NX Webinar – next generation design equipment
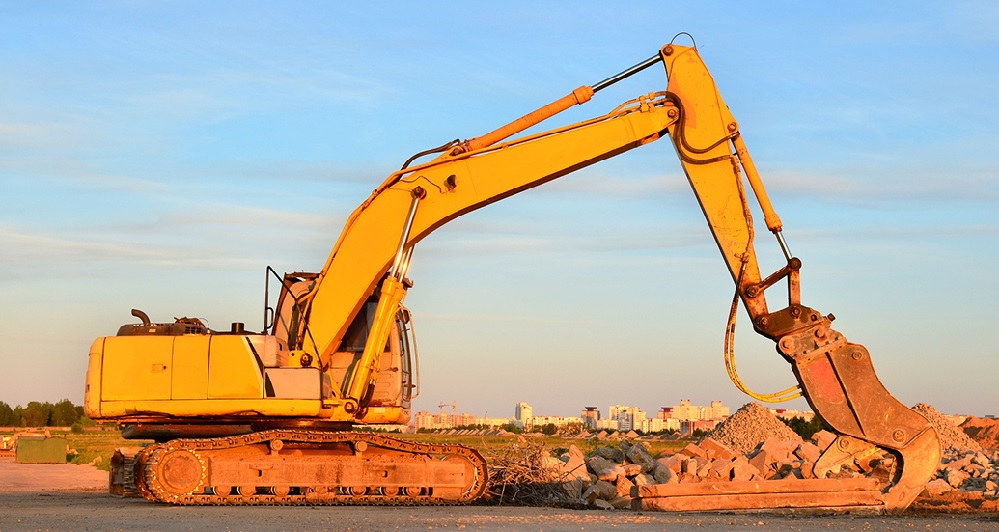
In the following webinar, Hendrik Lange, Director of Heavy Equipment at Siemens Digital Industries Software, and Thomas Spangler, Senior Marketing Manager of Product Engineering Software, provide pertinent information regarding next generation design equipment.
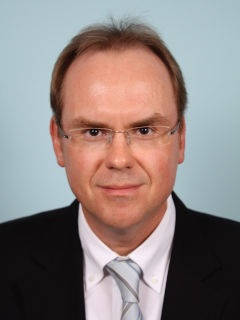
Today’s heavy equipment world is not merely the sequential design, building and commissioning of a product. Single discipline tools and isolated parts are not enough to address complex engineering. The next generation of design engineering technology understands the product and how all the different engineering disciplines come together in digitalization.
Therefore, digitalization is not an option but a necessity. A digitalization chain impacts several areas of people’s lives, including how they stay informed, how they purchase items and how to manufacture products.
Also, it affects business models. The pace of innovation and the ability to disrupt it are crucial to succeeding. Subsequently, this increases the pressure on enterprises in all industries to open new business opportunities.
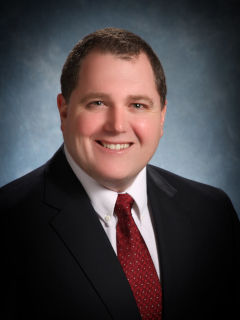
Global trends in heavy equipment
The heavy equipment industry is being significantly impacted by global trends in these key areas: agriculture machinery, construction equipment and mining equipment. Heavy equipment is rapidly becoming very complex due to increasing variance, connectivity and automated operations. Additionally, there are regularity changes in sustainability, emissions and safety.
At the same time, market trends and globalization are influencing heavy equipment. The Asia Pacific region represents the largest and fastest-growing regional market. So, as new players enter the market, companies must differentiate themselves to stay competitive, emphasizing performance. And labor shortages are occurring on a global scale, making it difficult to find qualified manufacturing personnel for specialized equipment. Moreover, European cities are planning to ban internal combustion engines – with other counties soon to follow. Additionally, various soils and environments can result in stress on a machine, which affects both design and complexity. Finally, global manufacturing distributions result in lower labor costs in some markets offset by higher shipping prices, thus driving the need to service equipment locally.
Growing design complexity
All these factors are driving design complexity in the heavy equipment industry. These include an increase in the number of variations to accommodate regional markets, and new production processes are emerging that provide greater flexibility to the end-user to adapt to market demand. Also, market segments are becoming narrowly defined with specialized machines. End users are demanding all levels of connectivity between machines, operators and work sites to optimize their use of heavy equipment. This connectivity creates large amounts of data to be analyzed and used for increased efficiency.
Connectivity enables autonomous operations, which is widespread in heavy equipment, to improve land utilization and promote agricultural efficiency. This is driving more electronics and electromechanical systems into heavy equipment. Additionally, governmental regulations for heavy equipment are increasing in emission reduction. For example, the United Kingdom is requiring a nearly 100 percent decrease in CO2 emissions by 2050.
Safety is also crucial to companies, with operators running machines all day. There is the need to reduce equipment fatigue, while maintaining productivity and reducing downtime. Also, there is a push toward new powertrains and lightweight designs to improve quality and performance while reducing costs. Therefore, validating these designs upfront, against market and government requirements, is vital to global competition.
The result is a need for improved product design processes to address customer, competition and governmental pressures for achieving zero harm, zero unplanned downtime and zero emissions. Autonomous operations also require simulation to ensure reduced worksite and operator hazards. Thus, the interconnected work site decreases risk by providing better operator information and job site coordination. Whereas, lightweight designs and innovative powertrains help reduce emissions and improve fuel economy.
To deliver greater innovation at higher quality and lower cost, heavy equipment companies need comprehensive 3D product design. Siemens’ integrated and intuitive solution suite, with broad and deep best-in-class capabilities, allows design teams to explore multiple machine or mechanism solution approaches to quickly arrive at the most cost-effective, innovative, functional products. It is now possible to build larger, more sophisticated and comprehensive models that encompass all design features to overcome the challenges of validating multi-configuration requirements.
Siemens is helping heavy equipment companies to create products in a digital environment to optimize their performance digitally before committing to a physical prototype. This is a holistic approach that provides transparency across various engineering disciplines—mechanical, electrical, software and fluidics—creating tomorrow’s advanced heavy equipment.
Siemens Digital Industries Software is helping drive transformation to enable a digital enterprise where engineering, manufacturing and electronics design meet tomorrow.
Xcelerator, the comprehensive and integrated portfolio of software and services from Siemens Digital Industries Software, helps companies of all sizes create and leverage a complete digital twin that provides organizations with new insights, opportunities and automation levels to drive innovation.
For more information, view webinar, visit siemens.com/software or
follow us on LinkedIn, Twitter, Facebook and Instagram.
Siemens Digital Industries Software – Where today meets tomorrow.
About our experts
Hendrik Lange is the Director of Heavy Equipment at Siemens Digital Industries Software since 2012. That same year he was appointed as the industry lead for the heavy equipment industry. Previously, he supported the industry lead for the automotive and transportation industry as Director of Automotive and Transportation. He was also previously was responsible for automotive industry marketing in EMEA, and worked in various roles in pre-sales, post-sales and business consulting in Germany. Before joining Siemens in 1999, Hendrik worked for EDS in Germany and in Charlotte, North Carolina. He holds a master’s degree in mechanical engineering.
Thomas Spangler is the Senior Marketing Manager of Product Engineering Software. Tom has more than 25 years of experience in CAD and CLM, including 15 years in design, IT and data management in the automotive industry at both the OEM and supplier levels. Tom completed his master’s degree in Business Administration in 2006 and joined Siemens in 2008 as a marketing manager. He has created and contributed to multiple product launches, marketing campaigns and other initiatives.