The real and virtual world combine with closed-loop validation
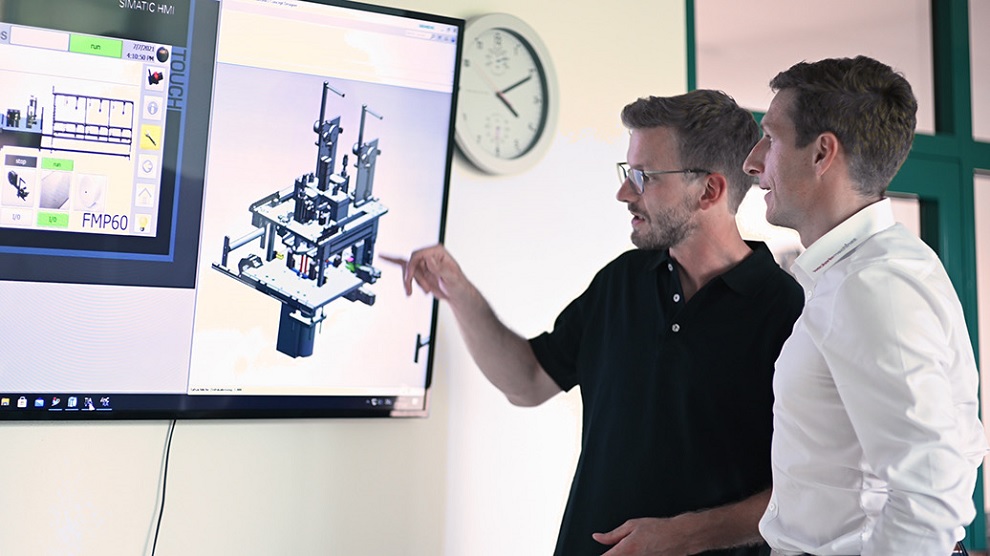
In an article in Industrial Machinery Digest (IMD), Rahul Garg, Vice President for Industrial Machinery & SMB Program at Siemens Digital Software Solutions, discusses how the demand for highly complex products is driving OEM requirements for customized machines.
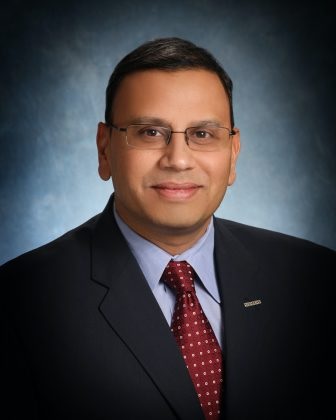
Modern machines are intricately complex. Machine builders require simulation early in the design and verification processes to meet their specifications. Virtual simulation improves the speed of innovation, so it is essential to associate the accuracy of simulations with real-world machine operation in a physical environment while minimizing prototype and testing. However, using a closed-loop validation process, Intelligent Performance Engineering (IPE) helps validate simulation with real-time feedback from sensors in machine data.
Read the IMD article for more information.
Intelligent Performance Engineering responds to complexity
There is consumer demand for integrated products and services tailored to discrete needs. Therefore, machine builders must provide a wide range of customization for standard machines to meet customers’ requests. Simultaneously, there is demand in the marketplace for better throughput and performance. At the same time, energy efficiency, quality and safety have resulted in increasing numbers of complex machines integrating advanced technologies for smart connected systems.
So, these systems combine mechanical and electrical controls that assist OEMs in creating customizable and compliant machines that are reliable and efficient. Machine builders are facing a threat from more affordable competitors worldwide. Thriving as a top competitor depends on digitalization to drive innovation, differentiation, and cost competitiveness. This mindset separates a company from its peers. Intelligent Performance Engineering provides a way to assist OEMs in realizing designs quicker and improving productivity.
IPE helps teams evaluate the variations needed for next-generation machines in a virtual environment, proficiently achieving an ideal balance of cost and performance while accomplishing optimum reliability.
IPE provides three crucial differentiators to assist machine builders: multi-physics simulation and testing, integrated design and simulation, and closed-loop validation.
A comprehensive digital twin
An essential element of a closed-loop validation is using a digital twin, where teams efficiently evaluate the capability and limitation of product variations through integration between designers, analysts, and live data, focusing on improving design metrics. Also, a digital thread automates information sharing between engineering teams, analyst production, test teams, and service engineers.
The comprehensive digital twin’s foundation integrates into design and simulation, where many engineering disciplines capture simulation and validation results in a central repository. Now teams can efficiently evaluate product variations’ capability and limitations through integration between designers, analysts, and live data, focusing on design metrics. Using a digital twin supported by digital threads, machine builders increase design flexibility, improve productivity, and progress innovation processes to build the next generation of smart industrial machines.
So, during the design and simulation stage, validating the virtual machine using a digital twin lets a team validate designs early, quickly testing multiple configurations and understanding the impact of variables without needing a physical prototype, which is more costly. However, the simulations require reality-based assumptions. Therefore, a virtual digital twin can lack the exact criteria environments the machine will encounter when operating in the real world. So, to ensure that the simulation assumptions have not discounted vital behaviors or taken a broad view of the design, it is essential to test and validate the machines in the physical environment where the closed-loop validation process occurs.
Closing the loop delivers optimal machines
When a machine moves to a physical prototype and into real production, it is ready for test-based and run-time validation. Then the machine builder can harness and wire out the suitable sensors to collect real operational machine performance data in real-time – complemented with virtual sensors. When scrutinizing how a machine performs, closed-loop validations provide a real sense of how a machine meets the customer’s needs.
Then you look at data variables: production rates, noise, and vibration to deliver real-time feedback that is gathered and looped back into the digital twin to validate and improve the correctness of test criteria for future simulation models. This method efficiently connects simulation data to the design object, ensuring that simulation models are accurate to provide machine builders significant insight into validating and enabling the fine-tuning of parameters that improve future design and engineering.
Learn more in Rahul’s article.
Siemens Digital Industries Software drives the transformation to enable a digital enterprise where engineering, manufacturing, and electronics design meet tomorrow.
Xcelerator is a comprehensive, integrated portfolio of software, services and an application development platform. The portfolio accelerates the transformation of businesses into digital enterprises. It unlocks a powerful industrial network effect – essential requirements to leverage complexity as a competitive advantage, no matter the industry or company, to transition seamlessly to create tomorrow’s complex, efficient machines.
Related links:
Listen to IPE podcast04 from this series.
About our author:
Rahul Garg is the Vice President for Industrial Machinery & SMB Program, responsible for defining and delivering key strategic initiatives and solutions and global business development. He and his team are responsible for identifying key initiatives and developing solutions for the industry while working closely with industry leading customers and providing thought leadership on new and emerging issues faced by the machinery industry. Rahul’s experience and insight are derived from 25 year career delivering software-based solutions for product engineering and manufacturing innovation for the global manufacturing industry, spanning a career in R&D to program management, sales and P&L management and having focused exclusively on the industrial machinery and heavy equipment industry since 2007.