How to fly the electric aircraft before you build it
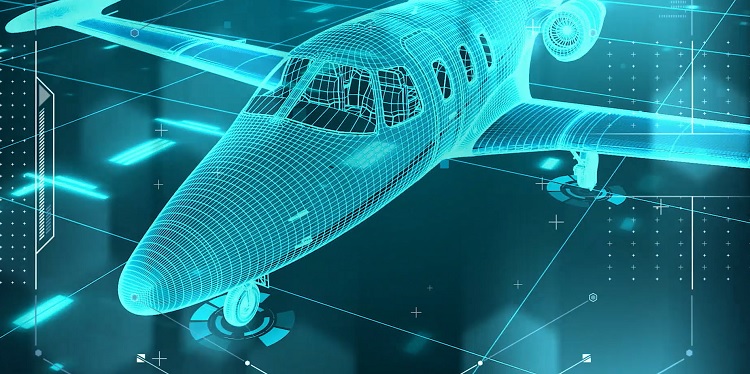
Where today meets tomorrow: how simulation software is bringing innovative changes to the aerospace industry
In our previous blog, Transitioning aircraft propulsion from carbon to electrons, we discussed aircraft transitioning from aviation fuel to electricity and how electric propulsion could potentially change how they’re designed.
Now, I’d like to talk about the technology needed to develop a fully electric aircraft. How can manufacturers design and produce aircraft and components that meet requirements for new electric aircraft type certifications? Without the time or expense of testing that was conducted decades ago, what software and technology can prove reliability and safety before building the aircraft?
The aircraft certification process guides companies in demonstrating flight characteristics, reliability and structural integrity. Traditionally this process involves a significant amount of testing requiring expensive physical prototypes that could take months or even years to build and evaluate. With the advancement of design and simulation capabilities, however, the balance between test and simulation is shifting more and more to play complementary roles. This leads to more thorough assessments of an aircraft’s capabilities and ultimately a safer design on significantly faster schedules and lower cost.
For new aircraft designs, especially electrically propelled flight vehicles, this shift will require aircraft manufacturers to develop new capabilities for proving designs. So too, the certifying agency will need additional skills to review the design and oversee the test and simulations assuring compliance with applicable standards.
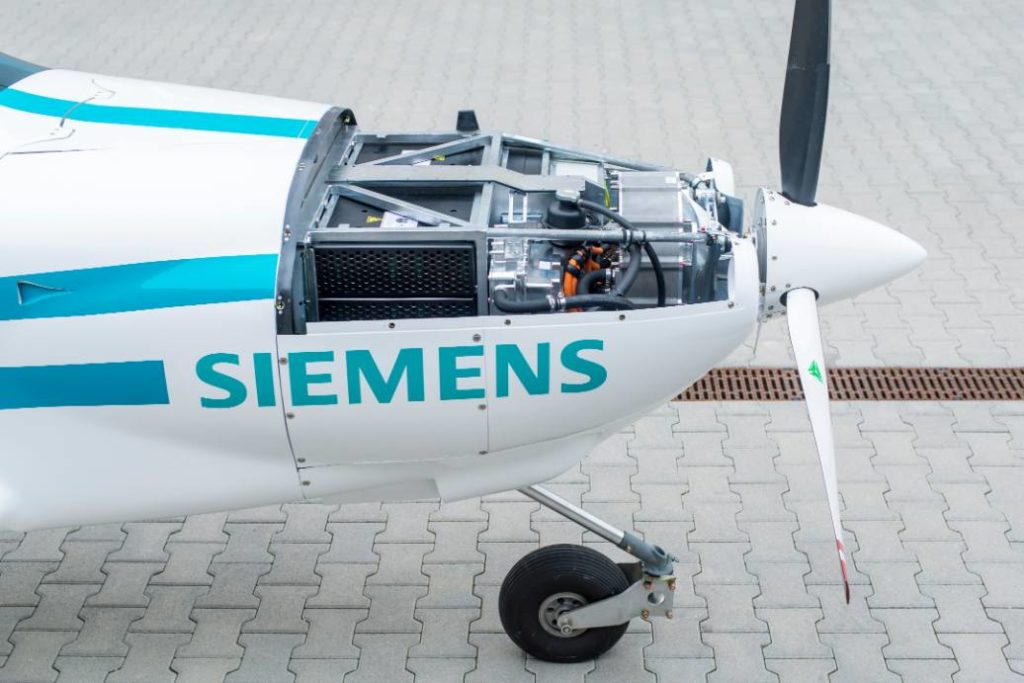
The technology to build electric aircraft
When gas turbine aircraft engines were first developed, many operational variables couldn’t be accounted for in the design. Consequently, failures had to be witnessed in-service. Our ability to utilize simulation avoids this trial-and-error approach or actual in-flight failures during the introduction of a new kind of propulsion system. The capacity to do this effectively is key to the rapid evolution and application of new electric propulsion systems.
With electrical systems, there is a broad design envelope and engineers must filter through choices that yield the safest operation at the lowest maintenance cost and at the lowest cost-per-hour of operation. Instead of needing decades to go through the evolution of engine design, it can be simulated upfront in a matter of weeks or months.
These simulations must encompass both the mechanical and electrical aspects of the design to be fully predictive. It is here that the concept of a comprehensive digital twin becomes so important. The digital twin captures all aspects of the function and production of the aircraft in a virtual environment. In this way, capturing a total understanding of the product and the processes necessary to manufacture it can be used to optimize the aircraft.
For example, lightweight design is critical for the function of an electric aircraft. Utilizing weight-saving materials like composites are a huge advantage in aircraft design, and with electric planes it is crucial. Minimizing weight enables an electric aircraft to fly farther on battery charge. So fully optimizing the aerostructure by creating a digital twin makes electric aircraft even more attractive as alternatives to conventional aircraft.
With an electric plane, the electric system is not just there for propulsion. It’s system critical to the overall operation of the aircraft. Unlike a scenario in which part of an aircraft system might fail on a gas turbine, but has the ability to fly, an electrical system must be structured to avoid any potential dependencies that could lead to larger system failures.
Engineering teams consider a wide array of potential flight scenarios. There are predictable scenarios such as temperatures and altitudes, but also interactions of flight conditions that may not be intuitive. For example, aviation systems are designed with multiple levels of redundancy to assure safe operation even if one system fails. However, there may be failure modes that interact between different systems, such as power and control. Modeling the performance through failure modes and effects analysis (FMEA) gives critical insights to help mitigate the risks inherent in new flight technologies, which may also include significant software as part of its operation. Powerful simulation technology supporting FMEAs for the overall system is essential to understand whether spurious, unpredictable events could be difficult for pilots to manage.
The digital twin’s capability to integrate the electrical and mechanical design supports modelling the aircraft’s performance in a new way. A high-fidelity digital twin can be bombarded with different scenarios and operating environments, yielding a better understanding of system interactions. With a new technology like electric propulsion this is also extremely valuable due to the ability to do trade studies virtually without having to produce flight hardware for test.
In addition, certifying the aircraft is tied to the simulation’s ability to demonstrate a complete set of flight scenarios were considered, proving the electric aircraft will operate as designed. Ultimately, a physical version will be flight tested to fully comply with the certification requirements. By verifying that the simulation enabled by the digital twin matches physical test data, the certifying agency can be confident that the aircraft will perform as expected. Simulation via a comprehensive digital twin demonstrates the safety and reliability of the aircraft, minimizing the need for multiple physical prototypes, helping the aircraft get to market faster and more profitably.
How electric aircraft will succeed
Aircraft manufacturers invest significant amounts of time and resources to achieve even small gains in operational efficiency of their aircraft. Their customers always demand more capabilities at lower cost. To achieve market leading positions, manufacturers embark on new programs and employ new technologies to meet those demands.
Companies demonstrating the big advantages in transitioning to electric aircraft can speed up its adoption. Some manufacturers feel that by adopting electrical prolusion, they can reduce maintenance costs by as much as 80 percent. On top of that, it’s possible to extend the service interval longer than with a conventional aircraft. This lowers the overall cost of operation which helps electric aircraft fleet owners compete better in the marketplace.
Finding the key value points for an electric propulsion scenario derives from basic questions about the aircraft’s operation:
- How will it be charged?
- How much does the aircraft cost to fly per hour?
- Are maintenance costs lower?
- What kind of range will it have?
- Does it have proven reliability?
Currently there are select market segments where the scales tip decidedly toward electric propulsion: trainers, small civil, and short hop commuter flights lead the list, but there continues to be plenty of room for innovation.
How the plane will receive its electric charge is at the top of the list of operational questions and drives the consideration of what types of planes are appropriate for electric propulsion.
In some instances, the battery system itself can be removed and replaced on the ground rather than the need to plug the plane upon landing. While this technology exists for smaller aircraft (see video), the problem is uniformity at airports all over the world and whether a compatible battery, in stock and charged, is available. A fleet operation where there is a single type of plane, like a cargo plane, that has specific airports it flies into and has the infrastructure to charge and replace several 1,000-pound batteries, for example, is a possible step in the right direction.
The digital twin can even evaluate the charging system and the airport itself to optimize the entire operation.
It will also take meeting stringent certification requirements and governmental cooperation from agencies like the Federal Aviation Administration for electric aircraft to succeed. A comprehensive digital twin that includes the aircraft and its associated aviation systems can help to meet these requirements.
It also helps build everything in the virtual world before creating real parts, aircraft, systems, and even airports. With a portfolio like Xcelerator, aircraft design teams have access to the tools to design, simulate and optimize individual components, systems, and the manufacturing process before the plane takes flight.
With access to this technology, you can fly it before you build it.
Check out Fibersim, NX, Teamcenter, Simcenter, and Capital (part of the Xcelerator portfolio) in action: