Small and medium sized companies can commission and deliver manufacturing systems faster and cheaper
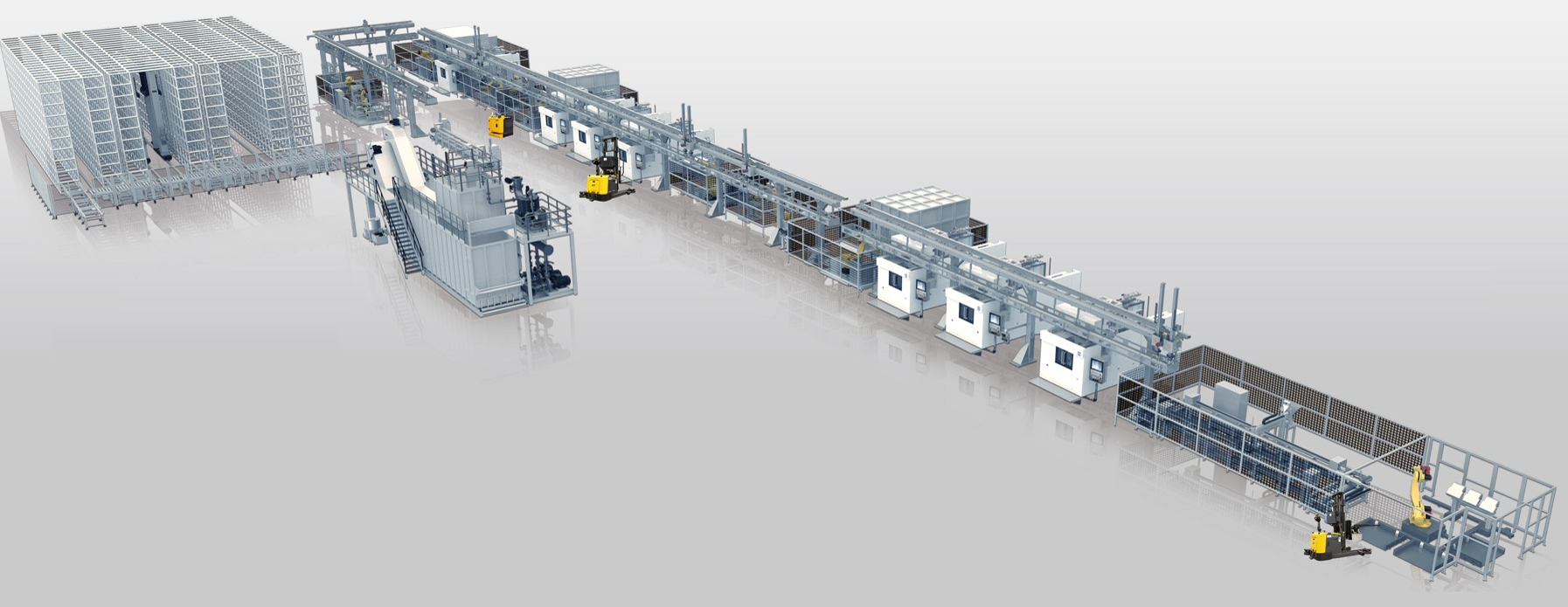
Shanghai SmartState Technology Co. Ltd (SSS), is a spin-off from Shanghai Jiaotong University (SJTU). It leverages IP, R&D, and engineering resources from SJTU, focusing on the development and commercialization of advanced machining and smart manufacturing equipment, processes, and turnkey solutions.
“Shanghai Smart State is a very special and innovative company. They have a great vision, led by experienced industrial veterans, and supported by energetic young talents. We are very pleased to be a part of the journey and are committed to developing a long-term partnership with SSS.”
Richard Li, GM of automotive industry Greater China at Siemens Digital Industries Software
SSS used to have a long design and deployment cycle due to their traditional waterfall process, that is, to start with the CAD drawing for the product – in this case, an automation line with robots and CNC tools for mixed production of multiple engine block parts, assembly, and testing. Once the design was complete, the team would have to wait for the hardware to arrive before commissioning the line on the shop floor. This caused long lead times and many unforeseen issues could happen during commissioning. If anything were to go wrong, in addition to risk of damaging the physical assets, the engineers would need to redesign the components and order from their suppliers again, or reprogram the robots, making the project cycle even longer. The result is increased cost, unstable product quality, and long project delivery times that added cashflow pressure to the young company.
SSS started to use Process Simulate in the Tecnomatix® portfolio from Siemens for virtual commissioning to upgrade their process. Once CAD design is finished, the engineers build the digital twin for the production equipment and manufacturing process using Process Simulate software, including part conveying, robotics part handling, CNC machine tending, test station tending, etc. It not only helps to achieve full process visualization, but also helps the engineers to check mechanical collisions to avoid problems during physical deployment. For example, once a robot collision with equipment is detected, the engineer can adjust the robotic path to avoid such collisions. Later, the offline programming packages in Process Simulate can generate the robot control program for those paths automatically, which can be downloaded to the physical robot controllers for use. The engineers also used the cyclic event emulation functions in Process Simulate to build in the logic of the production process since the line is designed to produce multiple products. Such logic was then implemented with Siemens PLC programs and tested fully in the digital world using the combination of Process Simulate Virtual Commissioning and Siemens TIA Portal/PLCSim Advanced (Siemens’ virtual PLC software) before downloading to the physical PLCs on the shop floor. In other words, the solution was used to jointly design, validate, and optimize mechanics, robotics, and automation systems in the digital world. This practice is independent of the hardware, therefore zero burden to procurement and no risk of damage to physical assets.
“In one project, SSS was able to avoid tens of interferences in layout and manufacturing process in the design phase. Tens of robot programs and PLC programs were also tested and authorized in advance. As a result, the commissioning time was reduced by almost three months, the delivery time was reduced by 125 days, and the overall cost was reduced by 14%.”
Mr. TIAN Ang, deputy head of digitalization department at Shanghai SmartState
> Watch this video from SSS to see how they use Siemens software to execute virtual commissioning with the digital twin.
“SSS took a very challenging task in their sector. The SSS team managed to master Siemens digital twin technology in a short period of time to realize its value and now Siemens is also getting cutting edge requirements from SSS. Our global R&D team speaks very highly of SSS and hope to strengthen technology collaboration.”
Peter Ni, account orchestrator for SSS at Siemens Digital Industries Software
“With great support from the Siemens team, SSS is now exploring extending the digital twin to other applications, such as remote monitoring and maintenance of delivered products, assembly process planning, automated machining process planning, and continuous improvement of our products and services. The digital twin is also extremely useful for internal and external communication.”
Mr. TANG Shuilong, director and head of digitalization department at Shanghai SmartState
—–