Product lifecycle’s role in designing the cars of the future
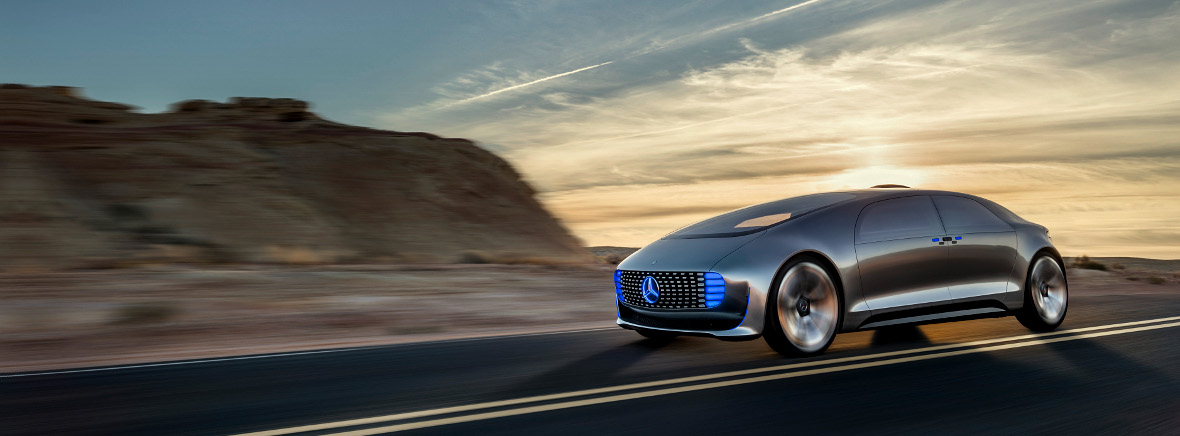
The cars of the future will pose design challenges that companies must be prepared to address. Instead of the car’s main selling point being the ultimate driving machine, we’ll watch the focus shift to cars becoming comfortable, convenient moveable homes.
In his series on cars of the future, Ed Bernardon has looked at what’s in store for today’s cars and what challenges we must prepare to face. In part one, he explored how today’s cars could face the same fate as the horse and mainly become a source of entertainment or put be put to work on the farm. In part two, he discussed the new challenges we’ll face as cars of the future arrive and ethical questions we must begin answering.
Here, he examines the changes that future cars will bring that will inevitably impact the business strategies of the automotive industry.
As cars of today evolve into “pod cars” and become our temporary homes on wheels, companies that offer product lifecycle software need to evolve to help their engineers face the design challenges these changes present.
Product lifecycle software will need to evolve as companies begin designing cars of the future.As we consider the changes the cars of the future will bring, let’s dig deeper into three areas.
Software and electronics. There’s a dramatic shift in vehicle complexity toward more software and electronics. Consider electric cars, where software and electronics could control acceleration, braking and stability by precisely manipulating the rotation of four wheel motors. The four moving parts of the wheel motors and their control systems could replace the far more complex internal combustion engine drivetrain in today’s car, which has thousands of parts.
Today’s complex geometric, mechanically intensive automotive designs will be replaced by equally or more complex designs but with a complexity residing more in software and electronics rather than mechanical parts.
Cars have more lines of code than Facebook and the Large Hadron Collider.According to the New York Times, a typical high-end car today has 100 million lines of code. This is quite a bit if you consider that Facebook has 60 million and the Large Hadron Collider has 50 million lines of code, which is also about seven times more than the world’s most advanced commercial airliner, the Boeing 787.
As complexity increases in cars of the future, engineering software will have to change to meet it.
The total amount of software will continue to increase when to car-to-car communication is added that will provide features such as:
•Real-time traffic information that forms the basis of efficient traffic-aware navigation;
•Driver safety solutions that increase occupant safety by actively detecting and taking action when hazardous conditions emerge; and,
•Parking innovations to enable drivers to search for and lock in parking spots both on and off the street.
These cars of the future are destined to be just one more thing on the Internet of Things, where vehicle software will also provide information to robotic machinery on how to assemble itself.
Engineering software, must change to help engineers design and manage this new complexity as software and electronics, not geometry, comes to dominate complexity.
Composite materials. The future car must be environmentally-friendly. As a result, lightweight design will play a key role in the quest for fuel efficiency and sustainability. The second thing to think about is today’s steel welded car bodies that will be replaced by a mix of materials and assembly methods.
Future cars must be environmentally friendly, so we should expect to see more composite materials.
Body structures will become lighter and more efficient as the push for energy efficiency accelerates. New materials like plastics, metals, magnesium and aluminum will be used with high-performance steel that may be selectively reinforced with carbon fiber.
Consider the i3, BMW’s initial effort to use carbon fiber composites everywhere in a passenger cell. The i3 approach was similar to aerospace design; full sheets of composite fabric, layered to create a stiff crashworthy lightweight part.
But carbon fiber is one of the most expensive raw materials ever used in a car, so this is a costly design approach. BMW took lessons learned from the i3 and used them to develop a more cost effective use of carbon fiber in the 7 series.
BMW is one of the car companies currently experimenting with composite materials.
On the 7 series, for instance, carbon fiber is used sparingly to reinforce high strength steel to create a light weight B-pillar. Elsewhere in the body, composites and steel combine with aluminum and magnesium — a far more cost-effective weight reduction strategy.
One potential cost-effective solution for cars of the future? Composites, steel, aluminum and magnesium
Car assembly methods will also change to accommodate these new material combinations. Cars won’t only be welded, they may be bolted, screwed, glued or even printed or “foamed” into place. Assembly may even be eliminated altogether with additive manufacturing methods such as 3D printing.
New experience must be built up for this automotive material revolution. Engineering software must help engineers accelerate how new design experience is created to replace experience gained over the past 80 years from engineering welded steel body cars. A challenge we face with the multi-material car engineering is freeing the engineer from gaining this experience by building and breaking prototypes. Instead, engineers will gain experience in part by simulating these new pod cars and their manufacture.
At a minimum, engineering software solutions for future cars must do more than reduce the dependency on prototyping. It must also distribute and make new knowledge a few engineers gain, quickly accessible to larger engineering organizations; so engineers don’t repeat past mistakes.
Interior design. A third area to consider is the shift away from emphasizing exterior styling and mega V8 power and toward interior design, comfort and convenience. The tools interior decorators and stylists use must meld with those of the mechanical, electrical and software engineers. New disciplines in the shadows today, such as comfort or user experience engineering, will play a greater role.
Interior design will play a much larger role in cars of the future.
Trades between these disciplines must be considered, along with more familiar areas like performance, manufacturability and cost.
Interiors options will explode as users will want more and more options just like we ask for in our homes today, such as new seating configurations, tables, beds and even lighting – a chandelier, anyone?
In the future, car companies will take on more of the qualities of software companies, and software companies will become more like automotive companies.
Car companies will take on more qualities of software companies.Engineering software must evolve if companies like Ford, Daimler and even Apple or Google are to efficiently design vehicles that will be the mobile living rooms where we work, play or sleep while being whisked away to our destination.
Engineering software companies must change so they can efficiently design these mobile living rooms of the future.
We know what these future challenges are, so we all must begin thinking how to prepare for and address what’s coming.
We need to start thinking now about how these changes will affect our future. Unless, of course, you’re like that frog in a pot of water about to boil and are fine with waiting until a little bit later.
This concludes our introduction on the cars of the future. Stay tuned for additional content!
Tell us: What features are you most excited to see in future cars?
About the author
Edward Bernardon is vice president of strategic automotive initiatives for the Specialized Engineering Software business segment of Siemens PLM Software, a business unit of the Siemens Industry Automation Division. Bernardon joined the company when Siemens acquired Vistagy, Inc. in December, 2011. During his 17 year tenure with Vistagy, Bernardon assumed the roles of vice president of sales, and later business development for all specialized engineering software products. Prior to Vistagy, Bernardon directed the Automation and Design Technology Group at the Charles Stark Draper Laboratory, formerly the Massachusetts Institute of Technology (MIT) Instrumentation Laboratory, which developed new manufacturing processes, automated equipment and complementary design software tools. Bernardon received an engineering degree in mechanical engineering from Purdue University, and later received an M.S. from the Massachusetts Institute of Technology and an MBA from Butler University. He also holds numerous patents in the area of automated manufacturing systems, robotics and laser technologies.