Digital Part Production – synchronized part production – ep 3. Transcript
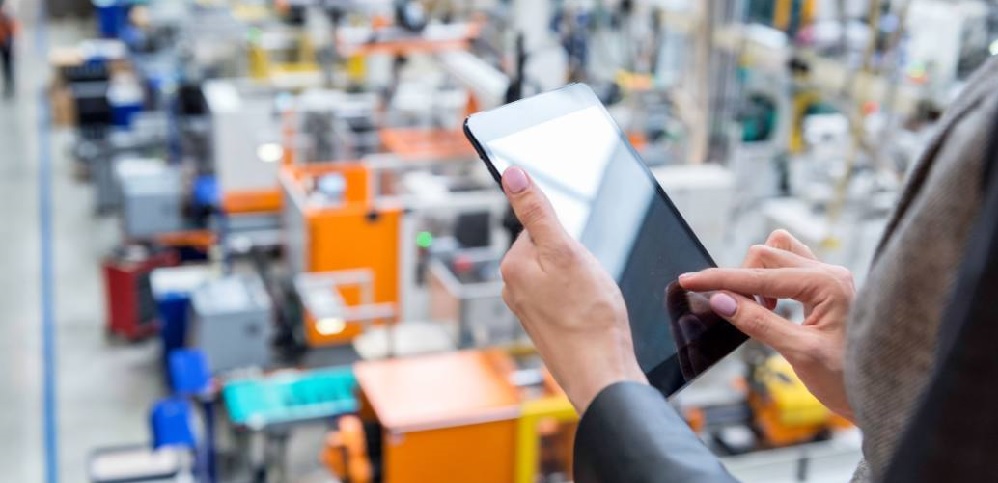
The flow of manufacturing information is becoming more complex as authoring and collecting data across diverse people and processes in an organization is a significant challenge in combining automated and manual information. Subsequently, manufacturers must leverage this data into their decision-making, using organization and structure.
Information must be leveraged to make good decisions; otherwise, it leads to mistakes and waste across the full product lifecycle; from the office in the supply chain and delivery of parts, raw product, to the shop floor and where the parts are produced. It’s unfortunate that manufacturers don’t realize there are more efficient and less error-prone approaches they can implement.
Manufacturers and machine builders are facing the challenge of increasing complexity in new machine introductions. Siemens provides solutions for these challenges with Digital Part Production (DPP), which is the process of having a fully connected digital thread, merging the digital world and the physical world to create a continuous digitalized communication process with several differentiators.
DPP is a combination of different solutions connected in the Siemens portfolio, including highly automated CAM, synchronized part production and additive manufacturing. This podcast focuses on synchronized part production.
Joining us are engineering experts Rahul Garg, Vice-president of the mid-market program at Siemens Digital Industries Software, and Brad Rosenhamer, Portfolio Development Executive for Siemens Part Manufacturing Software portfolio.
Read the transcript, below, or listen to the audio podcast:
Read the transcript:
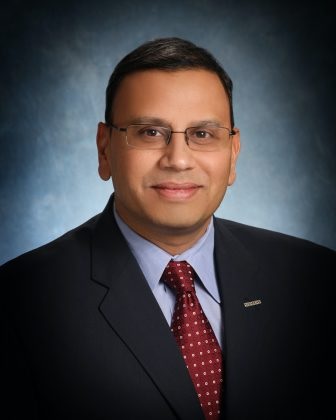
Bill Butcher: Hello everyone, and welcome back to Siemens Digital Industries Software podcast series on Digital Part Production brought to you by the Siemens Digital Thought Leadership team. I want to welcome you back to the series, Rahul Garg. As you may recall, Rahul is the industry leader for Siemens Industrial Machinery industry. And we’re excited to have to join us today with this episode, Brad Rosenhamer. Brad is a Portfolio Development Executive focused on manufacturing operations, industrial machinery, heavy equipment and automotive markets. Guys, thank you very much for being here today.
In our last two podcasts, we talked about the evolution of technology within the machinery industry and the key trends that continue to shape the industry today. We also introduced the Digital Part Production solution at a high level where Rahul, as you may recall, you discussed the three key differentiators: highly automated CAM, synchronized part production and additive manufacturing. In our last session, we discussed machine manufacturers’ benefitting from automating their manufacturing process and using highly automated CAM solutions that allow OEMs to reuse proven data that automates programming and optimizes machine processes to deliver consistent results. I think we did a pretty good job of highlighting how companies can benefit from programming tools that feature advanced machine technology. It includes supporting automated transitions, single-pass material removal and methods that shorten cycle times.
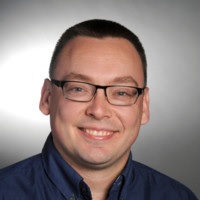
In this session, will be discussing the advantages of synchronized part manufacturing strategies, and specifically how equipment manufacturers can improve their planning by adopting a closed-loop manufacturing process. They are executing and improving their manufacturing plan by introducing intelligence into it. So, Brad, let’s start the conversation with you. What are the specific challenges that machine builders face as they try to improve efficiencies and the quality of their part manufacturing process?
Brad Rosenhamer: Most manufacturers today struggle with getting the correct data to the right person at the right time during the manufacturing process. Manufacturing information flow is becoming more and more complex as authoring data and collecting data continues to occur across a greater diversity of people and processes in your organizations – and whether that’s automated or manual, bringing all that information together is a real challenge. So, manufacturers look to leverage this information into their decision-making. But without applying organization and structure to the data, the results are ad hoc. When data is not leveraged to make good decisions, it leads to mistakes and waste across the entire product lifecycle, all the way from the office in the supply chain and delivery of parts, raw product, to the shop floor and where the parts are produced. Unfortunately, manufacturers don’t realize there are more efficient and less error-prone approaches they can implement.
Bill Butcher: Well, you mentioned mistakes and waste, and we talked on this series several times about customization. Customization is a huge opportunity for manufacturers today. So, why is it essential to have a synchronized part manufacturing process, and what are some of the risks in not doing so?
Brad Rosenhamer: Yes, with the industrial machinery industry, and it becoming more and more complex as machinery companies add more customizations into their modularized machines, these customizations do not change the desired delivery schedules that their customers expect. They don’t change the price points generally; they’re just really looking to have exactly what they want when they want it. The scenario would be doing this while delivering it in a lean manner. The solution requires synchronization of customer-configured components that in the past were standardized. These components have challenging geometries with tighter tolerances but always with lower lot sizes. And introducing this variation into the product creates a new supply chain problem that requires synchronizing component part production while minimizing inventory. Therefore, they are applying all the lean concepts to these parts that applied to the standardized parts of the past. If it’s not synchronized, then part inventories must increase, and warehouse space must accommodate that increase, with longer lead times. Ultimately, this affects the organization’s competitiveness in an industry where speed and capability are critical aspects of that business.
Bill Butcher: It brings up another point too. So, Rahul, when we talked about connected processes and digitalization as we have throughout this series, we need to include in the conversation the concept, of course, of the digital twin. So, what is unique about the digital twin in the context of digital part production and synchronized part manufacturing?
Rahul Garg: A digital twin can automatically capture all the design simulation and machine parts into a central repository. This synchronization requires integrating quality plans at critical points in the process. So, for example, using inline inspection to ensure good machining time is not wasted on a part that is already scrapped. It helps to reduce the overall time to delivery, and obviously, maximizes the production capacity. The leveraging the integrated toolchain of the whole CAD, CAM, CNC process cuts translation errors and speeds up the overall process. Therefore, Siemens brings some unique capabilities with a well-integrated solution, from design to machining to cutting parts. We are probably one of the only vendors in the world that can bring that integrated CAD, CAM CNC solution. We have got some unique customers who are already taking significant advantage of these. I think we spoke about all these customers; PM Bearings for example, in the past, making high precision linear bearings. And by taking advantage of this integrated solution, they were able to reduce their programming time by up to 80 percent on the workpiece tooling and then overall on the machine’s usage.
Bill Butcher: Yes, and I know we’re going to spend a little time in this session to talk about another customer example. But to continue down that path a little bit further, can you outline the benefits for those manufacturers that incorporate synchronized part manufacturing into their process?
Rahul Garg: Yes. Equipment manufacturers can improve their total planning by adopting a closed-loop manufacturing process. Obviously, as part of that whole improved planning, they maximize their resource utilization in the factory. The factory where parts are being manufactured is one of the highest-cost items. And the more you can improve the utilization, the better it is to the overall profitability, in which case this process becomes efficient. So, all the labor and quality content from part order is tracked back to the digital twin for traceability, for process improvements, and can help further with cost reduction. Machine shops can be dynamic environments with scheduling changes happening every day and sometimes every hour. And having a flexible scheduling tool allows them to put all the bill of processes, the recipes right up front and help them determine the best path forward and the best utilization of their resources and the machines. And then, the analytics built on the accurate model during the production process can help provide that closed-loop feedback to ensure that the production is fully optimized and can help make manual improvements on otherwise manual process.
Bill Butcher: And synchronized part production is one of the three main differentiators that we’ve identified for this solution, and we’ve discussed digital connectivity. Let me ask you about connectivity at this level between the differentiators of highly automated CAM, synchronized part production and additive manufacturing. Why is it so critical that manufacturers look at the sum of all manufacturing processes instead of just focusing on one area at a time?
Rahul Garg: This is a great point here, Bill. Today, in many manufacturing shops, the processes have evolved, and they have become siloed, and becoming optimized in that silo and process. Still, they have not been optimized throughout the entire process. So, this is where the whole synchronized part production can help in a significant way. Part manufacturers can take advantage of a continuous thread of information from engineering through manufacturing, planning, and execution to ensure optimized scheduling, ensure optimized control traceability and quality, and eventually compress the delivery schedule. Time to delivery is not going to change, and anything you can do to improve will become a significant advantage for companies. And manufacturing planning solutions that capture all the needed information, all the necessary data for the work, bringing all of that together and serving it down to the operator makes it very easy to ensure that the work gets done to the highest possible quality. And more importantly, it drives flexibility into the process and provides invaluable aspects in a hectic and dynamic shop environment to control it better. And companies that can optimize throughout this flexible, transparent, data-driven decision-making process are eventually going to be the ones that are going to be the winners. This process is accomplished by managing a digital twin that can help you retain your labor challenges: quality reporting, material genealogy, quality states sequencing – all of which can be made available through a digital twin and a digital thread process.
Bill Butcher: I think that’s a good example of looking at the sum of all the manufacturing processes and the benefits of integrating them. Brad let me come back to you. Are there any other examples of companies that have taken this holistic approach that Rahul just described and implemented? And if so, what kind of benefits have they received?
Brad Rosenhamer: There’s a small company with a long reach founded in 1967 in the southwest of France called Proform. At first, it specialized in the cold forming of tubes and then quickly became a specialist in the bending of all types of stainless steel and nickel alloys. Today, Proform is a critical player in the market dedicated to manufacturing complex tubular parts and participates in several industries, including chemicals, pulp and paper, food and beverage, pharmaceuticals, aerospace and even automotive. Proform’s know-how includes cold bending and shaping, hydroforming, crimping and welding. They looked at some business challenges where they needed to implement a scheduling solution that can keep pace with the company’s growth. When you’re looking at growth, there is a challenge to see how you can utilize existing assets to keep up; frequently, taking months, if not years, to increase that capacity. So how do you manage all your customers’ expectations for deliverables? That’s a huge business challenge. When managing diverse materials, part types and deadlines, there are different industries with various part types, increasing asset utilization time to deliver the business’s profitability goals best. Then, there is a need to increase your manufacturing capacity. Anytime you’re growing that way, it’s a huge challenge to scale sustainably. So, those were a lot of their business challenges. The key to success is anticipating the spikes or lows in the workflow, whether resource capacity, employee availability or incoming supply changes. The ability to predict and model them before they happen can give a competitor an advantage in a market because they can best prioritize their deliverables across any of those conditions.
They optimized the use of the raw materials, which was a key to their success. They were putting their raw materials toward their best customers, toward their highest profit products and toward their best opportunities. Also, they were improving project management capabilities, knowing where they need to invest and how to manage those things in the future. The results speak for themselves. They increased the administrative efficiency of their work centers by 87 percent, meeting deadlines and achieving a 96 percent best-in-class on-time delivery rate, and then multiplied their workload by 20 times. This improvement reduced the number of people administrating their work centers from three to one. Thus reducing the number of changeovers, reducing the demand, minimizing the machine changeover, and contributing to a twenty-times multiplier increase. We even have a quote from them: in 20 years, the workload has been multiplied by 20. Three people within the planning department dealt with 30 work centers running eight hours a day in the past. Whereas now, one person in the department deals with 260 work centers running 24 hours a day. I think that speaks to what a good scheduling tool can do for you and how it can respond to the market demands.
As a result, the company now better anticipates the critical situations and when they’re going to occur to know precisely what they’re going to do. They can enable their staff and push their decisions down in their organization so that the area’s manager is able to recognize the condition occurring and make a decision sooner to the time they anticipate that change occurs, and sooner to the time where it mitigates that impact. They have reliably met their deadlines for their customers’ deliveries. They optimized their manufacturing supplies, knowing this can also impact how you do your maintenance and plan your maintenance on your machines. It reduces their manufacturing waste because they have fewer changeovers occurring. They capitalize on their technical data, getting the correct data to the right people at the right time, as we talked about earlier. And they are then improving project management so that as they’re introducing new capabilities into their organization, doing it in a planned and progressive way. And then lastly, just simply increasing their working capacity: being able to produce more product with the same number of assets, the same number of resources, ultimately, this is what everyone is trying to achieve – and what they achieved.
Bill Butcher: This is a great example, Brad; thanks for sharing that with us. And some of the metrics on the results are over-the-top impressive. It’s clear through this story how part manufacturers can increase operational efficiency by using one integrated system to design, simulate and machine parts. Thank you both, Rahul and Brad, for the time and information you shared today during this podcast on synchronized part manufacturing. And I hope you will all join us again as we wrap up our series in the Digital Part Production Solutions for Industrial Machinery in our next episode.
During that podcast, we’ll be taking a deeper dive into the topic of additive manufacturing and how this technology can provide an advantage to part manufacturers by creating complex geometries that would be difficult or impossible to achieve with traditional manufacturing methods. Until then, this is Bill Butcher saying thank you for joining us.
Siemens Digital Industries Software drives the transformation to enable a digital enterprise where engineering, manufacturing and electronics design meet tomorrow.
Xcelerator, the comprehensive and integrated portfolio of software and services from Siemens Digital Industries Software, helps companies of all sizes create and leverage a comprehensive digital twin that provides organizations with new insights, opportunities and automation levels to drive innovation.
Listen to the DPP Podcast03 for the audio podcast.
Also, for more information on Siemens Digital Industries Software products and services, visit siemens.com/software or follow us on LinkedIn, Twitter, Facebook and Instagram.
Siemens Digital Industries Software – where today meets tomorrow.
About our experts:
Rahul Garg is the Vice President for Industrial Machinery & SMB Program, responsible for defining and delivering key strategic initiatives and solutions and global business development. He and his team are responsible for identifying key initiatives and developing solutions for the industry while working closely with industry leading customers and providing thought leadership on new and emerging issues faced by the machinery industry. Rahul’s experience and insight are derived from 25 year career delivering software-based solutions for product engineering and manufacturing innovation for the global manufacturing industry, spanning a career in R&D to program management, sales and P&L management and having focused exclusively on the industrial machinery and heavy equipment industry since 2007.
Brad Rosenhamer is a Portfolio Development Executive and experienced Senior Director of information Technology, focusing on infrastructure and application, with a demonstrated history of working in the mechanical, electronic and industrial engineering industry. Brad is skilled in value-driven business process strategy, development and implementation.