How to solve product development process challenges
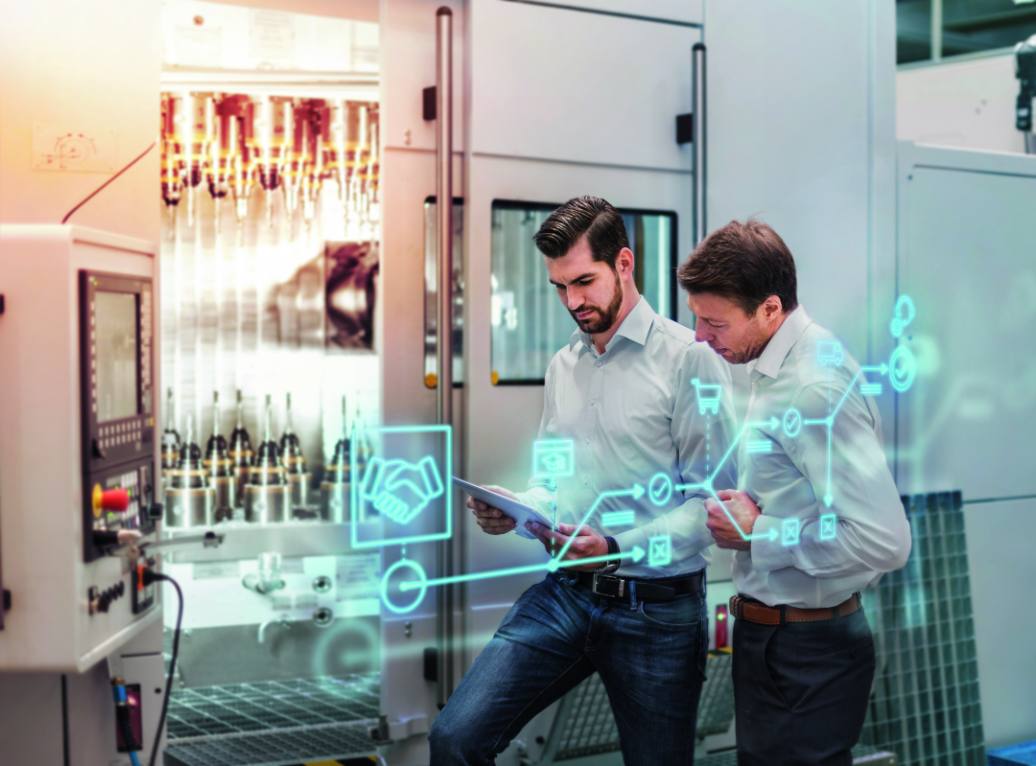
To remain competitive in a world where technological advancements makes yesterday’s electronics obsolete tomorrow, companies are struggling through the product development process as they attempt to cut down time-to-market and minimize product mistakes and failures while keeping costs low and reducing delays.
In the first part of this blog series, we identified five challenges that have significant, negative impact on the success of New Product Development and Introduction (NPDI). These product development problems result in an accepted 50 to 80 percent product failure rate.
In this post, we will examine three challenges in more detail and how companies can counter them.
1. Increasing complexity
The Problem. Today’s increasingly mechatronic products contain a far greater ratio of software, electronics and integrated circuits peripherals to mechanical components than ever, and this ratio is on the rise: embedded software is proliferating as mechanical components are decreasing. Electric toothbrushes can link to an app to your phone, indicating if you’re brushing too hard. Cars used to be totally mechanical; you pressed on a gas pedal, opening valves and allowing air and gas through for acceleration. Now, you step on the gas pedal and the software sends a signal to the engine.
Companies deal with this problem by lining NPDI processes up in serial – mechanical passes to electrical, which passes to software. Typically there are inefficiencies and loopbacks as the design is revised and versioned and as more teams get involved. And, of course, there’s the ever shortening time-to-market demand.
Companies that collaborate well often use conceptual sketches to pass knowledge and promote parallel working, but even this fairly advanced method can be time-consuming and fraught with errors: colleagues don’t understand the concepts, or they aren’t working on the latest version. Imagine working on a project only to discover that you were working on the wrong iteration. Wasted time, departmental silos and confusion drag companies into higher rates of product failure at higher costs.
The solution. World-class NPDI organisations use the latest mechatronics concept design innovations to allow for fully functioning concept models that can be shared with downstream processes. This approach ensures feature, form and function are loosely defined and can be simulated before the final design is agreed upon.
But why stop at design? Engineering and manufacturing can adopt virtual commissioning to take hardware out of the loop and begin testing manufacturing code, even deriving the code directly from the digital twin, long before the design is finalised. This means that when the product is ready to be manufactured, companies know the manufacturing process will be right the first time with no glitches or hiccups, which shortens time to market.
2. Knowledge transfer and translation
The Problem. A key study in the journal of Information and Organisation by Valéry Merminod and Frantz Rowe shows the impact of appropriate knowledge transfer and translation within the NPDI operations of a consumer electronics company.
The researchers conducted a longitudinal action study over four years, where tools for knowledge-sharing were implemented to improve NPDI performance. In the methods section, they draw upon the use of “glitches,” such as stops or errors in the product development process, to measure the effectiveness of communication-of-knowledge between the multiple departments involved in NPDI. A “knowledge transfer glitch” was counted in the overall results if it caused a significant impact on time-to-market.
These were the baseline results at the experiment’s offset:
• 40 percent of information was found in the right place when it was needed
• 30 percent of the team had access to the product’s digital visualisation
• 60 percent of key deliverables in project milestones were met on time
• 20 percent of deliverables were validated by management
Prior to implementing knowledge transfer tools, in this case PLM, the authors noted these issues:
1. Project Knowledge distributed across several information silos;
2. Drawings accessible only through CAD tools (accessible only by engineers)
3. Exchanges of information were performed through email
4. Semantic errors
5. Lack of documentation
The Solution. Following the successful implementation of the PLM system, in this case, Siemens Teamcenter, the results were substantial:
• 90 percent of information was found in the right place at the right time (previously 40 percent)
• 90 percent of the team had access to digital visualisation of the product (previously 30 percent)
• 95 percent of key deliverables in project milestones met on time (previously 60percent)
• 90 percent of deliverables validated by management (previously 20 percent)
• Technical specifications updated in real-time and contained within associative documentation
Implementing this communication strategy represented a faster product development process and significantly less risk. In the end, the number of errors decreased from an average of 26 glitches per project to fewer than 10.
3. Emotional Decisions
The Problem. Well-established research shows that the more invested a team is in a new product (money or time), the more irrationality creeps into the product development process. Stakeholders make emotional decisions based on fear of regret, rather than logical, fact-based rationale. This effect is similar to the “opportunity loss effect” that gamblers experience when they are on a losing streak – they are risk averse when winning and risk taking when losing. (Kahneman & Tverksy, “Choices, values, and frames”; Stanovich, Decision Making and Rationality in the Modern World.)
This phenomena is often being discovered at the gatekeeper area, where a number of factors – such as inaccurate cost estimations from previous gates, incorrect information presented to the gatekeeper or lack of a rigid process – are ignored. Confirmation bias creeps in, allowing gatekeepers to use only the evidence which supports their “gut feel.”
The problem, and the answer, is well documented. Even as far back as 2008, Robert Cooper in the Journal of Product Innovation Management states, “Rigidity in the NPDI stagegate process is essential to increase a company’s control over NPDI” to reduce varied results and increase rationality of these decisions.
However, this is easier said than done. Many gatekeepers are presented with static, incomplete or outdated information with no ability to drill down, and no time to go find that data.
Worryingly, up to 76 percent of decision makers’ time is spent on non-value add actions such as searching for and translating data. “Best guesses” and “gut feel” decisions result when this data is too difficult to find, impossible to translate or simply does not exist.
The Solution. World-class manufacturers ensure the data that decision makers need to do their jobs is available to them when they need it, and that it’s easily accessible. They also ensure they see only the data relevant for the task at hand, and that it’s live data, as opposed to static, outdated Excel files that are outdated as soon as they’re generated.
A cost-effective New Product Development and Introduction with minimal product glitches and failures is possible, but companies seeking to get their products to market with the same old routines while expecting better results is wishful thinking. There are tools and processes that can help navigate through complexity, emotions and strained knowledge placing organisations on the right track to more successful product launches.
This concludes part two of our series on increasing your success with new product development. Stay tuned for the final blog in our series highlighting the final two product development problems and challenges impacting NPDI and the solutions available to increase efficiency and time-to-market and reduce glitches.
About the author
Everything I do is for the sake of my children’s children. I want them to enjoy the things that we take for granted, but I feel we need to make significant changes to the way we consume and manufacture products. This motivation drives both my personal and professional worlds. I believe Industry 4.0 and digitalisation allows for a significant step change in wastage in manufacturing. I think Dr. Seuss said it best, “Unless someone like you cares a whole awful lot, nothing is going to get better. It’s not.”