Majenta Drives Dax Cobra Development with Solid Edge
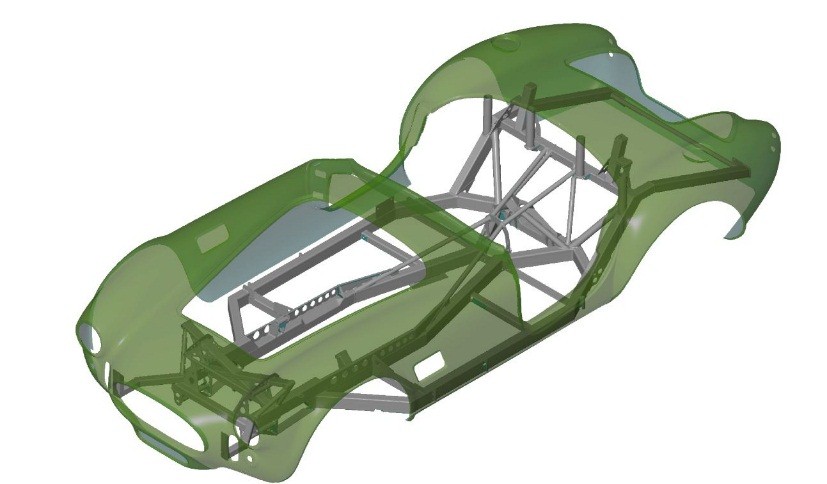
The story of the UK Solid Edge reseller Majenta PLM and the DAX Cobra 427 covers a lot of ground in the mechanical design technology realm. The story is interesting because it uses technology in a way that should encourage those who have been reluctant to start using advanced design tools, and it also showcases some technology that has come a long way in recent years. This story shows a way forward for groups who may have thought that they were so far behind the current technology that they could never catch up.
In the words of Mark Parry, Managing Director of Majenta PLM,
We find that many customers think it’s too late/difficult to start their CAD journey – too many drawings, calcs, metal templates, no skilled staff ready to take on the challenge. We’re not just talking about starting out fresh with CAD on a new project, but to get all the legacy product into the system, especially if they only have one/a few key products and produce variants of that.
DAX is a company that produces a very popular Cobra 427 kit car in the UK. The cars are plainly gorgeous, and meticulously detailed. They have continued to develop the chassis over time. DAX has sold over 4000 kits in the past 30 years, and they also offer turnkey finished vehicles for those who prefer not to get their hands dirty.
While their product has always been superior, the engineering documentation processes consisted of drawers of paper drawings, some missing documents, some of them not in electronic format. In discussing their situation with the pros at Majenta PLM, DAX was considering 3D CAD, but was a little overwhelmed at the thought of recreating all of their engineering data in 3D.
To resolve this, DAX engaged Majenta PLM to deliver Solid Edge format 3D data for their entire Cobra 427, along with training. Majenta employed Solid Edge along with partner products from Keyshot and Quadrispace to fill the need. This catapulted DAX into a front row seat for 21st century engineering technology, solving several problems at once, with the effect of immediately giving DAX all the downstream benefits of 3D data which were previously unavailable to them. Some of these benefits include what-if trials, simulation/analysis, build manuals/animations, photorealistic rendering and the ability to globally source components. Those of us who use 3D on a daily basis sometimes take for granted the number of things you can do with the digital data that we weren’t able to do with just 2D or paper drawings. You cannot
overstate the importance of visualization for both technical and non-technical purposes. People who cannot understand a CAD drawing can more easily relate to a photo-realistic rendering, or even a scaled down 3D print of the entire vehicle or just a single component.
To help them bring DAX into the digital age, Majenta PLM partnered with a CAD customer, Physical Digital. Physical Digital has a rich heritage in the UK auto racing scene, having worked with some of the biggest names in the British auto industry. Physical Digital came into the DAX facility, and in the course of about a day, scanned the Cobra body, cabin interior, chassis, and a majority of the mechanical parts.
The scanning involved a verified high resolution DSLR camera to take a number of images from different positions around the car. This enables the system to capture the position references places around the vehicle. Markers were placed on the car body to act as reference points to match data from multiple scans into a single data set. A GOM ATOS 3D optical scanner was used to capture high density surface measurements. The scanner calculates its position on the vehicle by locating the reference point pattern from the photogrammetry. The result was a highly accurate scan of the 427, inside and out.
3D scanning is an area that is growing with less fanfare than its cousin technology, 3D print. In the past, scanning reflective or transparent materials often created challenges, but using the GOM ATOS triple scan with advanced projection technology this presented much less of an issue and car bodywork was easily scanned without any surface preparation. The hardest part to scan was the glass, however this was easily overcome by applying masking tape to enable easy capture.
Another difficult area of the scan was the internal cabin. This was due to the amount of detail in the environment from the dashboard and instrumentation to the seating and all other leather trim detailing. Materials such as carpet don’t offer a real solid surface to scan, and can also offer challenges.
For the mechanical parts and frame, Solid Edge was used, with the scan data and existing drawings.
Again we hear from Mark Parry:
In one day we scanned a whole car key components including chassis and key components, used the information in most cases as reference to then quickly model the parts. Solid Edge with Synchronous Technology is the easiest and fastest way to take in multiple CAD files and quickly model/modify the data to generate the product, also for the jigs and fixtures if required.
You can just place surfaces over the scan data, but having a real engineering model with CAD-perfect geometry enables you to make clean changes, dimensionable drawings, and more functional assemblies. So even though Physical Digital captured highly accurate data in the scan, sometimes this data was only used for reference, instead of creating CAD models directly from the scan points. Scan data can include small imperfections, and does not result in the mathematically perfect planar or cylindrical surfaces that we are used to working with inside CAD programs. For this reason, a number of data capture methods may be brought together to model some of the mechanical components, including 3D scan data, existing 2D drawings, and even physical measurements with calipers.
An example of this would be the DAX 427 chassis. A complete build was generated in Solid Edge mainly using the Frames functionality working from the scan reference data as well as the original 2D drawings that DAX had provided and some measurements of the physical frame to help verify the CAD data.
Purchased parts have been modeled up in Solid Edge as solid data. This was achieved through referencing scanned information or taking measurements from the purchased parts.
You might not ordinarily associate Greenpower, an electric car build/race competition, with the high octane muscle of Dax and the Cobra 427, but Majenta was able to pull these parties together. Working with the local college, who also use Solid Edge, Majenta held a modeling challenge to help gather the bulk parts. This enabled the students to gain industry modeling and engineering experience, with the winners able to work on the show stand at the Kit Car Show. The link with students is essential to build the ‘engineers of tomorrow’ in working on a real road-going iconic car as well as their involvement in Greenpower. (www.greenpower.co.uk).
Our initial project, an electric car challenge which requires students, guided by their teachers and an industry mentor, to design, build and then race an electric car. Holding events at weekends at major motor circuits around the UK ensures excellent attendance from the general public who can witness the amazing vehicles, focus and team work evident at these events.Since that first event in 1999 Greenpower has expanded significantly and now works with 500 schools and over 8000 students around the UK.
Greenpower International Finals will be held on the 10th – 11th October 2015 at Rockingham Motor Speedway where the vehicles will be seen alongside the finished DAX Cobra 427.
There are currently a total of 1,127 parts in the Solid Edge assembly file.
Summary
The end result is that DAX was able to get most of their active parts lists created in Solid Edge very quickly with the help of the experts at Majenta PLM. With the training provided on the software, DAX can now continue to develop their already great product line in the digital age with virtual testing, prototyping, and marketing. Having an expert guide to the world of advanced engineering software helped DAX leapfrog others in the field, and provided a template for future development work.
Comments