OEMs, suppliers and how to use a program management system
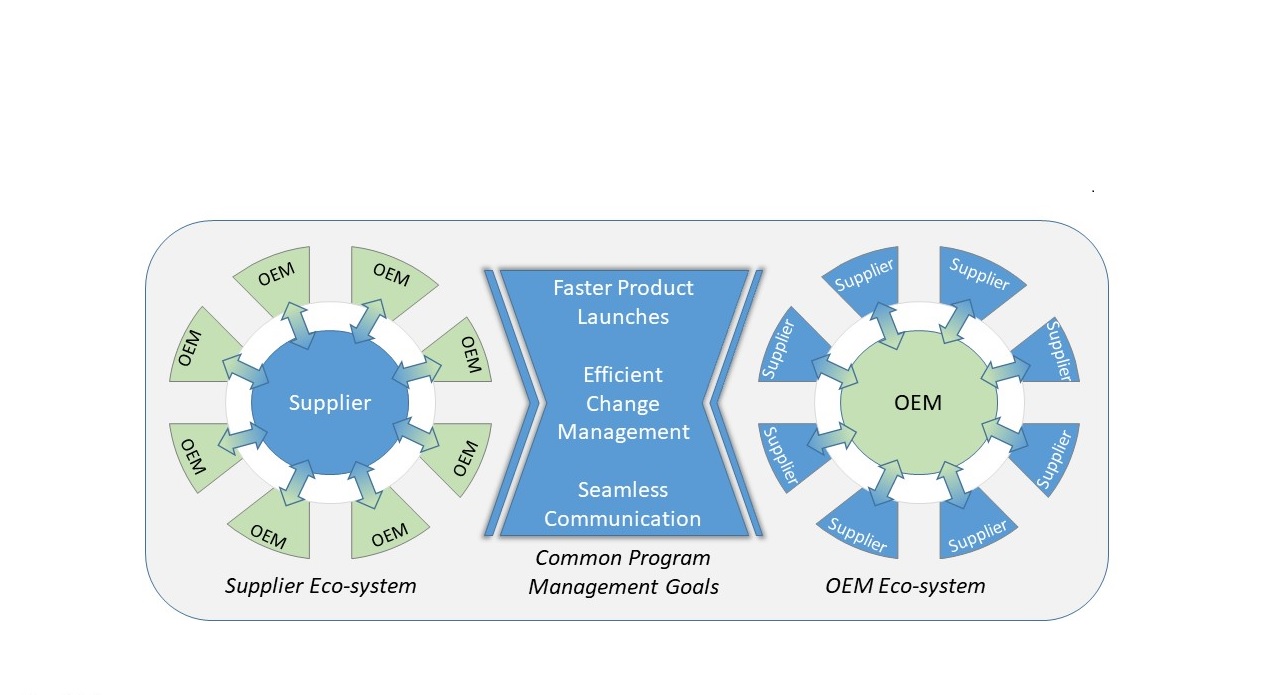
The challenges of program management between OEMs and Tier 1 suppliers vary, but they essentially are struggling to meet the same goal: use their program management system to reduce time for new product introduction.
OEMs usually have a specific way to manufacture a product, however, that product may change as development and design evolves; it’s imperative for the suppliers to be flexible. Unfortunately, many OEMs and suppliers’ program management tools and methods aren’t set-up to meet development milestones efficiently and struggle with time delays and cost overruns.
I would like to discuss the unique problem for OEMs and Tier 1 suppliers in how their program management system functions. People are often focused on completing tasks without really focusing on a specific deliverable or end-goal.
Given the complexity of systems and the fast-paced new product introduction (NPI) cycle, it’s imperative to combat these challenges now, communicate with greater efficiency and avoid the issues lack of communication has from development all the way through production.
What are the key challenges from OEMs’ perspective?
Automotive and aerospace products are complex systems of systems where mechanical, electrical and software components come together. OEMs know this, yet still struggle with understanding that if all internal and external activities are not aligned to meet the product development milestones, then delays can occur, resulting in loss of major market share.
To make matters worse, there might be excessive cost overruns to rush production; when things are sped up, mistakes are often made.
In the automotive and aerospace industries, hundreds of suppliers are involved in manufacturing a single market product. Aligning activities is a challenging and daunting task as small parts need to be assembled at specific points so parts are produced efficiently in a way that minimizes bottlenecks.
A real-world example is a seat heater in a car. The control of heater might be through the integrated panel, the manufacturer of the seat and the manufacturer of the dashboard panels – all three might be different, yet they are all interdependent. So, if the activities involved for the seat manufacturer aren’t aligned with that of the integrated panel manufacturer, testing the overall vehicle integration cannot proceed.
Multiply that scenario by the many such interdependent systems within any given vehicle or aircraft.
Currently, most program managers use spreadsheets and other task-oriented tools to manage these types of processes. They aren’t integrated with the product data or requirements data, and these tools are not holistic or integrated with other systems well enough to manage the deliverables which drive the tasks and schedules. To remain competitive, OEMs must strategically implement a better program management system.
But what about their suppliers?
What are the key challenges from the suppliers’ perspective?
Every OEM has its own product development cycle with its own specific nomenclature. One OEM, for instance, calls its milestone “Physical Build 1,” but another calls it “First Physical Prototype,” yet the supplier makes similar parts for both that must be specific to the vehicle build milestone. For the Tier 1s, aligning activities to a particular milestone for a particular OEM presents challenges; there are concurrent activities going on for multiple OEMs with different phases of each of their programs.
Program managers must also remember specific OEM nomenclature or maintain a glossary of what they mean. Every time a new request from the customer comes to them, they have to refer to the glossary to understand the level of detail the customer is requesting, and then provide parts accordingly. However, if they can maintain a template of deliverables as per the customer milestone, they can recall it with ease and have a list of tasks and schedule ready.
Suppliers are tasked with planning their internal activities and resources on minimal resources, sometimes drawings marked up early in the product development cycle rather than a fully released drawing. As deliverables are needed, whether they are in close proximity of milestones from the same or different OEMs, tracking activities and creating meaningful reporting is extremely challenging.
If, on the other hand, OEMs see a supplier struggling to meet their expectations, they might lose confidence and look for alternative sources, with the supplier ultimately losing business.
Meeting these challenges
As long as companies continue to use only task-oriented tools to maintain organization, it will be harder to bid and budget correctly, supply on time and keep up with customers. Organizations must find the right program management tools to efficiently manage deliverables tied to their parts and communicate changes, whether it’s milestones or customer needs.
At a minimum, manufacturers can implement a few program management steps. Using templated deliverables/schedules and an integration with the bill of materials and change management will drive faster setup and communication when time-sensitive milestones and events are created or updated. Integration with extended organizations means OEMs can plan and align all supplier and internal activities as per their milestones, and tier 1 suppliers can plan and align all activities for a specific event of an OEM.
Overall, program managers and project managers can have an excellent visibility of changes and thus control them.
The best way to combat the challenges is increasing your ability to better align with the extended organization regarding expectations and necessary documents – including formats and other attachments like inspection reports and layout information – and track their availability at the right time for successful product launches.
Final thoughts
OEMs must work with many suppliers as they manufacture a product, and often have a definite way of managing programs. Suppliers must be flexible to OEMs’ needs.
OEMs and Tier 1 suppliers are different, yet similar in the way they’re run: they want to bring products faster to the market. When organizations are set up with a deliverable-centric system, they can quickly manage change in a lean environment, tasks are value-adding and the owner has a clear definition of what the completion criteria for the tasks are. They’re not bogging down the process.
Using static, task-oriented programs and spreadsheets is obsolete and time-intensive. Deliverables must meet requirements and be delivered on time, within budget and of sufficient quality. Organizations that are using a comprehensive program management system and are more deliverable-centric, with better integration with their part information, will be more lean and agile with better success rates.
It’s up to both OEMs and suppliers to identify the wastes and delays in their launches, stay focused and move faster in NPI.