eBook: Challenges and solutions when working with mesh models
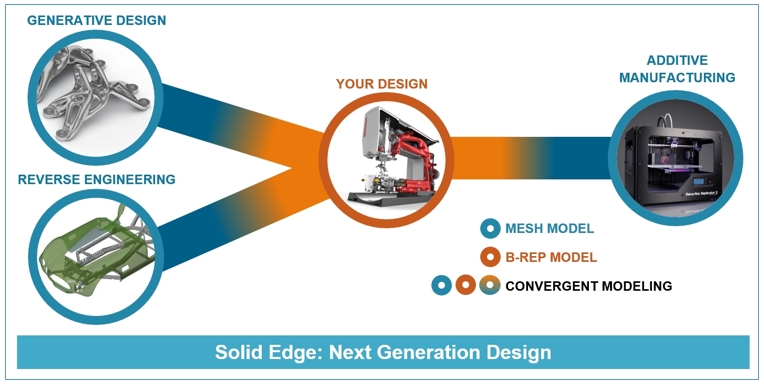
New eBook from looks at the challenges around working with mesh models
A new eBook from industry analyst Lifecycle Insights looks at the challenges that designers are facing in working with mesh models, and the potential solutions provided by new design technologies such as Siemens Convergent Modeling that are being made available in Solid Edge ST10. I highly recommend you read this eBook if you work with mesh models today or see possibilities for doing this in the future.
Chad Jackson, President of Lifecycle Insights, points out that productivity for creating design geometry has increased dramatically in the last few years with both parametric modeling and direct modeling having a positive impact. But these technologies create boundary representation (or b-rep) geometry to exactly define the surfaces that make up the solid models.
Meanwhile, mesh geometry is becoming increasingly important due to the following major trends:
- New “topology optimization” or “generative modeling” tools that create organic looking models to satisfy requirements to maximize strength while minimizing weight and material usage result in mesh models
- The availability of large libraries of 3D designs in mesh formats, such as .STL files
- The increased use of Reverse Engineering to capture the design of existing physical components so they can be recreated as CAD models, or so that new components can be designed to work alongside them
- The consumption of mesh models by fast growing 3D Printing and Additive Manufacturing techniques
According to Chad, current CAD tools are very focused on working with b-rep models, and are not so good at working with mesh models. Designers may need to install and learn specialist software to work with mesh models and this is an overhead that prevents them from focusing on the creative design process.
Incorporating mesh models in the product development process is increasingly important
Chad next looks at new technologies that are being introduced that have the potential to solve this problem. Some of the scenarios these tools can support include:
- Mesh geometry can stay as mesh, but you can perform operations on it using your standard CAD commands to add features. The resultant body is still a mesh body, but you can edit the new features in a similar way to editing b-rep features.
- Use the mesh geometry to add simple b-rep geometry that will allow you to exactly align and constrain the mesh body with your other b-rep bodies in an assembly
- Place different views of the mesh body onto a drawing sheet
- Prepare mesh bodies for 3D printing by adding support structures or changing the quality of the mesh geometry
Chad’s final takeaway is that “For too long, mesh geometry has been considered a fringe case in design. However, as it becomes more mainstream, engineers are losing productivity. CAD applications that offer integrated Parametric, Direct and Facet Modeling capabilities offer real promise to take progressive steps to greater productivity.”
With our addition of Convergent Modeling technology in Solid Edge ST10 we are giving our users excellent capabilities to integrate mesh models into their everyday design processes. You can see this for yourself in our ST10 demo videos. I also believe we are just scratching the surface of how these new tools can benefit our Solid Edge users. Please let us know what you think of the potential for these new capabilities, and as the software is released later this summer, how you are using them.Solid Edge ST includes Convergent Modeling technology and enables designers to work easily with both mesh and b-rep models
Comments