Hype and reality of additive manufacturing applications
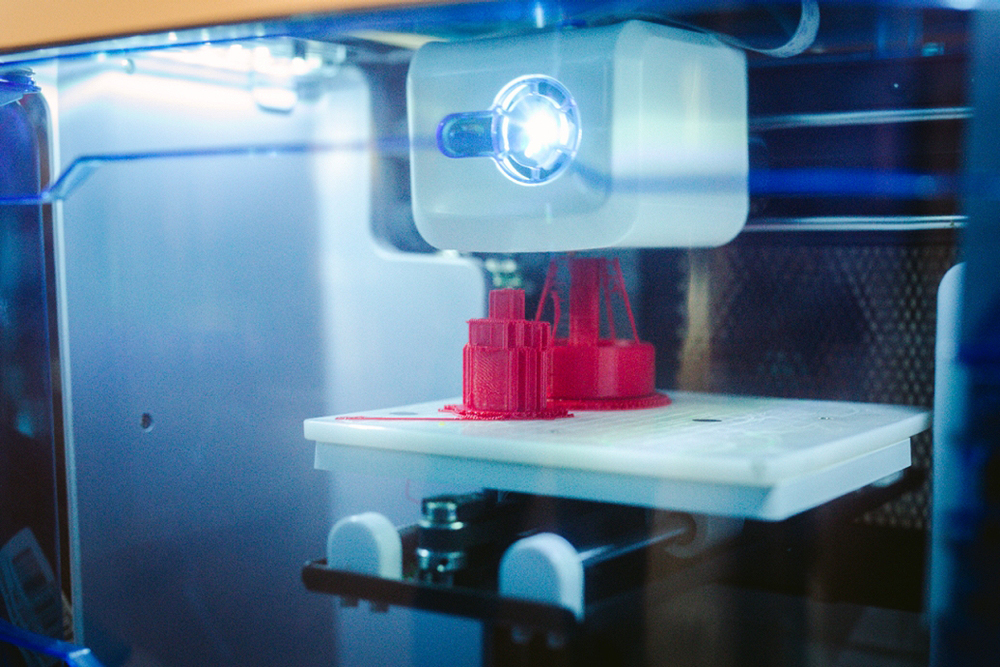
Is your company ready for industrial-scale additive manufacturing? As a member of the Siemens PLM Thought Leadership team, we are joined by Robert Meshel, Siemens Director of the Additive Manufacturing Network Initiative. It’s a new, online collaborative platform, designed to accelerate the use of additive manufacturing in the global manufacturing industry.
Our four-part blog series on additive manufacturing applications includes:
-
- the hype and reality of additive manufacturing,
-
- industrial-additive manufacturing risks and opportunities,
-
- jumpstarting industrialized-scale additive manufacturing, also known as ISAM, and
-
- where do you start?
We’ll define some use-cases and talk about how industrial-scale additive manufacturing may be right for your business.
You can follow us on Soundcloud, Stitcher and iTunes for this entire podcast series.
Dean Haehnel: What is ISAM and how does it differ from what manufacturers are using today?
Robert Meshel: If you look at the entire market for additive manufacturing, it’s focused on rapid prototyping — which is many times called 3D printing. Industrial additive manufacturing is how we go from prototyping into real parts that are going to be used in production and consumed by customers.
When we look at the projections for additive manufacturing applications, the market is estimated to be around $7 billion if you follow reputable analysts. The expectation for this market is to continue growing at a pace of about 25 percent, to triple itself within the next five years.
It’s apparent that the market for prototyping is exhaustive and there is a need to go into the production of real parts. This is where the significant promise of additive manufacturing resides. There needs to be a leapfrogging into this industry to move from where it is today into a completely repeatable and reliable set of processes.
The manufacturer needs to have a better understanding of how to process materials, set-up machines and monitor the entire production value chain process. This is the knowledge that does not fully exist in the market. However, there are some high-profile experimental projects by large companies that understand that additive manufacturing is a monumental promise for them.
Companies such as Siemens, GE Aviation or BMW are moving into industrial-scale production. It’s not to that level yet; however, companies like those mentioned understand that additive manufacturing has the potential to change the way they perform their business. That’s why they’re investing so much into this amazing technology.
Dean Haehnel: Many people talk about the potential benefits of additive manufacturing. What does it mean when you say ISAM will open an entirely new business model?
Robert Meshel: It’s multiple levels. Firstly, products are going to look different. Additive manufacturing allows many capabilities that are not possible with traditional manufacturing. For example, light-weighting, or the ability to build very complex structures, cannot be produced or customized with the existing manufacturing process. Additive manufacturing is building part by part, and therefore you can make modifications into each part without adding more cost into the overall production process. Products can be reimagined from traditional methods.
So, there needs to be more effort in how you design for additive manufacturing and the kinds of materials you are using. The execution process is quite different. So, you need to reinvent your process.
It’s not only how you design, but how you run processes that fit into this design via the production of new technology and expertise. There are unique issues like internal production to support additive manufacturing versus outsourcing. This is just one example of potential process change. Moreover, you need to engage with new vendors, new partners, upgraded equipment and reconfigured workflows.
However, once you harness these sets of capabilities and have the high-proficiency that customers expect for additive manufacturing, you can climb to achieve a new level of redefining your business? It’s the purest path and manifestation of the Industry 4.0 vision – a fully digital process, which is the promise of additive manufacturing – the holy grail of manufacturing.
Eventually, my entire business process is going to be quite different because the products and process are going to be changed. That’s why companies are seeking to harness this technology. One of the barriers that hinder manufacturing from being more aggressive at meeting the potential benefits of industrial additive manufacturing is merely inertia. Organizations stick with what they know, especially if it is working. It’s hard for them to move to the next level.
Dean Haehnel: The potential benefits must be huge because you’re eliminating vast amounts of capital, increasing efficiencies, producing designs you couldn’t manufacture before and so on. Can you address some of these potential benefits?
Robert Meshel: In the short term, additive manufacturing is still a relatively expensive process. It’s not going to be easy to demonstrate an immediate return on investment. There needs to be some investment in the capital because the materials are costly. It’s a new industry, and the processes are still being shaped; therefore, it’s pricey. However, the promise behind additive manufacturing is enormous by eliminating the need for new tooling and having to store vast amounts of in-house product – a significant benefit and shift in manufacturing.
A prime example is spare parts. If you look at companies that are delivering products that require maintenance, it necessitates a substantial stock of parts to support their products in areas like automotive, locomotive or airplanes. The costs to produce and store these parts in warehouses is significant, reaching 40 to 50 percent of the overall balances of the company. In addition to producing and storing is the cost of shipping. With extensive inventories, it can sometimes take years for the part to be used by the consumer.
However, moving to a fully digital process allows you to produce as needed. So, instead of a warehouse, the design is stored in a database and shipped digitally to be produced upon consumption, reducing your physical inventory to zero – an enormous benefit to manufacturers.
Dean Haehnel: What do you think it’s going to take for 3D printing to achieve these industry-scale levels of production?
Robert Meshel: I think multiple elements need to be improved. The range of materials needs to grow to support it. Also, the quality needs to improve, and this refers to building repeatable processes. A significant amount of printing is failing and needs to be replaced and redone. This is unacceptable with industrial-scale additive manufacturing. However, knowledge is accumulating. If you go to companies like the Service Bureau, they are beginning to collect this knowledge and information and with the know-how to improve it.
Also, this is valid for many machine companies which have tremendous ability and experience in running their machines efficiently. If you can build these ecosystems while combining all these elements, manufacturers can quickly collect the relevant information under a new domain, to harvest it with technology to meet their needs. The result will be a reduction in the cost structure, which is relevant to the problem with costly transporting and the use of materials, with more incentive for companies to produce larger volumes. Therefore, the entire cost of the materials is reduced, which is typical to any new industry.
Dean Haehnel: If I’m a listener today and I’m interested in beginning this ISAM journey, what do I need to do to prepare for industrial-scale printing?
Robert Meshel: There are two major factors: how to do a partnership and be open to collaborating with external entities, and how to leverage knowledge and expertise. This involves teaming up with partners, talking with people in the industry and learning from everyone, everywhere. Also, attending conferences, reading blogs and articles on additive manufacturing, watching webinars and listening to podcasts. You need to be a part of the additive manufacturing ecosystem and begin gaining knowledge. The information is out there. The problem is sometimes finding it.
Secondly, begin to experiment with additive manufacturing yourself. You need to investigate your business and the product that you produce to find areas where additive manufacturing might be advantageous. Bring together domain experts in design, simulation and manufacturing. You can always learn from others, but there is no better way than your own experience. Consider setting up an additive manufacturing set of competencies to gain first-hand knowledge and experience with your system.
What we see with many of our customers is that they have started their journey by leveraging the service bureaus, but they discover that the knowledge resides at the service bureau, which is not the best avenue for the process. Continuing to work with service bureaus is essential, but they need to begin experimenting internally as well. We see more companies build their internal service bureau for their own needs in conjunction with service bureaus.
Dean Haehnel: That’s excellent advice. When I’m out traveling and talking with visionaries in the additive manufacturing industry, many of them share Siemens feeling that industrial-scale additive manufacturing is the next significant evolution of technology. However, they all seem to have different timeframes of when this will happen. How long do you think it will take before industrial-scale additive manufacturing is commonplace?
Robert Meshel: This is a new technology and industry. If we look back and try to compare to other past emerging technologies, I think this has the real potential to become an exponential technology. The nature of exponential technology is that when it starts, it appears slower. There’s deception with this progress because linearly it seems slower. However, there comes a tipping point where technology begins to race. Then it exceeds everything around it. There are plenty of examples of this in digital photography and IT technology. 3D printing is one of these technologies that is going to grow exponentially. However, it takes time. It’s not going to be immediate.
Everybody that goes into this journey needs to understand that this is an investment in the future. It may take three, four or five years; but, it will happen. Eventually, additive manufacturing is going to be yet another manufacturing technology. Today it’s still a technology in development, but soon that’s going to be fully integrated into the manufacturing processes. No manufacturer is going to be able to avoid using additive manufacturing because of the value it provides.
Dean Haehnel: Thank you for your insights, Robert. We covered the meaning of industrial-scale manufacturing. The benefits of additive manufacturing and its relevance to ISAM, what it’s going to take to achieve industrial levels of manufacturing, how to begin the journey to ISAM and how long it may take for ISAM to become commonplace in manufacturing.
Listen to this entire series via podcast on Soundcloud, Stitcher and iTunes.
This concludes our first in a four-part series of blogs taken from a transcribed podcast. In our next blog, we discuss the risks and opportunities of industrial-scale additive manufacturing – where today meets tomorrow.
About the author:
Blake Snodgrass is a writer for the Thought Leadership team in Siemens Digital Industries Software, which supports several venues, including the Thought Leadership blog for the company. He speaks with experts in their field who provide compelling insight into innovative technologies affecting industries and how this can impact the future. Blake has a Bachelor of Arts degree in Mass Communications and more than 25 years of experience working for IT companies, with roles in technical writing, marketing communications, user-experience design and content development.
Robert Meshel, Director of Additive Manufacturing Network, Siemens Digital Industries Software Solutions
Robert Meshel is the Director of the Siemens additive manufacturing network, an online collaborative platform designed to accelerate the use of additive manufacturing in the global manufacturing industry. This initiative was born under his previous role, where he re-joined Siemens Digital Industries Software as the director of the strategy for the manufacturing Engineering Software unit. Driven by the passion for innovation in technology and business models, Robert was relentlessly pursuing new strategic opportunities developed within the organization or by partnering with external ambitious startups that are seeking to make a significant impact. Robert originally joined Tecnomatix in 1996, where he served in various technical management capacities, including head of portfolio management, director of product management and business consulting.