Align workflow and increase productivity with PLM
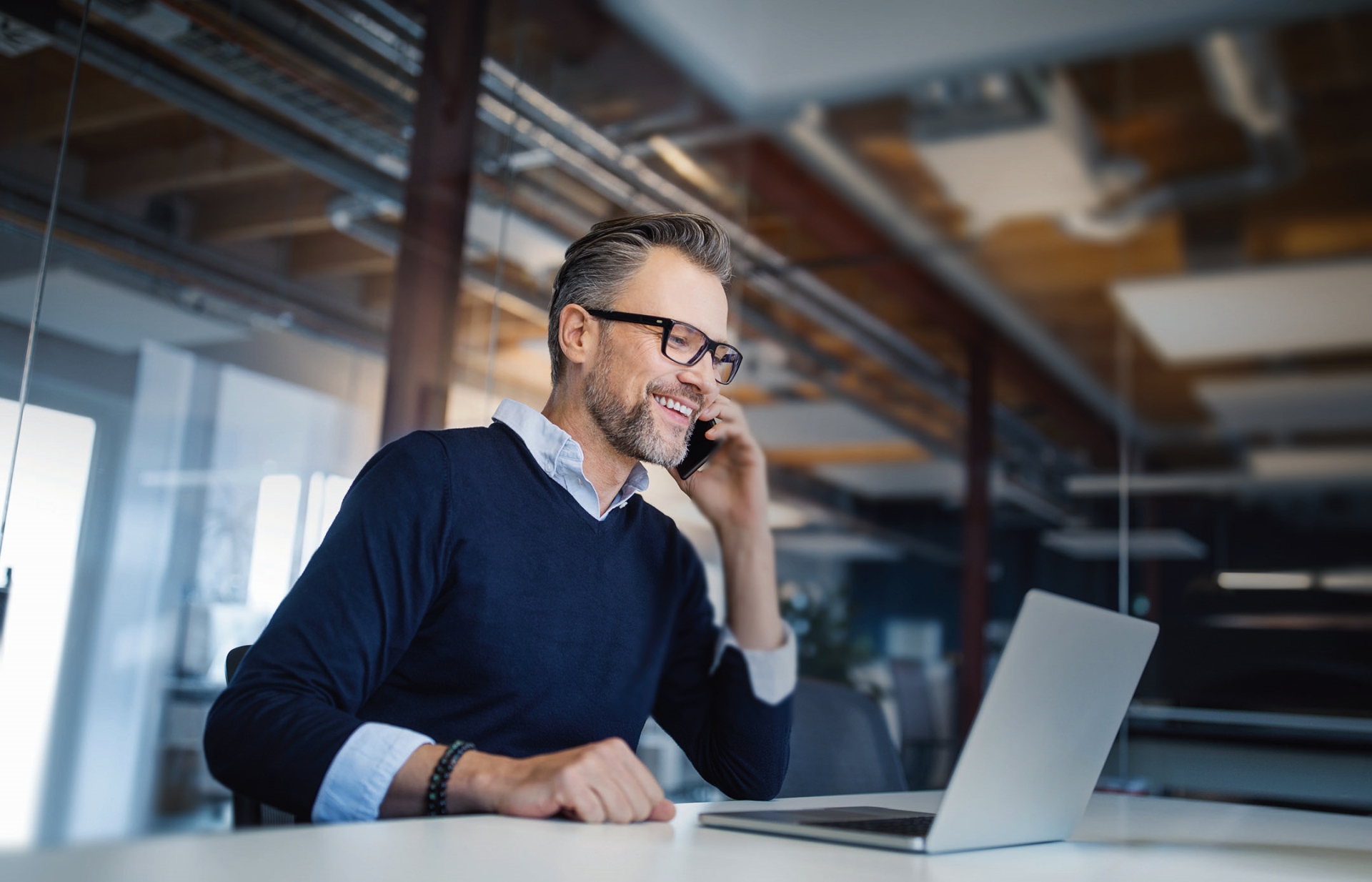
Product lifecycle management (PLM) software is the cornerstone of product development and manufacturing efficiency. It enables companies to manage workflows around the initial design, engineering, simulation and manufacturing of a product while enabling seamless collaboration between departments, management and outside suppliers and vendors. When a company adopts PLM, it streamlines all aspects of manufacturing and eliminates many problems that small and medium businesses (SMBs) face when bringing a product or component to market. Siemens PLM, Teamcenter X and PLM for Component Manufacturers are part of the Siemens Xcelerator portfolio and have been specially designed for SMBs and enterprise manufacturers alike.
How can PLM accelerate product development?
Many SMBs are using disconnected software to track, plan and develop products and component manufacturing. Disconnected software in a manufacturing environment creates data silos that make it hard to collaborate and understand the complete operational workflow of the company. Engineering departments are prone to errors by using out-of-date data; they miss opportunities to reuse existing engineering designs and have trouble collaborating with their peers and outside partners due to CAD interoperability hangups. While many companies have found ways to smooth over these problems, PLM from Siemens can accelerate your product development by providing a software environment that seamlessly brings all your engineering data together. Once implemented, you’ll find that many areas in your engineering department are inadvertently wasting time.
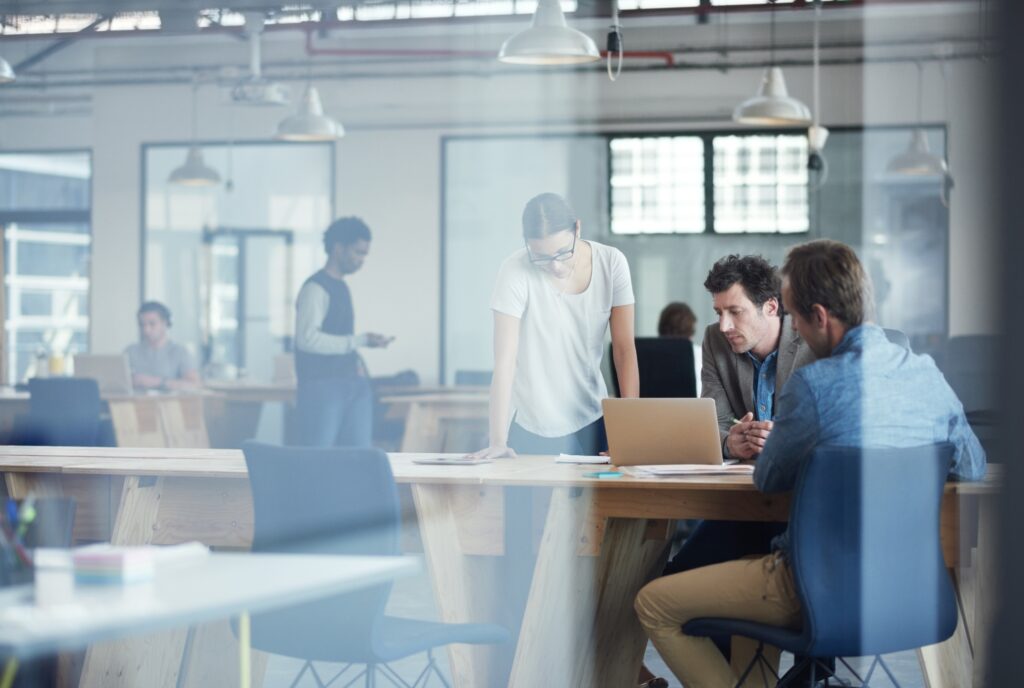
PLM enables next-generation operations management
Aligning your engineering teams and moving their data into a single source of truth with PLM will save your company time as it transitions from order to manufacturing. You gain the ability to track and standardize your processes in a single software environment while eliminating gaps in knowledge across your company. In turn, your operations management activities will see increased efficiency and throughput.
With a PLM solution that has been specifically designed for component manufacturing, you can rapidly implement new processes to communicate across your business with your customers and your suppliers. This is crucial in an age of disruptions across supply chains. An integrated design workspace and purpose-built data-sharing tools are built into Teamcenter to improve all aspects of customer and supplier collaboration. PLM is just one way your business can begin its digital transformation. Join a host of SMBs that are accelerating their engineering software solutions and explore more on our engineering software hub page.
Introduction to Accelerated Engineering
In this video, we share the power of the digital thread we call Accelerated Engineering.
Accelerated Engineering is a single, integrated, multi-disciplinary platform that allows small to mid-size manufacturers to produce high-quality products, address increased competitive pressure, and shorten cycle times while staying on budget and creating a sustainable platform for growth.
Ranked #1 best PLM software by G2
G2 ranks products based on customer reviews. G2 named Teamcenter the best PLM software for any size company – outperforming 99 others. Take a look at the PLM software comparison grid to see the top ranking for Teamcenter.
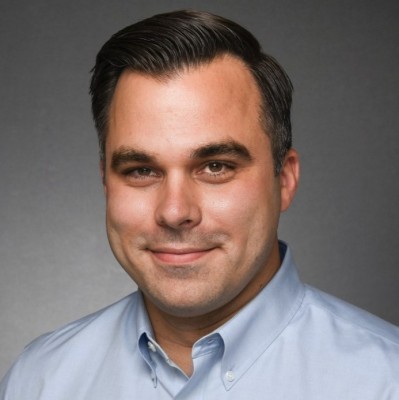
About the author
David Lyell is a marketing manager for Siemens Digital Industries Software and serves the Small and Medium Business industry. He has spent his career in manufacturing and marketing across several industries, including automation, job shops, additive manufacturing and woodworking.