Building the future of Aerospace Part II
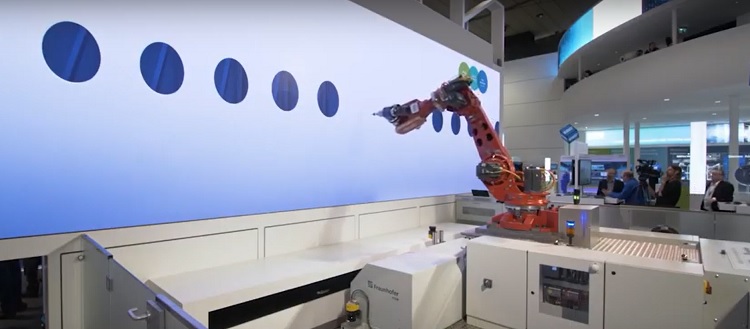
In yesterday’s blog I talked about the unusual trends driving 6,000 startups to enter the aerospace and defense industry. Digitalization and a new era of mobility and space exploration are pushing us at an innovative pace I haven’t seen in my 30+ years in the industry.
We’re in an amazing period of transition lead by such advancements in digital twin and digital thread capabilities. I encourage you to read my blog “Building the future of Aerospace Part I if you haven’t already.
In this blog, I’ll talk about some examples of how the digital twin is going beyond product design and enhancing the production and performance of the product itself.
The future of production – additive manufacturing
Additive manufacturing, also known as 3D printing, is revolutionizing how parts are designed, built and assembled. This technology paves the way to implement new materials and manufacturing technology. For instance, the geometry of a part can change when not constrained by a typical design or manufacturing process and enable putting the materials only where they are needed. A major benefit: weight and cost reduction, which are huge issues in aerospace. (Figure 1)
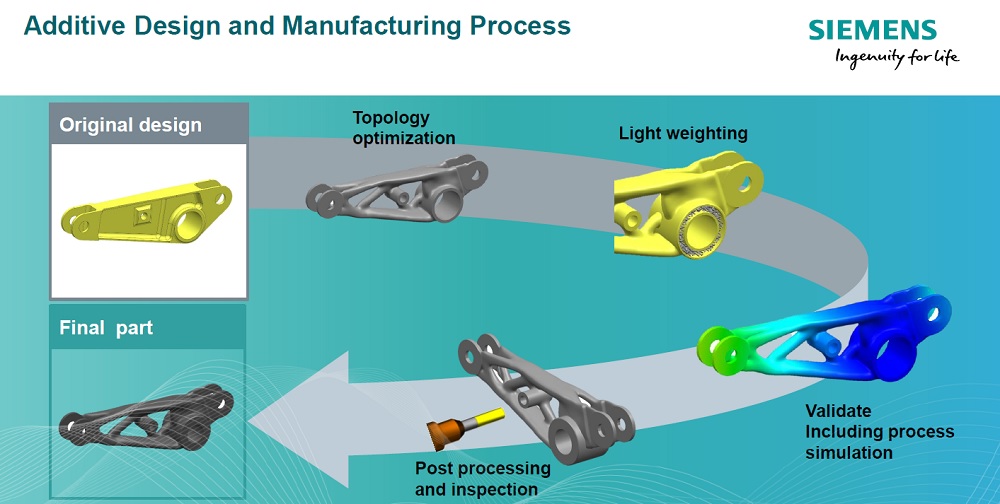
Additive manufacturing goes beyond making individual parts — it’s also enhancing products by unitizing more structures in ways we could never imagine. Light weighting of structures and additive manufacturing is one way our customers can obtain the results they need.
Oh, and here’s a wild approach that some companies are working on: within space exploration, additive manufacturing has the capability of moving the factory from the Earth into space where products can be printed on-demand. This enables much lighter structures since they aren’t subjected to loads seen during launch.
AR/VR – changing people, processes and tools
Augmented reality (AR) and virtual reality (VR) are two exciting advancements that are going to change how people work, both individually and collaboratively, to design products. This technology will give users a true sense of scale and proximity, so they have a better understanding of the design early in the product lifecycle.
Imagine having the capability to “work inside” your vehicle as you design it and locate features and components in a way that mimics how you might install or maintain the actual component.
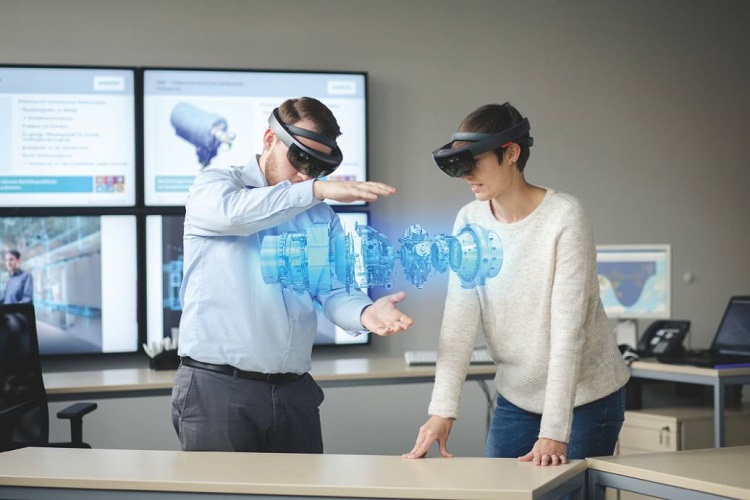
The 3D capabilities of this technology strengthen the linkage between the virtual design world and augmented reality on the shop floor. 2D drawings and work instructions are replaced with 3D augmented reality. From there, users can:
- Locate parts based on 3D models,
- Verify and confirm correct part installation,
- Automate checking of installation,
- Automate recording of task completion
But that’s not all when it comes to the factory of the future.
Factory of the future
The factories of the future will transform the way products are manufactured in the aerospace industry. With simulation and digital twins, manufacturers can evaluate different factory layouts, automation capabilities, automated guided vehicles (AGVs) and other environmental factors in a virtual world before they invest in their construction or revamp. With the environment a major concern these days, companies are eager to find new and more innovative ways to go green — think what these more efficient factories of the future will mean for sustainability and waste reduction.
Flexible automation will help companies reduce investments in tooling while also making greater use of cobots. If you’re not familiar with the term, it’s quite simply a robot that works side-by-side a “human” technician to help with the heavy lifting or non-ergonomic installations.
Where today meets tomorrow
The complex nature of building the aerospace products of the future, especially in the midst of technological advancements, globalization and pressure for more sustainability, is prevalent.
Companies can use digital twin, additive manufacturing and more to adapt quickly and forge new business opportunities.
To do this quickly and cost-effectively, I’ve found that companies using simulation that validates and verifies multi-domain and multi-physics attributes are in a better position to enter the market. This is not limited to designing the aircraft but spans across planning and optimizing the actual factory where their products are produced.
As a trusted leader in providing the A&D industry with proven digital solutions that solve our customers complex challenges, we’re bringing future technologies to our customers today. This can take many different permutations such as access to embedded tools and databases connecting current and future information technology, to operational technologies, to highly integrated engineering technology environments. That’s what we mean when we say, “Where today meets tomorrow.”
Watch the video below:
Digital threads turn siloed data into connected disciplines and processes. These threads form the neural network of a digital twin – a virtual entity that mirrors the physical world, turning data into insight to continuously design, build and optimize throughout the production lifecycle.
While circumstances beyond our control prevented our gathering, I was interested in gaining insight from my peers this year at SAE Aerotech. I ask that you comment below to share your thoughts on the future of aerospace and what you feel will drive innovation.
For more information, I urge you to check out this on-demand webinar, “Preparing for the Future of Aerospace and Defense.” Much of what I discussed in this blog will be covered in greater detail in this webinar.
Oh, and here’s a pretty cool video we just released that highlights some of the technologies involved as the industry transforms to a more digital enterprise. Also, below is an episode from our podcast series Talking Aerospace Today. In this episode, I discuss in great detail more about the future in aerospace. Enjoy!
Finally, if you need more information or have a specific need in mind, I suggest you visit our Aerospace and Defense website.
Comments