Engineering.com: how industrial AI, cloud and industrial metaverse are powering manufacturers in 2025 and beyond [ARTICLE]
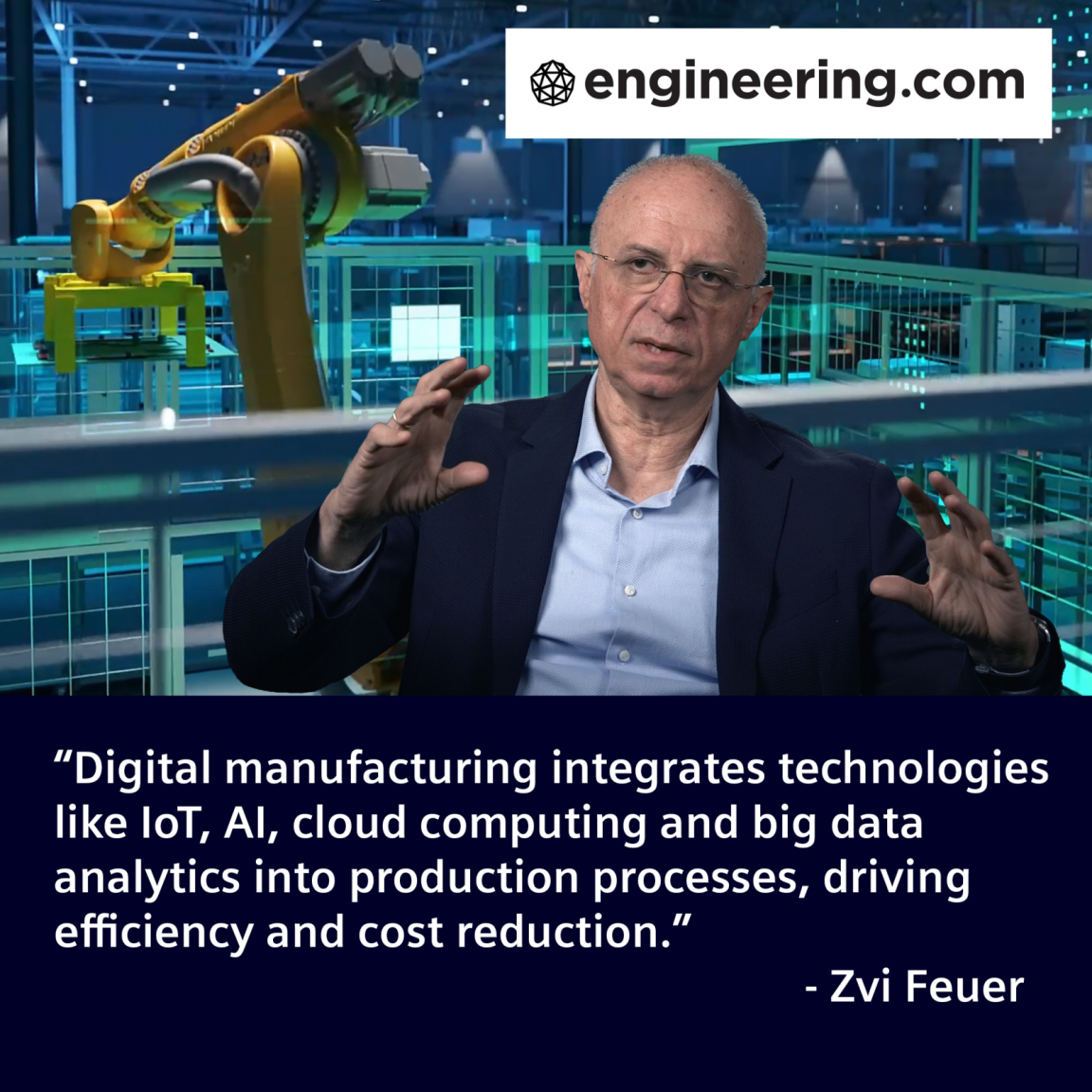
Engineering.com, a leading media outlet producing news, analysis, and how-to content for engineers, recently featured Siemens Zvi Feuer, Senior Vice President, Digital Manufacturing Software Solutions, discussing the exciting advancements in the works for 2025 and beyond. These innovations represent a transformative leap in how manufacturing technologies are evolving to meet the needs of a rapidly changing world.
In the Engineering.com article, explore the latest industry trends and how manufacturers are addressing them. Discover the latest technologies, such as digital threads that unify production workflows, next-generation cloud-based solutions and the transformative impact of artificial intelligence (AI) across the entire design-to-manufacturing process.
The digital thread: unifying manufacturing planning and production
At the heart of Siemens digital manufacturing solutions is the digital thread, a unified framework that connects all aspects of the production process. This enables a seamless flow of data across the entire manufacturing ecosystem, creating a single, real-time view of the product lifecycle. By linking every step, manufacturers can unlock significant efficiencies and increase time-to-market.
An area where I see a big emphasis is digitalization of manufacturing and planning of the production facility to ensure that we are much more efficient, effective, resilient and agile to enable a much higher utilization of production facilities.”
Zvi Feuer, Senior Vice President of Digital Manufacturing at Siemens
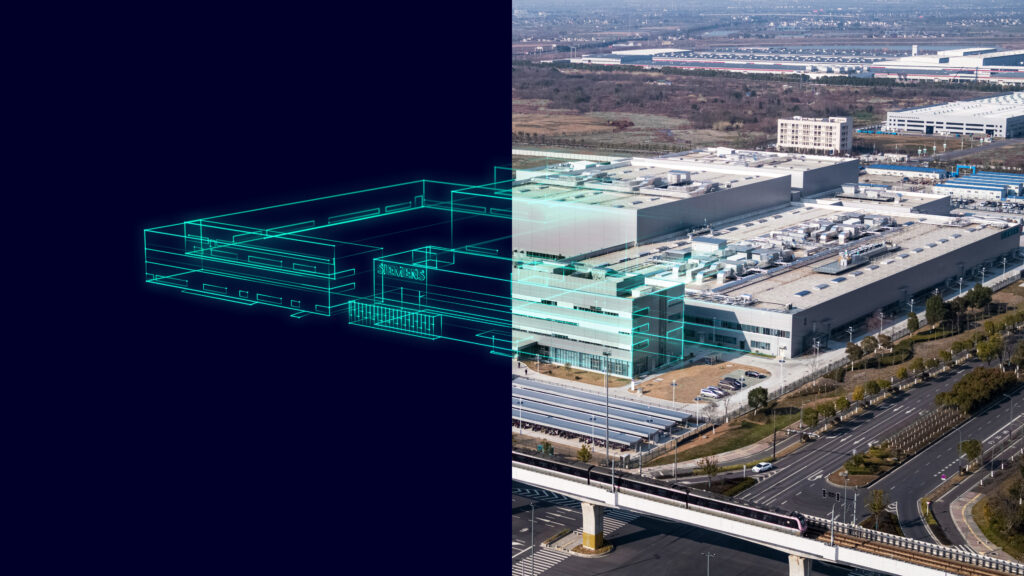
For example, think of production optimization within a digital factory twin and how it can streamline inventory management, reduce throughput time, and precisely tune buffer sizes to minimize waste and idle resources.
Using Tecnomatix Plant Simulation, manufacturers can model, simulate, and analyze production systems and logistics processes. This enables manufacturers to optimize material flow, foresee bottlenecks, and validate decisions in a risk-free virtual environment.
Another compelling example of the digital thread in action referenced in the Engineering.com article is the creation of a comprehensive digital twin where a Chinese manufacturer in Nanjing, China simulated various scenarios and processes in a virtual environment, ensuring that every element of the factory, from robots and automated guided vehicles (AGVs) to human interactions, were optimized before any physical investment was made. This resulted in reduced costs and ensured that the final facility operated smoothly from day one.
A new era for manufacturing with industrial AI
Industrial AI is at the core of Siemens strategy to help manufacturers overcome complex programming tasks that once required years of expertise. With AI copilots integrated into solutions like Process Simulate, manufacturers can now simplify complex programming tasks. This technological leap frees up valuable resources, accelerates processes, and reduces the chance of human error.
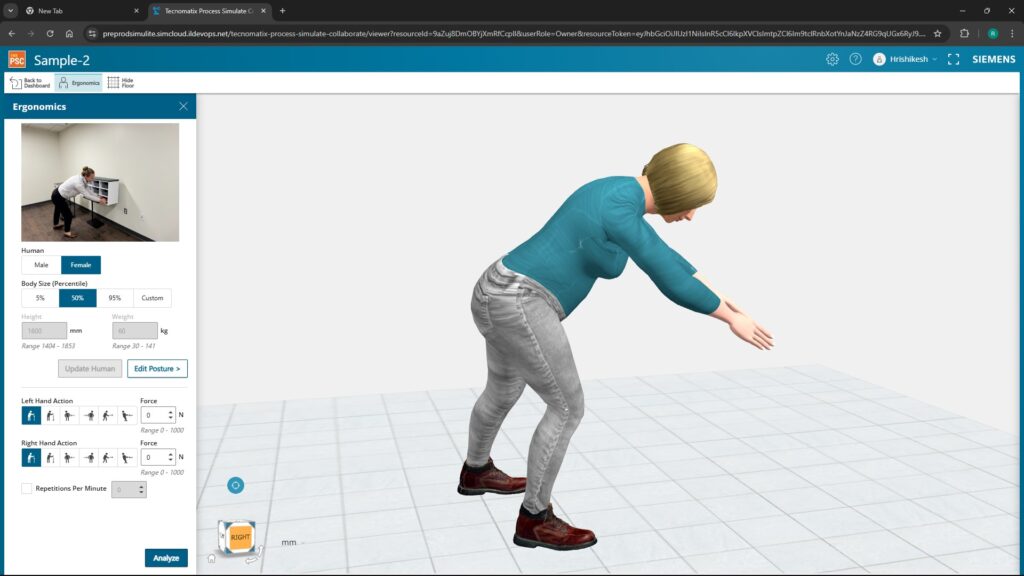
Another example is how AI-driven human simulation is transforming manufacturers approach to ergonomics by improving the analysis of high-risk scenarios. Using Process Simulate Collaborate ergonomics capabilities, analyze a photo and generate 3D models of worker movements, identifying potential injury risks and enhancing workplace safety. This proactive solution empowers manufacturers to address ergonomic challenges easily, fostering safer and sustainable worker environments. Customize the size of the human to pose, assign hand force exertions and action frequencies, then all variables are taken into consideration and feedback is provided about the task safety.
Cloud computing – the catalyst for smart manufacturing
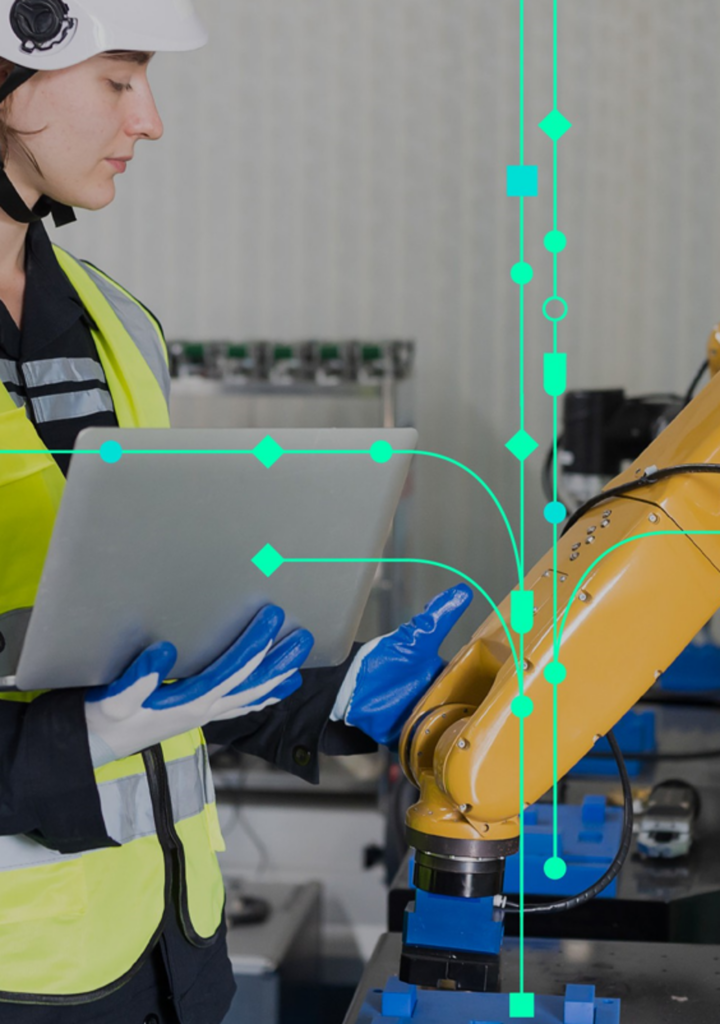
The cloud plays a pivotal role in Siemens vision of transforming manufacturing operations. With the recent launch of Process Simulate X and Plant Simulation X, manufacturers have access to industry-leading digital manufacturing capabilities with the added benefits of cloud-based deployment, gaining the flexibility and security they need to scale their operations efficiently.
Cloud-based deployment empowers manufacturers with scalable, cost-efficient tools for higher productivity and quick expansion of digital manufacturing capabilities. Tailored for varying complexity, Process Simulate X and Plant Simulation X offers cost-effective, customizable solutions to meet diverse manufacturing needs, from small companies to large enterprises.
Reimagining collaboration with the industrial metaverse
The Engineering.com article features how Siemens works with partners like NVIDIA to create a fully immersive digital environment that mirrors real-world manufacturing operations. The industrial metaverse combines digital twins, IoT sensors, and high-fidelity visualization to create a new way of working. It’s an environment where manufacturers can collaborate, test, and optimize before anything is physically produced.
For example, explore a battery production scenario using Process Simulate where manufacturers can leverage the physics-based digital twin within a virtual shared space, the industrial metaverse transforms collaboration across value chains.
Using a digital twin built with Siemens Xcelerator software, interactions between robots, AGVs, and humans in the production cell are accurately simulated. The battery pack assembly line is then modeled in NVIDIA Omniverse, which connects seamlessly with Siemens digital manufacturing tools.
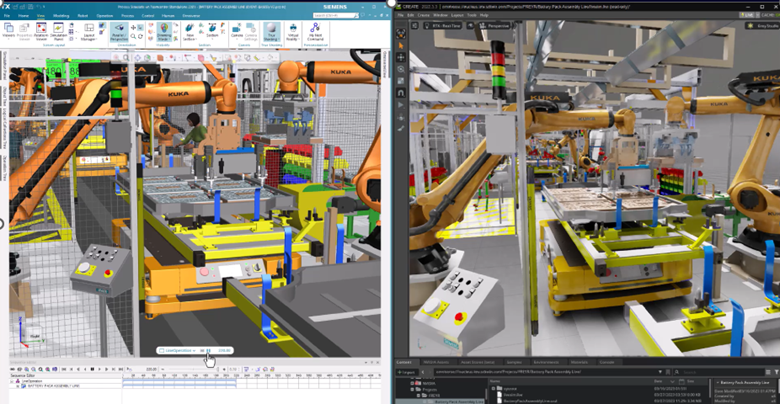
The future of manufacturing
Zvi points out that the convergence of AI, cloud computing, and the industrial metaverse is setting the stage for a new era in manufacturing. These digital technologies are not just improving productivity—they are redefining how products are designed, manufactured, and optimized. As manufacturers continue to adopt and integrate these technologies, they will realize unparalleled efficiency, sustainability, and agility.