2022 Flexible Manufacturing Study: Understanding Small and Medium-Sized Business Priorities in Manufacturing
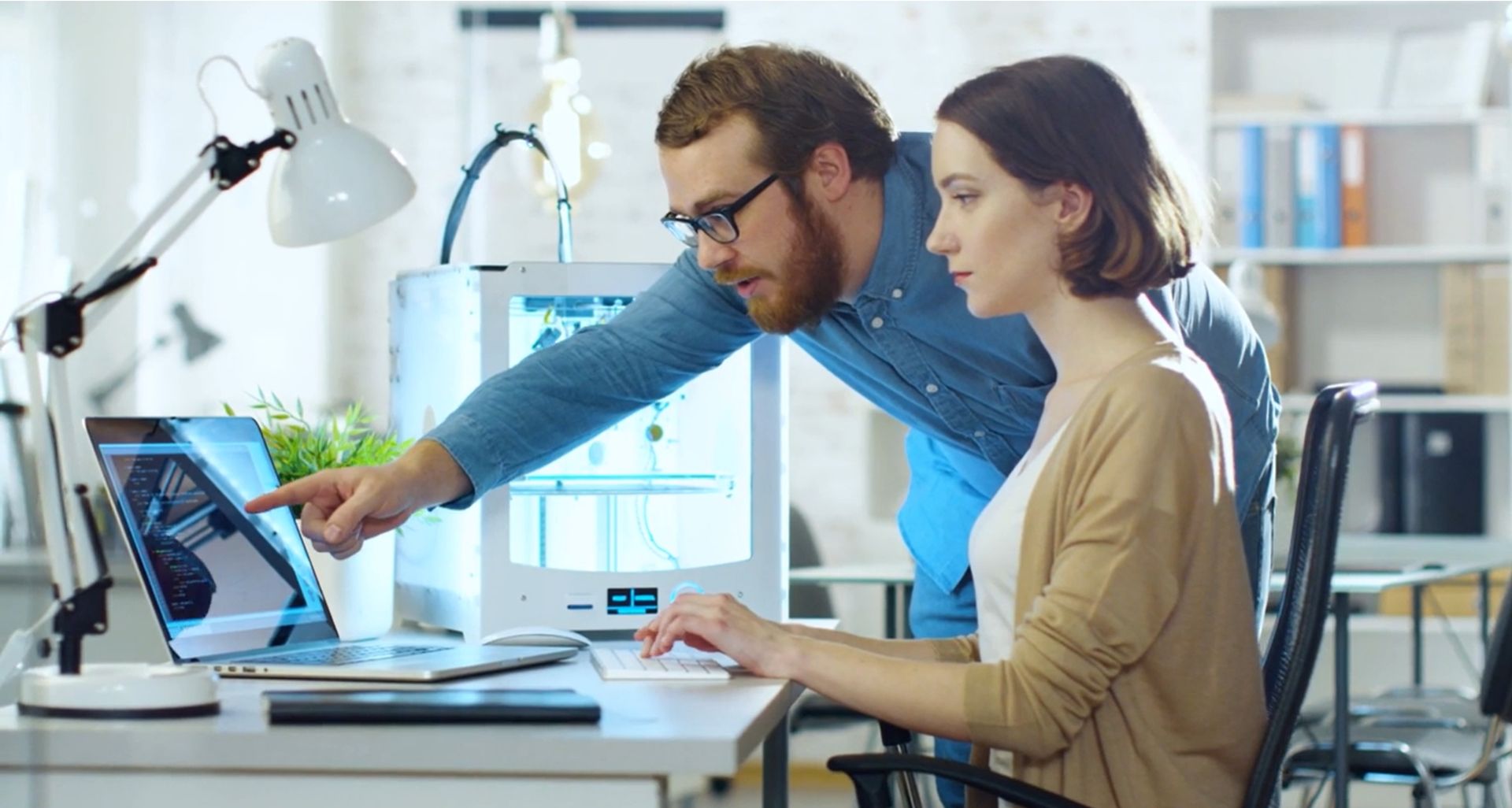
Many large companies have digitally transformed their manufacturing operations to speed up their time to market, improve product quality, and increase profits. What has not been as clear, however, is whether small and medium-sized businesses (SMBs) can achieve the same benefits through digital transformation. To find out, Lifecycle Insights conducted a global, survey-based study to better understand the impact of SMBs’ digital transformation efforts.
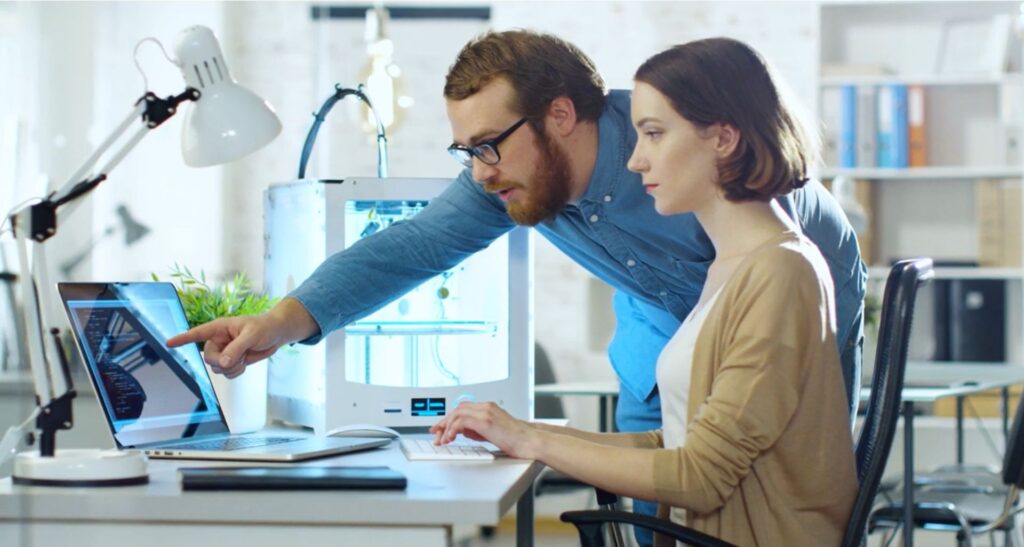
Study Objectives
The 2022 Flexible Manufacturing Study gathered responses from manufacturing executives at SMBs in a variety of industries. Lifecycle Insights conducted the study to gain insight into the factors driving SMBs to improve manufacturing efforts as well as the relative priority levels of those efforts. This post will detail the study participants’ demographics and the study’s main takeaways. Specifically, it will explore respondents’ manufacturing priorities, their willingness to introduce industrial internet of things (IIoT), and their views on additive manufacturing.
Study Demographics
Of the 275 manufacturing executives who participated in the worldwide study, 35% are based in North America, and 38% are based in Europe. The remaining participants came largely from Asia and South America.
The largest percentages of study participants came from sectors commonly inhabited by SMBs. These industries include industrial machinery (35%); consumer products (26%); heavy equipment (20%); mold, tool, and die (15%); and high-tech products and electronics (13%). Some respondents also came from tier two or three of the automotive (7%) or aerospace and defense (4%) industries. Tier two and three companies are part of the supply chain in these sectors but do not sell directly to original equipment manufacturers (OEMs).
Nearly all respondents (97%) came from companies with annual revenues of less than $1 billion. Respondents represented companies from several different revenue ranges. Just under one-third (29%) of respondents’ companies made under $100 million, while 22% had annual revenues of between $100 million and $300 million. About a quarter of respondents (24%) reported company revenues between $300 million and $500 million. The study also included participants whose organizations make between $500 million and $750 million (13%) and those who earn between $750 million and $1 billion (9%).
Making Improvements to Manufacturing
Findings from the 2022 Flexible Manufacturing Study reveal that improving manufacturing is a top priority for 57% of all respondents. A further 31% identified better manufacturing as a desired organizational outcome for their company or engineering department.
What is driving this desire for change? One-third of respondents indicated that competitive pressures—the need to get products to market quickly, lower product cost, and create innovative products—are the greatest factor driving their manufacturing improvement. Well over half of manufacturing executives (60%) said that these pressures are a top-three factor in their desire to better their manufacturing outcomes.
Additionally, 15% of respondents said seasonal, cost, or product requirements are driving their companies to improve manufacturing. The same percentage cited regulations and incentives, such as sustainability requirements and safety or security standards, as the top such factor.
The Adoption of IIoT Solutions
Employing IIoT solutions is one of the primary ways companies seek to improve manufacturing. Nearly half of all respondents (49%) indicated that introducing IIoT into their manufacturing was either their company’s top priority or their engineering department’s top priority. An additional 30% said introducing IIoT is a desired outcome for their companies.
Many of the traditional office and digital tools used to manage manufacturing at SMBs are limited in functionality. These disconnected solutions make it difficult to automate tasks. They are also susceptible to data loss and lapses in communication between stakeholders. In short: They’re inefficient, and they hinder productivity.
On the other hand, IIoT solutions enable companies to capture and share manufacturing equipment data in real time. As a result, organizations can improve their overall equipment effectiveness, product quality, and even forecasting accuracy. These solutions use sensors to gather equipment performance data, making it possible to detect anomalies in the equipment’s operation and address them quickly to avoid production shutdowns. IIoT solutions can also provide insights into key metrics such as energy consumption, which is vital for companies tracking progress toward sustainability goals.
Growing Interest in Additive Manufacturing
Additive manufacturing is another approach gaining popularity with manufacturers. Lifecycle Insights’ study sought to understand this interest by asking participants to share their plans around additive manufacturing over the next two years. About one-third of respondents (32%) said their companies would have significant use for additive manufacturing over the next two years. Another 31% indicated that their companies would have moderate use for additive manufacturing, and about a quarter (25%) said they would have some use for it.
Additive manufacturing is on companies’ radars because it shortens new product development time. Using this technology, companies can more quickly create and test prototypes, saving time and effort during a challenging stage of development. Additive manufacturing also enables companies to work with greater agility. They can incorporate customer feedback into incremental design revisions to stay ahead of consumer preferences and remain competitive. The technology also facilitates the easy incorporation of innovative materials into products.
The good news is that additive manufacturing is already accessible. Print bureaus, where companies can create prototypes using their CAD models, can be found around the world.
Conclusion
Today’s companies face intense competitive pressures. To reduce their time to market, lower product cost, and create more innovative, higher quality products, these companies are making the improvement of manufacturing a high priority.
IIoT solutions are one way that companies can address this priority. This technology allows manufacturers to quickly capture key real-time data related to equipment performance. By analyzing this data, companies can:
- gain crucial insights that help them predict and prevent costly equipment failures and unplanned downtime;
- maintain a high level of product quality; and
- make progress on their sustainability goals.
Additive manufacturing is another solution that helps companies increase efficiency as they pursue their manufacturing goals. This technology can help shorten the development process by making prototyping, testing, and incremental design improvements far simpler to execute.