising the likelihood of errors being carried through to the final spacecraft.
Digitalizing risk
A model-based approach can help circumvent many of these issues, and a key component of such an approach is building a digital twin. A digital twin is a virtual model of a product that analysts can test and simulate to identify mission risks. Additionally, as those risks are discovered, the digital twin can automatically gather the relevant data and upload it into generated data reports. This avoids the slow pace of manual data gathering and allows analysts more time to examine and act on their findings.
There are other ways the digital twin helps optimize the mission assurance process. Sourcing data directly from the digital twin helps standardize and integrate terminologies, methodologies, and parameters used throughout development. This helps create analyst-agnostic analyses, meaning analysts of all backgrounds and expertise can use the collected data to come to the same conclusions, further reducing the chances of inaccurate analyses. The data is also easily traceable, increasing its potential for reuse in future analyses. The opportunities from model-based mission assurance are numerous and can significantly help space agencies get spacecraft off the ground with confidence.
Keep spaceflight risk-free
Whether a spacecraft leaves Earth and arrives safely to its destination relies heavily on efficient, reliable, and accurate mission assurance analyses. Yet historical document-based approaches threaten to hold back the process as spacecraft become more complex and domains become more diverse. With a digital twin, however, space agencies are empowered to create new, efficient model-based approaches that can overcome the challenges mission assurance analysts face every day. Optimized mission assurance analyses powered by the digital twin today are the key to preventing spacecraft from turning into debris tomorrow.
To learn more about model-based space mission assurance, check out this webinar featuring a use case described by Nancy Lindsey, OSMA R&M Deputy Technical Fellow from the NASA Goddard Space Flight Center.
Siemens Digital Industries Software helps organizations of all sizes digitally transform using software, hardware and services from the Siemens Xcelerator business platform. Siemens’ software and the comprehensive digital twin enable companies to optimize their design, engineering and manufacturing processes to turn today’s ideas into the sustainable products of the future. From chips to entire systems, from product to process, across all industries. Siemens Digital Industries Software – Accelerating transformation.