New connector design improves robustness and flexibility for a modular robot system
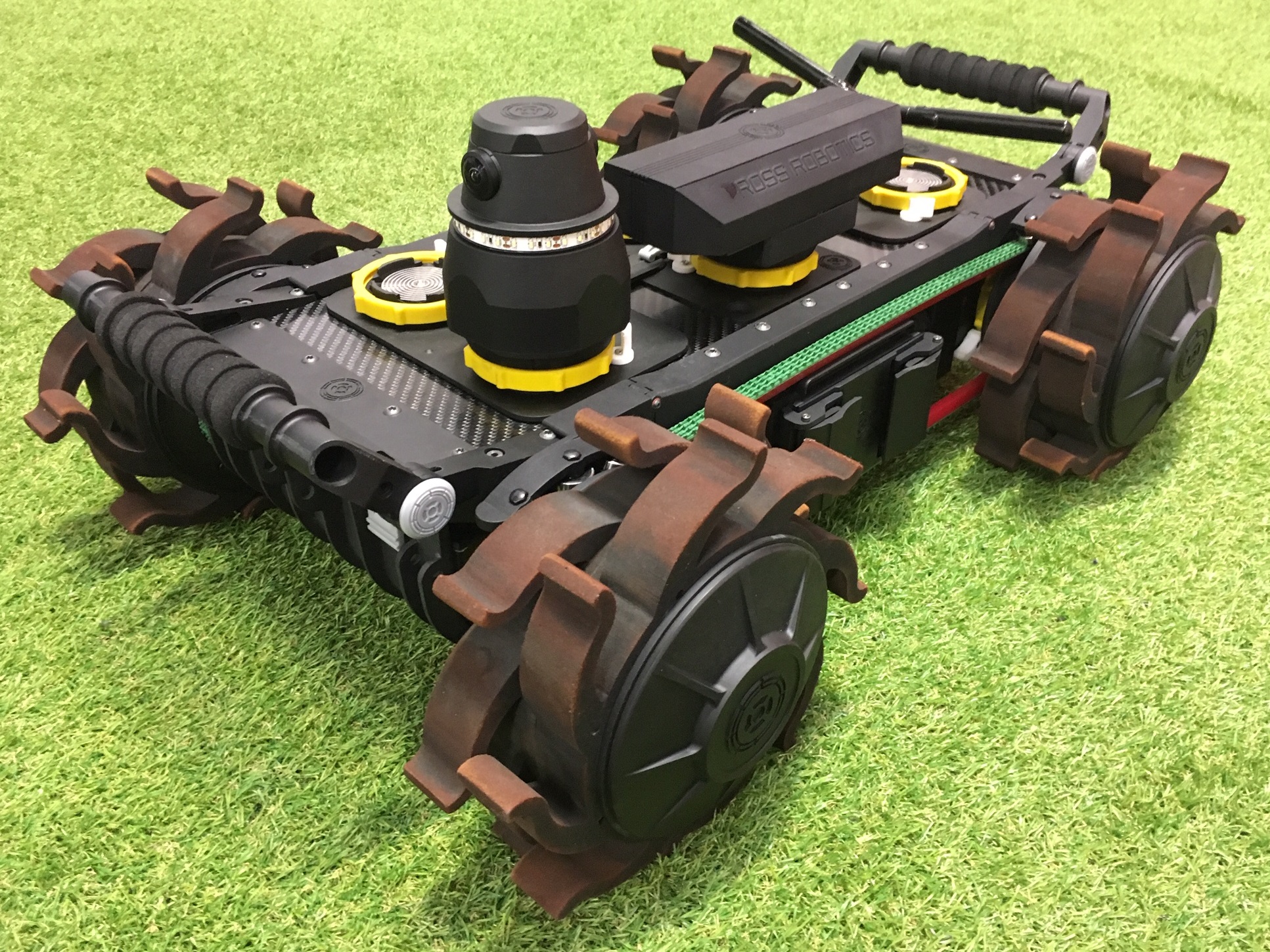
Ross Robotics in the UK is a fast-growing developer of modular robots that are used for inspection and maintenance operations in a variety of industries. In a recent interview with Philip Norman, co-founder and director of research and development, we discussed their development of a new type of connector. Philip describes the challenge they faced: ”We needed a means of connecting robot modules to one another that would provide both a robust physical connection and reliable power and data connectivity. Our robots are made up of modules that can be reconfigured to make different types of robot to perform different tasks, so the connector between the robot modules is a critical design feature.”
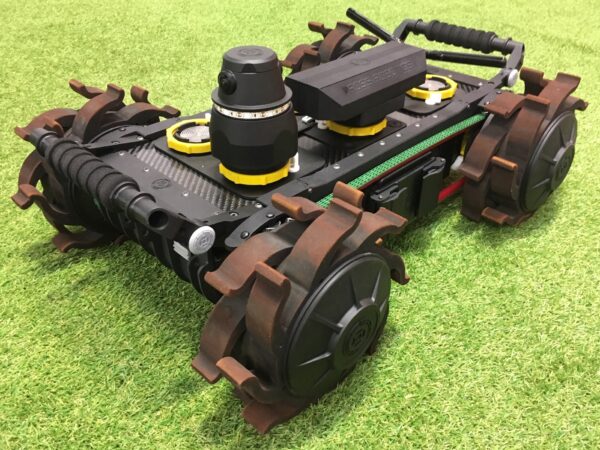
Some of the requirements for the connector include:
- Simple operation with no tools required
- Ability to reposition rotationally
- Support power transmission rates of 20 Amps continuous, 60 Amps transient
- Reliable transmission of data with no loss of packets
- Non-magnetic (no ferromagnetic components)
- Extremely low mass penalty
- Small form factor (ideally 50mm diameter and shallow, with a maximum depth of 9mm)
- Designed for manufacturing at a low cost
- Easily modifiable to suit a range of specific requirements
One interesting thing I learned in my conversation with Philip is that reliability is a major issue for robots that are deployed to perform a variety of tasks, often in uncontrolled environments. “We have seen data that showed a mean time between failures of just 30 minutes for some robot deployments. We spend a lot of time thinking about the robustness of our systems and building in redundancies and support for self-healing. For example, if a single drive motor fails the robot can still maneuver and perform necessary tasks.” The connector is a prime example of a design challenge where reliability and robustness are major considerations.
Elegant design solution and manufacturing considerations
Philip has come up with an elegant solution to meet these requirements. The “Slimline” connector is comprised of two discoid plates with coaxial ridges that engage with each other in a cone-to-cone mating configuration. He used Solid Edge 3D CAD software with synchronous technology to precisely model the subtle cone geometries that would ensure reliable transmission of power and data. Philip said, “Synchronous technology enabled me to rapidly experiment with different parameters to find the sweet spot for the cone geometry. Using a history-based modeling system would have made this very onerous, and I probably would have tried fewer options, which would have meant a less thorough exploration of the critical parameters.”
The two halves of the connector are created from just two parts. The total mass is 20gm, and the mated connectors are less than 8mm deep. The connectors are 3D printed, then selectively metallized to produce a sequence of conductors and insulators. The same device conventionally manufactured would require between twenty and thirty separate parts and a lot of assembly. When they move to higher volume production, Philip plans to use injection molding for the manufacturing process.
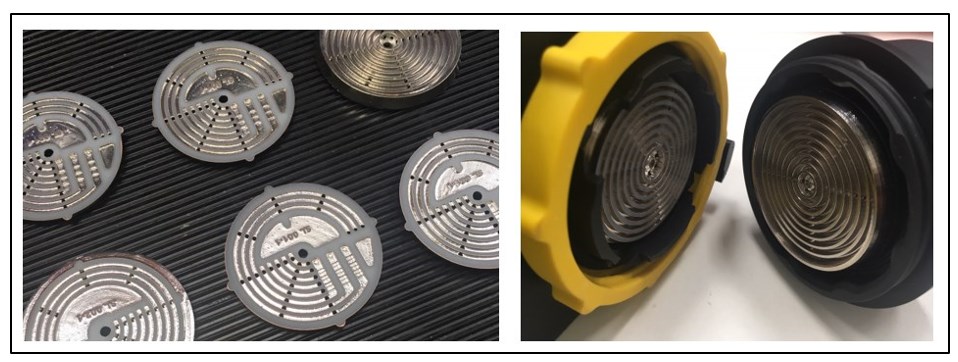
Testing and future plans
The connector has been tested informally to demonstrate that it can carry 20 Amps continuous; it will next go through formal testing. The Slimline connectors are installed with a plug and socket arrangement that ensures a progressive interference fit and an easy locking action using a threaded collar for tool-free connection. Philip has also developed an actuated locking device to support one of the challenging goals of their modular robot system, enabling robots to build robots.
The next steps in the development of the Slimline connector are likely to include using Solid Edge Harness Design software to configure and optimize the connection of wire harnesses to the Slimline connector. A gigabit version of the Slimline connector is also under development and Philip is aware of potential applications in adjacent industries such as oil & gas, nuclear decommissioning and aerospace. In fact anywhere where a lightweight, extremely compact connector is required and especially one which does not require precise alignment before mating.
You can read a complete case study about the design of the Robosynthesis® modular platform using Solid Edge here.
Comments