Understanding 3D printed part strength
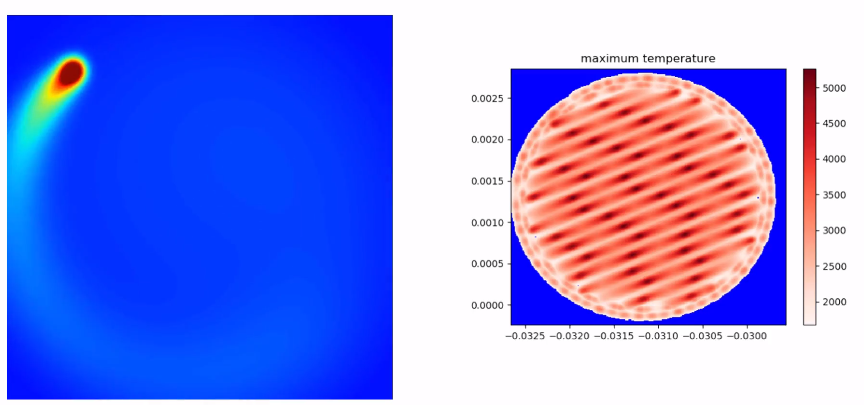
It’s not too late to watch some great discussions from Realize Live 2021 before they are gone on June 25th, one of them is roundtable discussion on printed part strength and fatigue assessment for additive manufactured components. Ashley Eckhoff is joined by Hayden Cornwell, Dr. Michael Hack and Dr. Hunor Erdélyi to understand how print strength plays a major role in industrial scale adoption of 3D printing, or AM. The full presentation will be available until the 25th, but to make sure at least some of the great information is preserved, let’s discuss some of the highlights.
Printing a metal part is, on the whole, a more capable method for manufacturing complex structures. Molds can be used in some circumstances, but not without excess engineering work to create multiple models while building up the final mold. The improvements to process with AM are not without their challenges however – melting metal powder to build up the 3D form allows microscale distortions in the material in a very different way than with casting where the material is in a similar phase throughout the cooling process. This challenge shows itself in many forms, from printing defects during printing, to altered performance characteristics in the part and even to long term changes to the durability and fatigue thresholds for the components over its lifetime. Each play into the workflows companies are adopting to fully utilize AM technologies.
At the smallest scale, it is important to understand how the material is being melted and what impact that has on the material strength. AM is such a precision process that changing one manufacturing variable can upset component quality. If all parameters are retained, but the part is rotated in the build tray, the resultant part may develop a higher likelihood for shear deformations than if it was printed in another orientation. This is why it is so important to simulate the build process of AM components, a change may seem simple, but because we are still learning the intricacies of the technology there is limited “common sense” to the process compared to more established manufacturing techniques.
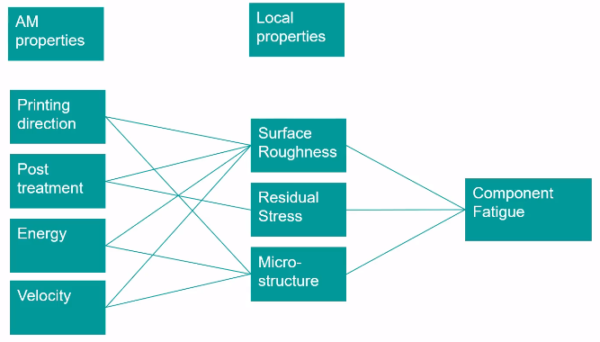
Moving up from the micro-scale to the meso-scale, a manufacturer must also understand that even if a part is not deformed, changes to the structure can result in different performance in the part. This can rear its head in a variety of ways, with one of the most common being changes in the porosity of the final components. If an area of stress concentrations is near a region of higher than normal porosity, the part may experience a ductile failure at the edge of the usable range. But these variations are not all detrimental, some designers and engineers build porous regions into their components to shed weight, improve vibration response and even change the thermal properties of the material. But as with ensuring the AM process does not produce deformations, optimizing the printed mass requires robust simulation tools to understand not just how the material will respond after production but that it will be able to be printed.
For the full story, including how machine learning plans into Siemens’ solution for the adoption of industrial scale additive manufacturing, make sure to register for realize live and watch this roundtable discussion before June 25th. We have so many to innovations to share about our work in additive manufacturing and Realize Live is the best place to get all of it in one place, we hope to see you there!
Siemens Digital Industries Software is driving transformation to enable a digital enterprise where engineering, manufacturing and electronics design meet tomorrow.
Xcelerator, the comprehensive and integrated portfolio of software and services from Siemens Digital Industries Software, helps companies of all sizes create and leverage a comprehensive digital twin that provides organizations with new insights, opportunities and levels of automation to drive innovation.
For more information on Siemens Digital Industries Software products and services, visit siemens.com/software or follow us on LinkedIn, Twitter, Facebook and Instagram.
Siemens Digital Industries Software – Where today meets tomorrow