The Secret Language of Surface Design
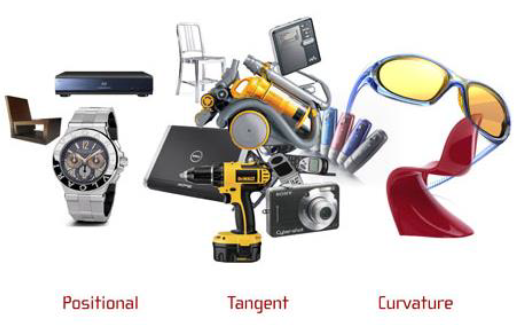
Dan Staples asked me to call some attention to a surfacing presentation that was made at Solid Edge University 2013 by a French company called SEB. SEB designs and manufactures a lot of small appliances that you probably use in your home.
This type of consumer product is notoriously difficult to model correctly. Their presentation was called “The Secret Language of Surface and Meaning in Product Design, and talks about some of the techniques used to get the curvature transitions correct.
This image of a link is a great demonstration of various types of curvature continuity used in many types of design. It’s not just visual, there are often functional specifications that require this type of approach. There are a lot of mechanical advantages to smothing sharp corners including safety, weight/strength optimization, elimination of stress concentrations, ease of cleaning, aero/hydrodynamics, and so on. I believe that as CAD tools become more and more powerful in the area of organic shapes, we are going to see a transformation in a lot of machine design.
Where straight manufacturing (CNC) costs are not the driving concern, I think we will see more and more machine components start to specify more optimized shapes. Other manufacturing methods are able to produce organic shapes for the same or even less cost as prismatic shapes (forging, casting, molding, powder metal, 3d print).
A sharp edge, depicted in the body on the left is said to have “contact” or “positional” continuity. That is, the face on one side of the edge contacts the face on the other side of the edge. The center body has a simple round or fillet, and is said to have tangent continuity, which in English means that the curvature continues from one face, through the round, to the other face. There is no sudden break in the tangency. The example on the right shows curvature continuity. This means that the curvature changes gradually as one face blends to the other. A normal round has constant curvature, so it takes either a special round type or a special technique to create a blend between two faces in this way.
Evaluation of this type of surface is usually done visually, using lights or reflective backgrounds. The “zebra stripes” shown above are really just the part being evaluated made perfectly reflective, and put inside a box painted with black and white stripes. Like looking at the side of a beautifully curvy automobile, you can see any imperfections as unterruptions in the reflections.
Whether you’re aware of the language used or not, products that are made with these concepts are around you every day.
The real question here is whether Solid Edge is able to handle this kind of design. With the new capabilities added to the blue surf, and curves, Solid Edge can give you C2 continuity where ever you need it.
SEB has been demonstrating this type of design in their real world products for years now.
I worked in this kind of design for many years before joining Solid Edge. I can tell you that the handle shown to the right is much more difficult than it looks to get correct. Part of the reason is that the parting line for molding is designed right into the part from the beginning, not added after the design was complete. Models like this usually happen in two steps – one to just get the overall shape, and produce the parting line from the overall shape, and then a real manufacturing model that starts from the parting line, and makes everything else fit.
A PDF of SEB’s original powerpoint presentation is attached to this article.