Why CAD BOM Separation?
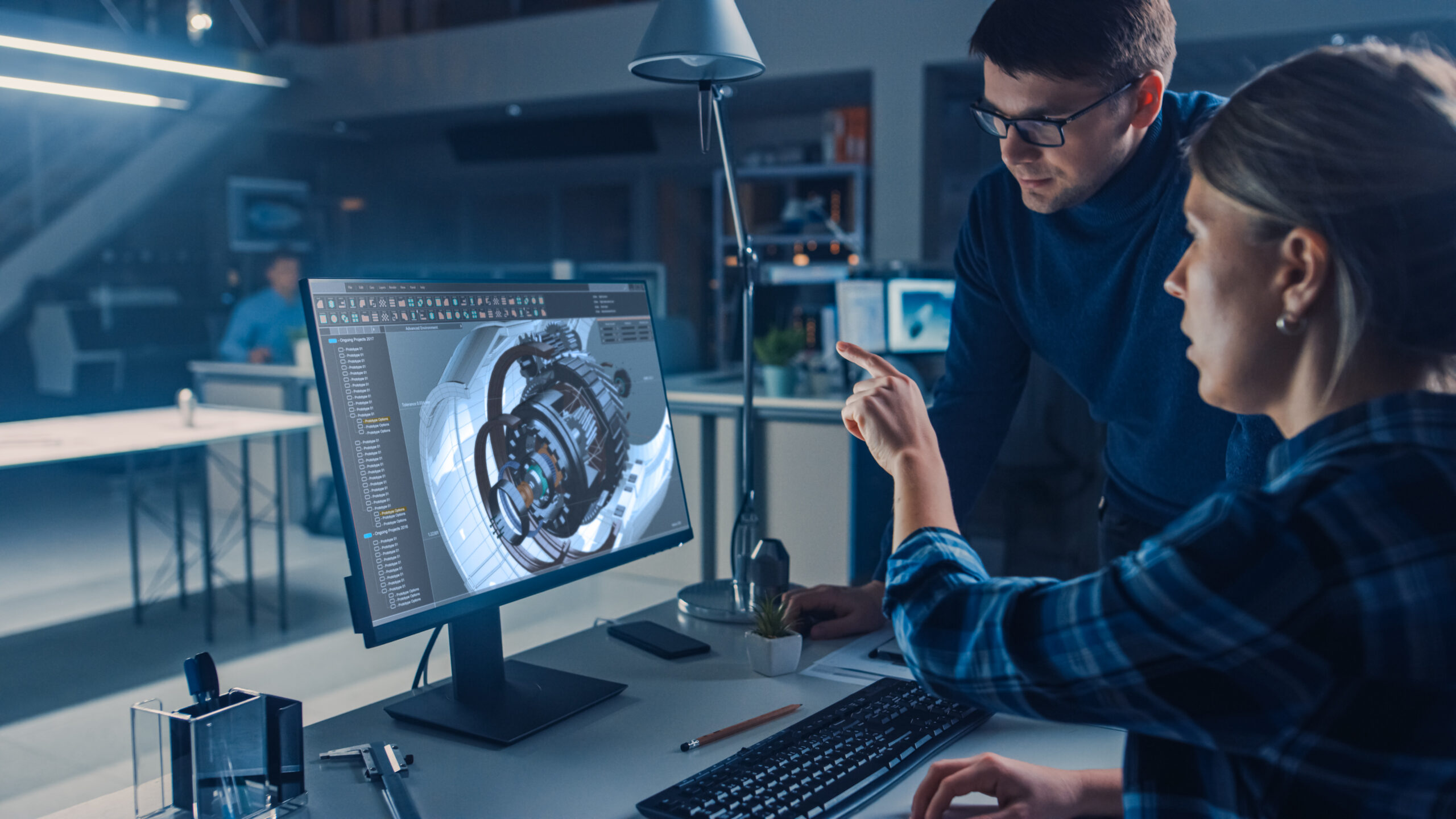
Parts Distinct from Design
Have you heard of EBOM before? The engineering bill of material (EBOM) for a product is a list of physical parts and assemblies designed and released by product engineering. CAD BOM (aka design BOM or design structure) is virtual and describes the product from a geometrical perspective. CAD BOM primarily deals with design structures linked with 3D CAD data. Design structures typically store the position information and contain lots of engineering-specific data, often termed non-BOM data. This is a repository for working data.
Historically, manufacturing/business parts have originated and managed in distinct – ERP/homegrown BOM systems. In contrast, design parts are managed in CAD management applications, and this has been an established practice at manufacturing firms. However, both need to be handled with some autonomy in a product lifecycle management (PLM) system.
Engineering communities have endlessly debated the need to manage a part distinct from design. Managing parts distinct from design provides relevant stakeholders within an enterprise the required lifecycle independence and associated flexibility to author and access part information and design information and manage their maturity throughout the product lifecycle. However, in a product lifecycle management (PLM) system, both need to be handled separately with some autonomy while evolving in a coordinated fashion.
Single BOM comes with Limitations
Managing design aka CAD and part content definition as a single integral item warrant a single lifecycle for design and part data for the program’s life. There is no difference in the breakdown/organization of design and part structures that force multiple groups to compromise. Key milestones are coordinated and managed closely between multiple groups that author part and design data. Changes impacting only one group inadvertently impact all other groups.
CAD BOM Separation
In today’s complex digital landscape, the evolution of a product involves orchestrated maturity of many individual disciplines: design, engineering, manufacturing, planning, service. Each domain has a way to view and organize a product and specific properties and behaviors to assign to a product’s parts and assemblies.
Efficiently managing, controlling, and eliciting change on such an orchestrated set of product data begins with accurately aligning the evolving product design, aka CAD BOM, and the product engineering BOM.
Our customers have been talking with us for a long time about their needs for having a different product design and product EBOM. While the product’s design and EBOM views are complimentary, they have other data structures and support various functions. Also, the way the design and EBOM evolve is quite different, with different business processes and different roles in the company taking part in them.
For example, designers, research & development, and the different engineering disciplines use various design tools to author, innovate, and create a rich set of designs to be inserted into a design definition. On the other hand, product engineers, purchasing, regulatory, and service must define and manage cost, logistics, opportunities, operations, regional availability, and rules in what constitutes the product EBOM.
For another example, in some companies, design tends to take the lead. Design systems and components evolve first, and much of the EBOM tends to resemble the design structure, with some additions in the EBOM from product engineers. However, in other companies, the EBOM takes the lead. The product engineer defines the assemblies and parts to be designed, and the design structure tends to resemble the EBOM.
Key Drivers for having a Distinct CAD BOM Separation
- Different lifecycles for design and part data over the program’s life allow the data to mature independently.
- Part of designing cardinality criteria:
- A single design represents multiple parts, e.g., color parts.
- A single part represents multiple designs, e.g., flexible hose that can be routed in multiple ways.
- Purchased part assembly listed as a single part in EBOM that has a design structure.
- The breakdown/organization of design and part data is optimized without one group compromising the other.
- Design data can be organized in a different way than how EBOM is organized. For example, zones can arrange design, and EBOM can be managed by functions or modules.
- The design structure may have a dummy or reference data that is not relevant in the EBOM.
- Changes can impact design, EBOM, or both, and there is a need to isolate change to design or EBOM when necessary.
Automated Alignment Creation and Maintenance is the Key
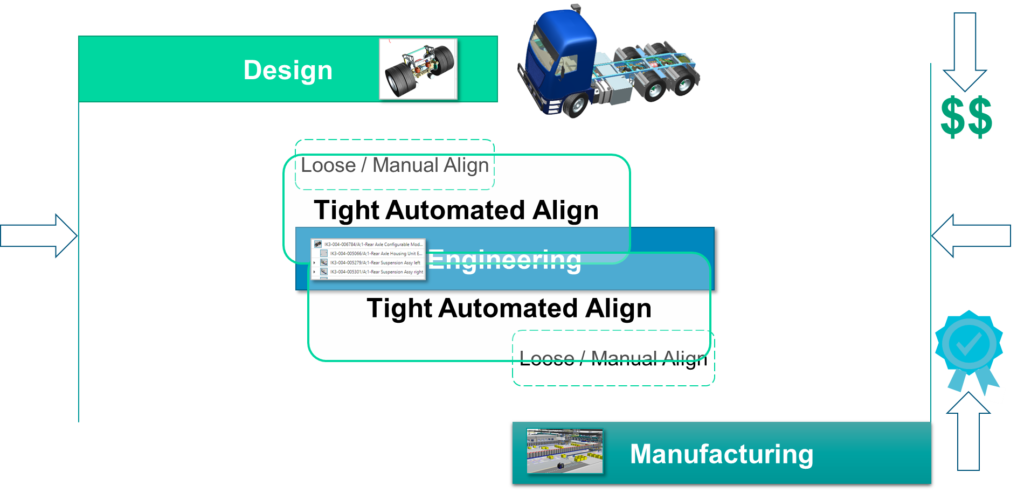
However, achieving the things I mentioned above implies keeping two separate evolving structures in synch with alignment. For even mildly complex products, this is a difficult task that requires a heavy administrative overhead and often is unattainable.
CAD BOM/design to EBOM alignment is a crucial underpinning for achieving high concurrency between design, engineering, and manufacturing domains where alignment provides the needed dependency among the different disciplines while allowing each part with its own set of data and processes to mature at its own pace.
There are only incremental improvements to reduced process time, increased quality, and decreased costs with loose and manual alignment. However, with automated alignment, a company can realize significant time collapse in the product engineering process, improve the quality of deliverables, and reduce development costs.
What is Teamcenter Design EBOM Alignment?
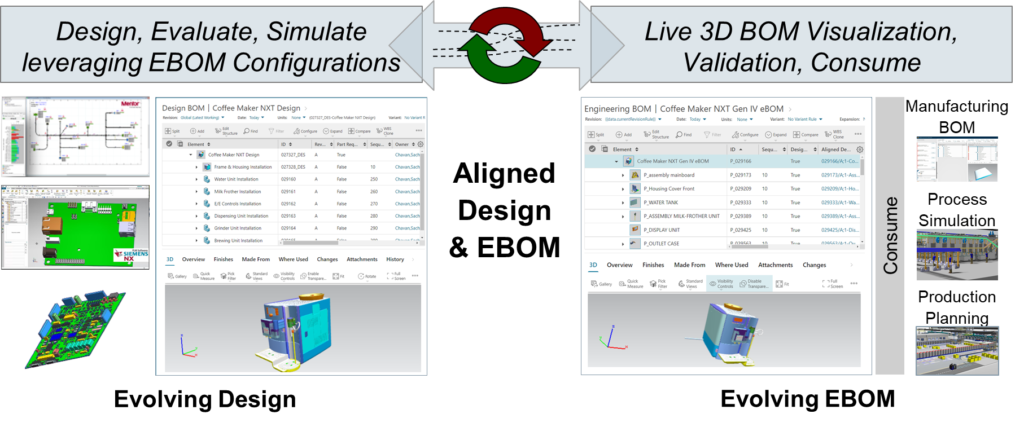
Most customers have also expressed a strong desire to keep their design and EBOM in a single system to get a richer, more complete view of how a design can potentially impact engineering and manufacturing.
This will enable customers to manage an overall change process that incorporates design and engineering changes and even downstream to manufacturing.
Engineers would gain the ability to visualize their product configurations with real-time design data, enabling a collapse in collaboration time between design and engineering.
Design EBOM alignment product helps enable the digital thread by auto-aligning the design structure with the engineering BOM throughout the product lifecycle, supporting engineers with auto-generation designs, parts, and structures, design through engineering product traceability, and 3D EBOM visualization.
Design EBOM alignment provides:
- Aligned multi-domain data (mechanical, electrical, software) in separate but coordinated EBOM and design structures.
- Interactive design and EBOM alignment authoring supplemented with visual accountability checks, embedded 3D BOM visualization, and cross probing support.
- Automated alignment of BOM generation capabilities that are executable using configurable workflows.
- Visibility from design through engineering to improve impact analyses and change management.
Digital Product Management with CAD BOM Separation
To conclude, CAD BOM separation is needed to manage complex digital products, and alignment between CAD and EBOM is crucial for achieving concurrency between design, engineering, manufacturing domains. However, there is a need to remove the overhead of authoring and maintaining the alignment throughout the product lifecycle. This is best addressed through system-aided automated alignment authoring and updates that our Design EBOM alignment product brings to the table.
If you’d like to see and learn more about how going CAD BOM Separation check out these articles as well:
Computer-Aided Design Articles
Comments
Leave a Reply
You must be logged in to post a comment.
Guys, can’t we explain this a bit more simple please?
My only take from this is: ‘wow, complicated stuff, danger ahead’
my 2 cents….