How Siemens PLM is prepared to help customers’ digital transformation
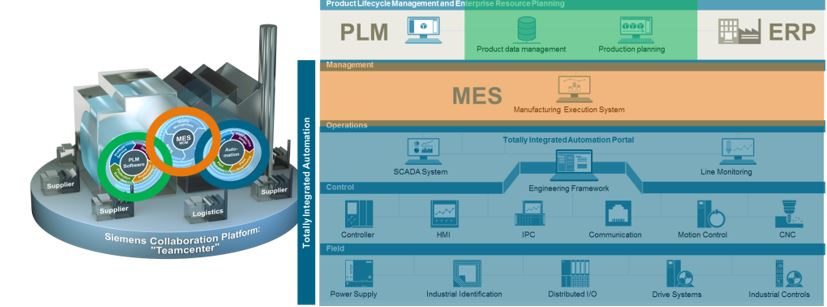
As companies face new challenges with constant market changes and increased complexity in their products and processes, they’re finding it more difficult to beat their competition in going to market and, quite frankly, survive. Most companies understand that a digital transformation of some type is necessary to meet these challenges, but they don’t know how to complete that transformation.
The answer is in improving their business process integration. Companies need to understand that three of their major IT systems can no longer be viewed as separate entities. Product lifecycle management (PLM, enterprise resource planning (ERP) and manufacturing execution systems (MES) will not deliver as much value to companies if they continue to be improved independently of one another. Instead, all three systems need to be incorporated into a closed-loop process.
In his series on why companies should have a closed-loop ERP, PLM and MES process, Matthias Schmich examines how this new digital enterprise helps companies conquer these challenges. In part one, he explores how these ERP, PLM and MES systems are typically developed on separate paths. In part two, he discusses why companies must now treat the three systems as part of a whole rather than as individual components. Here, he delves into what the future looks like for companies if they take this approach and how Siemens PLM is poised to help its customers successfully incorporate this approach.
The future IT landscape will have three major pillars: PLM, MES and ERP. They are quite distinct today, but they will have to be integrated to create closed-loop processes.
It’s common to use ERP and MES to synchronize manufacturing to make manufacturing planning and execution a better process. PLM and MES integration focuses on accelerating production ramp-up times and to establish a feedback loop between product design and production. PLM and ERP integrations are common today, but in most cases, it’s only as a transfer in one direction of master data and bill of materials from PLM to ERP.
Links between all three domains are rare in practice, but it will become far less rare in the future. Without this business process integration, business processes will still have gaps and manual interaction. By integrating MES, PLM and ERP, manufacturers create a closed loop that enables them to learn.
By implementing business process integration, manufacturers will create a closed loop that helps them learn.
How this business process integration could help configuration management
Today, product baselines – including as-designed, as-built and as-maintained baselines – are kept in different systems. But to ensure traceability in the future, this information will be linked together. A typical scenario for a PLM, MES and ERP integration with a closed loop could look like this:
• PLM owns the as-designed product configuration, the bill of materials and the routings.
• The PLM-ERP integration ensures that ERP has the product information, but does not change that information.
• The ERP sends information to MES about the materials to be assembled and production orders. MES sends ERP information on execution time, quantities and non-conformance.
• Real-time information from the shop floor is managed within MES.
• PLM sends routings, routing sequences and electronic work instructions to MES.
• Then, MES sends back the as-build data to PLM.
In this example, the integration focuses on a business scenario for configuration management. Companies need all three systems along the value chain, but the ownership of the as-built information remains in PLM. ERP and MES interact and ensure the data is correct when it’s ready to be transferred. The systems partner with each other based on defined rules about their roles and responsibilities.
What Siemens PLM is doing to help customers complete a digital transformation
This kind of business process integration could offer increased value in time-to-market and leaner processes without gaps. Until now, integrating PLM, MES and ERP has been seen as complex regarding the process and required technical interfaces.
Now, Digital Enterprise Platforms with PLM and MES share parts of their data and process models, which makes it much easier to integrate.
The PLM-MES and ERP-MES integration quite often exist on a data exchange level. To create a closed-loop-system, all three must be brought together. More standards are available to interconnect these tools. Companies like Siemens have common data models for PLM and MES to share data without interfaces. A Digital Enterprise Platform has open interfaces to communicate with applications like ERP in both directions.
Beside all technical questions, the process definition with clear roles is key for a successful integration of the systems. The integrated middleware often has industry best practice processes out-of-the-box, which allows an easy and fast implementation.
For this successful integration to occur, companies will need a Digital Enterprise Platform that includes major enterprise software tools, such as PLM and MES, to master technical product data information and its processes along the product lifecycle, including manufacturing with closed loops. ERP will still play an important role and be more tightly integrated with PLM and MES than it is today. However, ERP will focus more on released data and will manage logistics and financials processes. Compared to today, it will have reduced functionality for engineering and manufacturing operations.
Siemens PLM is in a position to offer its customers a holistic solution that covers all major digital transformation requirements. Over the past 15 years, the company has developed an extensive suite of software products to create the Digital Enterprise Software Suite. The suite consists of PLM, MES and automation systems. The backbone of the Digital Enterprise Software Suite is Teamcenter, which is a collaborative product data management platform for business process integration.
For a successful business process integration, you need a Digital Enterprise Platform — and Siemens PLM is in a unique position to help.
The Digital Enterprise is the future platform that can manage digital product data and digital production data to bring them together. In case of Siemens, PLM and MES are already part of the platform. This allows easy integration because interfaces are not necessary, allowing industry best practice business processes to come together in the solution. Because ERP will have reduced functionality, the integration with PLM and MES is necessary. But it will be different than what we see today, and it will also be based on industry-specific processes.
Companies are rightly worried about what their futures will look like. They should expect to see changes happen more quickly in the marketplace, and they should expect that their competition will continue to be fierce. But if companies undergo a digital transformation to create a closed-loop PLM, ERP and MES process with the help of Siemens PLM, they can plan on having a productive and profitable future.
This concludes our introduction to having a closed loop ERP, PLM and MES process for a successful business.
About the author
Matthias Schmich has more than 30 years of experience in multiple management positions and has expertise in founding a company, managing IT and consulting. Matthias studied computer science in Karlsruhe from 1980 to 1984. He started his career at Robert Bosch and soon co-founded the Eigner Company, where he was one of its presidents. In 1993, Matthias moved to Müller Weingarten, where he was the IT manager for five years and was responsible for the company’s IT processes. He then joined Andersen Consulting and founded the company C´vis Consulting soon after, where he was responsible as the external program manager for global PLM initiatives. From 2004 until 2008, he was the head of business consulting at AGILE/ORACLE. Since 2008, Matthias has worked for Siemens Industry Software, first as the EMEA project management office manager and then as the vice president for services in Germany until 2014. He is currently the vice president for strategic business in the German Zone and focuses on Industry 4.0 and the digitalization of the value chain.