Ramp-up production faster: extend PLM with manufacturing planning solutions
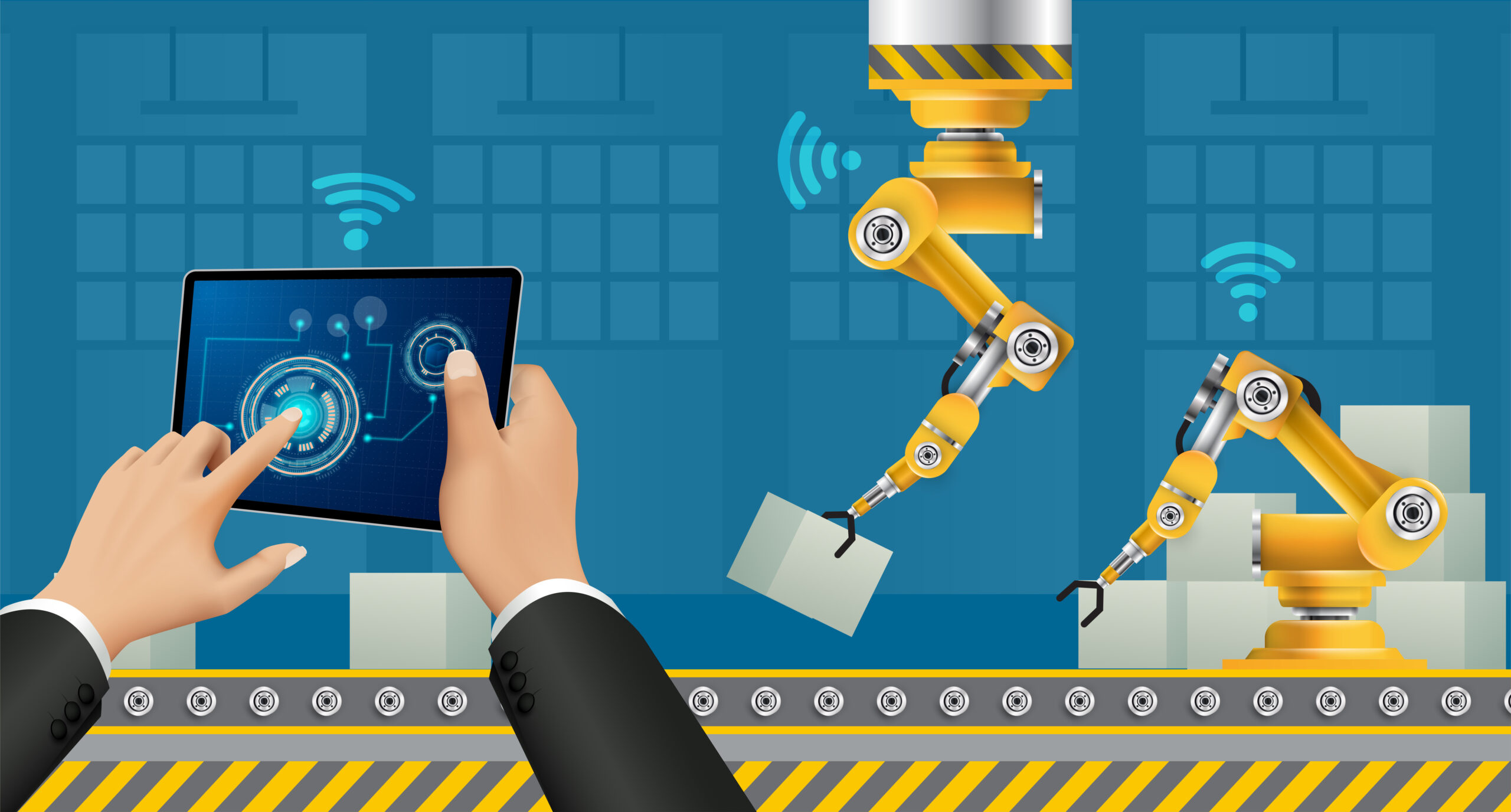
Thinking about adding manufacturing planning to your PLM-based digital enterprise? Read on to add more pros to your list!
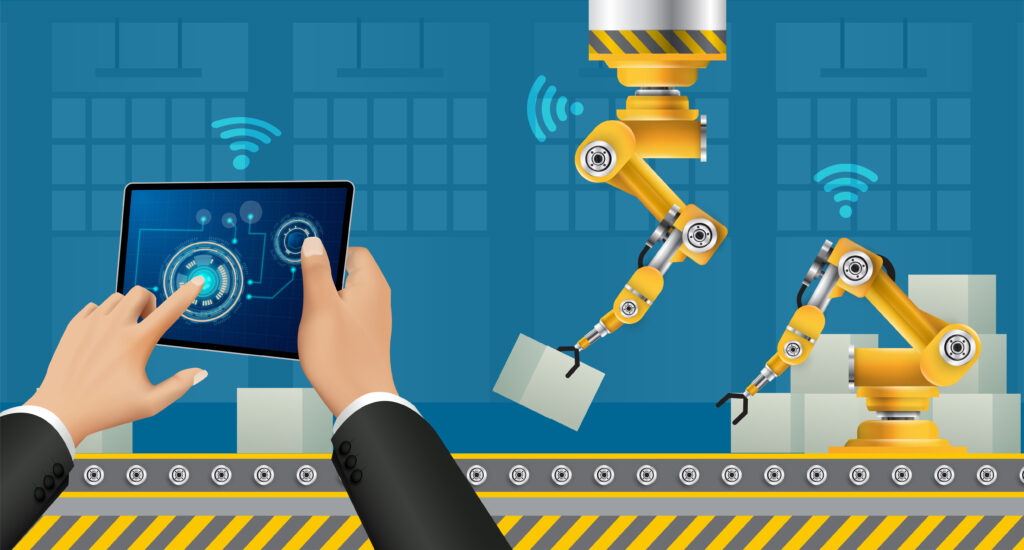
Working in data silos with sub-optimized processes between functional domains typically creates significant data redundancies that lead to costly mistakes, poor product quality, and delayed time to market. A platform that captures product and manufacturing planning data across the lifecycle and enables a digital thread for collaboration between design, manufacturing, and service domains – will help to reduce the risk of costly issues, improve product quality, and get products to market faster.
By 2028, 80% of digital threads will start with PLM, with increased investments to adapt PLM as a digital thread foundation platform, up from 45% today.
-Gartner®
Why extend the digital thread to manufacturing planning?
With a PLM backbone for your manufacturing planning processes, you can shift left your planning activities to start earlier in the lifecycle of the product. Why? Planning for your manufacturing and assembly processes, leveraging knowledge from the product lifecycle will reduce risk of production issues later on in the process. You also have the ability to capture, share, and reuse knowledge across functions and locations. This can help eliminate wasted time and effort trying to recreate or locate necessary information and allow for more efficient development of new manufacturing processes. Benefits of including manufacturing as part of the digital thread include:
- Robust early collaboration between design and manufacturing for proposal development and New Product Introduction (NPI)
- Rapid production ramp up leveraging standard templates and practices that streamlines delivery of accurate and validated data to the shop floor
- Real-time access to product data, importance of product data release status, such as work in progress, or approved to production, change management, internal and external and horizontal collaboration and reuse of best manufacturing practices
- Accurate and controlled information flow up stream (engineering) and downstream (production)
- Global insight into manufacturing planning, modifications, additions, or exchanges between production in different regions and plants
- Online view of the work instructions data that is always up to date, this ensures a higher level of trust from the shop floor and increased quality
- A foundation to digitalization of manufacturing with a proven and stable platform from which to grow
- Support changes more efficiently, where the cost of change is lower and so is the investment
Digital threads connecting design to manufacturing
The digital twin is at the heart of any smart manufacturing strategy used from design to new product introduction (NPI) to plan for, simulate, predict, and optimize the product’s build quality and the efficacy of the production system building it. Digital threads connect manufacturing data and processes to design engineering early-on in the product lifecycle to ensure quality manufacturing process planning. The process plans are then validated using simulation solutions. The digital threads provide a controlled and consistent data feed to stakeholders in different domains across the digital enterprise, from design to manufacturing to production operations.
Siemens digital manufacturing solutions enable you to collaboratively create, validate and optimize manufacturing information, such as the manufacturing bill-of-materials (MBOM) and bill-of-process (BOP), concurrently with product design. By providing a common environment for multiple disciplines that share the same requirements, users can easily author and navigate multiple views from a common structure and leverage automated tools to compare and validate information structures. This also provides consistent ways to deal with revisions and versioning and enables users to view and validate re-use of costly production assets across multiple programs.
Shorten ramp-up time with closed-loop connected manufacturing
Ultimately, we have this one point of truth. Our digital factory solution based on Siemens software is the right way forward for BSH, especially because our overall goal is closed-loop manufacturing.
– Philipp Winter, BSH
BSH Home Appliances is a global leader in their industry. The company’s portfolio includes well-known appliance brands like Bosch, Siemens, Gaggenau and Neff as well as the ecosystem Home Connect and service brands like Kitchen Stories. BSH is represented in some 50 countries and is a Bosch Group company.
Thanks to the Siemens Xcelerator business platform, including the Teamcenter product lifecycle management (PLM) backbone and Siemens digital manufacturing solutions, product development at BSH is directly linked to manufacturing. All BSH designers, development engineers, procurement specialists, planners and industrial engineers in the plants can access the same data and assembly trees via Teamcenter.
Currently, local industrial engineers and planners have access to tools for Teamcenter Easy Plan, Tecnomatix Process Simulate, and NX Line Designer. These tools allow BSH to organize and optimize production lines for maximum performance for globally distributed plants, complex product variation schemes, line balancing, productivity and production efficiency, human health and safety issues, robotics and even collaborative robots (cobotics). They have also enabled BHS industrial engineers to shorten their ramp up time by 33 percent.
“We have leveraged digital manufacturing solutions from the Siemens Xcelerator business platform for many years. This has resulted in an accurate digital twin of our factory ecosystem. Now we have added Easy Plan, which is our latest planning software, to do our line balancing and all our time management on the production lines.”
Teamcenter Easy Plan features an award-winning user experience (UX) for complex manufacturing process planning. It is an open, web-based software solution that as its name suggests, is designed to be easy to use. Production supervisors, line planners and operators across global BSH plants can access critical data in Teamcenter via a task-based interface from a mobile device, tablet or on a touchscreen on the production line. With a click of a button, users can easily change between tasks from high-level planning to line balancing and work-instruction authoring.
Learn more about connected PLM-based manufacturing planning
Check out Teamcenter Easy Plan with a free 30 day trial
Explore our integrated manufacturing solutions
Gartner, How CIOs Can Use PLM to Generate Value From Digital Threads, Sudip Pattanayak, 13 February 2024.
GARTNER is a registered trademark and service mark of Gartner, Inc. and/or its affiliates in the U.S. and internationally and is used herein with permission. All rights reserved.