Siemens and Deloitte Pave The Way For Xcelerated Reshoring
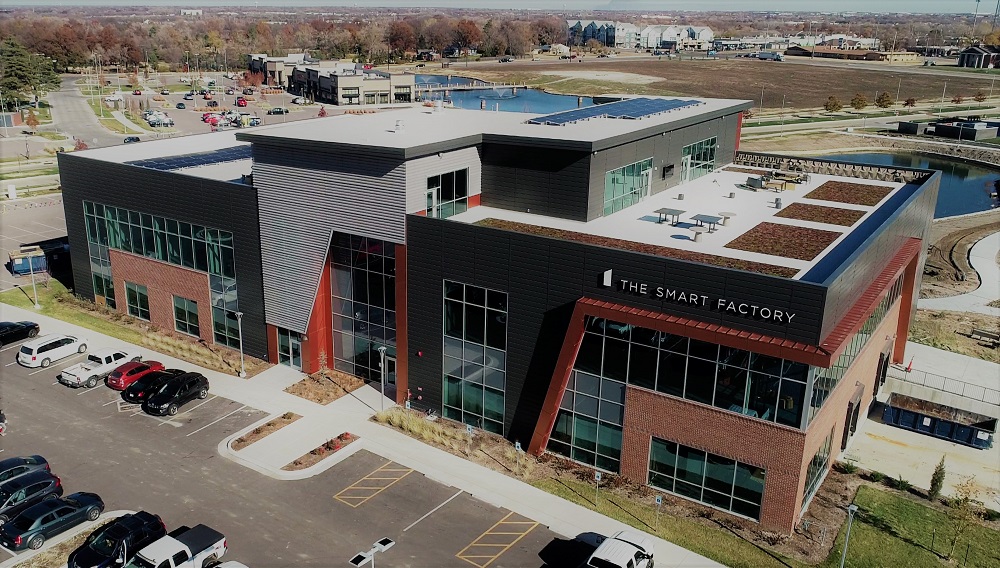
Overcoming Localization/Reshoring Challenges
For years, manufacturing companies have moved more and more work offshore. Recently, that trend seems to be reversing. Today, manufacturing companies are looking to move their operations from Asia to North America by reshoring, localizing, or regionalizing there. They are motivated partly by a desire to gain more control over their supply chains, but also by the need to shift production closer to the end customer. This allows companies to contribute to their local economies and increase sustainability by reducing both their logistical costs and carbon footprints. The use of a comprehensive digital twin and digital threads—created and supported by the industry-leading technologies and capabilities provided by Siemens Xcelerator and Deloitte—can help companies successfully reshore in an innovative, affordable, and non-disruptive manner.
Localization/reshoring entails establishing new manufacturing facilities or improving existing ones, in a location closer to actual demand—in the United States or in any other country where the company serves a customer—which can be a complicated endeavor. When determining how and where to start, organizations must consider, among other things:
- New manufacturing technologies
- Government incentives and tax breaks
- Potential costs including capital improvements and labor
- The capabilities of the local workforce
- Expected profits and returns on investment.
And the list doesn’t end there. Organizations must also determine the layout and logistics of their facility, timing and market conditions, and competition as they begin working on the development of a smart factory. Siemens and Deloitte have aligned to provide invaluable technical and business expertise to companies that are reshoring, localizing, or regionalizing.
This article explores the role of connected digital tools from Siemens and Deloitte that can facilitate smart factories’ conception, planning, simulation, creation, management, and long-term innovation.
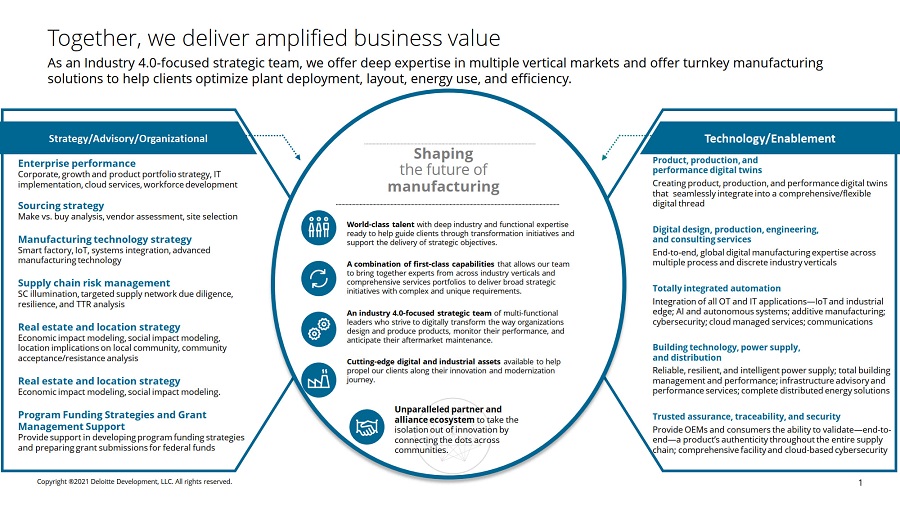
The Need to Remove Uncertainty
While localization/reshoring has its share of challenges, the good news is that a comprehensive digital twin of the product, production method, manufacturing line, and structure can dramatically reduce costs, risks, and time. Moreover, the data generated will allow key leaders to make critical decisions faster and more accurately before ever bending metal or pouring concrete. Simply put, it allows targeted investments, increased predictability, and maximized flexibility.
Before companies invest, they need to understand many aspects of their manufacturing plant. This includes what size facility to use, the availability of skilled labor, the cost of labor, the footprint of all machines, power requirements, and the plant’s output, as well as details on sustainability, environmental impact, and end-of-life situations.
Reshoring demands a significant investment of resources, so accurate information is critical to making smart business decisions.
Using the Digital Twin for Accurate Manufacturing Planning
An exact digital twin of the proposed manufacturing plant can provide companies a high level of accuracy. Combining digital twins of the product, production, and plant creates a digital thread that provides stakeholders with access to every critical detail, including information about plant layout, manufacturing lines, throughput data, and so on. These comprehensive digital models assist with both “greenfield” projects begun from scratch and “brownfield” projects that re-use existing facilities and must be completed while considering existing site constraints. Engineering executives can explore multiple “what-if” scenarios when using a simulation of their digital factory. For instance, engineers can change the layout of the machines and simulate the impact of this change on the electrical cabling cost, material handling infrastructure cost, or ventilation improvements inside the plant. In this way, a digital twin helps companies arrive at the best possible layout and design for a factory. They can study and optimize throughput, cost, material handling, inventory, and other operational parameters well before investing a single dollar in the construction of the factory or the procurement of machines.
Using the Digital Twin to Improve Manufacturing Operations
The best part is that the benefits of a comprehensive digital model don’t end once the factory is up and running. Companies can compare real-time data from the actual factory with digital simulation data. They can then spot anomalies and schedule predictive maintenance at the right time. This gives manufacturers a considerable advantage when it comes to keeping production at peak performance.
Predictive maintenance increases the life of machines and prevents costly downtime. Executives can even use the data from the real factory in conjunction with artificial intelligence and machine learning to add even more value to existing operations. This data helps to predict future output; helps organizations envision potential problems and correct them; and allows executives to forecast accurate measures while increasing overall equipment effectiveness (OEE).
Lessons for Reshoring at the Smart Factory @ Wichita
The Smart Factory @ Wichita (one of Deloitte’s immersive experience centers) is a 60,000 square foot sustainable space located on Wichita State University’s Innovation Campus. The Smart Factory includes a fully operational production line and experiential labs for developing and exploring smart factory innovative capabilities. As a founding member of The Smart Factory @ Wichita, Siemens exhibits a 3,000 square-foot bay and works with Deloitte and 20 other ecosystem partners to offer hands-on learning opportunities with immense value for companies looking to reshore, localize, or regionalize their operations in North America. The highly digitized production facility uses artificial intelligence, the Internet of Things, and robotics to teach companies to better manufacture products, create new business value, unlock data-driven insights, and automate (or eliminate) business processes. Companies can participate in workshops to create roadmaps for digital transformation. These roadmaps are supported by hands-on interactive experiences with industry 4.0 technologies spanning from design to manufacturing. The Smart Factory @ Wichita, also brings digital transformations to life by demonstrating how to merge existing technologies with new ones.
Additionally, the University of Wichita’s Innovation Campus facility helps companies construct new business models while boosting productivity and sustainability. Organizations looking to accelerate their digital transformation need to look no further. The Smart Factory @ Wichita is a powerful hands-on learning lab where companies can practice embracing the innovation they need for reshoring success. Thanks to this collaboration, manufacturers can learn to leverage industry 4.0 within their organizations and be more agile in the face of disruption.
Siemens and Deloitte: A Formidable Alliance
Deloitte and Siemens have leveraged their long-standing relationship and unmatched global capabilities to help companies maximize reshoring success. No other team offers this level of industry leading manufacturing expertise. Deloitte offers consulting services in industry 4.0, while Siemens provides the Xcelerator platform, the top manufacturing software in the world, to help companies build digital twins and digital threads of their products and manufacturing facilities—before they’re even built. Whether a manufacturer’s pain points are digital, organizational, or both, this strategic relationship unlocks new capabilities, data and innovations.
Interested in learning more on how Smart Factory capabilities can provide opportunities for value creation at both greenfield and brownfield facilities? Read the article.