Streamline heavy equipment design for customization
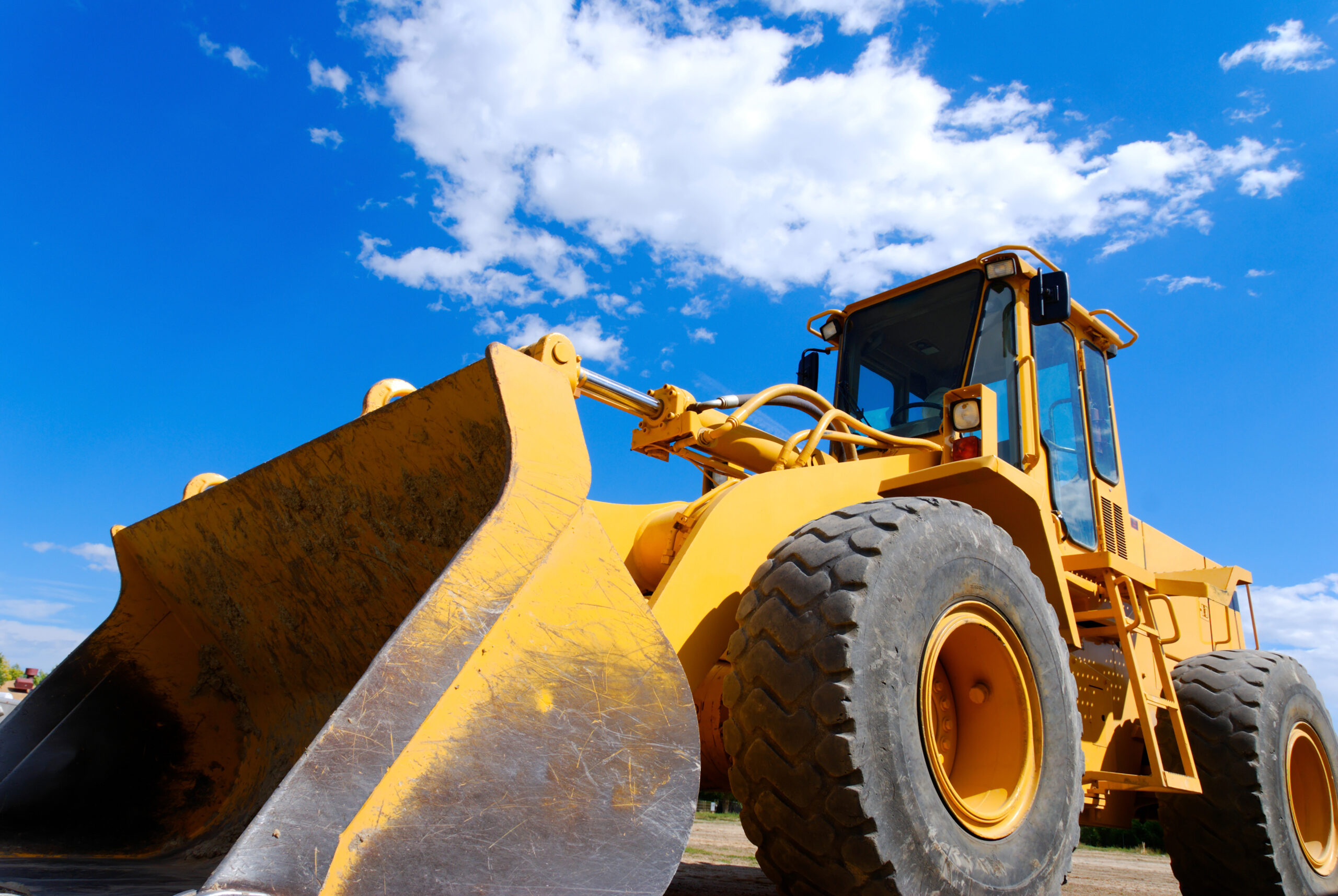
The landscape of heavy equipment manufacturing is evolving, with increasing demand for customized solutions driven by specialization and customer preferences. Accelerating heavy equipment design to meet these demands means manufacturers are turning to innovative approaches like product lifecycle management (PLM) systems to stay competitive.
Challenges of heavy equipment customization
- Longevity and adaptability: Heavy equipment often operates for decades, necessitating frequent upgrades and retrofits. Compatibility between OEM configurations and service upgrades is crucial, leading to field adjustments.
- Retrofitting for connectivity: The rise of connected and autonomous fleets requires retrofitting field equipment for compatibility, ranging from simple fixes to complex component replacements.
- Globalization complexities: Designing equipment for diverse markets presents challenges due to regional differences. OEMs must navigate decisions on assembly locations and parts sourcing.
- Knowledge management for customization: Delivering customized products efficiently requires effective knowledge management to align with customer specifications and engineering standards.
PLM-based heavy equipment variability management approaches
To stay competitive and profitable, heavy equipment manufacturers with highly configurable product lines are seeking flexible, scalable platforms that can help them deliver more product variants, drive commonality and re-use, and integrate with their overall product development process and business systems. These are the primary variability management approaches that manufacturers deploy:
Configure-to-Order (CTO): Based on design selection at the time of order, maximizing re-use of existing parts and components. Heavy equipment manufacturer JCB has used a CTO approach to manage their 200,000+ possible product variations. Check out the JCB case study for more details.
In the above video, you can see how Teamcenter Product Configurator’s intuitive and simple UI helps users manage configured products and create custom variants. Drawing from a single repository, all product variability data is externalized from the structure. The user can easily create and filter variant conditions for a structure within a grid-based view, then visually configure the product based on these established rules.
Engineer-to-Order (ETO): Involves design creation at the time of order, aligning complex products with detailed customer specifications. Companies like Mitsubishi Heavy Industries have utilized the ETO approach to deliver unique specifications to their customers.
This video shows a sales configuration management workflow using Siemens’ ETO solution, Rulestream. You can manage multiple configuration domains under the same solution, which helps streamline processing and enables reuse of customized products and best practices. The solution allows you to select from a list of sellable configurations and visualize it in 3D, retrieve the costs for the customized product from ERP, and automatically generate a custom quote.
Hybrid CTO/ETO Process Environments: Many products have elements of both approaches, requiring integrated solutions to drive and support variability management.
Best-practices for heavy equipment variability management
CTO and ETO variability management can help companies address a variety of fundamental business needs. Below, you’ll find a list of common business needs and how CTO/ETO help address those needs.
- Respond to customer preferences: Establish a central repository for all product variability data and use automation to capture engineering rules efficiently.
- Manage complexity of multi-domain systems: Provide a single, consistent definition of variability across all domains and offer change control for effective product features.
- Offer product variety without driving up costs: Drive part re-use, prevent duplication, and automate creation of fixed assemblies.
- Visualize specific customer orders: Generate 100 percent buildable end products and streamline visual validation of configurations.
Teamcenter helps customers define and manage their product variability under a single integrated definition, allowing them to implement these best practices. Ultimately, this common digital variability infrastructure helps them reduce costs and increase efficiencies, regardless of the degree of customization.
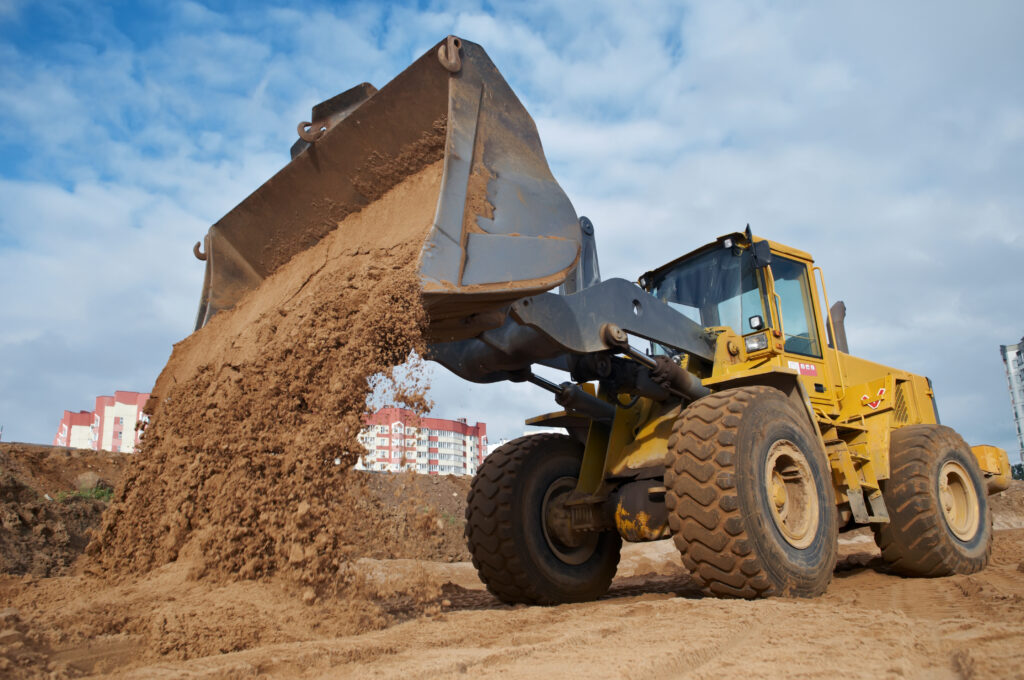
Accelerate heavy equipment design
Accelerating heavy equipment design is mandatory to deliver the complex, customized products your customers demand today.
When you start from the early stages of design with an integrated multidisciplinary design approach, you can more effectively meet all requirements and deliver what your customers demand faster at a lower cost. Take control of your heavy equipment design process with fully integrated solutions. Our comprehensive end-to-end integrated solution helps break down silos by connecting teams and tools. Reduce time to market while improving quality and meeting regulations.
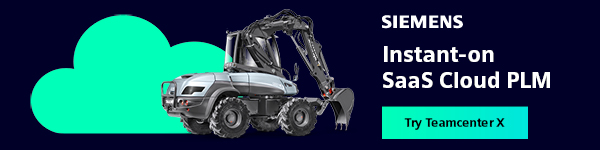
Check out more related heavy equipment content on this topic:
- Video: Rethinking variability management for heavy equipment
- On-demand webinar: Overcome product variability challenges with PLM software
- White paper: Managing variability with heavy equipment PLM software
No matter how you choose to deploy Teamcenter,
you get the same proven solutions designed to help you innovate faster.