Cooperative design for AM
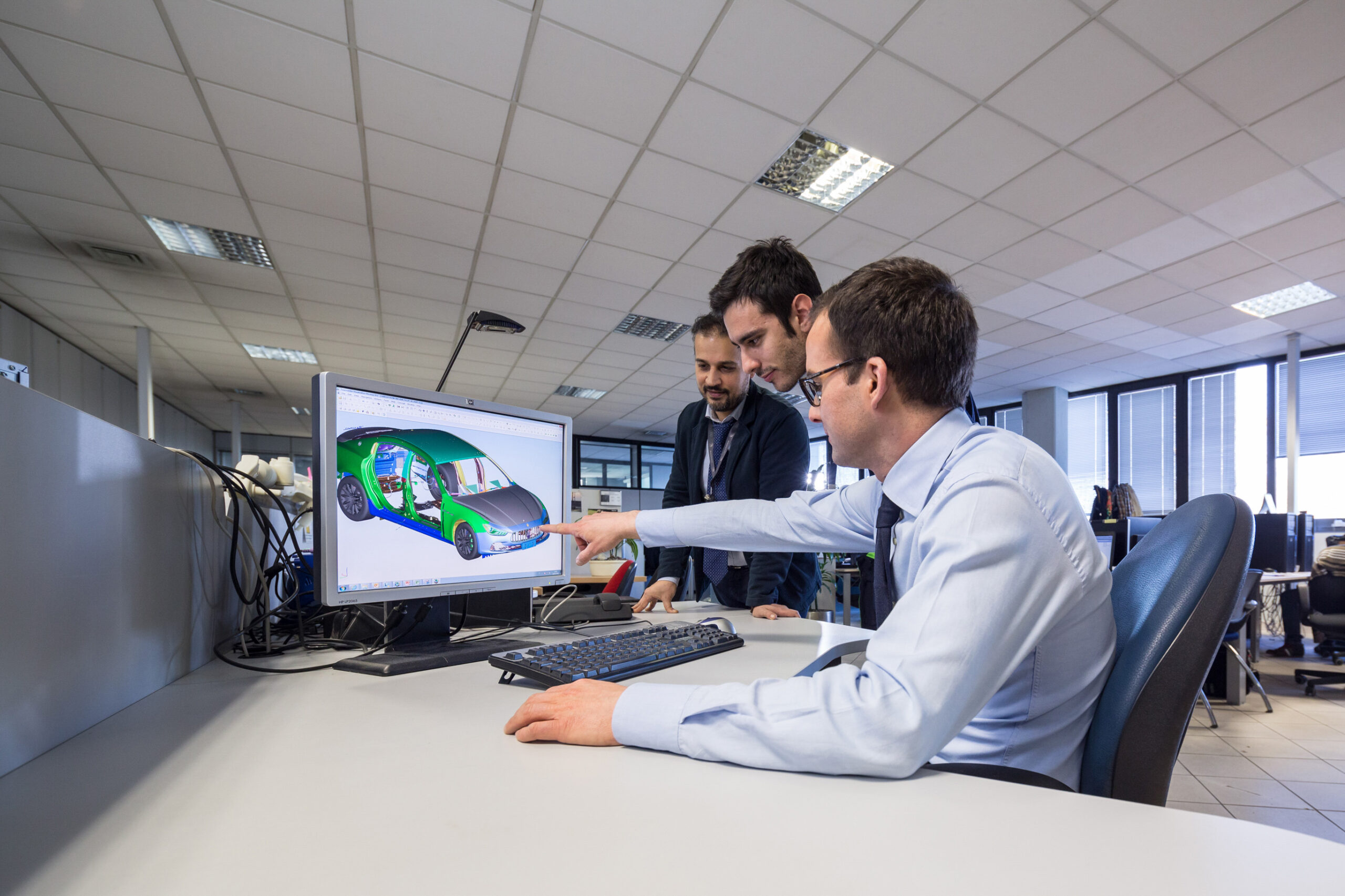
Additive manufacturing (AM) may not be ready for high volume production, and no where near the scale of injection molding processes. But that may not be the final use case for this amazing technology. Because AM has shed so many of the limitations imposed by traditional manufacturing methods, the design possibilities are numerous. From consolidating entire assemblies into a single part, printing organic geometries without expensive one-time-use molds or adding complex structures to a design. With all these cases for the adoption of AM, there is one hurdle beyond the technological advancements – the need for cooperative design, manufacture and service.
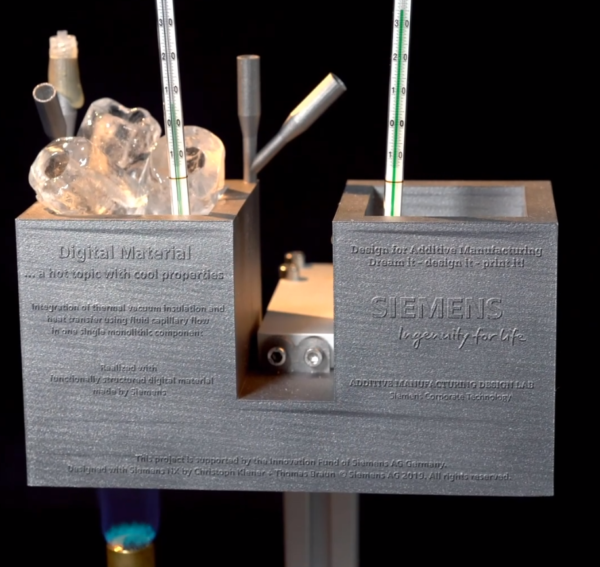
The goals almost every company lists as the benefits for AM are based around cost, efficiency and flexibility. These are admirable goals for a business, but they do not speak to the complete potential of the technology. Instead, AM can be leveraged to combine not only systems, but entire engineering domains. This goal is exemplified in Dr. Christoph Kiener’s recent demonstration of a monolithic heat pipe at Siemens’ FormNext Connect. The project involved innovative printing methods to attain porous metals, complex heat transfer calculations for, the physics of fluid wicking and much more.
For reference, the device above works by moving a condensed working fluid and its vapor phase between the heating area above the burner and the hot-water side (used as a thermal sink). This is all done through variating the porosity of the internal structures, encouraging capillary action. The cold side is also protected by a vacuum layer within the body to force as much heat as possible into the working fluid instead of the ice.
Each of the domains required field-expert input and collaboration in attaining the final design. Today it is rare to see an individual complete a product from concept to production, but even when there are teams working on a project it is often a group of similarly trained individuals. This becomes more evident moving to larger and more complex systems where each domain of the design pulls their specific systems from the complete product and interfaces are validated on re-connection. This works well for automotive and aerospace companies working on connected systems, especially with a digital twin approach, but when there is only a single part, communication needs to be available from the start.
For the heat pipe example, that means finding a common solution between the material scientist working on the porous metal, the chemical engineer choosing the working fluid for heat transfer and even the manufacturing team ensuring the final design can be printed. Each team member brings their expertise to accurately and efficiently deliver the combined system. Comprehensive simulation environments and multi-domain software packages help with this tight communication between engineers, designers and manufacturers.
The same can be said for another Siemens AM application example – the fennel bulb burner. To consolidate a system of multiple components manufactured separately and joined later, the fennel bulb was created. All air, fuel and cooling lines were integrated into the burner head to improve production time, reduce weight and make the entire system more efficient. The burner was successfully integrated with fluid flow paths but required multiple knowledge domains to ensure the fuel and air would not mix prematurely nor create undue risk around flammable materials.
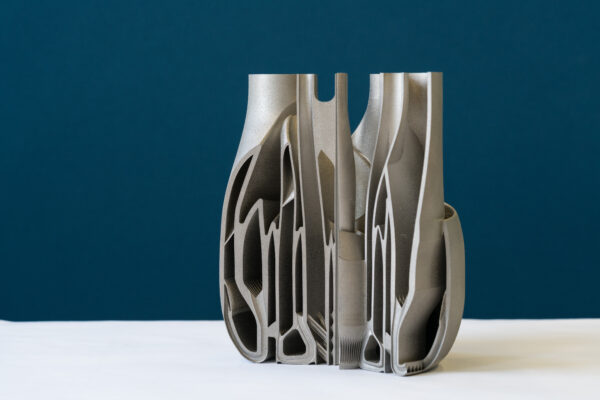
But these examples only begin to scratch the surface of what could be possible with additive manufacturing. With more work in 3D printed circuit boards, components could be directly integrated into a system just as parts are being consolidated today. Hydrodynamic bearings could be printed in a single assembly. And as we learn more about the possibilities of the technology, who knows how AM could be integrated with other technologies and disciplines.
The future of additive manufacturing is still ahead of us and while sophisticated software and brilliant minds are improving it, there is still work to be done before AM reaches the ubiquity of the traditional manufacturing methods – CNC, casting, molding, etc. And while AM may never surpass these techniques in terms of production volume, or gain dominance in tailored use-cases, it will find its place as a go-to method for the custom, complex and innovative products of tomorrow. Siemens’ work in additive manufacturing is where today meets tomorrow.
Siemens Digital Industries Software is driving transformation to enable a digital enterprise where engineering, manufacturing and electronics design meet tomorrow.
Xcelerator, the comprehensive and integrated portfolio of software and services from Siemens Digital Industries Software, helps companies of all sizes create and leverage a comprehensive digital twin that provides organizations with new insights, opportunities and levels of automation to drive innovation.
For more information on Siemens Digital Industries Software products and services, visit siemens.com/software or follow us on LinkedIn, Twitter, Facebook and Instagram.
Siemens Digital Industries Software
– Where today meets tomorrow.