Automation World feature: robot grippers creating a more sustainable future for manufacturing
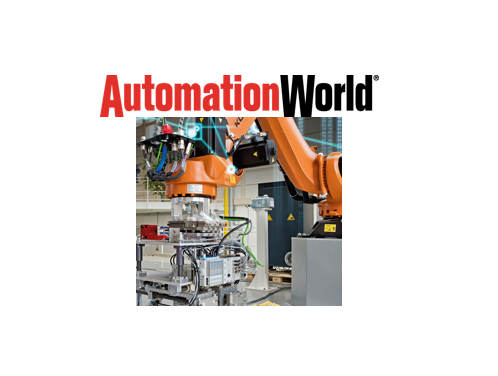
Automation World features how manufacturers can integrate lightweight design principles into gripper fabrication processes using additive manufacturing in tandem with the integration of simulation tools such as Siemens Tecnomatix Process Simulate.
In a recent interview between Automation World and Siemens discuss how additive manufactured grippers are fostering a more environmentally conscious future for robotics. Robot grippers have traditionally been manufactured completely using metal, resulting in heavy designs that are often over-engineered for their intended tasks. These grippers, in most cases are constructed to lift relatively light and less complex parts, have harmed energy consumption, particularly for battery modules or similar components. With over 3.5 million robots in operation globally, the potential for reducing carbon dioxide (CO2) emissions and energy consumption is immense. It’s important to note that more than 500,000 new robots enter the market annually and most of them require an individualized new gripper. Therefore, the implementation of lightweight additive manufactured grippers can lead to a substantial reduction in carbon dioxide emissions.
Hear from Siemens additive manufacturing expert and explore the Automation World article.
Why is this so important? Well, think about all the robots out there. By making their grippers lighter, we’re helping these robots use less energy. It’s like switching from a big, gas-guzzling car to a smaller, more fuel-efficient one. In doing so, the grippers can also embrace the latest, most up-to-date design so it’s a win-win scenario that combines efficiency with cutting-edge innovation.
Through the utilization of fully associative topology optimization, facilitated by cutting-edge software such as Siemens NX Additive Manufacturing, manufacturers can seamlessly integrate lightweight design principles into their gripper fabrication processes. This approach not only accelerates the design phase but also empowers workers with the agility to make real-time modifications, ensuring optimal performance in dynamic industrial environments.
In the automotive industry alone, there are estimated to be more than one million robots in factories across the globe. Many of these robots are lifting and positioning parts too unwieldy for humans to handle or repeatedly placing parts in precise locations. In many cases, the robotic grippers that move these parts weigh more than the parts they are moving, like sheet metal panels. Many automotive companies realize these types of robot work cells are good candidates for lightweight robotic grippers.”
Dennis Nier, Additive Manufacturing Business Development, Siemens Digital Industries Software
A more sustainable future for robotics
The integration of simulation tools such as Siemens Tecnomatix Process Simulate plays a pivotal role in quantifying the environmental and cost implications of gripper design iterations. By accurately calculating energy consumption and CO2 emissions, manufacturers can make informed decisions that prioritize sustainability without sacrificing operational efficiency. Such tangible benefits underscore the transformative power of lightweight grippers in driving sustainable manufacturing practices on a global scale. Lightweight additive manufactured robot grippers represent more than just a technological advancement; they help support a shift towards sustainability and efficiency in industrial robotics.