How a service knowledge management system fills in the blanks (Part 3)
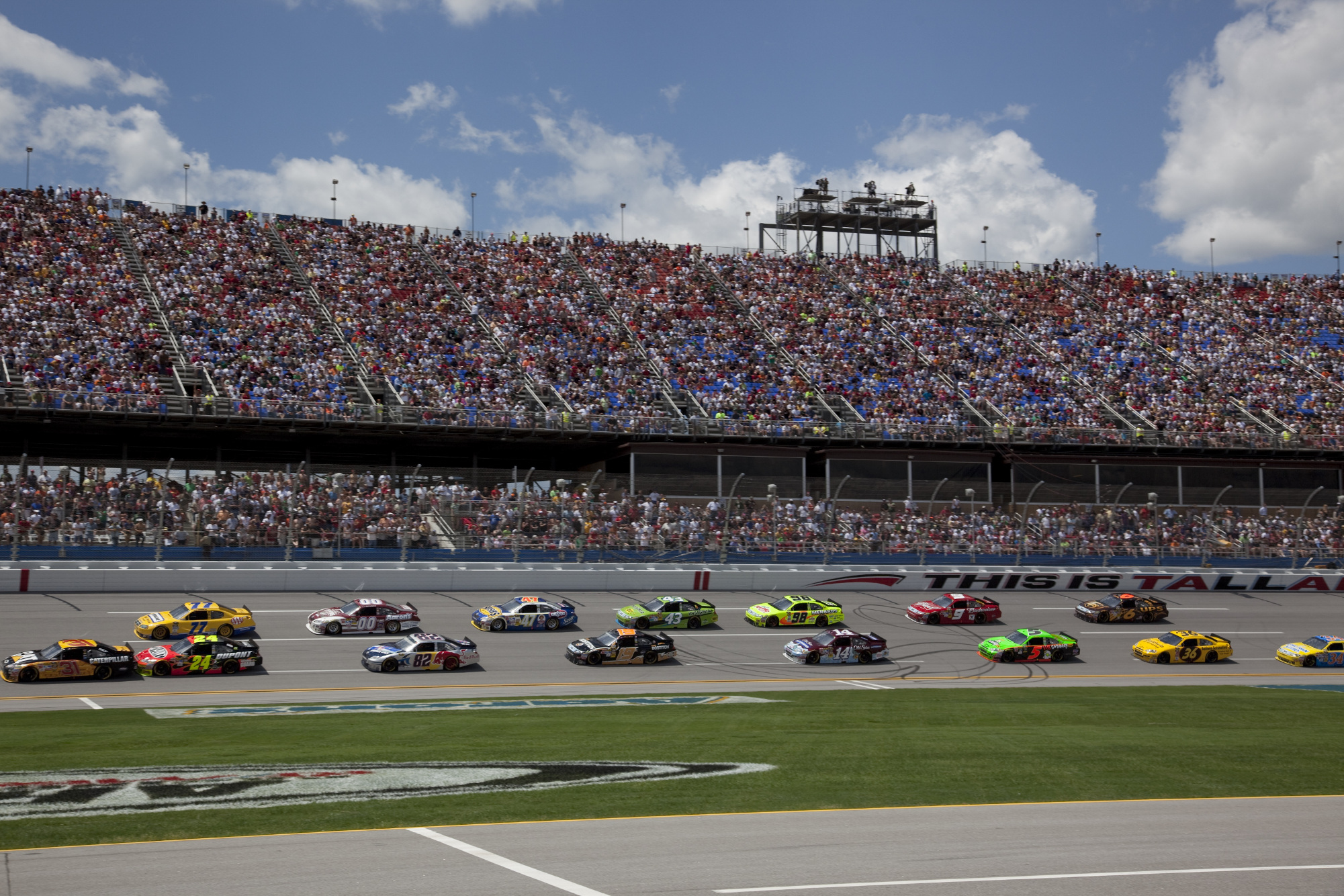
IoT and Big Data require service knowledge management to complete the understanding of product to succeed at service.
Connected products seem new, but they’ve been around for a while. Vending machines send inventory information via the Internet or cellular networks to report what sold and what needs to be restocked. Other products, such as machines on a factory floor or jet engines, can send thousands of bytes of data in minutes.
These sensors send lots of information from the field. This information is great for the future product design, but what about today? Important information can still be missing that helps customers to address operational issues now through actionable, smart data. This is why they need a service knowledge management system.
In this series, Steve O’Lear has explored why companies need these systems in their overall service lifecycle management plans. In part one, he discussed how these systems help customers maximize their investments. In part two, he used the repair of a deep sea oil rig pump to explain how this system benefits service teams. Here, he explains how these systems allow customers to observe trends and how these systems help automotive industry customers.
Use service knowledge management systems to observe trends
We’ve already seen how a service knowledge management system helps service teams when we don’t immediately identify problems. But what if we catch trending failures early with the Internet of Things (IoT) and Big Data?
Let’s go back to our deep sea oil rig pump. We monitor the pump and analyze sensor data for trends. Someone notices vibration readings trending toward their limits and flow is down. We may have options beyond just shutting down until repair. We could run the pump to the point of failure as we did in our previous example and produce nothing. Or, we could adjust the pump’s production rate and wait until we can take it offline at a less disruptive time.
If we have the configuration information on parts, software and operational parameters in our PLM-based service knowledge management system, we also know that the pump can run at a lower production rate where vibrations and temperatures drop off, extending the pump’s life. We have this information because we simulated and tested the pump with different parameters and production levels during design and development. This information is in our service knowledge base as part of our digital twin for the pump.
With that knowledge, we decide to use the pump at a lower rate to extend production until the repair. Pumping 200 barrels per day is better than no barrels, so we download the modified operating parameters into the pump’s controller and reduce its production rate. In the meantime, the service team makes sure it has the right parts for repairs. The team works with the customer to decide the best downtime. If the customer has a number of similar pumps under service contracts, the team may use the service knowledge management system to see if those pumps are similarly configured and service those as well. The team can ask the best questions to plan the service. If the bearing is failing, is it from a specific lot from a specific vendor? Where else is that lot installed? Have we seen problems with these other installations? Should we do preemptive service to avoid a possible failure?
This is why this service knowledge management system is so important for repairs. When we send the team to fix the pump, it could cost more than $100,000 just to get them to the rig. If the team doesn’t go with the right parts, the right tools or the right documentation, it’s a wasted trip, and the customers still has degraded or no production. Having access to the service knowledge containing all of the pump’s information helps the team quickly and efficiently do its job and helps the customer maximize revenue. With the service history for all pumps, the manufacturer or service provider can determine what works better than expected, adjust service cycles, understand what’s failing and the corrective actions to take in design, manufacturing and service.
Before you get to the track you need a service knowledge management system to handle all the data about your product to keep it winning.
Automotive service knowledge management systems
The oil rig pump is just one example in one industry, but other industries benefit from having this service knowledge management system to enhance IoT and Big Data. Let’s take automobiles – specifically, race cars. A company builds and leases more than 700 engines per year to NASCAR racing teams as well as the engines in its own racing teams. The company has simulated and physically tested its engine designs and developed performance and lifecycle information about every part in the engine. When it builds an engine for its own use or for a customer, it knows important information such as the supplier, lot number, how much usage the part has on it, whether it’s new or whether it’s slightly used but good for another race. When the company puts the engine in a car on the track for testing, it records information about the track, the car, the engine configuration and how the car and engine performance.
The detective work begins if an engine fails. The company uses the service knowledge management system to examine the part’s entire history, from its raw materials to when it was installed. The company looks at the design, the supplier and the manufacturing process. If it finds a problem, it takes action. If the part’s inventory came from the same supplier and same lot, the company will quarantine the parts. It will look for other engines with the same lot part that may be suspect and replace the part before it fails.
Why all of this action? There’s no time for failure once the green flag waves and the race starts. But the data the company uses here isn’t part of Big Data and the IoT. It’s part of the service knowledge management system that provides part configuration and the physical product’s history.
This concludes part three of our series on how to use smart data for smart service. In part four, Steve O’Lear discusses service lifecycle management systems in the aerospace industry. Stay tuned.
About the author Steve O’Lear has been in the information system industry for more than 35 years. He has held positions in consulting, services management, sales and marketing across computer hardware, timesharing services (cloud), supercomputing and custom information management solutions in various industry segments. He has more recently focused on PDM and PLM, and many of his customer engagements have been in the A&D industry and with discrete manufacturers. He is currently focused on product marketing for solutions related to document management and service lifecycle management. Early in his career, Steve recognized the need for manufacturers to manage product development data and processes more holistically and became involved with the development, implementation and marketing of PDM solutions. He has also recognized this need with PLM and is now promoting the importance of the support phase in the product lifecycle as products become platforms for service for manufacturers.