Advanced Machine Engineering adopts a digital twin approach to deliver complex machines
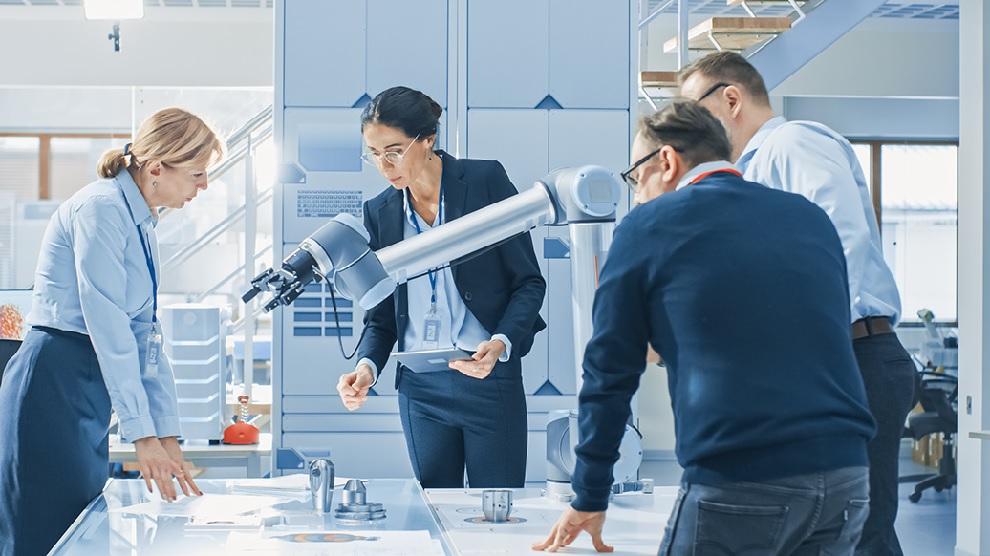
In a Machine Design article, Rahul Garg, Vice president for Industrial Machinery & SMB Programs at Siemens, provides knowledge about a digital thread approach to engineering that encourages collaboration among engineering disciplines and leads to a simulation-driven digital twin.
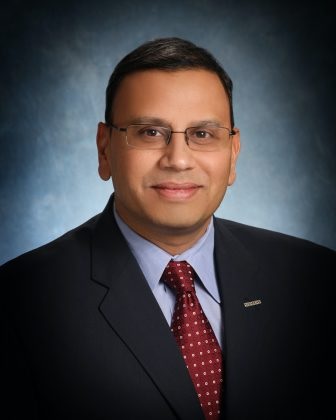
When adopting a digital thread approach to engineering, machine builders accelerate the delivery of tomorrow’s highly complex machines, providing a competitive edge. In addition, advanced machine engineering (AME) provides visibility, allowing machine builders to capture and incorporate design feedback from internal and external stakeholders. Rahul Garg discusses how this virtual process, based on simulation and the digital twin, benefits an advanced machine’s entire development and deployment.
“The industrial machinery landscape is rife with unprecedented challenges—supply chain shortages, labor scarcity and entrepreneurial market disruptions. At the same time, machine builders are tackling outdated legacy processes and technologies that threaten growth,” says Garg.
These megatrends in the industry drive machine builders to rethink how they respond to changing market demands while optimizing quality to remain competitive. Simultaneously, changing consumer preferences are driving product manufacturers’ need for highly agile, flexible machines capable of creating a wide range of products.
It is essential to have smarter machines to integrate hardware, software, and services into a cohesive environment. Automation is necessary to drive higher efficiencies into machine builders’ processes while maintaining competitive differentiators. In addition, sustainability increases with automation within operations to promote the sustainability goals of end customers.
These trends are motivating machine builders to their daily practices digitally. Using a digital thread approach to engineering, machine builders can expedite the delivery of complex machines, providing a competitive advantage compared to legacy processes. A digital thread approach uses AME to drive certainty for next-generation machines, leveraging a cloud-based methodology that promotes collaboration among the fundamental engineering disciplines leading to a simulation-driven digital twin. The result is superior flexibility with better quality and time-to-market.
Cloud-based teamwork
Advanced machine engineering leverages cloud accessibility, creating visibility across several teams to develop smart machines. It includes all engineering disciplines—mechanical, electrical, electronics and software engineering—merging them into a single source of truth via the cloud. In addition, it maximizes data reuse and supports an integrated change process to ensure a standard delivery process.
“Engineering teams can now store, access, and utilize real-time dashboards, schedules and documents at any time, from anywhere. It drives efficiency into the machine development, boosting overall productivity,” says Rahul.
Additionally, machine builders can capture and incorporate design feedback from internal and external stakeholders. This ensures the creation of effective machines while avoiding delays and managing product costs. By previously incorporating feedback, the design process and machine builders can account for supply chain issues and source materials from outside vendors.
Digital twin and virtual commissioning
When you stream communication between disciplines, the cloud provides data sharing vital to creating a comprehensive digital twin of the future machine.
“The multi-disciplinary model of the proposed machine connects mechanical, electrical and automation engineers to evaluate performance, energy use, output and other key indicators. Then a digital twin can simulate everything virtually, reducing the need for costly and time-consuming physical prototyping”, says Garg.
The virtual process, based on simulation and the digital twin, provides benefits around the development and deployment of an advanced machine, including:
- Design: Machine builders can use the cloud-based digital twin to simulate models and test thousands of features against thousands of requirements. That leads to finding errors earlier in the design process while pushing the creative boundaries of manufacturing.
- Testing: The virtual analysis is enhanced through closed-loop testing, where artificial intelligence and machine learning algorithms identify potential improvements—ensuring the production of the most flexible and optimized machines.
- Manufacturing: When it is time to commission the machine for the factory floor, advanced machine engineering supports testing the PLC code in a virtual world running on the digital twin. The result is streamlined stress-free physical commissioning. Virtual commissioning can ensure your PLC code is tested and evaluated before getting it on a physical machine. A machine crash in the digital world costs nothing.
- Lifecycle: When customer requirements change, machine builders have an easily accessible process for updating machine programming logic or refreshing machine models using the digital twin and simulation.
Modular designs, collaboration, and the digital twin
AME provides the foundation for modular design with cloud collaboration and the digital twin. It’s a highly desirable approach where machine information and specifications are contained within modular “blocks.” These blocks are reusable across projects and customized to fit customer needs. For example, engineers can open a block containing a preexisting machine’s bill of material (BOM). Then they save the block as a new project and change it to include updated parts or components that meet a customer’s specifications.
Modular designs are cost-effective, creating a path to scale for mass customization. It is possible to produce highly distinguishable machines quickly and cost-effectively from a shared set of modules.
The result is that machine builders can accelerate their bid times, responding to a larger number of inquiries and delivering a significant number of orders, expanding their business’s profitability. Modular design is also vital for rapid machine configuration. When customers require change, machine builders have an accessible process for updating machine programming logic or refreshing machine models. Also, it’s possible to trace design iterations and comprehend specific decision-making. The machine’s digital twin makes it possible by providing a virtual machine mockup, where machine data is available to reference and update.
Delivering complex machines
Advanced machine engineering gives machine builders the powerful capabilities to survive and thrive in the demanding and competitive industrial industry. It integrates all the engineering disciplines to empower collaboration across the design teams through real-time cloud tools.
The result is a comprehensive digital twin of the machine that supports complex simulation to create optimized machines without physical prototyping. Additionally, this method creates an environment for modular design, where machine builders quickly and cost-effectively can adapt to shifting market requirements. Advanced machine engineering enhances machine builders’ productivity, speed-to-market, and quality, providing success in the marketplace.
Siemens Digital Industries Software helps organizations of all sizes digitally transform using software, hardware and services from the Siemens Xcelerator business platform. Siemens’ software and the comprehensive digital twin enable companies to optimize their design, engineering and manufacturing processes to turn today’s ideas into the sustainable products of the future. From chips to entire systems, from product to process, across all industries, Siemens Digital Industries Software is where today meets tomorrow.
Rahul Garg is the vice president for Industrial Machinery & SMB Programs at Siemens, responsible for defining and delivering key strategic initiatives and solutions and global business development.