Automated Model Calibration in FloTHERM – A Future Cornerstone of Simulation Based Workflows, Today
Available in the recently released FloTHERM V11.1 is the ability to calibrate a FloTHERM simulation model so that it matches experimentally measured results. The calibration process is automatic and results in a model with unrivaled levels of predictive accuracy. The experimental results used are not simple thermocouple based measurements, but T3Ster based measurements that provide insight into the complete heat flow path from die through IC package, PCB, chassis and to ambient. Electronics thermal applications are typified by multiple parts, glued, soldered, bolted, crimped and bonded together in various ways. The scope for erroneous data input to a simulation model is high, especially when it comes to such contact/TIM thermal resistances. Such a calibration is a sure fire way to minimize the ever present risk of ‘bad data in -> bad simulation data out’.
The T3Ster (pronounced: “trister”) measurement system can be thought of as a thermal sonar system. An IC package is subjected to a step change in power dissipation, the resulting junction temperature vs. time response is (accurately) measured. This profile is then mathematically converted into a Structure Function, a representation of all the thermal resistances and thermal capacitances the heat experiences on its path from heat source (die) to fixed temperature (infinite capacitance) ambient. All deduced from just monitoring the temperature rise response of the heat source, a form of remote sensing.
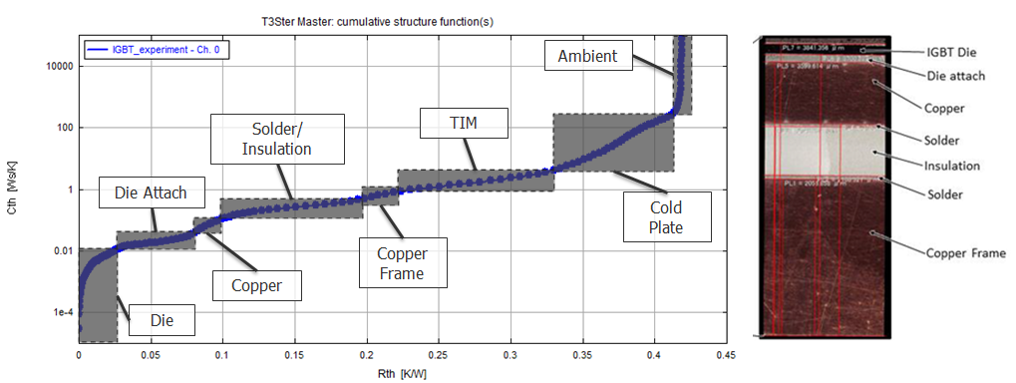
Such information can be exported from the T3Ster post-processing software for import into FloTHERM.
The FloTHERM model can then be automatically modified to replicate the transient T3Ster measurement. This involves a one button automatic: setting the model as transient, setting the time grid, ensuring the power dissipation step and starting ambient temperature is the same as the experiment.
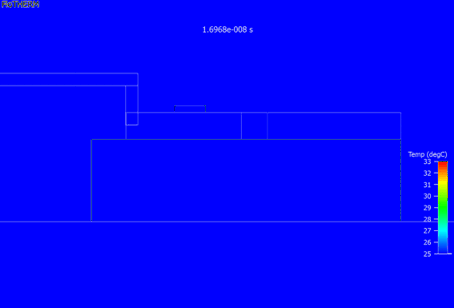
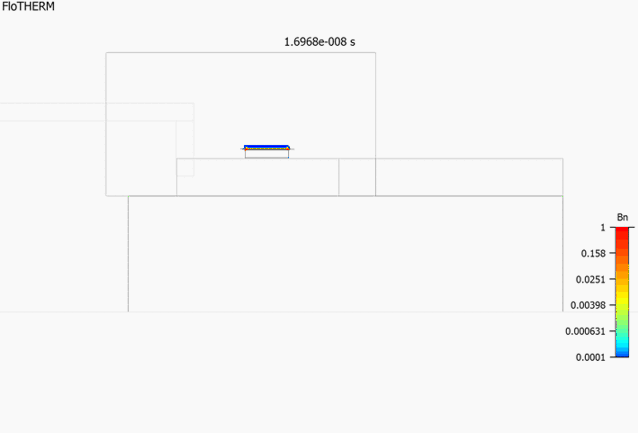
An optimization study is then performed in FloTHERM, involving automated modification of user nominated model parameters with repeat simulations, until such time as the experimental and numerically simulated structure functions match (as would the Zth responses).
The calibrated model can then be used with high confidence, passed along the supply chain, used to derive 2R of DELPHI CTMs etc.
Byron Blackmore, the FloTHERM Product Manager, will introduce and demonstrate this remarkable new capability in two webinars on Wednesday 20th January (11:00 AM – 11:45 AM Europe/London and 10:00 AM – 10:45 AM US/Pacific). An opportunity to ask further questions as well. Registration is via this link: https://www.mentor.com/products/mechanical/events/maximize-the-accuracy-of-your-flotherm-models-using-t3ster-measurements
Over the last two decades the numerics of simulation solver technologies have matured, as have parametric and optimization features, MCAD and EDA interfacing, post processing etc. The future of simulation will not stagnate at this current level but will see a move towards data input validation and synergies with experimental methods. The Mechanical Analysis Division of Mentor Graphics is well placed to both pioneer and support such an approach now and in the future!
12th January 2015, Ross-on-Wye.