How heavy equipment manufacturers can conquer cost challenges
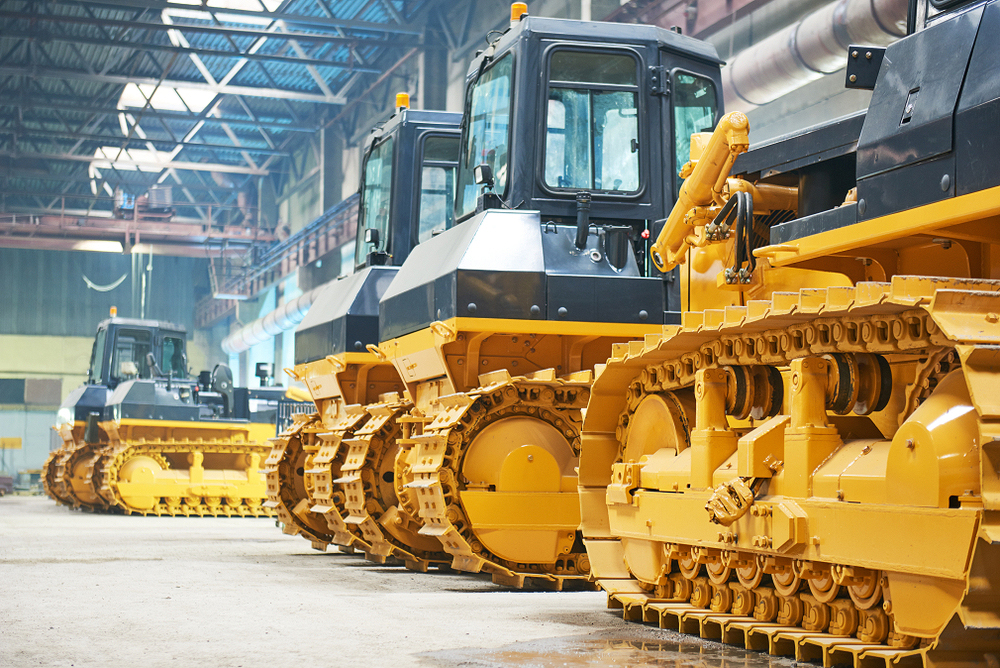
Heavy equipment manufacturers are feeling the squeeze.
Tariffs on steel and aluminum are impacting their ability to meet new customer demands. One manufacturing expert described the situation as causing “a lot of chaos, with companies trying to figure out what their strategies are,” according to an article about the recent Fabtech conference.
Tariffs place increasing pressure on heavy equipment manufacturers as they search for ways to accommodate customer demands for unique products that meet global agricultural and construction needs. Manufacturers need to find ways to remain competitive in more markets as expansion in developing countries is expected to drive a compound annual growth rate (CAGR) of 4 percent in the construction machinery industry by 2024, according to a Global Market Insights report. Agricultural equipment makers will experience similar growth, with a CAGR of 7 percent over the next four years, according to Market Research Engine.
The current economic environment could impact heavy equipment manufacturers’ ability to remain competitive. In fact, one supplier to the industry said tariffs have increased lead times on steel orders from 6 to 8 weeks up to 12 to 14 weeks.
Meanwhile, manufacturers must adjust designs to meet varying regulations in different countries, including complex global emissions standards, which increases manufacturing variability and R&D costs. Heavy equipment manufacturers must find ways to minimize costs and meet customer demands in this uncertain climate.
This is where collaborative manufacturing becomes critical. Collaborative tools can increase speed and accuracy during the design process and bring real-time field information into product refreshes and new product development.
Enhancing collaboration across the enterprise
By now, most manufacturers are aware of how digitalization can streamline the product design and testing process. But how can it improve manufacturing collaboration?
In the planning stages, digitalization helps manufacturers develop standardized processes from build of materials management to equipment costing. For instance, they can quickly reconcile differences between the engineering build of materials and the manufacturing build of materials to avoid future production challenges.
Also, a disconnect typically exists among design, engineering, manufacturing, tool makers and suppliers. They may lack visibility and traceability into quality issues. One of the key characteristics of collaborative manufacturing software is the ability to integrate sets of data from different applications that engineers use across the product lifecycle. It reduces the potential for quality problems or redundant work because the entire organization has “one version of the truth” that anyone working from anywhere can access and use at any time.
Design and validation is another area that can encounter challenges without collaborative tools. One of the ways digitalization helps manufacturers in the design and validation process is through the use of 2D and 3D factory modeling and layout.
In the past, it was common practice to “over-engineer” design capabilities in parts to accommodate demands. This approach leads to over-design and manufacturing of parts without concern for material costs of steel—which in turn creates waste and excessive costs in production. Simulation capabilities allow heavy equipment manufacturers to meet durability, adaptability, energy-efficiency and unique material needs without having to conduct multiple, time-consuming lab tests. Taking advantage of new materials manufactured through an additive design and manufacturing process will further help.
Collaborative manufacturing will continue to be an integral part of heavy equipment design and production as manufacturers try to reach new markets and meet evolving customer demands. It reduces the potential for design errors, delays and costly rework that can impact market performance and global competitiveness for heavy equipment manufacturers.
This concludes part one of our series on collaborative manufacturing. In part two, we discuss how precision farming can become a reality amid through collaborative engineering strategies and technologies.
About the author
Rahul Garg is the vice president for industrial machinery and heavy equipment industry at Siemens PLM Software, responsible for global business development. He and his team are responsible for identifying and delivering strategic initiatives and developing solutions for the industry, working closely with industry-leading customers and providing thought leadership on new, emerging issues facing the machinery industry. Rahul’s experience and insights are derived from a 25 year career of delivering software-based solutions for product engineering and manufacturing innovation for the global manufacturing industry. He has held leadership positions in multiple areas, including research and development, program management, sales and P&L management, having focused exclusively on the industrial machinery and heavy equipment industry since 2007.