Digital Manufacturing helps Airbus achieve its ambitious goals
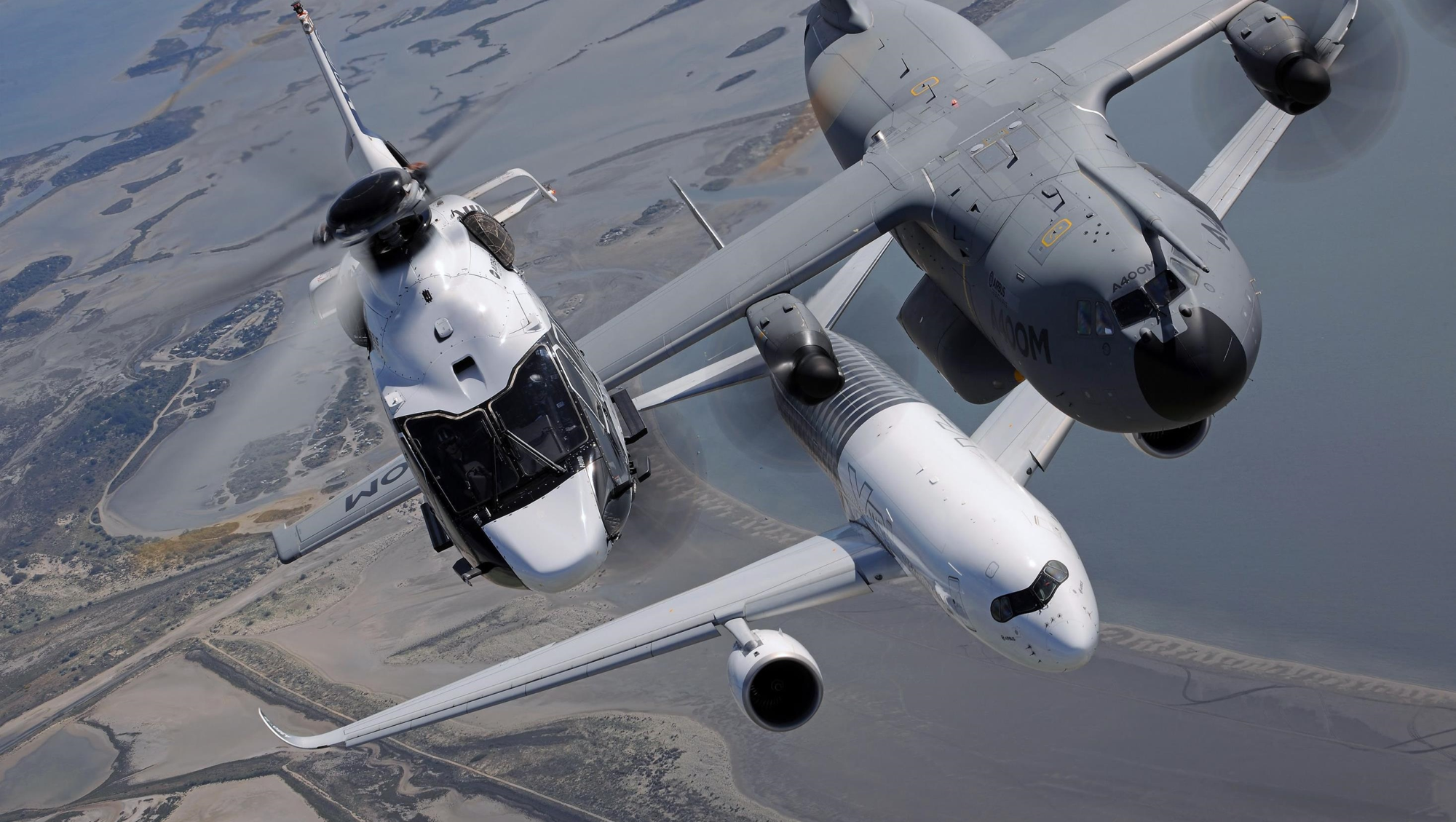
Airbus uses Plant Simulation and HEEDS software for closed-loop modeling, simulation and optimization of aircraft design and industrial architecture in the early phase of development.
Airbus’ ambitious environmental goals
Airbus is an international pioneer in the aerospace industry, with commercial, defense, space, and helicopter divisions within their global operations. At the forefront of the aviation industry, Airbus has over 130,000 employees across 35 countries and 180 sites. Airbus has partnered with Siemens Digital Industries Software on their digital transformation journey. At Realize LIVE 2020, Siemens’ global customer event, Airbus presented their latest accomplishments in manufacturing innovation. This blog summarizes their presentation.
Airbus has ambitious aviation industry targets. Their dedication to sustainable growth is reflected in their commitment to improving aircraft fuel efficiency and reducing CO2 emissions, all while fulfilling their growing backlog of orders. They successfully improved their aircraft fuel efficiency by 2.2%, on a target of 1.5%, each year from 2008 to 2020.
So how are they achieving their goals? Innovation. Airbus had to design lighter-weight aircraft that could use sustainable fuels, with capabilities like single-engine taxi, idle reverse thrust, continuous descent, and more. They needed a sophisticated digital manufacturing infrastructure that could create innovation efficiency.
The digital manufacturing infrastructure
Airbus required a complete digital manufacturing infrastructure that allowed the creation, evaluation, and comparison of various industrial scenarios to optimize their complex designs and manufacturing processes. They needed to bridge the engineering and industrial perspectives to tackle new demand and create innovation efficiency.
Airbus’ advanced industrial architecture included methods and tools for:
- Co-development during product concept phases
- Versioned multi-scenario generation using an AI engine and supporting set-based design
- Identification of missing technology bricks that were used to design the most competitive scenario
They created an end-to-end data chain that connected the program view, the product view, industrial architecture scenarios, and dynamic performance assessments. Scenarios included different variations of industrial design, including centralization, global allocation, and level of vertical integration.
During evaluations, a series of inputs are used to calculate the static industrial performance of a scenario, including the operational level, the production cell level, and the production line level – ultimately getting to a full scenario level. Inputs include variables such as workload, energy consumption, number of workers, and site information such as hourly wage, country energy rates, and country CO2 emissions. A scenario evaluation included product line and global non-recurring costs (NRC), recurring cost (RC) of labor, recurring cost (RC) of resources, and CO2 emitted by line.
These scenarios are handed over to Plant Simulation in the Tecnomatix® portfolio of digital manufacturing software and enriched with simplified manufacturing execution system (MES) variables necessary for optimization.
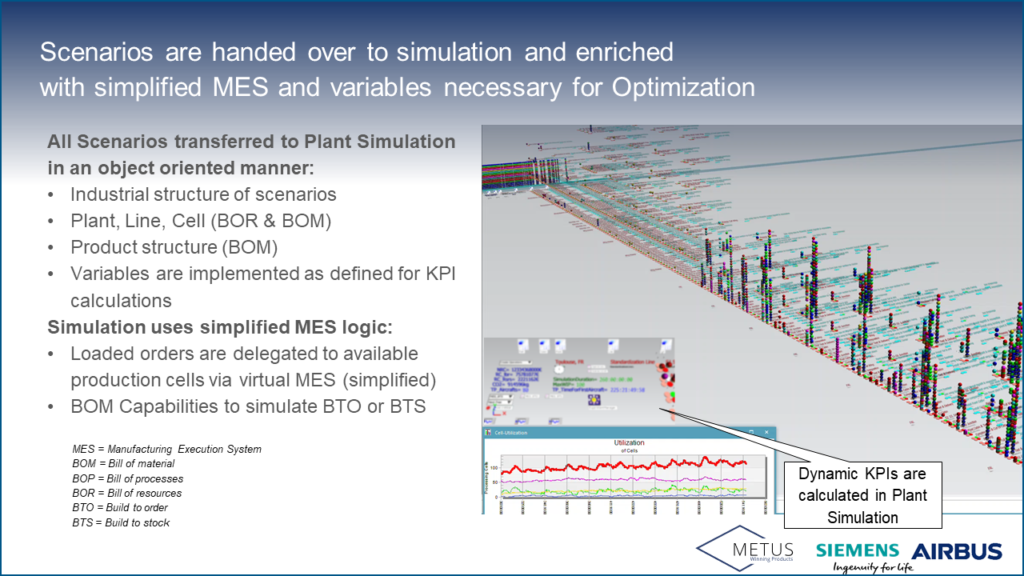
Tecnomatix Plant Simulation
Tecnomatix Plant Simulation allows manufacturers like Airbus to model, simulate, explore, and optimize logistics systems and their processes using discrete event simulation and statistical analysis capabilities.
Plant Simulation is a critical component of Airbus’ digital manufacturing infrastructure. Their scenarios are transferred to Plant Simulation in an object-oriented manner, including plant, line, and cell structure – Bill of Resources (BOR) and manufacturing Bill of Materials (mBOM), as well as product structure or engineering Bill of Materials (eBOM). Loaded orders are delegated to available production cells via virtual MES BOM Capabilities to simulate build to order (BTO) or build to stock (BTS) manufacturing. Metrics are measured throughout simulation, which reveal work in progress (WIP), utilization of cells, energy consumption of resources, and other resource statistics.
Airbus uses Simcenter HEEDS™ software, a powerful design space exploration and optimization solution, to drive product innovation. HEEDS accelerates the product development process by automating analysis workflows, maximizing the available computational hardware and software resources, and efficiently exploring the design space for innovative solutions, while assessing the new concepts to ensure performance requirements are met.
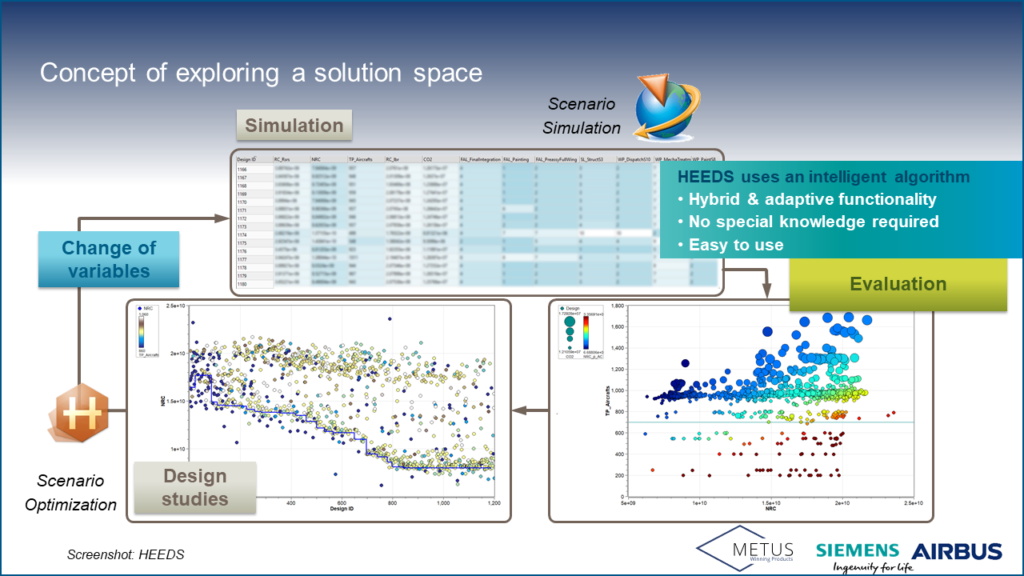
In conjunction with Plant Simulation, the desired performance profile is defined, and HEEDS determines a number of suitable variants. HEEDS uses an intelligent algorithm to optimize hybrid and adaptive functionality. HEEDS allows Airbus to understand the most important levers for improvement. These levers are then used as inputs to further the evaluation of scenarios. The entire digital solution drives the overall best design with the appropriate specifications.
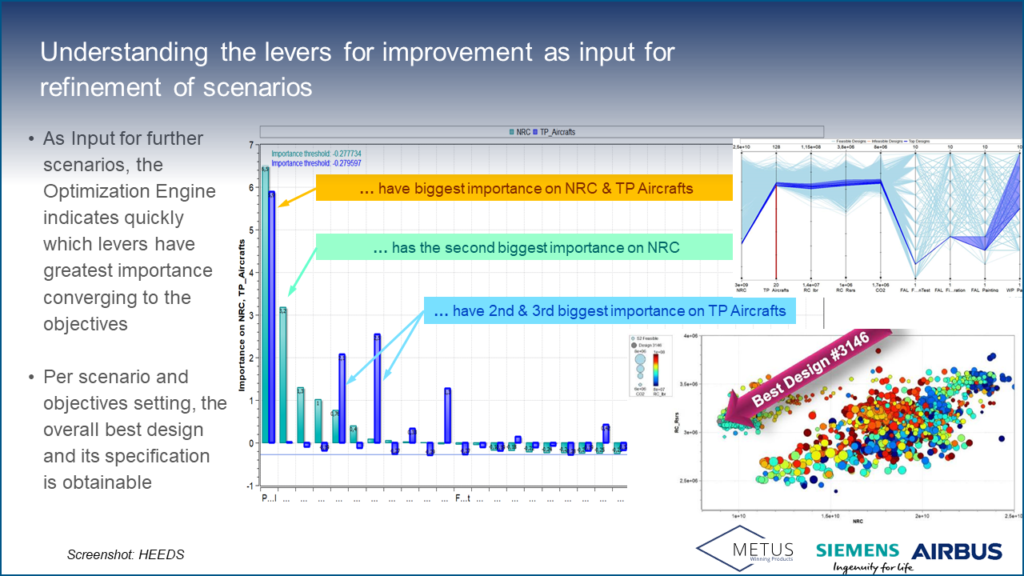
Airbus closed-loop innovation efficiency
These connected systems give Airbus the capabilities for closed-loop modeling, simulation and optimization of aircraft design and industrial architecture in the early phase of development. The systems support the entire process, from product and industrial requirements all the way to the physical industrial system. Their feedback to the product design early in the process dramatically reduces time to market and improves cost efficiency. Airbus is then able to rapidly iterate to an optimal and validated design, having analyzed many alternative concepts.
Siemens continues to partner with leaders across manufacturing industries to build products and systems that improve sustainability, safety, quality, and compliance, allowing them to better serve their customers, and contribute to a more prosperous world.
—–