What’s new in Tecnomatix? (January 2022)
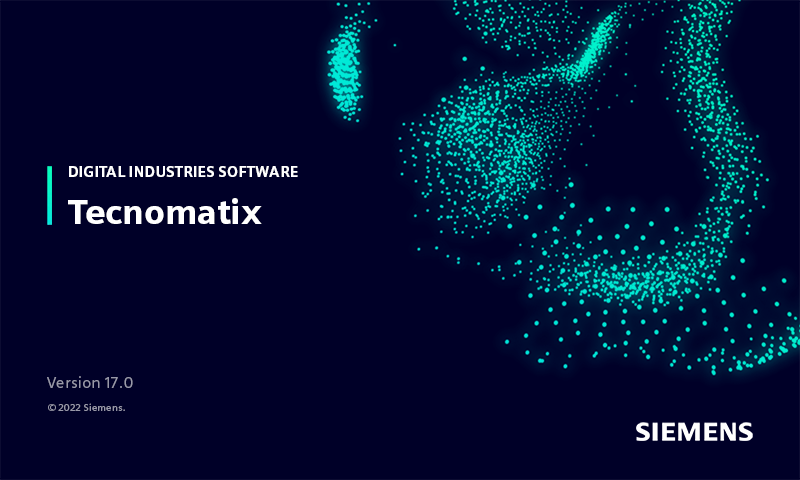
Next-level digital manufacturing with Tecnomatix.
Companies of all sizes in all industries use digital manufacturing software in the Tecnomatix® portfolio to meet their strategic objectives in today’s challenging business environment. Tecnomatix software helps turn innovative ideas into transformative products with more manufacturing flexibility and greater production efficiency.
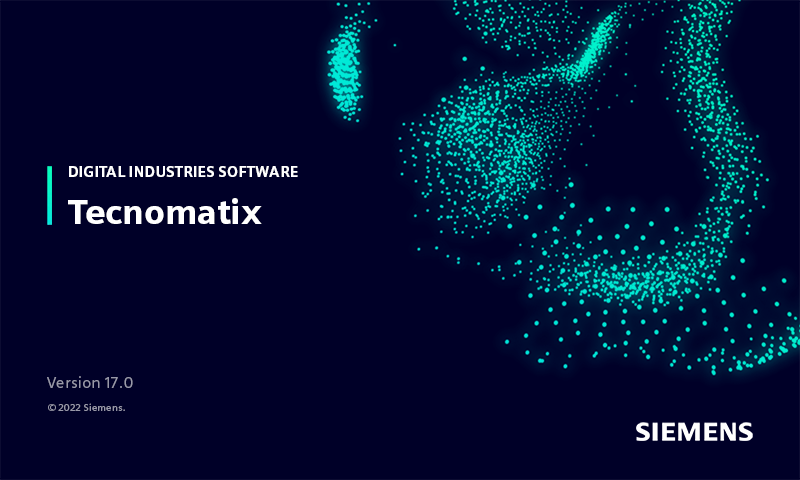
Tecnomatix 17.0 delivers exciting new advancements. From robotics and virtual commissioning to human simulation and virtual assembly, Tecnomatix software helps companies reduce risk and develop better manufacturing operations well in advance of production.
We are excited to deliver this new release to you!
Don’t have Tecnomatix software? > Try it for free.
See the highlights from Tecnomatix 17.0:
> Teamcenter Share
> Robotics
> Commissioning
> Human
> Virtual reality
> Assembly
Tecnomatix with Teamcenter Share
To help customers of all sizes take the next leap forward in their productivity and gain additional competitive advantage, Siemens has introduced Siemens Xcelerator as a Service. This can significantly lower the barrier of entry for small companies and reduces IT costs for companies of all sizes by taking Siemens Xcelerator to the cloud. This expands our portfolio’s capabilities by making it more accessible, scalable, and flexible, and by making our portfolio and industry digital threads easier to access and implement.
For Tecnomatix Process Simulate, there are four key benefits of using Teamcenter Share:
- Collaborate on manufacturing process and equipment design, line layout and workstation design, manual operations and analysis, robotic process simulation and validation, and commissioning projects.
- Contextualize information such as markup of workstations, equipment designs, production system layouts within manufacturing process simulation studies, unlike generic tools.
- Consistency in work across teams by ensuring that all teams are working with the correct version of data or models, process templates, robot and automation programs, equipment designs and layouts, and manual process operations.
- Allow decision makers to view and understand Process Simulate study contents and results more easily, anytime and on any device.
Teamcenter Share is packaged with all Process Simulate products and provides cloud file storage for Process Simulate data types (.psz, .pszx, .psz-tc, .zip). Process Simulate with Teamcenter Share enables secure sharing of studies with colleagues outside of your company network and provides role-based access control.
Watch this video to see how Process Simulate and Teamcenter Share work together:
Return to top. ^
Robotics
Process Simulate Robotics helps you to program and validate your robotic processes in a dynamic 3D environment. It includes robotics applications for spot welding, metal processing, drilling and riveting, surface treatment, and assembly.
The following new capabilities are available in 17.0.
Robot safety
Speed reduction in 16.1.2 was only supported with RRS simulation. Now it is supports MOP. This allows you to emulate speed reduction based on a certain percentage of nominal speed, program pause, and emergency stop. These impact robot behavior as well as the time report.
The following video shows a human walking by the robot, and proximity sensors representing pressure carpets (for example) trigger their location. The yellow zone slows the robot to 50% of the nominal speed, orange to 20%, and red triggers a controlled stop. Once the human leaves the red zone the robot resumes motion. A second simulation shows the same case, but without the slowing / stopping logic. You can see the impact on the cycle time.
Swept Volumes now use visible safety features. Only the ones attached to the robot moving with its joints are swept. You can hide the rest of the robot and get a static sweep of the safety features to look for any breaches.
To improve the usability, when the Safety Robot Manager dialog is open, you now can activate other Process Simulate commands, e.g., show / hide objects, jog the robot, etc.
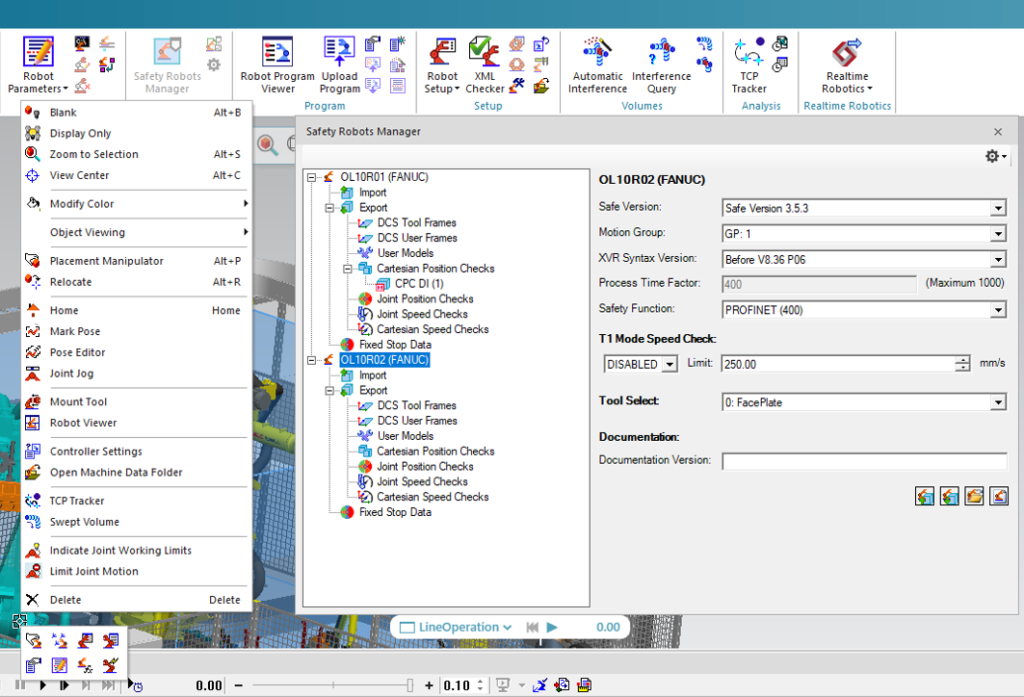
A new API call allows you to export the safety data through the API. This supports workflows where the safety settings are downloaded together with the program to assure full alignment of the production environment to the engineering digital twin.
In the downloads area on Siemens Support Center, you can find a safety kit updating any version after 15.1 to the latest one (like a multi-version hot fix).
ArtiMinds integration
Combined upload:
Tecnomatix Process Simulate and ArtiMinds Robot Programming Suite (RPS) generate each part of the program that eventually need to merge into a single continuous program. In 16.1.1, we managed to align the download. Now in 17.0 upload is also possible, and it populates Process Simulate and RPS accordingly.
Aligned components:
Robot models, grippers, and force and torque sensors must have kinematic dimensions that are identical for both RPS and Process Simulate. In Tecnomatix 17.0, a limited set of Universal Robots models and other devices are available in the installation. Those are aligned to the RPS model. Components can be aligned using a dedicated tool. When selected, aligned components are identified and later reduce the number of steps in the RPS setup wizard. Components that are not aligned can be used until alignment is done.
This video shows the improved interaction when creating a new operation. Selecting the robot identifies the robot and the components attached to it (gripper, camera, force sensor, torque sensor). If the Process Simulate component is aligned with the RPS component, a green check mark icon is added to the item. If it is not aligned, a red mark is added. If red (like the gripper in this case), you can click the icon to get the RPS component that is defined for the item. Successfully aligning all components makes RPS robot configuration much simpler, with only the meaningful stages available.
Dynamic Simulation:
RPS templates contain a variety of branches triggered by feedback from the sensing devices, e.g., force sensors, torque sensors, and cameras. Conventional simulations only show a specific path along the flow. Now you can also override the values in the decision nodes to simulate system behavior under various conditions. This flow is possible for cases when spiral search fails to locate the placement hole. This override is only used for simulation purposes and does not affect the downloaded program or robot behavior. These settings are used for the entire template. Simple search can find all override search options and they can be removed with a special command.
Other Improvements:
Locations in Process Simulate and RPS are better synchronized. A change in one system is reflected in the other. Now RPS simulation errors are logged in the Simulation Monitor instead of popping up error dialogs that interfere with the workflow.
Automatic path planner
Using the automatic path planner (APP) API, you can find external axes values and location orientation allowing for reach to all locations of an operation without any collisions and within joint limits.
The APP API selects the external axes combination that minimizes the variation of the external axes. For instance, when working on a robotic cell with a turn table and a rail, you can decide that the APP API should find a solution that minimizes the number of different turn table axis values to reach all locations.
Cables
In version 17.0, there is a new cable attachment available. This cable attachment can rotate, and the cable can slide through it. It is compatible with all existing attachments. Multiple sliding attachments can be chained alongside of retract system attachments.
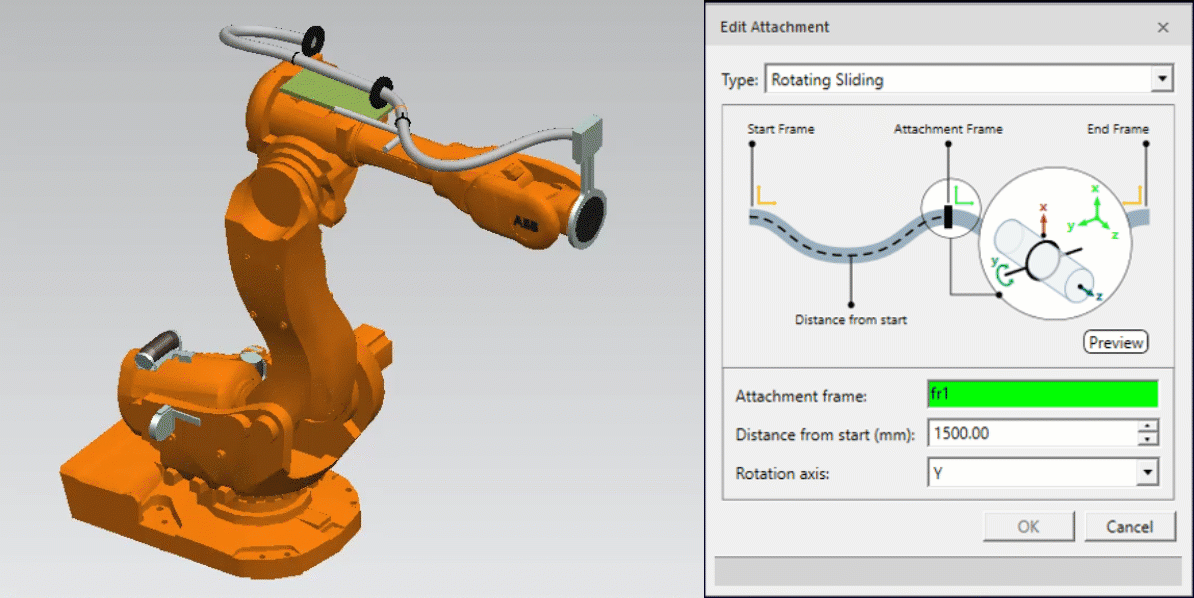
Paint thickness calculation
It is now possible to customize the paint thickness algorithm to improve its accuracy. You can edit a text file, containing the paint functions per brush, to extend the OOTB functionality or you can choose to replace it completely. With new capability to support a different calculation per brush, we can now also better support spray brushes, for which the algorithm also needs to consider the angle of the gun nozzle. In the function definition, you can choose either user-defined constants and parameters containing paint specific parameters, or hard coded keywords that are now available and documented in the paint files and the Tecnomatix documentation.
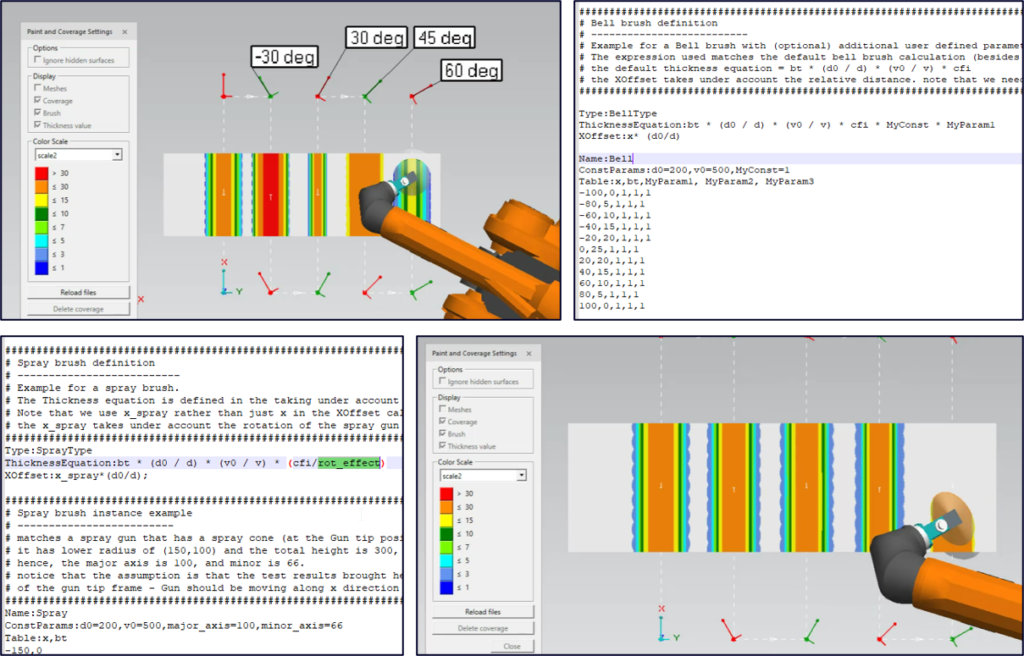
Waypoint planning
Aerospace and defense industry users who use Process Simulate on Teamcenter can now benefit from the waypoint capability for improved planning and programming. The Waypoint Viewer helps you to configure collision-free paths quickly and easily for robots by managing waypoints, which are used to define approach and escape paths between operations commonly used in drilling and riveting applications. These waypoints and the resulting operation structure that includes them is supported in both simulation and offline program download.

Waypoint planning to quickly and easily configure collision-free paths for robotic drilling and riveting processes.
Return to top. ^
Virtual commissioning
Process Simulate Commissioning helps you to run the PLC code that controls the station to validate robot motion, robot logic, and other mechatronic components such as clamps, conveyors, and the entire process sequence. Virtual commissioning works with real PLCs (hardware in the loop, HiL) or virtual PLCs (software in the loop, SiL), or with the Process Simulate Cyclic Event Evaluator/Emulation (CEE) internal evaluation tool.
The following new capabilities are available in 17.0.
LIDAR sensor fields
Up until this version, LiDAR sensors could only be used for visualization. In Process Simulate 17.0, LiDAR sensors have expanded in two ways. First, LiDAR “Fields” and “Monitoring Cases” can be imported via an XML interface. These XMLs can come directly from the sensor vendor’s software, like the SICK Safety Designer.
Secondly, in Line Simulation mode the LiDAR sensor is now based on an SCL script and returns an output if any active field is disturbed, allowing you to detect real objects and test dynamic scenarios that include safety laser scanners. The LiDAR can also dynamically switch Monitoring Cases, enabling real simulation and testing of various sensor-related scenarios.
Watch this video to see how it works:
Dynamic collision report
The Dynamic Collision Report now offers the possibility to create collision reports also in Line Simulation Mode. In Line Simulation mode the report can be activated prior to starting the simulation and records collisions as they occur. This information can be exported or printed for later use in reviews or for reporting hazardous situations in production. The Dynamic Collision Report in Line Simulation can come in handy especially for AGV motion validation by reporting collisions as well as clearances between the vehicle and its surroundings.
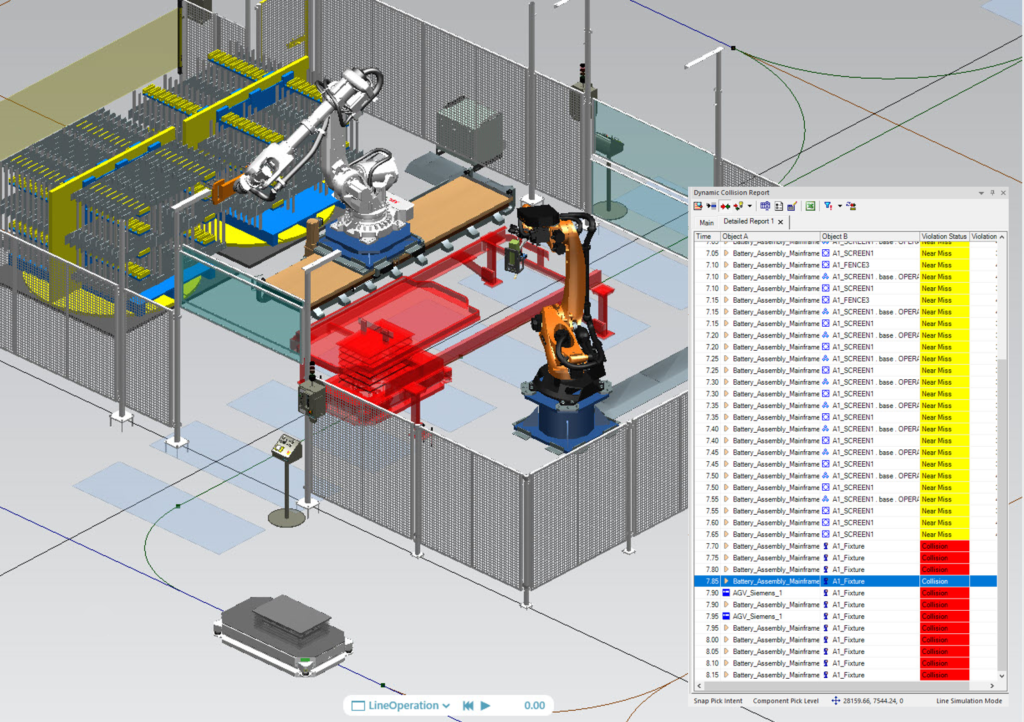
Exciting new capabilities
SIMOVE carrier control (protoype)
This prototype feature enables simulation of AGV Motion controlled by Siemens SIMOVE Carrier Control. To achieve this, two new sensors have been implemented in Process Simulate:
- Magnetic Tape Sensor: this sensor measures the distance between the current route the AGV is on and a reference frame of the AGV itself and reports the deviation. This result can then be put into a control loop (carrier control PID) to calculate the AGV’s continued motion, accurately reflecting reality, and enable following a track realistically.
- Secondly an “identification point reader” or simple “RFID reader” has been implemented, allowing the AGV to detect SIMOVE ident points when the AGV reaches them.
Watch these videos to see how it works:
Rockwell ControlLogix external connection (prototype)
This prototype feature allows for connecting Process Simulate directly to a Rockwell ControlLogix family PLC (CompactLogix / GuardLogix). The connection is direct and does not rely on OPC technology, greatly simplifying the virtual commissioning environment and improving performance by having fewer communication partners. The connection is a side application to Process Simulate and can be used with version 16.1.2 or higher.
Physical conveyors (prototype)
This prototype feature helps you to more easily model conveyor-based simulation using physics. You only need to take care of the layout and device operation (kinematics, behavior modeling), and the physical simulation handles how products (parts) are affected by external forces and shifts their positions accordingly. The application opens the door to easily build simulations for cases like stoppers, pushers, and more.
Watch this video to see how it works:
Return to top. ^
Human simulation and ergonomics
Process Simulate Human helps you to eliminate any risk to operators with walk path analysis, reachability tests, vision analysis, and ergonomics assessments.
The following new capabilities are available in 17.0.
Human library
With the addition of a Human Library, figures can be easily saved and loaded without the need to redefine their parameters each time. A family of figures can be created to represent company or assessment needs, and easily added to any study. With new default male and default female commands on the human ribbon, you can also select which humans you would like to have available for 1-click loading to any scene. Libraries can be customized to include anthropometric database selections, custom body size dimensions, ethnic appearances, and clothing color selections.
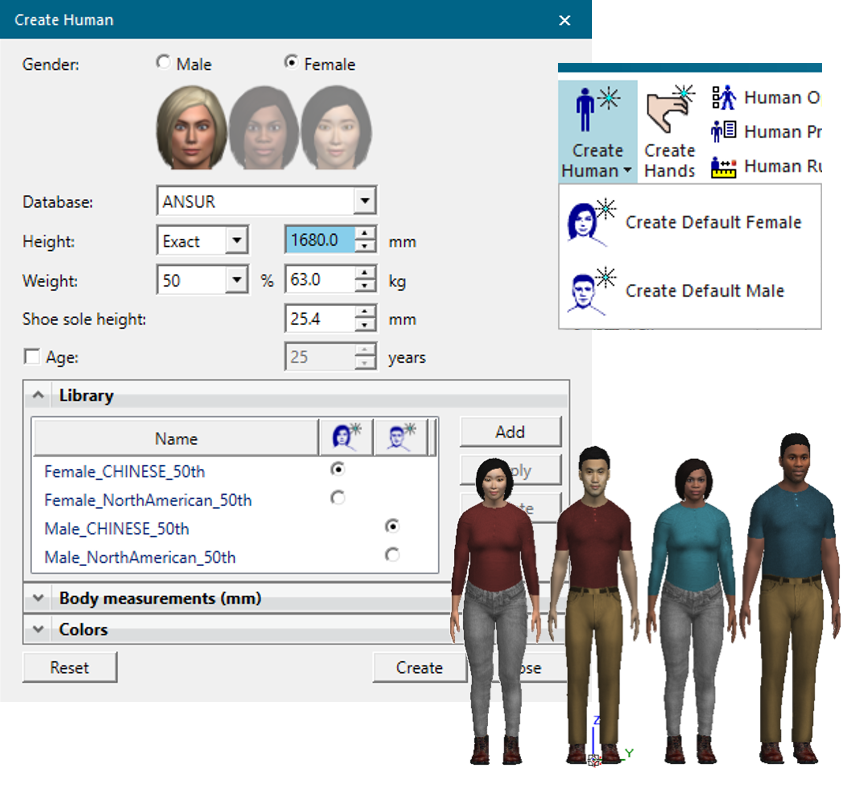
Human work zones
A Work Zone tool was added to quickly visualize if a workstation design adheres to ergonomic guidelines. The zones are fully customizable and allow for rapid validation enabling the performance of proposed tasks without extreme reaches. Work zones allow non-expert users to conduct ergonomic screening of a workstation design, as the reach guidelines are captured within the zone. Work zones can be used with or without a human in the scene, to rapidly confirm if a workstation or product design meets ergonomic reach guidelines. Zones can be exported as JT files and shared with others for easy communication of design requirements. Work zones are communicated to the Process Simulate Virtual Reality application to allow immersive optimization of workstation design and conformance with reach guidelines.
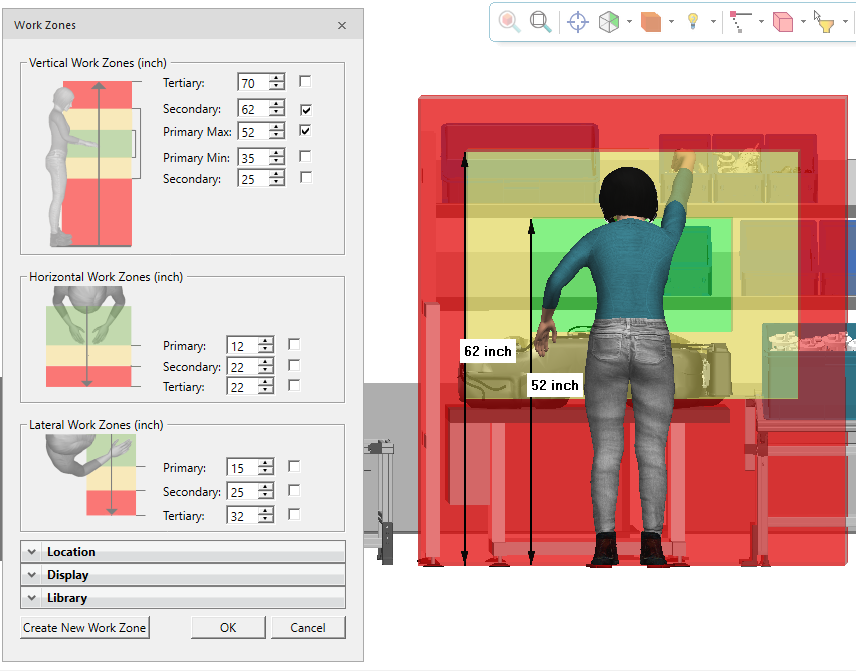
Human rulers
Human rulers were designed specifically for working with humans. The tool allows rapid measurement creation by selecting a commonly used point on the human or within the scene to place ruler ends. Measure to and measure from locations are set, along with parts of the ruler to be displayed (linear, X, Y, Z). Once created, rulers are stored with the human so that workstation modifications can be quickly evaluated in later sessions. Human rulers help you to conduct studies quickly and clearly communicate dimensional needs.
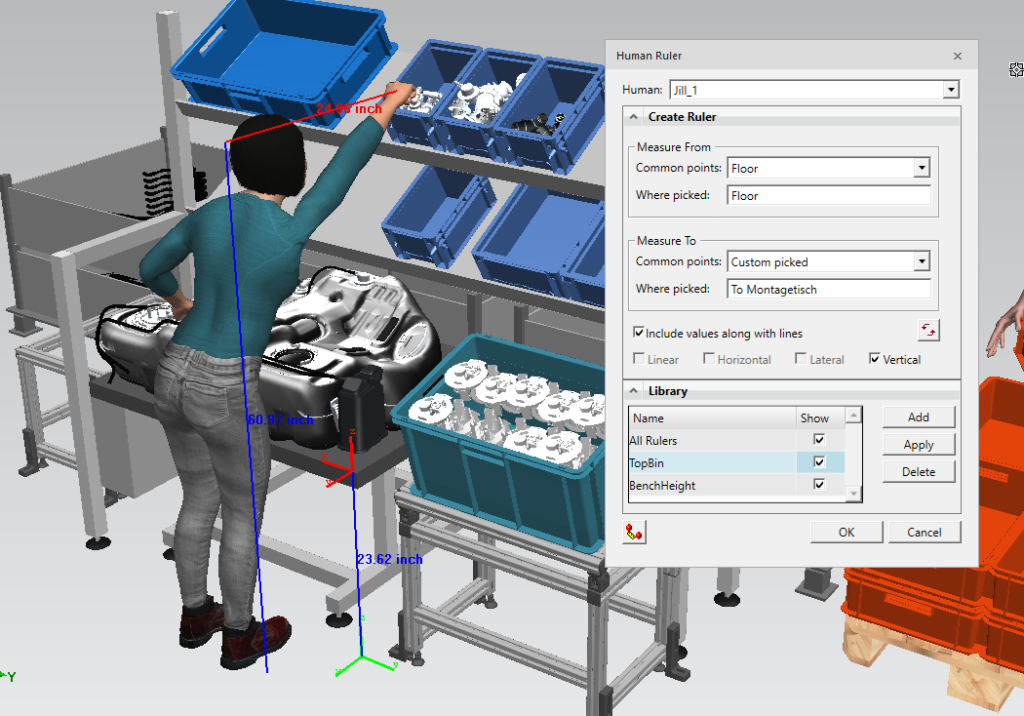
Return to top. ^
Virtual reality
Process Simulate VR delivers an immersive virtual reality environment for better engineering reviews, staff training and realistic process validation.
VR: Immersive ergonomic feedback
With ergonomic highlighting, human performance needs can be immediately evaluated while immersed. As the tracked person interacts with a workstation or performs an assembly sequence, postural feedback can be seen directly on the figure.
Postural feedback is provided to users in two forms:
- A new heads-up display (HUD) has been added when VIVE body tracking is active. The HUD can be enabled during full body tracking, to provide first-person feedback about your postures in real time. Furthermore, when posture recording is active, the HUD indicates the recording status so you can more easily keep track of your activities in VR.
- Real-time ergonomic highlighting allows for postures to be assessed in real-time by observing joint highlighting on the figure. When a human assumes a non-ideal posture, the affected joints are highlighted in yellow (warning) or in red (higher risk) to draw attention to body areas of concern. As the human moves, the highlighting continues to update.
Watch this video to see how it works:
VR: Collaboration
During a VR collaboration session, you and your colleagues can now immerse together while simultaneously using VIVE full body tracking to control your avatars. This brings an enhanced level of realism to the immersive experience. Together, in the VR scene, you can move naturally with others to evaluate assembly sequences, test and modify workstation layouts, review ergonomic risks, among other activities that would normally be performed face-to-face.
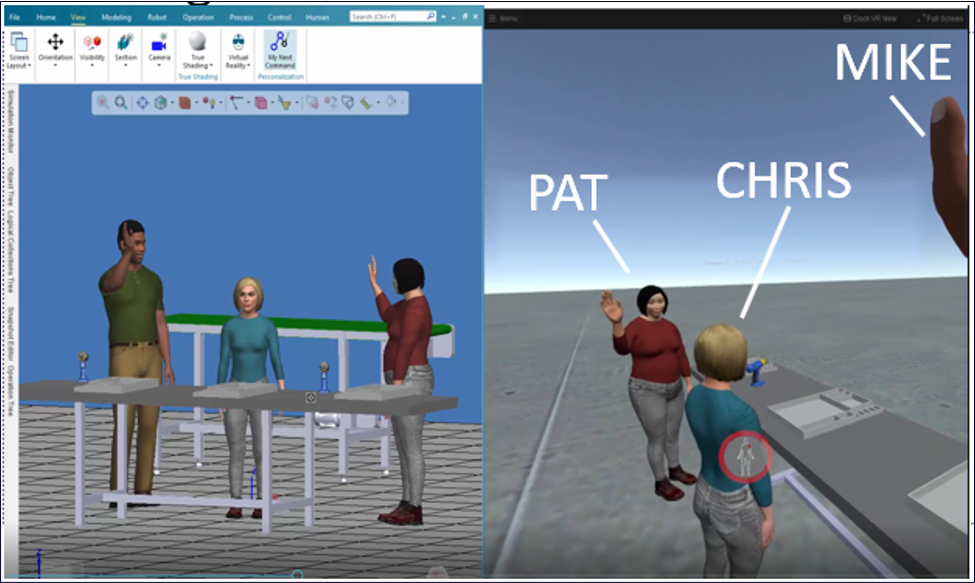
VR: Live hands
The live hands feature allows you to select objects to interact with while immersed in VR. New in 17.0, each object can be annotated with multiple design locations, enabling more complex assembly sequences to be performed in VR with greater accuracy. Specific ‘design’ locations can be selected for each object, so when acting out tasks in VR, items can be precisely placed.
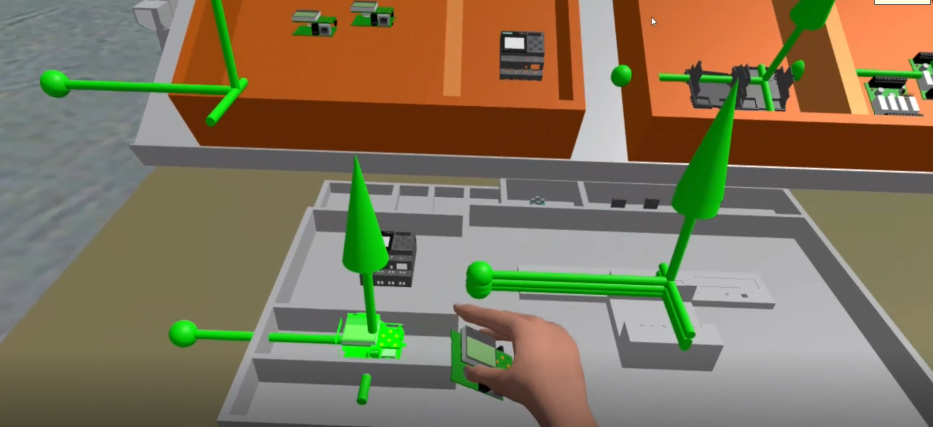
VR: Hardware support
The HP Reverb G2 headset and hand controllers can now be used with Process Simulate VR, to allow a wider range of hardware options. Guided set-up is available using the Microsoft Mixed Reality Portal.
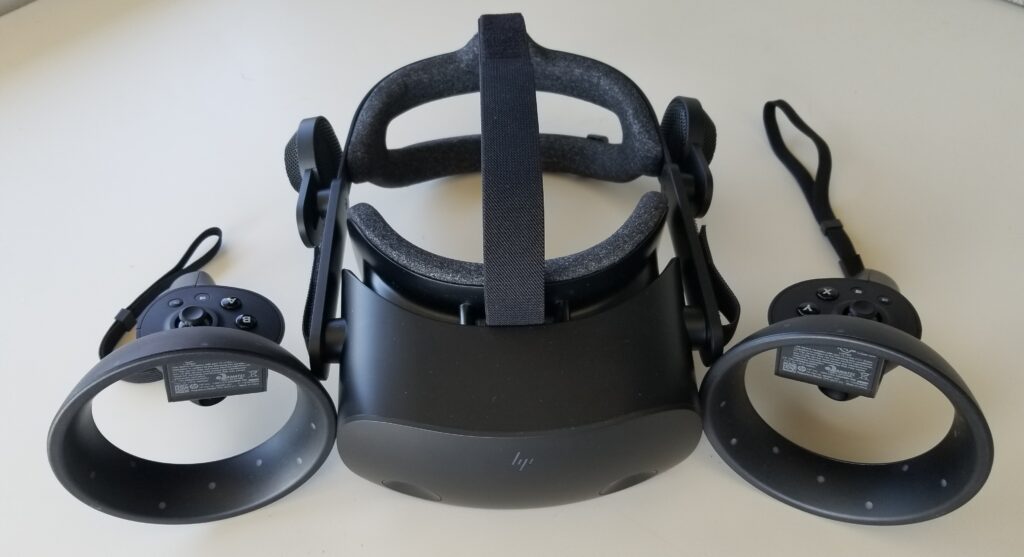
Return to top. ^
Assembly
Process Simulate Assembly helps you to run feasibility, go/no-go, and what-if scenario tests for a multitude of activities. You can perform assembly and disassembly sequence validation, and virtually assess material flow, load assist needs, factory layout, and more.
The following new capability is available in 17.0.
Smart tool position
Smart tool position enables selecting a tool and placing it easily on top of a fastener without the need to use placement and relocate tools. When the tool is dual sided, like a hex or Allen key, it is possible to flip the tool to place the other side over the fastener. You can turn on the compatibility options to verify match by shape type and by size. Matching by type is done using a trained AI network in the background. For matching by size, it is possible to regulate the permitted match tolerance, up to 20%. Known limitation in version 17.0 – the compatibility options are supported only for objects without exact geometry (i.e., those with approximate geometry).
Watch this video to see how it works:
Return to top. ^
—–
These are just highlights of the advancements delivered with the latest Tecnomatix release. For complete details on the new features of Tecnomatix 17.0 and its supporting releases, please refer to the release notes and new features presentations offered with the software download.
And, as always, hop on over to the public community and website for all things Tecnomatix.
Yours in digital manufacturing,
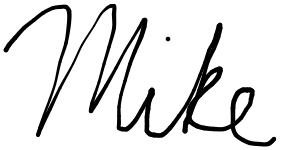
(on behalf of the entire Tecnomatix product team)
—–
Don’t have Tecnomatix software? > Try it for free.