Additive manufacturing beyond design
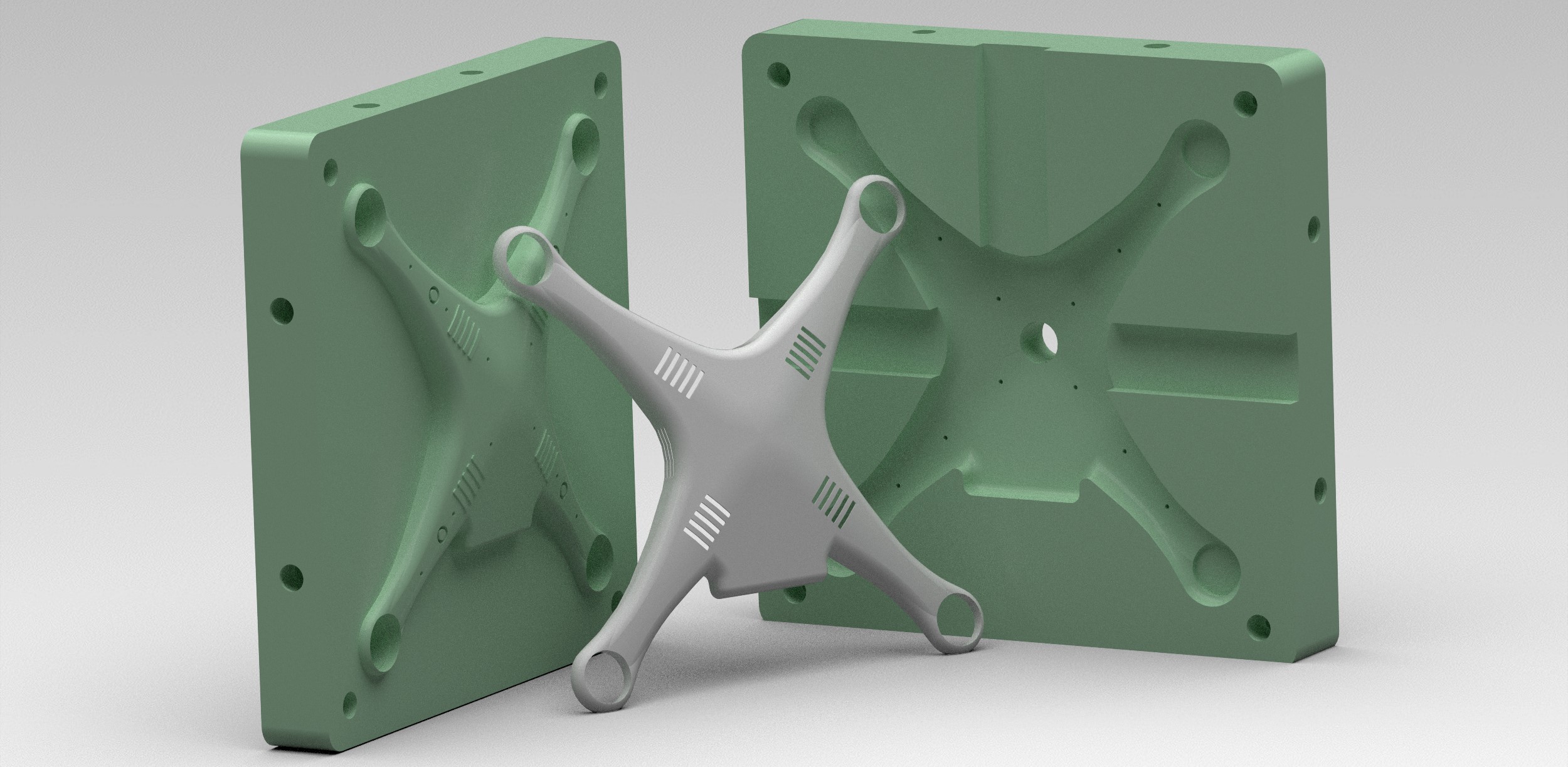
Additive manufacturing (AM) is still a relatively expensive method for component manufacturing when little to no customization is required. As long as a company intends to manufacture at high volume and low mix, AM will not be the primary manufacturing tool. That does not mean there is no benefit of AM, in fact many companies are implementing the technology as an aid to more traditional manufacturing processes – think CNC, injection molding and casting – to further accelerate these highly optimized processes. One of the most common of these acceleration tactics is to print the molds for injection molding, instead of waiting weeks or even months for a new mold on top of the high investment.
Printing the molds has multiple tangible benefits beyond lowered investment in new product lines. For increased part performance and longevity, cooling channels can be added to the molds. If a mold needs to be made of a more valuable material, because of reactivity or other constraints, printing it greatly reduces the amount of wasted material and the total cost of the part. And, depending on the additive technology, repairs can be made to existing molds to prolong their usable life near indefinitely. Applying AM to mold making creates a handful of unique problems that require extra though after the final product has been designed.
Injection molds operate at high temperatures, with rapid movement and are often quite large. Combine that with the smooth surfaces required inside and a standard AM workflow is not going to cut it, literally, many mold making workflows augment the AM process with milling in a hybrid AM process.
Splitting
The first step is to split the original geometry of the final part into manageable chunks for the printer. This could be along planar sections of the final model or from extracted faces – a must for organic geometries. Splitting a mold for AM production can take more upfront work in the design software than just milling a solid block, but this time will be balanced with the overall speed of the manufacturing process.
Arrangment
In the top CAD/CAM design environments for AM, the next step is fairly straightforward and, in some instances, automated to the specific machines being used – arranging the part. Not only does the final volume need to fit within the printing volume, the geometry needs to be operable across the entire component. This is not a much of a problem in laser powder bed fusion devices but can become an issue for multi-axis direct energy deposition machine since the print head move around the component.
Tool path plan
The next step is the same for both AM and milling procedures, aside from a few edge cases – path programming. If 5-axis applications, the orientation of the tool head while printing is far more important than for milling because AM needs to contend with gravitational effects. By printing normal to a surface, this effect is minimized. There are other caveats as well, tight corners for example produce a concentrated heat aera that can deform the material in AM operations. More of these examples can be found in a much more in-depth discussion on Mold Making Technology.
Verification and post processing
If using a hybrid AM machine, the next step would be to create the post processing path, likely with a milling head. This creates the required smooth surfaces for mold injection, just as is done with a standard milling operation but in a fraction of the time and far less scrap material. Without a hybrid AM machine, one would need to verify the tooling paths created previously for kinematics, collisions and voids. Barring those the part is printed, mounted and post-processed in a separate machine.
Whether using a hybrid 5-axis machine for AM mold fabrication or a combination of powder bed fusion and traditional milling, an end to end digital solution is key to refrain from jumping between multiple software environments before getting your part. Siemens NX software has you covered to accelerate the design and production process as a part of the Xcelerator portfolio. If you are looking for more information on AM from Siemens, check out our website on additive or register for Hannover Mesa for our virtual AM experience in April.
Siemens Digital Industries Software is driving transformation to enable a digital enterprise where engineering, manufacturing and electronics design meet tomorrow.
Xcelerator, the comprehensive and integrated portfolio of software and services from Siemens Digital Industries Software, helps companies of all sizes create and leverage a comprehensive digital twin that provides organizations with new insights, opportunities and levels of automation to drive innovation.
For more information on Siemens Digital Industries Software products and services, visit siemens.com/software or follow us on LinkedIn, Twitter, Facebook and Instagram.
Siemens Digital Industries Software
– Where today meets tomorrow.