The power of integrated product cost and carbon analysis in the automotive industry
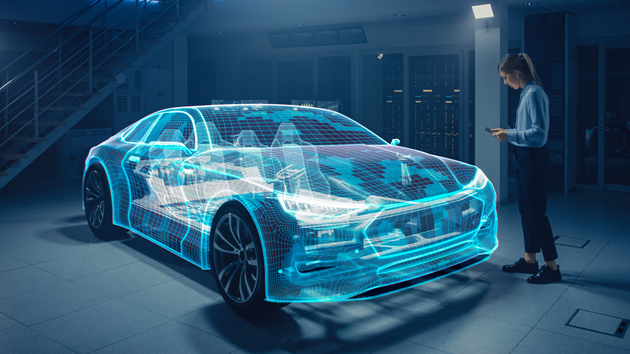
Alternative drives and fuels, such as e-fuels, are poised to play a pivotal role in meeting the goal of climate-neutral transport by 2050. By reducing carbon emissions across vehicle fleets, these innovative technologies offer a critical avenue for enhancing climate protection in transport.
As the automotive sector transitions to alternative drive technologies that leverage renewable energy sources—whether through electricity, hydrogen, or synthetic fuels—the carbon emission hotspot is expected to shift from the usage phase to the production and material upstream chain of vehicles (this blog focuses on passenger cars). This shift is particularly pronounced due to the vast network of up to 7,000 individual components and parts found in each vehicle. This trend is even more apparent for electric vehicles (EVs): EVs often carry a higher carbon footprint during production than conventional vehicles. The primary driver of this increased footprint is the carbon-intensive processes involved in manufacturing batteries and sourcing their raw materials.
Amid this transformation, using secondary materials derived from recycling is becoming increasingly crucial. By prioritizing materials with a lower carbon impact than their primary counterparts, industries can further reduce emissions. This strategy is especially relevant for aluminum and steel, given their significant mass contributions to vehicles and the potential for substantial reductions in production-related carbon emissions through more sustainable, recycled alternatives. The automotive industry’s strategy to reduce its carbon footprint goes far beyond the product’s usage phase and considers the entire life cycle of a vehicle, from raw materials to production and recycling (see Figure).
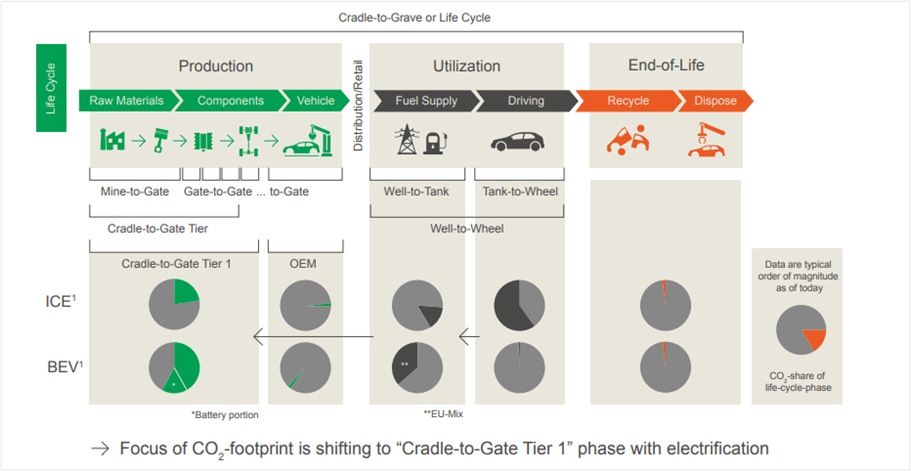
Source: CLEPA European Association of Automotive Suppliers
(1) CLEPA estimate based on https://www.volvocars.com/images/v/-/media/market-assets/intl/applications/dotcom/pdf/c40/volvo-c40-recharge-lca-report.pdf
Scope 3 carbon emissions usually make up the largest share of a company’s carbon footprint, the so-called corporate carbon footprint, and arise from upstream and downstream activities along the value chain, such as the transport and distribution of goods and services or the disposal of products by the end consumer. Other sources of Scope 3 carbon emissions are the extraction and production of purchased raw materials and the use of sold products and services. Original Equipment Manufacturers (OEMs) of the time have recognized all these aspects and are driving carbon reduction into their supply chain. But how exactly can the carbon footprint of car manufacturing be reduced?
OEM perspective: Supply chain transparency
OEMs set sustainability criteria as part of their procurement and supply chain management strategies. Contracts often require suppliers to provide environmental data and demonstrate carbon footprint reductions to align with the OEM’s broader sustainability targets and commitments to carbon neutrality.
Supplier perspective: Cradle-to-gate approach
Tier 1 and Tier 2 suppliers often operate within the framework of a cradle-to-gate approach, focusing on evaluating and minimizing the environmental impacts of their production processes. This assessment considers the impacts of sourcing and processing raw materials up to the point when their components or systems are delivered to OEMs. The adoption of this approach is typically driven by the need to meet stringent OEM requirements and align with broader industry sustainability goals.
Driving efficiency and collaboration early in product development
Profitability and sustainability are closely linked, as regulations like carbon taxes e.g., due to the EU’s Carbon Border Adjustment Mechanism (CBAM) tie environmental impact directly to costs. So, stakeholders involved in product development are currently grappling with significant productivity pressures. These challenges stem from the need for sustainable and profitable company growth amid escalating cost pressures and the rapid pace of innovation. So, they need to balance sustainability goals with costs early in the product development phase.
The challenge many automotive companies face is their processes do not provide end-to-end visibility of cost and sustainability data and control of that information across the extended enterprise. These disconnects in the value chain from early conceptual, design, cost, value engineering, procurements, logistics, manufacturing, upper management, suppliers, partners, and vendors create a lack of transparency and act as a barrier to making the right decisions on both cost and sustainability.
To stay competitive and sustainable, automotive manufacturers must evolve beyond isolated approaches to cost and carbon footprint calculations in early product development. Instead, they need to adopt a highly integrated solution. In a digitally driven landscape, companies that aim to streamline their operations for agility and accuracy will find integrated simulations of cost and carbon footprint essential for responsive and informed decision-making.
An integrated approach for calculating cost and carbon footprint is critical to accelerating this transition as it enables companies to reduce their product carbon footprint and design sustainability into their product, thus eliminating waste decarbonizing their products, and identifying the factors that affect costs, risk, and carbon emissions.
Embracing an integrated solution for cost and carbon management in product development
A sophisticated, integrative solution like Teamcenter Product Cost Management offers an end-to-end calculation of costs and carbon footprint for products and tools which is vital for understanding the product profitability. The solution stands out with its real-time scenario analysis, helping companies simulate design, material, manufacturing options, batch sizes, and location scenarios in the earliest stages of product development. Such analysis can support sourcing decisions that optimize costs and carbon emission impacts. The solution’s strength lies in its seamless integration with other Siemens Digital Industries Software and third-party solutions, enabling a true digital thread.
The solution aligns cost and carbon footprint data dynamically with the evolving bill-of-material (BOM) across every phase—from concept through development and validation, right up to the start of production. By aligning the BOM with updates from Product Lifecycle Management (PLM) and Enterprise Resource Planning (ERP) systems, teams can monitor every change in specifications and costs seamlessly. This capability is invaluable, particularly in complex industries like automotive, enabling a digital thread that spans engineering, procurement, and finance. Moreover, integration with solutions for manufacturing process planning enables automated cost calculations, where BOM updates and corresponding work plans from manufacturing systems are harmonized. This reduces manual data handling, as costs can be calculated quickly and precisely, allowing teams to track and analyze cost and carbon impacts efficiently.
These integrations must encompass the entire BOM, facilitating collaboration across all stakeholders throughout development. Today, cost engineers in purchasing departments typically work in siloed systems, calculating the costs of specific parts without referencing the full product BOM. While they assess purchased parts—such as individual gears from a supplier—these parts exist on the same BOM as the final assembled product (e.g., a vehicle or gearbox). To future-proof digital strategies, organizations must shift toward a software solution that allows for dynamic, BOM-wide calculations at each stage of product development.
An early-stage assessment of carbon impacts in Teamcenter Product Cost Management provides critical insights, enabling cost engineers to consider supplier-side supply chain emissions. The integrated benchmark data includes information on cost and carbon footprint such as labor costs, physical data for common materials, used for cycle time calculation, and material prices. Machines for standard manufacturing technologies with technical and commercial data, pre-configured reference processes for numerous manufacturing technologies including data for battery cells and battery modules. Benchmark data on carbon emission for common materials, semi-finished materials, and energies for different countries. The solution allows users to simulate scenarios across variables—such as manufacturing location, material choice, and transportation mode—empowering businesses to make optimal sourcing decisions early in the product lifecycle. This ability to model environmental impacts early, even before suppliers finalize logistics or production parameters, uniquely positions Teamcenter Product Cost Management as a decision-support tool that informs discussions with suppliers to achieve lower emissions and optimize costs.
This is increasingly critical as companies face regulatory and consumer pressure to reduce their environmental impact. For instance, sourcing components from closer regions, rather than overseas suppliers, can significantly lower carbon emissions associated with transport. Connections with Siemens Digital Logistics support transport simulations, while the connection to Supplyframe provides instant access to cost and carbon data for electronic components. As electromechanical components are adopted, this connectivity is an asset, allowing users to evaluate material and sourcing changes efficiently and holistically.
Driving future-focused decisions
In the rapidly evolving landscape of the automotive industry, staying competitive requires more than just innovative designs and cutting-edge technology. Amidst fierce competition, fluctuating market demands, and increasing regulatory pressures, the importance of cost optimization has never been more critical. This is not just about slashing expenses; it’s about smartly managing and reducing product costs to enhance profitability without compromising on quality or customer satisfaction. In an era where agility, accuracy, and sustainability determine market leaders, a solution like Teamcenter Product Cost Management offers a decisive advantage, enabling businesses to calculate, track, and optimize both costs and carbon footprints holistically and automatically.