How to reduce week-long commissioning times
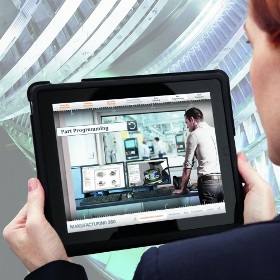
Why has no one thought about this before? How week-long commissioning times at the customer’s location can be reduced to a few days
Written by:
Matthias Heinicke, Siemens Industry Software GmbH
“Why has no one thought about this before?” is one of the most common rhetorical questions in the commissioning of complex industrial plants. Large scale systems can deliver great results if the software that is controlling them is written cleverly and without failures. Using sophisticated programmable logic controller (PLC) logic, with smart algorithms and clever case distinctions, can easily double the plant capacity. On the other hand, if the PLC software is based only on simple loops of copied and pasted processing it is often slow and the entire system has to contend with the nominal power.
How can really good, stable control software for large complex production facilities be created and tested before the system itself is built? Can control software that uses the amounts of data from numerous sensors and thus increase the system performance?
The answer is virtual commissioning. A computer model of the plant is created instead of the real system. This virtual image enables users to test controls and to improve PLC without physically moving material, without consuming energy, without creating noise and waste, to normal working hours and not into production breaks at night and on weekends. Best of all, it allows stress tests in the office, with the experts the company together without play updates on site at the customer at the last minute and to troubleshoot.
How does virtual commissioning work technically?
A complete production facility is modeled in Siemens PLM software Tecnomatix Plant Simulation
Sensors are created and named according to the real sensors using the OPC interface the simulation model with the Siemens TIA portal. In the TIA portal the real PLC code is developed. This video, “Virtual Commissioning on Factory Level,” by Ralf Tobel, R & D Director, Tecnomatix Plant Simulation describes the process.
Now, two cases are possible: Hardware in the loop and Software in the loop:
With Hardware in the loop, the real physical PLCs are connected with the simulation model e.g. using PROFINET –For an example, view “Siemens virtual commissioning portfolio,” video. Now the real PLC that will control the system later to the simulation model controls the simulation model. Special situations can be played through and analyzed like in a flight Simulator. These include, for example, the discharging of parts, overheating at sensors, lack of parts and smooth filing of gaps via PLC Control logic.
With the Software in the loop, no real PLCs are used, but PLC emulating software. The PLC code does 1:1 the code of which the system will control later. With this technology the complete system can be run on one PC in which the production is modeled, simulated, visualized, analyzed and optimized without cable to connect or hardware to be wired.
What is the benefit?
The virtual commissioning is not new but it is booming at the moment because of numerous Industrie 4.0 projects and is increasingly becoming a core technology. So reports the head of electrical engineering at Grenzebach Group. This video, “Tecnomatix Plant Simulation saves assembly time,” explains how they are achieving multi-week savings in operating per each project.
Another highly interesting case is described by Mr. Johannes Roeck from Siemens AG in ”Siemens – your partner for the entire battery manufacturing process.”
Modern lithium ion batteries are the key to the success of electric vehicles. Siemens supports the complete value chain from raw material extraction to testing the finished cells. The virtual commissioning of the lithium ion battery cells production reduces costs and increases profitability.
What are the restrictions?
Layout, size and complexity of the explored facility are nearly unlimited: the company Eisenmann, for example, installed at the airport in Doha a 1.6 km long electrified monorail system with 130 trolleys and roughly 20,000 transports per day.
“Using the joint work of the control programmer with the simulation expert who configured and used Plant Simulation, we created a virtual commissioning setup, in which we were able to identify and solve real problems of our routing strategy control program.”
“ Connecting Plant Simulation to the MFC, we were able to conduct some of this testing virtually, in the office. That’s another project first. More importantly, this means that the real commissioning effort was smaller. Because real onsite commissioning is expensive, this capability has the potential to greatly impact the competitiveness of our offering in terms of cost.”
Dr. Ullrich Ochs, Senior Manager Software Electrical Engineering, Eisenmann.
View our web pages to learn more about the virtual commissioning of complex production systems.
Ask an expert about a product, service or solution keyword “Virtual Commissioning using Tecnomatix Plant Simulation”
- Americas: +1 800 498 5351
- Asia-Pacific: +852 2230 3333
- EMEA: +44 (0) 1276 413200
Check out Siemens’ Manufacturing 360 tablet app!
Explore the world of digital manufacturing. See how Siemens’ software
for part and assembly manufacturing enable more efficient and nimble operations.
Download the FREE Manufacturing 360 app from Google Play or the Apple Store.