Avoiding certification delays in A&D – Summary
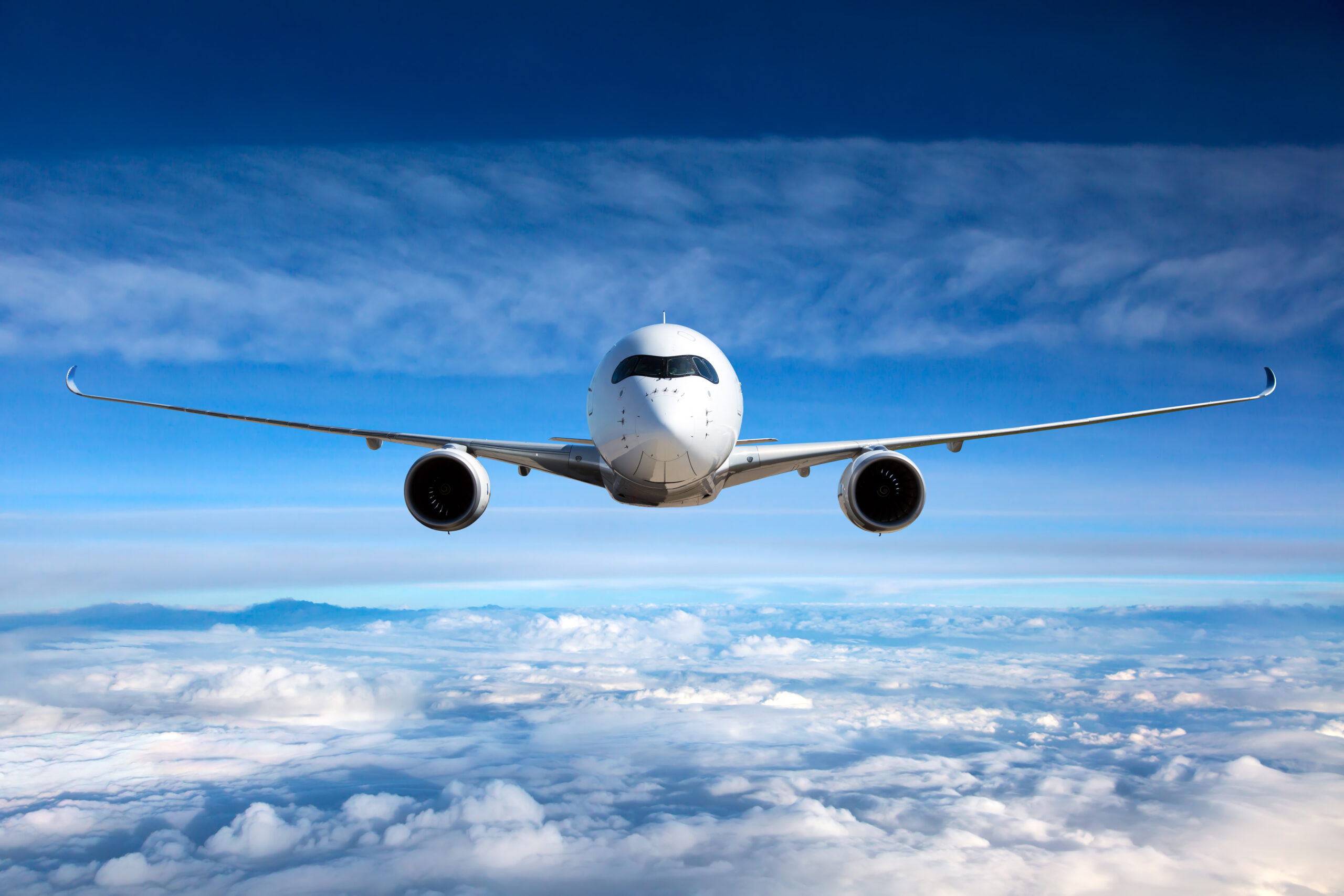
On a recent Aviation Week webinar, Todd Tuthill, Vice President of Aerospace and Defense (A&D) Strategy and Marketing for Siemens Digital Industries Software, spoke alongside Chad Jackson, Chief Analyst and CEO of Lifecycle Insights, about the biggest contributing issues to certification delays in A&D.
Delays to certification, the process of proving a product’s safety in collaboration with a certification authority, are becoming more intolerable as products become more complex and companies face continual pressure to reduce times to market. Todd and Chad used this webinar to identify the key issues that cause such delays and their solutions, including different data systems and design changes during certification; barriers to virtual testing; and the cost of building and maintaining physical assets.
How siloed data affects certification
Historically, A&D companies have used different software tools and data systems across engineering domains like mechanical, electrical, fluid dynamics, and others. As a result, these domains end up isolated from each other as design data is scattered across all the tools and systems with little to no traceability or connectivity. Without easy access to data from other domains, the risk of errors and delays later in the development process only increase.
Those errors may not be discovered until the most inconvenient stages, including certification itself, forcing engineers to make design changes at the last moments. Todd gives an example of finding an issue with an engine while testing a flight control system for certification. In most cases, the test would not need to be repeated, but it would if the new engine design, say, reconfigures the power system that supplies the flight control system. If data were not so disconnected, that issue would likely have been discovered in time for the first test, but with the current siloed system, engineers would need to revert their progress instead.
A solution to these data gaps, according to Todd and Chad, is to build a single source of truth, one digital location where engineers can store and retrieve data, as well as test their product. This may come in the form of a digital twin, a virtual representation of a product. Data from multiple domains could be aggregated around the digital twin, which can then be used to simulate and test a virtual version of an aircraft or spacecraft to better prepare for certification. As a single source of truth, the digital twin can provide better traceability between domains for data and help engineers locate design issues much earlier in the development process.
The barriers to virtual testing
Despite the steady growth of digital twin implementations, however, there are still barriers to virtual testing A&D companies must overcome, many of which are cultural. Many companies employ some degree of combination between physical and virtual testing, but physical testing is still typically favored. There is still a wide reluctance to see the “truth,” a model’s integrity as an accurate representation of a product, already inherent in the digital twin.
Much of this comes from the common behavior of normalizing traditional processes, even if portions of them are inefficient. Companies have historically relied on physical testing because they had no other option and are hesitant to make any changes. If companies want to remove potential problems that could delay certification, placing more trust in virtual testing would help tremendously.
Virtual-to-physical optimization
There would be good reason for this trust, as another significant issue delaying certification is just how expensive it is to construct and maintain physical assets. Physical prototypes are growing more costly, especially as issues like supply chain bottlenecks raise the price of materials and delay deliveries. Additionally, physical prototypes require large testing facilities to carry out tests, which require even more materials, time, and engineers to build. Virtual prototypes, meanwhile, allow companies to save money that would be spent on physical materials and construction. Virtual testing can also be done quicker and more frequently, giving engineers even more time to find and fix errors in preparation for certification.
The goal is not to completely replace physical testing with virtual testing. After all, a physical prototype would still be required by certification authorities today to guarantee safety. Rather, the goal is to optimize physical testing by incrementally increasing the amount of testing done in virtual space. Software and virtual models undergo continuous verification through agile development processes. Companies can apply those same processes to optimize their degrees of virtual-to-physical testing.
The main takeaway from Todd and Chad’s discussion is how scattered data can create delays in the certification process, and how a single source of truth like the digital twin can solve that with virtual testing. However, many A&D companies would need to learn to accept virtual testing as truth and increase their virtual testing capabilities through increments. Doing so can optimize physical tests and get A&D products certified and out the hangar faster.
Be sure to check out the full webinar to hear Todd and Chad’s entire conversation.
Siemens Digital Industries Software helps organizations of all sizes digitally transform using software, hardware and services from the Siemens Xcelerator business platform. Siemens’ software and the comprehensive digital twin enable companies to optimize their design, engineering and manufacturing processes to turn today’s ideas into the sustainable products of the future. From chips to entire systems, from product to process, across all industries, Siemens Digital Industries Software is where today meets tomorrow.