Discussing a whole new industry with The Battery Podcast – Ep. 1 Transcipt
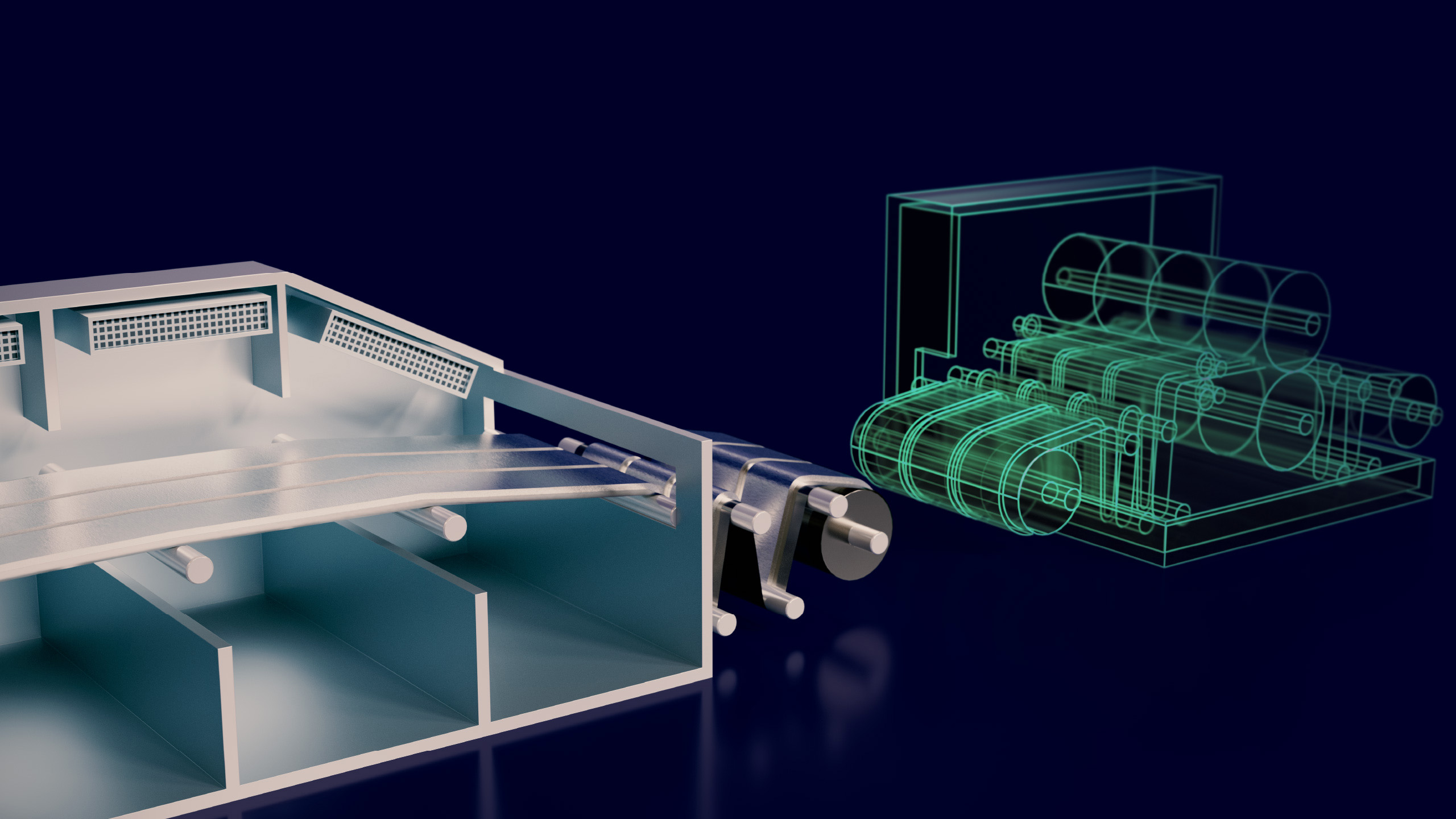
Siemens kicked off a new series devoted to the battery industry and the entire network of business supporting it from research to recycling. You can listen to the complete premiere on our podcast platform. What follows is the transcript of our opening discussion where we talk about the industry drivers, some important vocabulary, and a high-level overview of how we are already helping customers today. Please enjoy and we hope to see you soon for our next episode of The Battery Podcast.
Nick Finberg: Hello and welcome to the newest series from Siemens Digital Industries Software, The Battery Podcast, I’m Nick Finberg and I’m going to be your host and moderator for today’s session. But I’m joined by two guests, the first is Marc Deyda the head of strategy and communication for battery he also started the foundational work for the battery business in 2015 with others and has led machine builder and end customer projects in the battery market since. Puneet Sinha is the senior director of battery industry for Siemens Digital Industries Software. He has DI software strategy and cross-functional growth focusing on batteries. He has 15 years of industrial experience in battery product and business development working at auto OEMs, battery suppliers, and technology solution providers. Since we’re going to be talking about the battery industry and the world of batteries in general it might be important to define what we mean by those, so Puneet what do you mean by battery industry and what do you want to cover with this series as we bring in more voices to the discussion?
Puneet Sinha: Thanks for having us, Nick. For the battery industry, we are looking at the whole ecosystem from lithium mining and processing to material and chemistry development to cell and pack manufacturing, the integration of these batteries in systems (be it an electric car, electric aircraft, residential or grid level energy storage system) as well as recycling. It is very important to look at this whole ecosystem, because there are strong dependencies, technology wise, as well as the evolution of business across all these players. The way we look at it, the days when the cell suppliers are focusing on just producing cells, whereas end-customers focused only on taking battery packs and integrating them in system, are gone.
Increasingly, companies are evolving in their business value. Cell suppliers are increasingly looking to offer complete pack solutions. A lot of automotive OEMs as well as OEMs in other industries, such as aerospace and energy storage are heavily looking to morph themself into battery business. That means they’re investing heavily in cell development and manufacturing. And also, a lot of cell suppliers are investing in new chemistries. So, it is very important to look at the whole ecosystem and to understand the dynamics across all these players.
We want to talk to this whole ecosystem to understand and voice the challenges, the evolution of dynamics across the ecosystem, and how we all can work together to address the problems the battery industry’s facing today.
Nick Finberg: So even as kind of a layperson, one of the buzzwords that I’ve been hearing around battery industry is gigafactory. For those that may not know, can you explain what that is and why it’s important for the future?
Marc Deyda: Puneet has mentioned a lot of applications that are around all of us, and all will be fed with batteries. So, means we don’t need just one battery. We need thousands, millions batteries. And this wording gigafactory was founded nearly seven years ago and it means that okay, a lot of companies have pretty good ideas how to produce one battery. They develop recipes, for example, to produce these batteries but in a smaller range. And if it comes to a scale up factory, we have 20 million battery cells which is nearly 10 gigawatt-hours for example. You need more space, you need more factory site, and you need definitely more material. The machines have to be positioned in the factory and if you have a lot of machines like in a gigafactory, there is not only one stacking unit, there’s not only one coating unit.
There are in some cases, more than 50 of these machines. And the size of this battery gigafactory. One gigawatt hour will assume 10,000 square meter space. If you need 40 gigawatt-hours you can calculate, you need then 40 multiplicate with 10,000 square meter. This is a lot of space, and this is not done in your neighborhood. So, it means these 20 million cells a day, for example, will feed 200,000 e-cars and that production capacity is necessary to fulfill this demand which will come up until 2030. So, at the end of this decade, by around 3.6 terawatt-hour production capacity and that is the size of these gigafactory. They are absolutely necessary to fulfill this demand that we can use it for e-mobility, energy storage and all other applications worldwide.
Nick Finberg: That scale sounds massive. What are the challenges that these companies are tackling to get there?
Puneet Sinha: So, these challenges, Nick, are evolving very fast. If you were to ask me this question 14, 15 years back when I started working with batteries, that time we were staring at thousand dollars per kilowatt-hour kind of cost for battery. So, making a 200, 300 mile EV was almost out of question because the battery cost would have been more than the full vehicle cost in some ways. But in last 10, 15 years, the battery industry has really made huge strides. The cost of battery has come down almost 90%. Whereas because of all the improvements in the chemistry and in the design, the energy density of the battery has gone up almost 3x in the same time. So, these are some great progress that the whole ecosystem has made, but challenges remain. The challenges, some of the key challenges are the energy density of the battery. How many watt-hour you can put within a kg? How many watt-hour you can put it within a liter of volume?
Those still needs to be improved while making sure that the battery with as this new chemistry come the battery remains safe. It remains durable in the real world operation. So that continues to be a challenge and companies are investing in new chemistries, new cell designs, new pack designs. That continues to be a challenge. A much bigger challenge that has raised its head in last five to I would say last seven years, let’s say, is how companies can go and make these batteries or produce these batteries at scale cost effectively? As Marc mentioned this gigafactory, which is how you produce these cells at a giga scale. When you go from a small scale production to this giga scale production, a lot of new challenges start coming. The very first being how you set up these factories fast. Sometimes we are seeing these factories are taking four to five years to come into being.
That is too long a time for a large scale factory to come into play when the technology’s moving this fast. Another thing we are also seeing, which is I would say one of the biggest pain points right now with large scale production, that is scrap rate. In many of our engagements with our customers, various companies we have talked to, we are finding that in the first year of this large scale production, many of the companies are struggling with having a scrap rate as high as 70% or more, which is too much, too high a scrap rate for commercially viable large scale production.
Another thing. In addition to scrap rate is availability of material, availability of cheap material. So, in the battery chemistry, cobalt is quite a costly component. So, companies are looking at how they can go and pivot to the chemistries that are less costly and for which there is a more robust and diversified supply chain. These are some of the challenges but Marc, I’ll be interested to listen to what are some of the additional challenges you have seen in engagements with battery ecosystem.
Marc Deyda: Yeah, there are different ones. So, ecosystem means definitely also the integration of machines into the lines. A line is capable to produce these gigawatt-hours of production capacity, and the basic fundamental things are machines. And these machines are coming worldwide from different suppliers with different equipment’s in some cases, and that’s quite not easy to handle that for the end customers. They have to harmonize it or to interact with them, and the wish of the end customer is definitely kind of plug and play of these machines so that they are best optimized and ready to use. And this is in some cases different, really possible, but the quality issue will come up then. they have to interact these machines to connect them and have to make them fast acting with a high quality because this raw material is quite cost extensive, like Puneet mentioned.
And if they have high scrap rate, they have to improve and they have to improve the machine’s throughput, they have to improve the operation of the machine itself. They have even to make the operation easy for the operators because even this is a quite issue in the market. It’s ramping up business really fast but the resources, even the human resources are not yet available. So, they have to be educated. operation mode should be easy to use, easy to activate. Another thing is to make this production also stable, against some environmental humidity, temperature on the line. This has to be analyzed and has to be used in a safe mode to avoid this will have impact on the quality of the battery cell. Then yeah, the capacity. So, if you build up these huge demands of production sites, you need machines but not yet all over the world are so many machine builders available who can really offer that amount of machines.
The development of these machines has to be fastened up. And this is an ideal, what we also try to support with. We’ll have to build that already in a virtual environment and to validate everything, or even the production later on to start optimizing these machines that they are reaching a higher throughput. Then tracing also all that material that’s usable. So how much material do I have used for which amount of battery cells and what kind of material? And what parameters did I set up, for example, to have an optimized machine or optimized line output? This is something. Another challenge which is really, really important if you are working worldwide. So, there are a lot of huge companies who have their fundamental base in Asia, but they are working also in Europe as well as right now in the US.
They have to build up production lines in different regions, in different areas, and therefore they have to interact in a global team. The execution of the project to build up these gigafactories has to be aligned, and they need resources in these countries as well as systems and methods to make it happen, to have a faster start of production and decreasing the scrap rate. Then the scaling from an idea of a battery. So, in a labor environment, it’s maybe sometimes easy to develop a recipe but to scale it up to pilot, or then from pilot line to a mass production, that’s a different challenge
The customer needs support also from outside, from machine builders, from suppliers. And how? It would be maybe to expand their OT/IT solution whatever, for example, have a transparency of their production line and figure out anomalies within these production lines to have a better outcome. So, these are just a part of all these challenges. There are much more around, and if you participate once in the project, you will see there are so many things that are not visible, but you feel that there’s something to do.
Puneet Sinha: I fully agree with Marc and some of the great points he has raised. I just want to add a little bit more color. Marc mentioned increasing the production throughput, line of speed and a lot of the variables that come into it. One of the things that we also see, one of the key challenges sometimes especially for large scale manufacturing, there is a bound capital in some of the key manufacturing steps for cell. That means some of these steps of cell manufacturing take a lot longer than rest of the steps, and that starts causing a lot of the specific bottlenecks in the overall production. So how you go and overcome those bottlenecks in the production, such as the time that it takes for cell formation or aging as an example. These are some of the challenges that every company, be it a new entrant or an incumbent large enterprise who has been making these cells at large scale for many, many years, all of them are struggling with these issues.
Nick Finberg: So maybe at a high level, how are we helping them address these problems right now?
Marc Deyda: Definitely we as Siemens as a supplier, we want to integrate all the hardware and software and also, we hold services around. When we talk about an ecosystem, it starts already also with the planning of this production. That means I have an idea how much capacity do I want to produce, but how to develop that? This can already be done in a virtual environment. You can measure the throughput, you can measure the energy efficiency, you can also calculate how much machines do we need in this case. Then the next step would be how to develop these machines in combination with the machine builder. Then how to integrate them, how to standardize because standardization is definitely the enabler for the digitalization solutions, and that’s something what we definitely offer in this market as a global player. And we have on the simulation phase a lot of different accesses and ideas.
It starts from a process idea. It means how can I, for example, mix all these raw materials and how can I add this slurry that can be reused further to the coating machines. How can I then have an optimized coating process, reduce the tolerances? Because as we know, chemical reactions are always not under control as soon as the tolerances are too high. We try to reduce the tolerances in this whole processes. Then the logistic insight, all these different process steps to optimize the logistic flow to have a highest throughput as we mentioned. And also at the end, maybe use the data that are directly coming all at the to find anomalies with artificial intelligence to reduce, for example the formation time, which will have much more benefit for the end customers, but you have also to integrate the machine builders and convince them that this approach is easy to use and makes sense to integrate.
Yet another challenge is green energy and this is definitely something that has to be considered already at the planning of this production. So, what is really clean in a battery production? Definitely, energy use is a really major topic. So, when you want to be sustainable, you have to reduce the energy use. Then you have to reduce the use of raw materials or be more efficient. That is something that comes to sustainability. Puneet, do we have something to add on that?
Puneet Sinha: Yeah. Great points you made, Marc. I’ll just elevate it at a level, adding all the things that you mentioned is when we look at the ecosystem, when we look at the cell suppliers, one thing that is getting clear and we are hearing more and more of is that traditional methods of manufacturing, traditional ways of engineering batteries are not necessarily working to meet the ambitions that battery industry holds. That is battery industry is looking to 10x increase in its production capacity. That’s not going to happen if they continue using the traditional manufacturing practices.
More and more we are realizing companies are looking for this realization of how digital solutions, digital twin of production can help companies plan better. How they can validate their process before coming on the factory floor, before implementing them on factory floor, and how they can connect this digital world with the real world. That’s what a lot of companies are looking for. That’s where Siemens comes into play. Our focus is being a technology partner to all battery suppliers, to machine builders in their pursuit to address these challenges. In fact, eight out of top 10 battery suppliers in the world are leveraging our digital solutions to address such pain points.
Marc Deyda: And not only, Puneet, align to some other task, also via some project phases. So, a project is just successful as soon as the start of production is done smoothly and without any kind of problems. And if you see a real project of an end customer, that means you have at least nine phases and the idea is from us to be aligned with this end customer as well as the machine builder or also other integrators from the start of the idea until the start of the production even further on the maintenance level.
the service level afterwards with the production is in operation and therefore the idea is supporting this customer and if it comes, for example, to startups in some cases is quite difficult for them. They have so many challenges to erase. We try to consult them already at the beginning and try to find a really safe way, because they have invested a lot of money to save this money as well the investment to be aligned via the whole project phases. It means to design the installation, the commissioning, in the virtual environment, in a real world environment, ramping up and start the production in safe mode. This is what we want to do with these customers.
Nick Finberg: So, I know there’s a lot to cover and I know you guys want to keep this discussion going, but what are some of the upcoming topics and expert guests that you want our listeners to know about and make sure to subscribe for?
Puneet Sinha: So, Nick, our ambition is to have a dialogue with battery industry, with some of Siemens’ voices, bringing some of our customers, bringing some of the thought leaders in the industry to opine on various topics, such as, is a battery production really clean? Battery production consumes a lot of energy. Many times, 30 to 40 units of energy needs to be consumed to create one unit of battery energy. So how can companies make this very heavy energy intensive process sustainable, green and clean? Other topics such as how can companies reduce their recall risk with their new battery technologies. I mentioned earlier in the conversation about various efforts that are happening and increasing on developing next generation cell chemistries. We want to talk about that. What will it take to accelerate that development? What are some of the pitfalls that the chemistries that are developed in the labs many times don’t make it to the commercialization? So those are some of the topics we want to cover. Marc, anything more you want to add from your side?
Marc Deyda: I have mentioned it already a little bit, but okay, a factory without machines is not a factory, so that means we support the machine builder as well. And first the development, from process idea to a running machine as well as a material suppliers. When we talked about the end-to-end, it starts already how to get this raw materials. So that means we have that upstream or component production and even there we find ways to get these raw materials and to protect the environment. This is also important because when we talk about sustainability, there are a lot of generations coming after us and we have to keep this planet safe for them as well. So that means not using the raw materials, we want to use it in a clean way and in a sustainable way that upcoming generation can use it also for future purposes.
Nick Finberg: Those sound like great topics, and if our listeners want to learn a little bit more about how Siemens is addressing the gigafactory challenges before then, we will be showcasing our end-to-end battery story at events around the world. Our experts will be attending CIBF as well as Battery Show Europe in May. And come September and October, we will be in North America and India to show off what we have to offer. If you can’t make these events or want the information a little faster, be sure to check out our website siemens.com/battery.
Thank you and we hope to see you back soon to continue exploring the many facets of the battery industry.
Siemens Digital Industries Software is driving transformation to enable a digital enterprise where engineering, manufacturing and electronics design meet tomorrow. Xcelerator, the comprehensive and integrated portfolio of software and services from Siemens Digital Industries Software, helps companies of all sizes create and leverage a comprehensive digital twin that provides organizations with new insights, opportunities and levels of automation to drive innovation.
For more information on Siemens Digital Industries Software products and services, visit siemens.com/software or follow us on LinkedIn, Twitter, Facebook and Instagram.
Siemens Digital Industries Software – Where today meets tomorrow.