Secure your wire harness designs with the digital twin
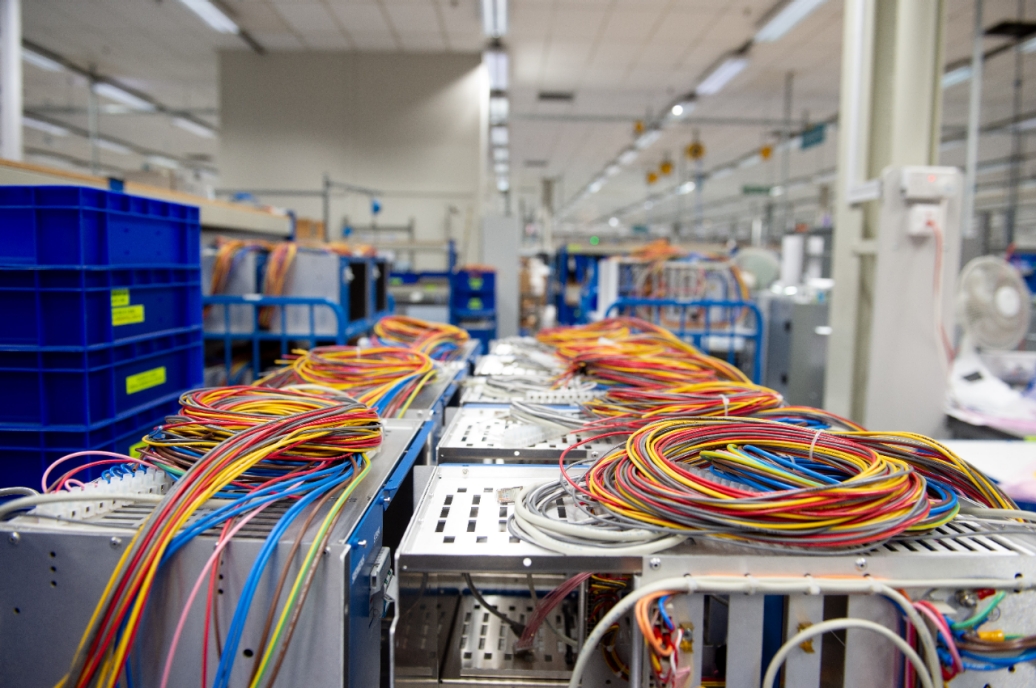
Wire harnesses are the unseen heroes of the Aerospace & Defense (A&D) industry. They snake and coil through the recesses of aircraft and spacecraft hidden from passengers’ eyes, ensuring that power is properly distributed to all the craft’s systems. What is also not immediately visible is just how sensitive wire harness design really is. Everything from minor errors, changes to other systems, as well as external factors like budget constraints can require engineers to redesign entire wire harness systems. These can lead to crippling costs and delays as A&D products increase in complexity and electrification while integrating advanced software and electronics. Traditional methods of wire harness design will not be able to keep up, but the comprehensive digital twin offers several advantages to maintain efficient design processes, including seamless data sharing, accelerated verification, and generative design.
A significant benefit of using the digital twin for wire harness design is seamless data sharing applied to the entire wire harness’s lifecycle. Traditionally, the process of designing wire harnesses has been an intensively manual one involving isolated transfers of information between different teams, usually through spreadsheets and emails. These transfers result in delays as teams interpret each other’s data and wait for responses, delays that are now unaffordable as industry trends demand getting products to market faster. The digital twin, meanwhile, coalesces all the data surrounding a wire harness around an easily accessible virtual model. Engineers from all involved teams and disciplines can access the data directly and transfer it across digital threads to anywhere in the product lifecycle, from design to manufacturing and beyond. Through the digital twin, delays between data transfers will drastically decrease, thereby accelerating the design process to meet modern requirements.
Another design factor hindered by traditional methods the digital twin can help address is verification. Due to the disconnected nature of the data exchanges between teams in traditional design, many engineering errors are not discovered until a physical version of the wire harness is built. Such errors are only noticed when the wire harness and associated systems are fully assembled, and when they are, engineers must redesign the harness and repeat the whole process over again – costing valuable time. What the digital twin can do instead is help uncover errors early on through simulation. Engineers can assemble a virtual representation of the entire aircraft or spacecraft and see how the components of the wire harness interact with each other and the wider product before a physical version is ever built. They can also go further by defining desired parameters and tasking algorithms to identify errors automatically. Problems in a wire harness’s design can be rooted out in advance, speeding up verification and reducing the need for physical testing.
The digital twin offers additional applications for automation, including generative design. As explained in a previous blog post, generative design offloads design tasks from engineers to algorithms. Companies and engineers can construct their own sets of requirements, which generative design algorithms will utilize to create their own iterations of a desired product. These algorithms can generate hundreds of design iterations within a short span of time, giving engineers plenty of options to analyze and choose from. They will also be able to incorporate and track external requirements, such as cost impacts and sustainability goals, and use them when designing different iterations. The time saved from delegating design to generative algorithms will give engineers more time to handle other engineering responsibilities. By automating design itself, the process becomes much faster and wire harnesses can be manufactured and implemented quicker.
These are just some of the advantages afforded by the comprehensive digital twin that will help any A&D company improve the design of their wire harnesses. Its abilities to seamlessly share data across disciplines, as well as automate verification and design processes offers companies the chance to optimize not just their wire harnesses, but also how they design wire harnesses for new trends in the industry. By using the digital twin, the next generation of wire harnesses will be able to take on the ever-increasing complexities of modern A&D products.
To explore more about how the digital twin can improve wire harness design, check out this white paper.
Siemens Digital Industries Software helps organizations of all sizes digitally transform using software, hardware and services from the Siemens Xcelerator business platform. Siemens’ software and the comprehensive digital twin enable companies to optimize their design, engineering and manufacturing processes to turn today’s ideas into the sustainable products of the future. From chips to entire systems, from product to process, across all industries, Siemens Digital Industries Software is where today meets tomorrow.