Closed-loop manufacturing helps meet customers’ challenges

The manufacturing industry faces significant challenges, with customers demanding more flexibility while desiring individualized products with superb quality and efficiency at the exact cost as mass-produced products.
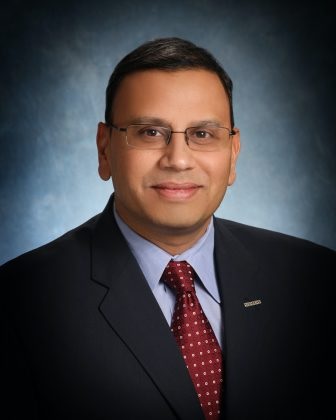
In answering this request, Rahul Garg, V.P. Mid-market program at Siemens Digital Industries Software, discusses how Closed-Loop Manufacturing (or CLM) enables companies to synchronize and optimize production across product design, production planning, manufacturing execution and automation. CLM constantly improves the manufacturing process of cost, time, and quality by creating a collaborative and connected information loop. As a result, it further accelerates the delivery of products optimally in quality and price. Additionally, CLM strengthens the alignment of as-planned/as-built products and as-used product information into a continuous iterative enhancement process.
CLM also addresses the challenges of the reverse flow of information to ensure that engineering teams receive appropriate feedback to improve product evolution value and accelerate problem resolution. In addition, it manages new product manufacturing introduction, speeding up time-to-market, and maintaining quality reliability and compliance requirements.
Closed-Loop Manufacturing includes:
- Determining the steps to build the products through manufacturing planning and engineering.
- Implement enterprise resource planning and scheduling capabilities to determine how the products will get created, paired against customer requirements and the schedule of the resources available for implementation.
- Ensure the maximization, reuse and utilization of resources dependent upon the supply chain for parts and materials.
A customer order is usually captured in a standard ERP system. The ERP or CRM secures the customer needs, while the PLM systems provide details of what needs to be manufactured and how to manufacture it.
The CLM contains three essential ingredients to assemble the product for the manufacturing operations process and how it’s tracked and built.
- PLM systems define the product, assisting the manufacturing process definition to the various resources utilized.
- Manufacturing Operations Management and MOM capabilities effectively combine the virtual world of PLM and real-world production. A MOM system is an evolutionary upgrade over traditional MES systems encompassing quality management, advanced planning and scheduling, manufacturing execution and enterprise manufacturing intelligence.
The supply chain is essential in manufacturing to enable product completion. Efficient collaboration with suppliers and customers provides a straightforward process to ensure new ideas for testing get applied and that suppliers deliver the product capabilities within the timeline to the quality specifications. All these attributes guarantee the completion and delivery of assured schedules.
Microsoft Office Manager (MOM) on the factory floor allows a manufacturer to collect and maintain large amounts of data on production using physical products. In the past, data was collected manually: billing information; was compiled by several physical sensing technologies like programmable logic controllers, PLCs, sensors, gauges and IoT devices.
This real-time data collection is valuable for knowing what’s continuously occurring in production. Also, that data feeds into the virtual world while the design, engineering, or manufacturing engineering people put together the overall processes.
Learn more in the podcast.
Xcelerator, the comprehensive and integrated portfolio of software and services from Siemens Digital Industries Software, helps companies of all sizes create and leverage a comprehensive digital twin that provides organizations with new insights, opportunities and levels of automation to drive innovation.
For more information on Siemens Digital Industries Software products and services, visit siemens.com/software or follow us on LinkedIn, Twitter, Facebook and Instagram. Siemens Digital Industries Software – where today meets tomorrow.