Products
Virtual commissioning with the digital twin
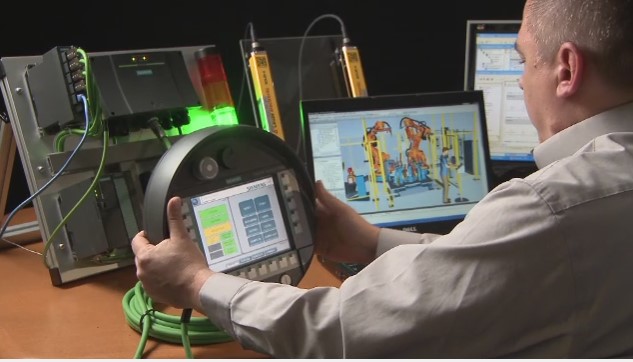
Authored by Noam Ribon, Senior Business Consultant, Siemens PLM Software
Manufacturers and, in extension, their suppliers are experiencing unprecedented pressures of competition: changing customer demands, ever shorter product lifecycles, increasing number of product variants, reduced product launch times, and increasing pressure in terms of earnings. At the same time, and to address these pressures, ever more flexible production machines and production systems are being introduced, with sophisticated tooling, mechanized automation, robots, transfer lines and safety equipment. To coordinate and ensure all of those pieces are operating in concert with one another, Programmable Logic Controllers (PLCs) are employed.
Commissioning
Given machine and system sophistication, a particularly critical and sensitive phase must occur prior to being able to start production. This phase is when deliveries from mechanical, electrical and controls engineering come together for the first time to form the production machine or system. Until now, such integration was only possible on the shop floor, which meant that every realized change or rework at that stage generated delays, increased costs, threatened loss of reputation, and potentially reduced market share, undoubtedly if such changes adversely affected machine delivery or production launch. Even when the only change is an update to the PLC program, engineers still incur delays or even production stoppages while they debug that PLC program against live equipment.
Introducing Virtual Commissioning
With the advent of the Digital Twin of the mechanical and behavioral model of the machine or system, Siemens PLM Software complements its applications with the ability to drive those virtual models with the same PLC programs that will drive the physical twin of the machine or system in production. This allows for visual observation of machine or system response to the PLC program, identification of potential shortcomings or areas for optimization, activities otherwise not possible before the physical machine or systems are available.
Virtual Commissioning allows engineers to connect the Digital Twin to the PLC to test, refine and optimize mechanical, electrical and logical designs, and the integration between them, well before hardware is assembled on the shop floor, without the need to delay delivery or stop production.
What Virtual Commissioning Provides
- A common virtual space for mechanical, electrical, controls and systems engineers to collaborate and develop simultaneously, rather than serially, at an early stage.
- An environment to perform early testing of mechanical behavior as driven by controls, early testing of control logic through observation of machine or system reaction to PLC output, and PLC reaction to machine or system input.
- In-depth simulation of the entire production plant with all its components, allowing ramp up or reconfiguration with minimal production stoppages.
- Shifting of commissioning off the production floor, reducing on-site personnel during the final commissioning phase from several weeks to a few days, cutting costs significantly.
- A realistic validation of a machine or system allowing for identification and resolution of errors, as well as optimization of the logic programmed into the PLC, by visualizing such things as improper material flow or an incorrect sequence of events.
Siemens Virtual Commissioning Products
Since commissioning spans varying device types and systems constructs, Siemens products are tailored to match specific commissioning needs. Each product is designed to highlight the specific characteristics and behavior of interest of the device or system for which it is intended. In all cases, hardware-in-the-loop simulation using various Siemens controls can be performed as part of the virtual commissioning process.
Robotic Assembly Systems: Process Simulate
Such systems or machines use robotics extensively. The PLC interacts significantly with the robot or robots and testing must take into account detailed robotic simulation. Examples of such systems are spot weld assembly lines, material handling systems, spray painting booths, and machines with integrated robotics.
Conveyance-Centric Material Flow Systems: Plant Simulation
Such systems are constructed of conveyors and devices, whereby the devices are attached to or perform in concert with the conveyors. Examples of such systems are automotive assembly conveyance systems, in some cases spanning across the entire plant, baggage handling systems, and material flow automation for both discrete and process manufacturing industries.
Machines with Moving Mechanisms Handling Parts: Mechatronics Concept Designer
These machines have internal mechanisms that move or process parts and interact with both PLC and CNC controls.Of major importance here is physics behavior of parts, such as gravity, force, torque, and load profiles used for sizing drives. Examples of such equipment are assembly machines used for packaging and machine tools used for milling and grinding operations.
About the author: Noam Ribon is a Senior Business Consultant with Siemens PLM Software with a specialization in Digitalization of Manufacturing, program, project and IT management. Noam has over 30 years of Computer Aided Design (CAD), Product Lifecycle Management (PLM), Digital Manufacturing and Digitalization (Industrie 4.0) software experience across various industries.
If you have questions or comments for Noam, please leave them in the comments section below.