Digitalization and the future of the Marine Industry
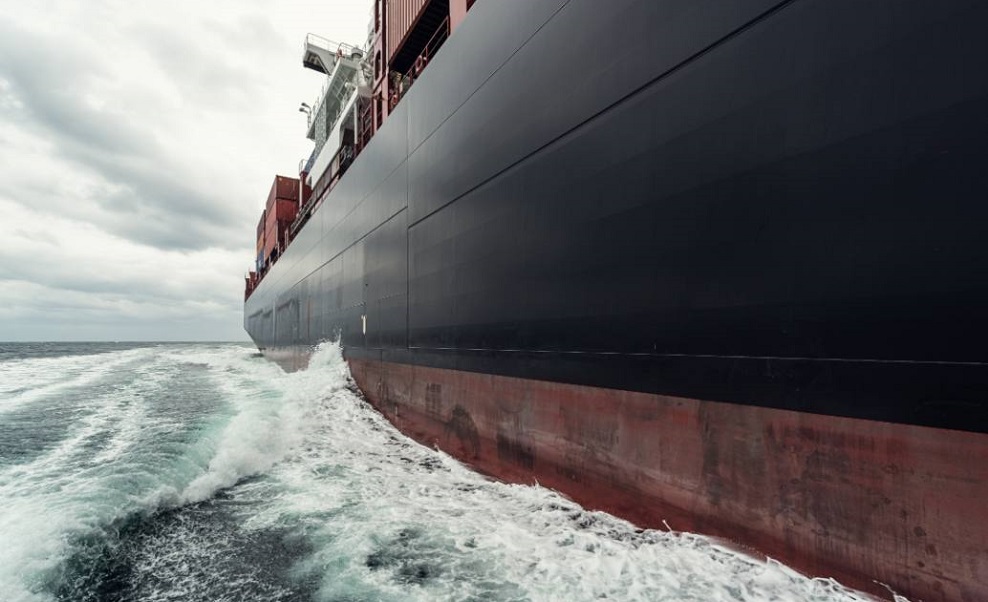
Augmented and virtual reality make digitalization possible for advanced maintenance strategies needing accurate data for ships and their components. Digital twin technology makes this a reality by representing a physical object in the virtual world, using as-designed and as-built operations and maintenance data. Then you can gather, maintain, and analyze this information through a digitalization platform that integrates and distributes this data when and where it’s needed.
The future of the shipping industry
In the shipping industry, they want to minimize risk by using onboard sensors that can alert the crew and onshore partners to potential problems before they occur. Also, operators want training that costs less; and virtual reality saves money while providing skill levels, creating a new training business for the equipment maker. Finally, it’s essential to minimize downtime, and augmented reality can guide the crew by giving on-site help with access to remote support, which is an opportunity for the equipment supplier.
Creating a digital twin of a ship or a virtual representation of its onboard systems may not be the entire vessel—but it’s a great starting point. A digital ship uses various innovative technologies available today in operation and management companies.
The design phase of shipbuilding is where a digital twin typically begins, as the first concepts are created and added to the design as it progresses. This digital twin will be updated as construction continues to make the as-built digital twin match more closely to the vessel. In addition, during operations and maintenance, the digital twin will continue to be modified to mirror equipment upgrades and other miscellaneous updates.
The digital twin will connect to onboard sensors, providing real-time or delayed access to operating data to analyze various facets of the vessel’s performance. These analytics will improve ship and fleet operations, thus, planning maintenance to balance wear on equipment, downtime, and maintenance materials and labor. This data can also be used to route planning for optimizing fuel use alongside speed and idle time at anchor. Modern ships already possess gigabytes of rarely used data, so they need to generate it, then gather and analyze it.
Managing risk and reducing operating costs also help crew members perform their jobs effectively. Having an utterly autonomous vessel is still off in the future; however, assistive technologies are being used on many bridges for collision avoidance. Also, minimal technologies aid with maintenance tasks by providing the crew with training and on-the-job information before the task. These virtual and augmented reality tools promote upskilling crew members on board and provide valuable data to colleagues onshore, lending their expertise.
Additionally, advanced analytics tools like artificial intelligence and machine learning help operators “see” things that humans can’t. For example, AI can help with route planning based on location data, providing ships’ masters with the ability to predict future positions, movements, and maneuvers in advance. They can also use this to game out routes, avoid collisions, limit fuel consumption, and enhance safety.
However, the maritime industry usually needs to catch up to adopting new technologies, so things must change for operators to become more efficient and sustainable.
Digital twin – a new method
Change can begin with a digital twin, whether for digitalizing a critical system or an entire vessel – a static or dynamic duplicate of a physical object or process. Designers have the earliest input into the digital twin.
Once validated as matching the real world, you can perform simulation, gather insight, and find and resolve situations, while planning for future scenarios.
However, the digital twin is only one part of digitalization. Digital technologies must become a core pillar that informs various areas of a business’s operations. Maritime enterprises are digital experts knowledgeable of emerging trends, so their operations attract future workers.
Ready for the future
So smart shipping begins with connecting data to good resources that can analyze and help operators maximize uptime and profit. You build intellectual property into information-based products. For example, with a digital twin of the equipment you can sell both augmented and virtual reality-based training alongside the physical gear.
Smart ships are the marine industry’s future, enabling you to operate with greater certainty and lower risk and sustainability.
Learn more about what’s going on in the shipping industry’s future from industry experts with a new upcoming Marine Podcast series beginning in a couple of weeks.
Siemens Digital Industries Software helps organizations of all sizes digitally transform using software, hardware and services from the Siemens Xcelerator business platform. Siemens’ software and the comprehensive digital twin enable companies to optimize their design, engineering and manufacturing processes to turn today’s ideas into the sustainable products of the future. From chips to entire systems, from product to process, across all industries, Siemens Digital Industries Software is where today meets tomorrow.