Smart manufacturing provides virtual manufacturing development for automakers
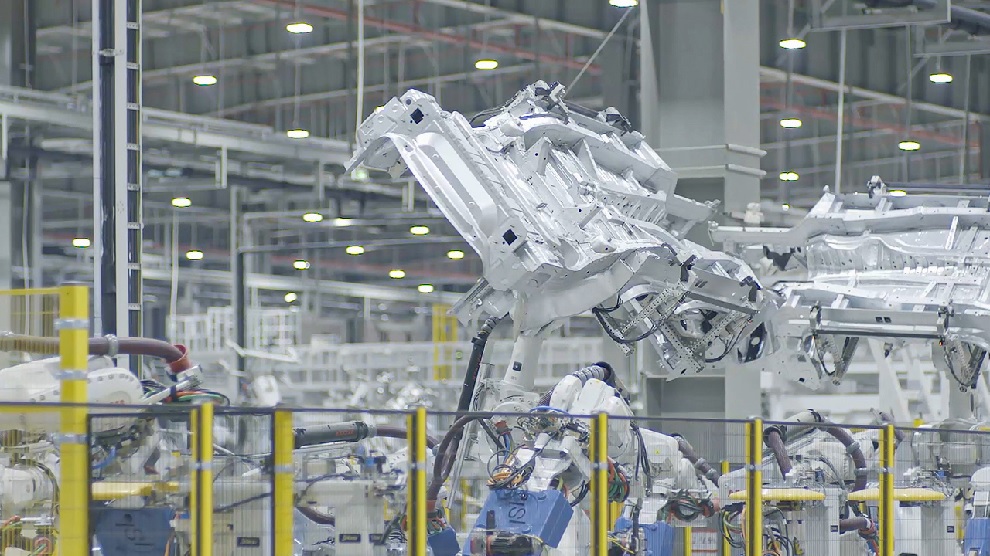
Technological advancements are changing transportation from conventional mechanics to complex sustainability – entertaining and connecting mobility driven by electronics and software. Staying current in a fast-changing market, automakers must rethink product design, development, and manufacturing areas. Research and development of new technologies like vehicle electrification and autonomous driving continue with traditional manufacturing processes and outdated equipment.
However, eventually, this will jeopardize their existence by risking production line disruptions, failed launches, cyberattacks, and penalties for non-compliance with environmental regulations. To succeed in the current market, automakers must be agile and resilient while accelerating innovation, managing increased complexity, and evolving manufacturing facilities to meet all sustainability and regulatory targets faster than the competition.
Download the white paper for more information.
Over several decades, automotive manufacturers have amassed enormous knowledge, allowing them to accurately plan development cycles and produce flawless launches for traditional vehicles. Through past accomplishments, some auto manufacturers are hoping their current processes, technology, data management systems, and equipment will bring continued future success. However, implementing smart manufacturing seems a monumental step that is too costly, time-consuming, disruptive, and risky; therefore, it is not embraced.
Digital transformation by adopting smart manufacturing
Fortunately, many automotive manufacturers know the need for digital transformation to compete in today’s evolving automotive landscape. A McKinsey Group report states that 70 percent are beginning to adopt smart manufacturing. By partnering with a solutions provider, these forward-thinkers are taking steps to decrease downtime, bolster cybersecurity, make real-time decisions, and introduce intelligent automation to improve productivity, flexibility, and sustainability.
In the last 30 years manufacturing efficiencies are improving the labor time to build a vehicle by decreasing build time 50 percent.
The industry is rapidly changing, and automakers cannot hold onto conventional production and siloed manufacturing; otherwise, they will not produce the next generation of vehicles with the latest manufacturing technologies.
Additionally, governments are imposing stringent sustainability regulations while consumers demand these innovations. So, OEMs must produce increasingly complex designs quickly. Therefore, it is crucial to have the ability to combine real-world data with cloud or edge-based simulation to develop, test safely, and commission virtually. Otherwise, a tightened schedule could lead to more errors, lower quality, launch delays, and dissatisfied customers. Outdated IT practices and old equipment in the factory hinder real-time manufacturing performance and maintenance, slowing production and preventing new technology integration that is essential to an automaker’s survival.
A virtual environment provides the groundwork for developing and testing manufacturing processes, configuring assembly line layouts, and training workers virtually before working in the physical world while providing repeatability, and fine-tuning quickly and accurately.
Using a digital twin of manufacturing, automakers have the flexibility to replicate global production rapidly. Also, a cloud-based centralized cyber-secure source of real-time data is available to ecosystems to facilitate knowledge sharing, standardization, production scheduling, planning, and global collaboration.
Better, faster decision-making with intelligent production and closed-loop feedback
So, rising complexity requires the implementation of new technologies, including vehicle electrification and autonomation. Top manufacturers are successfully managing this digitization transition and the power of data. Collecting and analyzing real-time data via sensors in the factory creates a closed-loop feedback system to improve quality and efficiency. Then it uses this data to generate automated acumens that will enhance industrial output. Furthermore, predictive maintenance strategies are optimized to improve flexibility and control with robust cloud and edge computing and processing capabilities.
Smart manufacturing cross-pollinates advanced AI technologies: the industrial internet of things (IIoT), and analytics embedded into traditional automation systems to increase factory automation, better process optimization, and higher cost savings.
Siemens smart manufacturing solutions
Siemens’ smart manufacturing solutions combine technologies and automation that increase factory efficiencies and profitability. They produce an intelligent production environment via data analytics, connectivity, and integrated simulations to solve issues in real-time to achieve output targets. By partnering with Siemens, automakers and suppliers modernize legacy equipment more rapidly with factory automation, improving real-time decisions with intelligent operations excellence to achieve cost savings and flexibility through a virtual means.
Learn more in the Smart Manufacturing white paper.
Xcelerator, the comprehensive and integrated portfolio of software and services from Siemens Digital Industries Software, helps companies of all sizes create and leverage a comprehensive digital twin that provides organizations with new insights, opportunities and levels of automation to drive innovation.
For more information on Siemens Digital Industries Software products and services, visit siemens.com/software or follow us on LinkedIn, Twitter, Facebook and Instagram. Siemens Digital Industries Software – where today meets tomorrow.